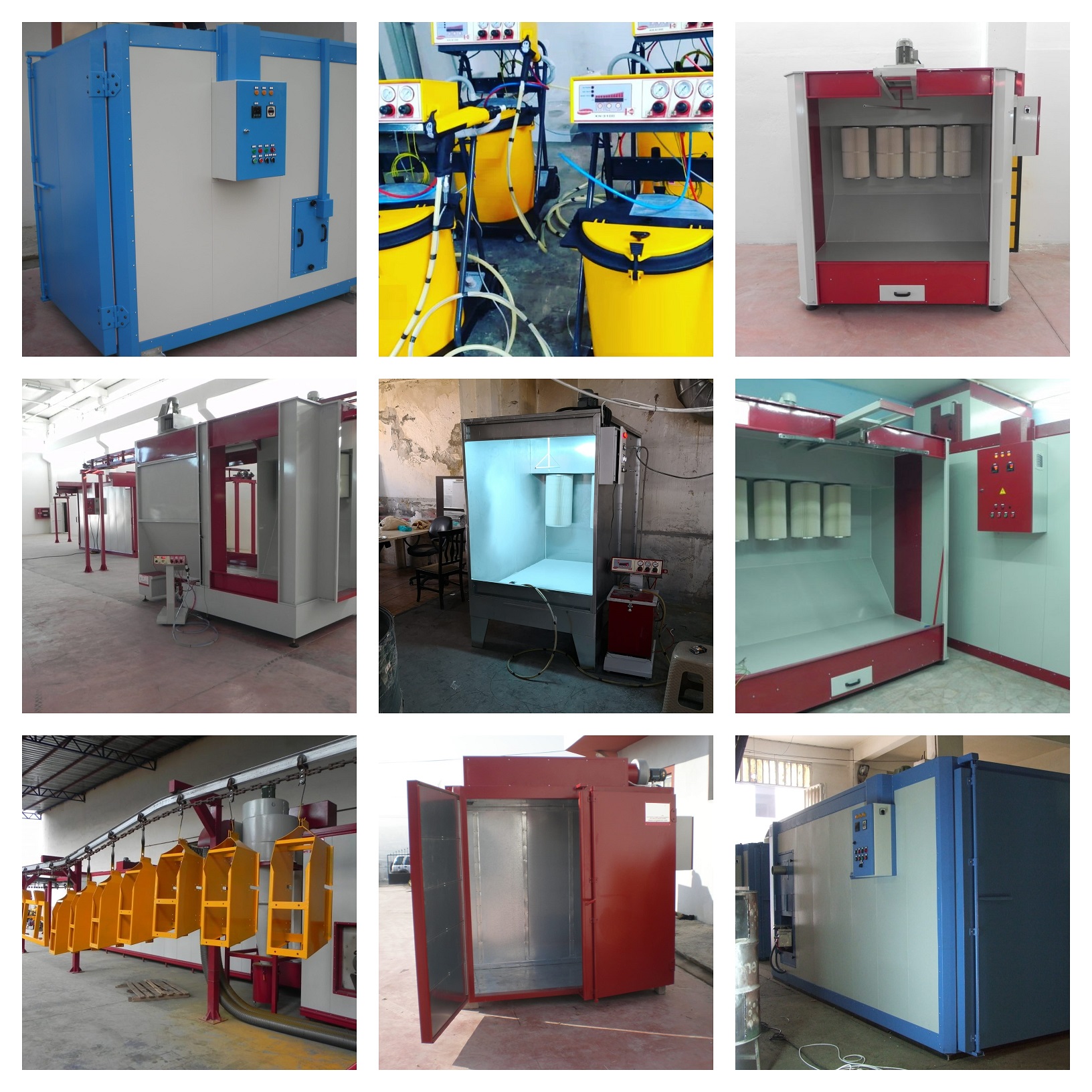
Equipos para Pintura Electrostática: La pintura electrostática se ha convertido en una tecnología esencial en la industria moderna debido a su eficiencia, calidad y capacidad para reducir el impacto ambiental. Este proceso, que utiliza la electricidad para adherir las partículas de pintura a las superficies, ha revolucionado la manera en que se aplican recubrimientos en una amplia gama de materiales, desde metales hasta plásticos.
¿Qué es la Pintura Electrostática?
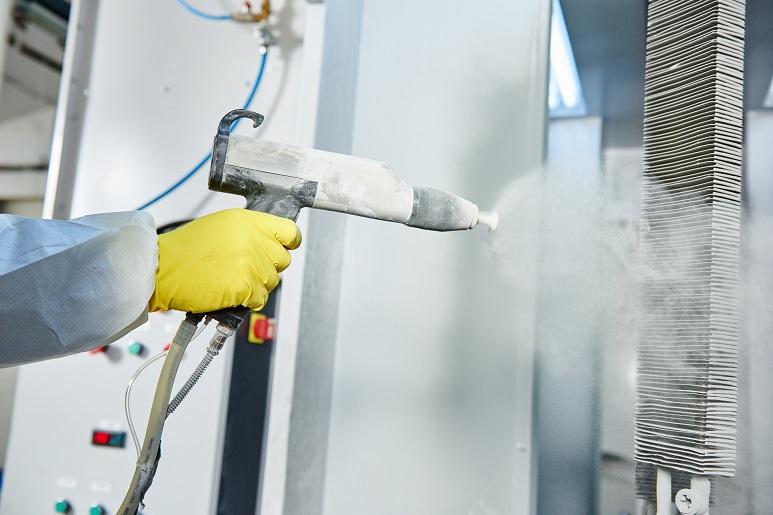
La pintura electrostática es un método de aplicación de recubrimientos que se basa en la atracción de cargas eléctricas opuestas. En este proceso, las partículas de pintura en polvo, que han sido cargadas eléctricamente, son proyectadas sobre una superficie que posee una carga opuesta. Gracias a la fuerza electrostática, las partículas de pintura se adhieren de manera uniforme a la superficie, creando un recubrimiento consistente y de alta calidad. Este método es ampliamente utilizado en la pintura de metales, donde la adherencia y la uniformidad son cruciales para garantizar la durabilidad y el acabado estético del producto.
Historia y Evolución de la Tecnología
El concepto de la pintura electrostática tiene sus raíces en el siglo XX, cuando se comenzaron a explorar métodos más eficientes y económicos para la aplicación de recubrimientos. La necesidad de mejorar la adherencia y reducir el desperdicio de material llevó al desarrollo de técnicas basadas en la electrostática. La primera aplicación significativa de esta tecnología tuvo lugar durante la Segunda Guerra Mundial, cuando se buscaba mejorar los procesos de pintado en la industria aeronáutica y militar.
En las décadas posteriores, los avances tecnológicos permitieron la refinación del proceso, pasando de simples aplicaciones manuales a sistemas automatizados que garantizan una aplicación precisa y controlada de la pintura. En la actualidad, la pintura electrostática es un estándar en numerosas industrias, destacando por su capacidad para proporcionar un acabado duradero y estéticamente agradable.
Importancia en la Industria Moderna
Hoy en día, la pintura electrostática es fundamental en sectores como el automotriz, la fabricación de electrodomésticos, la industria del mueble metálico, y en la producción de componentes industriales. La eficiencia del proceso no solo permite ahorrar material, sino que también contribuye significativamente a la reducción de emisiones contaminantes, ya que el exceso de pintura se recupera y reutiliza en gran medida.
Además, este método de pintura es reconocido por su capacidad para proporcionar una cobertura uniforme, incluso en superficies complejas, y por su durabilidad, lo que resulta en productos de alta calidad que resisten el paso del tiempo y las condiciones ambientales adversas. La capacidad de los equipos modernos de pintura electrostática para adaptarse a diferentes tipos de materiales y aplicaciones los convierte en una herramienta indispensable para la producción industrial a gran escala.
En resumen, la pintura electrostática representa una convergencia de eficiencia, calidad y responsabilidad ambiental, siendo un pilar en la fabricación de productos duraderos y visualmente atractivos. La evolución de esta tecnología sigue en marcha, con innovaciones que prometen hacerla aún más eficiente y versátil en el futuro cercano.
Genial, ahora procederé a redactar la sección sobre los Principios de Funcionamiento de la Pintura Electrostática. Aquí se explicarán en detalle los aspectos técnicos del proceso, sus fundamentos físicos y químicos, y se comparará con otros métodos de pintura. También se destacarán las ventajas y desventajas de este método en particular.
Principios de Funcionamiento de la Pintura Electrostática
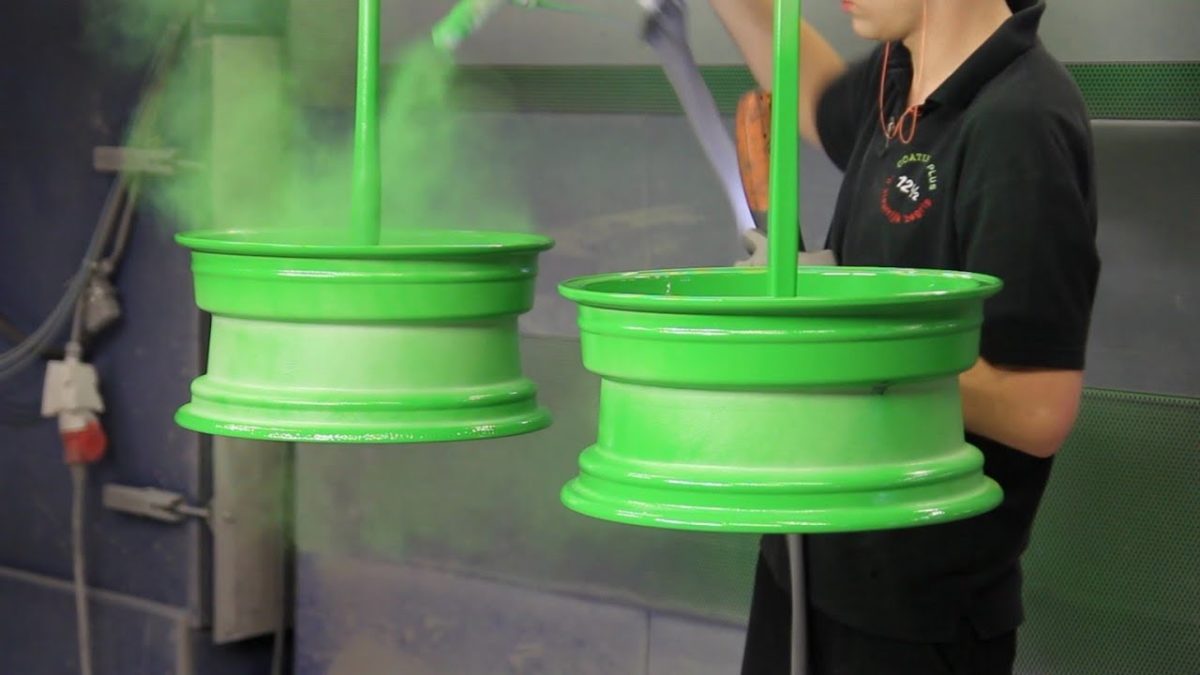
La pintura electrostática es un proceso altamente eficiente que se basa en principios físicos y químicos para lograr una adherencia uniforme de la pintura en diferentes tipos de superficies. Este método ha ganado popularidad en diversas industrias debido a su capacidad para ofrecer acabados duraderos y de alta calidad con un menor impacto ambiental.
Fundamentos Físicos y Químicos del Proceso
El proceso de pintura electrostática se fundamenta en la ley de Coulomb, que establece que las cargas opuestas se atraen y las cargas similares se repelen. En términos simples, el proceso comienza con la carga eléctrica de las partículas de pintura, generalmente en forma de polvo. Estas partículas se cargan positivamente o negativamente utilizando un dispositivo especializado, como una pistola de pulverización electrostática.
La superficie que se va a pintar, por su parte, se carga con una polaridad opuesta a la de las partículas de pintura. Esta diferencia de cargas genera una fuerte atracción entre la superficie y las partículas, asegurando que la pintura se adhiera uniformemente, incluso en superficies irregulares o de formas complejas.
Una vez que la pintura ha sido aplicada, la pieza pintada se somete a un proceso de curado, generalmente mediante la aplicación de calor en un horno especializado. Durante el curado, las partículas de pintura se funden y forman una película uniforme que se adhiere firmemente a la superficie. Este proceso no solo mejora la adherencia, sino que también otorga al recubrimiento una alta resistencia al desgaste, a la corrosión y a los agentes químicos.
Comparación con Otros Métodos de Pintura
La pintura electrostática se diferencia significativamente de otros métodos tradicionales de pintura, como la pintura líquida con brocha o pistola sin carga electrostática. Entre las principales diferencias se encuentran:
- Adherencia y Uniformidad: Gracias a la atracción electrostática, la pintura se adhiere de manera más uniforme, minimizando el riesgo de corrimientos o acumulaciones excesivas de material en determinadas zonas. En métodos convencionales, la aplicación puede ser más desigual, especialmente en superficies con geometrías complejas.
- Eficiencia en el Uso del Material: En la pintura convencional, una gran parte de la pintura puede perderse debido a la dispersión en el aire o a la aplicación excesiva. La pintura electrostática, en cambio, permite recuperar el material que no se adhiere en la primera aplicación, lo que reduce significativamente el desperdicio.
- Impacto Ambiental: La pintura electrostática genera menos emisiones de compuestos orgánicos volátiles (COVs) y permite una mejor recuperación y reutilización del material, lo que la convierte en una opción más ecológica comparada con la pintura líquida tradicional.
- Durabilidad del Recubrimiento: Los recubrimientos aplicados mediante pintura electrostática tienden a ser más duraderos y resistentes a la abrasión, la corrosión y las condiciones climáticas adversas en comparación con los recubrimientos aplicados mediante métodos tradicionales.
Ventajas de la Pintura Electrostática
- Alta Eficiencia: La capacidad de atraer las partículas de pintura hacia la superficie reduce el desperdicio y mejora la cobertura, lo que se traduce en un proceso más rentable.
- Calidad del Acabado: Proporciona un acabado uniforme, liso y sin marcas de pincel o rociado, lo que mejora la apariencia estética del producto final.
- Durabilidad: Los recubrimientos aplicados mediante este proceso son conocidos por su resistencia y durabilidad, protegiendo las superficies contra el desgaste y la corrosión.
- Amigable con el Medio Ambiente: Al reducir las emisiones de COVs y el desperdicio de pintura, este método es más sostenible que los métodos tradicionales.
Continuaré entonces con la sección sobre los Tipos de Equipos para Pintura Electrostática. Aquí abordaremos los diferentes equipos utilizados en el proceso, sus características, y cómo se integran en el sistema completo de pintura electrostática.
Tipos de Equipos para Pintura Electrostática
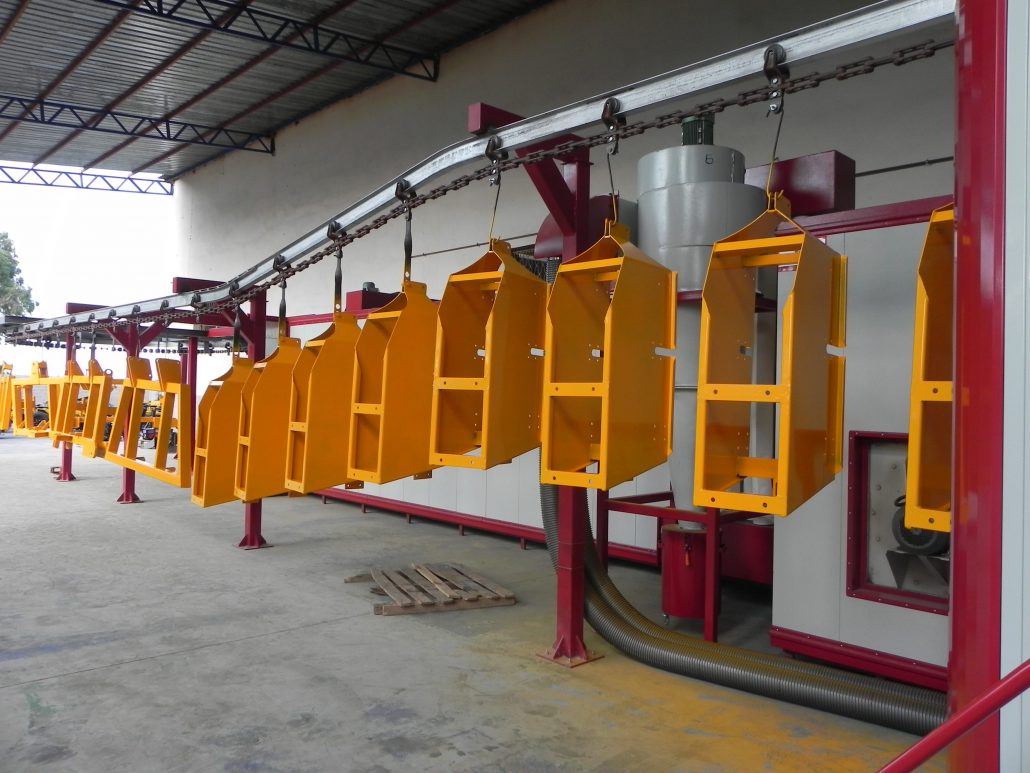
La pintura electrostática requiere de un conjunto especializado de equipos para asegurar un proceso eficiente y de alta calidad. Estos equipos no solo son responsables de la aplicación de la pintura, sino también del manejo seguro de los materiales y la optimización del proceso en términos de tiempo y recursos. A continuación, se detallan los principales tipos de equipos utilizados en la pintura electrostática.
Pistolas de Pulverización Electrostática
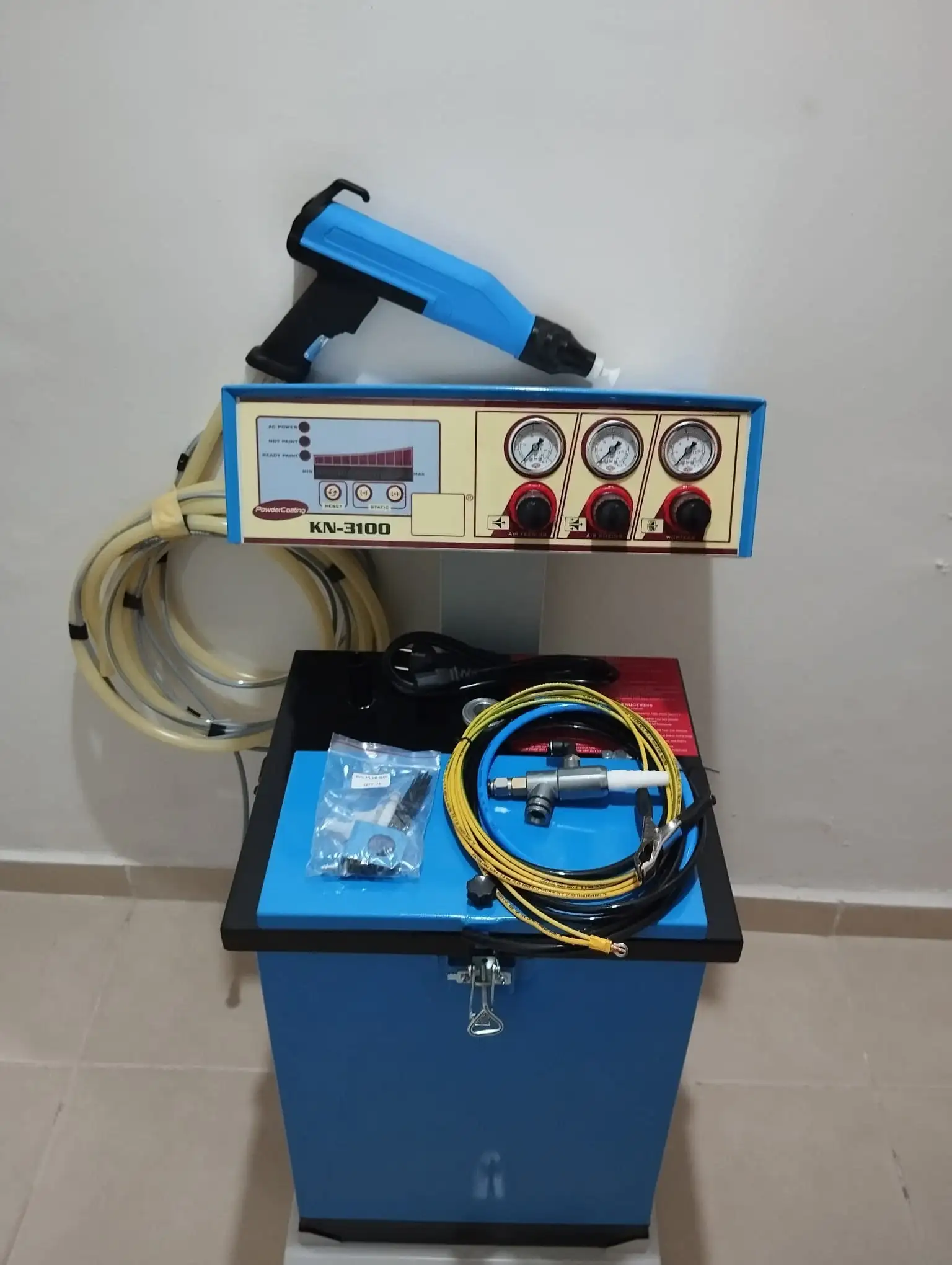
La pistola de pulverización electrostática es el componente central del sistema de pintura electrostática. Este dispositivo es el encargado de cargar eléctricamente las partículas de pintura en polvo y proyectarlas hacia la superficie del objeto a pintar.
Características Principales:
- Cargador de Partículas: La pistola contiene un mecanismo que genera una carga eléctrica sobre las partículas de pintura. Esta carga puede ser positiva o negativa, dependiendo del diseño del sistema.
- Boquilla de Pulverización: A través de la boquilla, las partículas de pintura cargadas son expulsadas en forma de nube. La boquilla está diseñada para proporcionar un patrón de rociado uniforme, lo que es crucial para asegurar una cobertura consistente.
- Tipos de Pistolas:
- Manual: Utilizadas principalmente en aplicaciones donde se requiere precisión y control directo por parte del operario. Son comunes en talleres de pequeña escala o para piezas únicas.
- Automáticas: Incorporadas en líneas de producción automatizadas. Estas pistolas están montadas en robots o sistemas fijos que permiten una aplicación rápida y consistente en entornos de producción en masa.
Ventajas de las Pistolas de Pulverización:
- Alta Eficiencia: Las pistolas permiten una alta tasa de transferencia de pintura, minimizando el desperdicio.
- Versatilidad: Pueden ser ajustadas para diferentes tipos de materiales y acabados.
Cabinas de Pintura
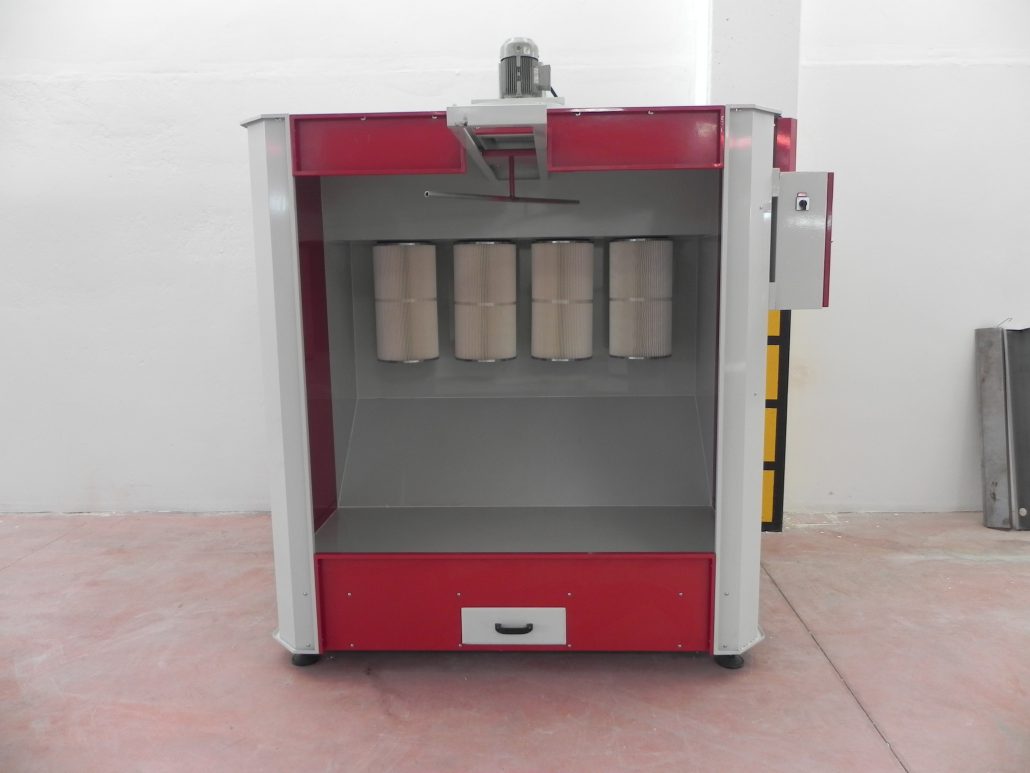
Las cabinas de pintura son espacios cerrados donde se realiza la aplicación de la pintura electrostática. Estas cabinas están diseñadas para contener el polvo de pintura y mantener un ambiente controlado, lo que es esencial para la seguridad y la eficiencia del proceso.
Características Principales:
- Filtración de Aire: Las cabinas están equipadas con sistemas de filtración que capturan el exceso de polvo de pintura en el aire, reduciendo la contaminación y permitiendo la recuperación del material no adherido.
- Sistemas de Ventilación: Garantizan un flujo de aire adecuado para evitar la acumulación de partículas y mantener un entorno seguro para el operario.
- Tipos de Cabinas:
- Cabinas Abiertas: Utilizadas en procesos donde se espera una menor acumulación de polvo. Estas cabinas cuentan con una parte abierta para la manipulación más fácil de piezas grandes.
- Cabinas Cerradas: Ideales para ambientes de alta producción donde es necesario un mayor control del polvo y la ventilación. Estas cabinas completamente cerradas permiten una mayor recuperación del polvo y un mejor control del proceso.
Beneficios de las Cabinas de Pintura:
- Mejora de la Calidad del Aire: Mantienen el ambiente libre de polvo, protegiendo tanto al personal como al producto.
- Eficiencia en la Recuperación de Polvo: Los sistemas de recuperación permiten reutilizar el material, reduciendo costos y desperdicios.
Las cabinas continuas para pintura en polvo
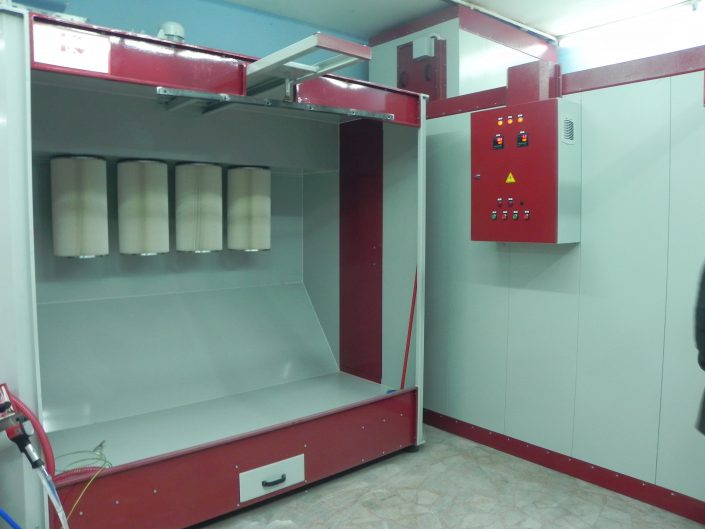
Las cabinas continuas para pintura en polvo son sistemas industriales diseñados para aplicar recubrimientos de polvo sobre una amplia variedad de superficies, utilizando una técnica eficiente y ecológica. Este tipo de cabina se emplea principalmente en procesos de pintura de metales, plásticos y otros materiales que requieren una capa uniforme y duradera. A diferencia de las cabinas tradicionales, que funcionan con ciclos discontinuos, las cabinas continuas están diseñadas para permitir un flujo constante de trabajo, lo que mejora la productividad y reduce los tiempos de espera entre aplicaciones.
El principio de funcionamiento de una cabina continua para pintura en polvo se basa en el uso de un sistema de transporte continuo para las piezas a pintar. Este sistema puede ser de tipo monorraíl, cintas transportadoras o carros motorizados que mueven los objetos a través de la cabina, donde se aplica la pintura en polvo mediante pistolas electrostáticas. El polvo se carga electrostáticamente para asegurar una adherencia eficiente sobre la superficie del objeto. Las cabinas están equipadas con filtros de alta eficiencia para recolectar el polvo sobrante y evitar su dispersión en el aire, lo que no solo mejora la calidad del acabado, sino que también cumple con las normativas ambientales.
Una de las principales ventajas de las cabinas continuas para pintura en polvo es su capacidad para manejar grandes volúmenes de piezas de manera constante. Esto las hace ideales para industrias con altas demandas de producción, como la automotriz, la fabricación de electrodomésticos y la industria del mueble. Además, el proceso de pintura en polvo es más eficiente en términos de materiales, ya que el polvo no utilizado puede ser reciclado y reutilizado, lo que reduce el desperdicio y optimiza los costos operativos.
El diseño de estas cabinas también incluye sistemas de control automatizados que permiten ajustar la cantidad de pintura aplicada según las necesidades específicas de cada producto. Los parámetros de la pintura, como la densidad del polvo, la velocidad de la aplicación y el voltaje de las pistolas, se pueden regular para lograr acabados de alta calidad. A través de estos controles, las cabinas continuas ofrecen una consistencia en la calidad del recubrimiento, lo cual es crucial para la satisfacción del cliente y el cumplimiento de las especificaciones técnicas.
A nivel ambiental, la pintura en polvo es una opción mucho más amigable en comparación con las pinturas líquidas tradicionales, que a menudo contienen disolventes químicos y otros compuestos volátiles orgánicos. Esto hace que las cabinas de pintura en polvo sean una elección preferida para las empresas que buscan reducir su huella ecológica y cumplir con las normativas medioambientales cada vez más estrictas. El proceso de curado de la pintura, que se realiza en un horno posterior a la aplicación, también es eficiente, utilizando temperaturas controladas para endurecer la pintura sin liberar compuestos nocivos al ambiente.
En términos de mantenimiento, las cabinas continuas requieren atención periódica para garantizar su funcionamiento óptimo. Los filtros y los sistemas de reciclaje de polvo deben limpiarse con regularidad para evitar obstrucciones y asegurar una correcta circulación del aire. También es importante verificar las pistolas de pintura y los sistemas de transporte, ya que cualquier fallo en estos componentes puede afectar la calidad del recubrimiento y la eficiencia del proceso.
En resumen, las cabinas continuas para pintura en polvo son una solución avanzada y eficiente para la aplicación de recubrimientos en diversas industrias. Su capacidad para manejar grandes volúmenes de piezas, junto con su sistema de control automatizado y sus beneficios ambientales, las convierte en una opción destacada en la fabricación moderna. Sin embargo, su correcta operación depende de un mantenimiento adecuado y de la supervisión constante para asegurar que cada pieza reciba el acabado deseado.
Además de los beneficios operativos y ambientales mencionados, las cabinas continuas para pintura en polvo también ofrecen ventajas adicionales en términos de flexibilidad y adaptabilidad a diferentes tipos de producción. Esto se debe a que las cabinas pueden configurarse para aceptar una variedad de tamaños y formas de piezas, lo que las hace ideales para una amplia gama de aplicaciones industriales. A través de la personalización de las configuraciones de las pistolas de pulverización y el ajuste de los sistemas de transporte, las cabinas continuas pueden adaptarse fácilmente a los requisitos específicos de cada línea de producción.
Otro aspecto importante de estas cabinas es su capacidad para mejorar la calidad del acabado final. La aplicación de pintura en polvo, al ser un proceso electrostático, proporciona una cobertura uniforme y densa sobre las superficies de las piezas, minimizando los problemas comunes que ocurren con otros tipos de recubrimiento, como las manchas, el escurrimiento o la formación de burbujas. Esto es especialmente crítico en industrias donde la estética del producto final es una prioridad, como la fabricación de electrodomésticos, muebles de diseño y componentes automotrices.
El aspecto económico también juega un papel importante en la elección de las cabinas continuas para pintura en polvo. Si bien la inversión inicial en la compra e instalación de estos sistemas puede ser considerable, los beneficios a largo plazo son significativos. El reciclaje del polvo, la reducción del desperdicio y la eficiencia del proceso de curado contribuyen a un ahorro sustancial en los costos de materiales y energía. Asimismo, la automatización del proceso de aplicación permite reducir la necesidad de mano de obra en comparación con los métodos manuales, lo que optimiza los costos operativos y aumenta la productividad general.
Las cabinas continuas también ofrecen la ventaja de una mayor velocidad de producción. Dado que las piezas se transportan continuamente a través de la cabina y el proceso de aplicación es casi ininterrumpido, el tiempo requerido para recubrir una gran cantidad de piezas se reduce significativamente. Esto es crucial en entornos industriales donde la rapidez es esencial para mantener la competitividad. Al integrar estos sistemas con otros procesos automatizados, como la carga y descarga de piezas, el tiempo de inactividad se minimiza aún más, lo que contribuye a una mayor eficiencia global de la planta de producción.
En cuanto a la seguridad, las cabinas continuas están diseñadas para cumplir con rigurosos estándares de seguridad laboral. El proceso de pintura en polvo no involucra el uso de líquidos inflamables, lo que reduce los riesgos de incendio en comparación con otras técnicas de pintura. Sin embargo, las cabinas deben estar equipadas con sistemas de ventilación adecuados para evitar la acumulación de polvo en el aire, lo que podría representar un riesgo para la salud de los operarios si no se gestiona correctamente. Los sistemas de filtrado y recolección de polvo están diseñados para minimizar la exposición al polvo fino y garantizar un entorno de trabajo seguro.
Finalmente, la versatilidad de las cabinas continuas permite su uso en diversas aplicaciones más allá de la pintura en polvo. Algunas cabinas están adaptadas para aplicar otros tipos de recubrimientos secos, como los recubrimientos cerámicos o las soluciones antifricción, lo que amplía su utilidad en sectores como la fabricación de componentes electrónicos, la industria aeroespacial o la producción de maquinaria pesada.
En conclusión, las cabinas continuas para pintura en polvo se han consolidado como una solución integral en la industria de recubrimientos. Ofrecen una serie de ventajas que van desde una mayor eficiencia operativa hasta una mejor calidad del acabado y un menor impacto ambiental. A medida que las industrias siguen avanzando hacia procesos más sostenibles y eficientes, las cabinas continuas para pintura en polvo se posicionan como una tecnología clave en la fabricación moderna, optimizando tanto los recursos como los costos, mientras cumplen con las estrictas normativas ambientales y de seguridad.
Además de las ventajas ya mencionadas, las cabinas continuas para pintura en polvo se están beneficiando de las innovaciones tecnológicas que continúan mejorando sus capacidades y ampliando su eficiencia. El uso de sistemas de control digital y software avanzado ha permitido una mayor precisión en la gestión del proceso de pintura, con sistemas que permiten la monitoreo en tiempo real de varios parámetros críticos, como el flujo de aire, la presión de las pistolas de pulverización, y la cantidad de polvo aplicado. Esta automatización y control permiten realizar ajustes instantáneos durante el proceso de producción, mejorando la consistencia del recubrimiento y minimizando el margen de error.
Los avances en la tecnología de filtros también han mejorado la eficiencia de recolección de polvo. Los filtros HEPA (High-Efficiency Particulate Air) de última generación, por ejemplo, permiten una captura aún más efectiva de las partículas finas de polvo, lo que contribuye no solo a la mejora de la calidad del aire en la planta, sino también a un ahorro significativo de material. El polvo que se recoge puede ser reciclado y reutilizado, lo que no solo reduce el desperdicio, sino que también disminuye el costo operativo general.
Otra innovación relevante es la mejora de los sistemas de curado, que es el proceso mediante el cual la pintura en polvo se endurece y se adhiere de manera permanente a la superficie tratada. Tradicionalmente, los hornos de curado utilizaban calefacción por convección, pero ahora se están implementando tecnologías de curado por infrarrojos y microondas. Estos sistemas permiten un calentamiento más rápido y eficiente, reduciendo los tiempos de curado y aumentando la capacidad de producción. Además, estos sistemas de curado más eficientes también pueden ahorrar energía, lo que tiene un impacto positivo en la reducción de los costos operativos.
El diseño modular de muchas cabinas continuas también ha ganado popularidad, lo que permite que las instalaciones se adapten a las necesidades de producción cambiantes de las empresas. Las cabinas modulares pueden escalarse fácilmente en función de los requisitos de producción, agregando secciones adicionales o ajustando el tamaño de la cabina sin necesidad de una reconstrucción completa. Esto proporciona una mayor flexibilidad para las empresas que están en expansión o que manejan diferentes tipos de productos a lo largo del tiempo.
En términos de mantenimiento, las cabinas continuas están equipadas con sistemas de autodiagnóstico y sensores inteligentes que pueden identificar problemas antes de que se conviertan en fallos graves. Esto permite a los operarios realizar un mantenimiento preventivo de manera más eficiente, lo que reduce los tiempos de inactividad y evita costosos reparos no planificados. Además, las cabinas están diseñadas para facilitar el acceso a los componentes clave, lo que hace que las tareas de mantenimiento sean más rápidas y seguras.
En el contexto de la sostenibilidad, las cabinas continuas para pintura en polvo se alinean con las tendencias de la industria que buscan procesos de producción más respetuosos con el medio ambiente. La pintura en polvo no contiene disolventes ni compuestos orgánicos volátiles (COV), lo que reduce significativamente la emisión de contaminantes en el aire. Además, el reciclaje del polvo no utilizado permite una mayor eficiencia de los recursos, disminuyendo la cantidad de residuos generados en el proceso. A medida que las regulaciones ambientales se vuelven más estrictas, las empresas que adoptan estas tecnologías se benefician no solo de la reducción de su impacto ambiental, sino también de una mejora en su imagen corporativa y cumplimiento normativo.
Otra área de crecimiento es la integración de las cabinas continuas con otros sistemas automatizados dentro de la planta de producción, como robots de carga y descarga, sistemas de visión artificial y controles de calidad en línea. Estas integraciones permiten una producción más fluida, eficiente y precisa, donde el proceso completo de recubrimiento se gestiona con mínima intervención humana. Además, la automatización puede reducir el riesgo de errores causados por la variabilidad humana, lo que se traduce en una mayor calidad y consistencia de los productos finales.
A medida que las industrias buscan procesos más inteligentes y eficientes, la investigación y el desarrollo en torno a las cabinas continuas para pintura en polvo continúan avanzando. Los fabricantes están explorando tecnologías como la pintura en polvo con aditivos especiales, que proporcionan propiedades mejoradas como mayor resistencia al desgaste, mejor protección contra la corrosión o efectos estéticos mejorados. La mejora de la tecnología de pistolas electrostáticas, por ejemplo, ha permitido una aplicación más precisa y eficiente del polvo, lo que resulta en un acabado más uniforme y una mayor tasa de transferencia de pintura, reduciendo así el desperdicio de material.
El futuro de las cabinas continuas para pintura en polvo parece muy prometedor, ya que continúan evolucionando hacia sistemas más rápidos, precisos y sostenibles. Las mejoras en la tecnología y la integración con otros procesos de fabricación permitirán a las empresas no solo mantener su competitividad, sino también satisfacer la creciente demanda de productos de alta calidad y bajo impacto ambiental. Por lo tanto, estas cabinas no solo están revolucionando la industria de recubrimientos, sino que también están marcando el camino hacia un futuro más eficiente y ecológico en la producción industrial.
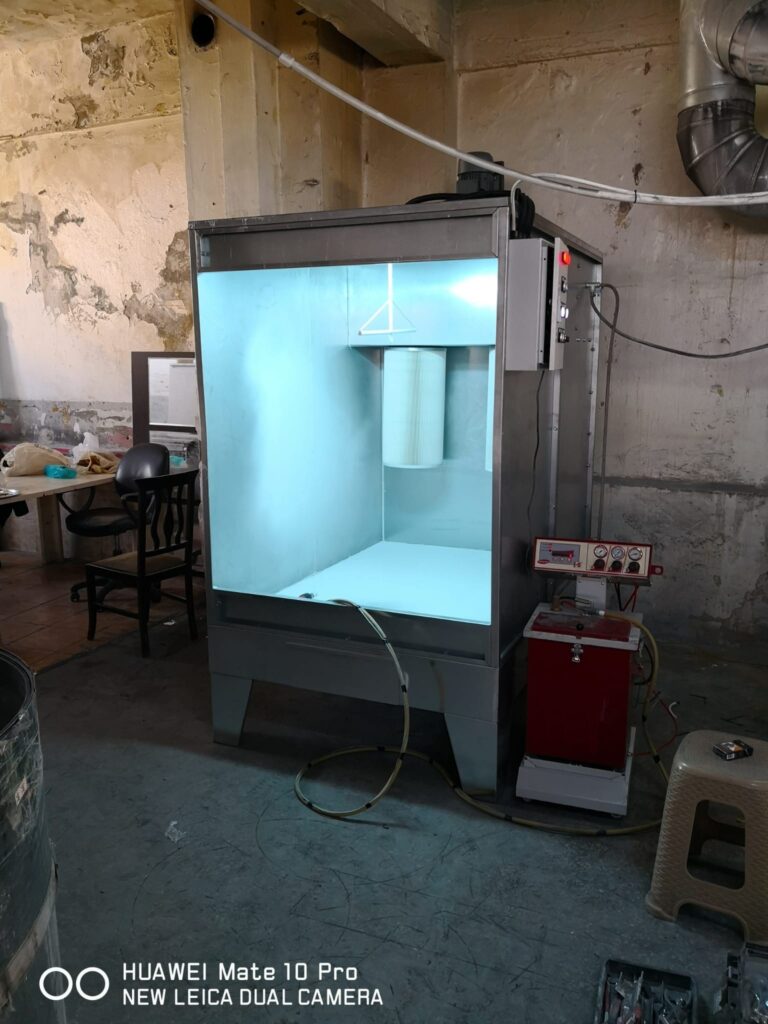
A medida que el mercado global de fabricación continúa evolucionando, las cabinas continuas para pintura en polvo están adaptándose a nuevas demandas, impulsadas por la globalización y los avances en la tecnología de producción. El aumento de la personalización de los productos ha llevado a una mayor variedad en los diseños y acabados, lo que, a su vez, ha elevado los requisitos de flexibilidad y precisión en el proceso de pintura. Las cabinas continuas están diseñadas para manejar estas demandas mediante la implementación de software avanzado de control de procesos, que puede personalizar las configuraciones de pintura para cada lote de producción, garantizando acabados únicos según las especificaciones del cliente.
Esta capacidad de personalización es especialmente importante en sectores como el de la automoción, donde la calidad de la pintura, junto con los acabados estéticos y las propiedades de protección de la superficie, es un aspecto crucial. Las cabinas continuas permiten la aplicación de capas finas y uniformes de pintura, que es fundamental para lograr una excelente durabilidad y resistencia a factores ambientales como la corrosión, la radiación ultravioleta (UV) y la abrasión. Además, el uso de diferentes tipos de polvo, como los que tienen propiedades especiales de resistencia a temperaturas extremas o características antideslizantes, amplía aún más las aplicaciones de estas cabinas en industrias especializadas.
El avance hacia la “Industria 4.0” también está afectando la manera en que se gestionan y operan las cabinas continuas para pintura en polvo. La digitalización de los procesos de producción, el uso de sensores IoT (Internet de las Cosas) y la integración con sistemas de análisis de datos y aprendizaje automático (machine learning) han permitido que los procesos sean más inteligentes y autónomos. Los sensores instalados en las cabinas pueden monitorizar constantemente factores como la temperatura, la velocidad del flujo de aire, la cantidad de pintura aplicada y la calidad del acabado. Con el análisis de estos datos, los operadores pueden predecir problemas potenciales antes de que ocurran y realizar ajustes en tiempo real para optimizar la producción.
El uso de inteligencia artificial y algoritmos de optimización también puede mejorar aún más la eficiencia operativa de las cabinas continuas. Por ejemplo, los sistemas inteligentes pueden predecir las variaciones en la calidad del polvo y ajustar automáticamente los parámetros de pulverización para mantener una consistencia óptima. Esto reduce la intervención humana, minimiza los errores operativos y garantiza un acabado constante en toda la línea de producción. También, la gestión eficiente del polvo reciclado mediante estos sistemas inteligentes no solo reduce los costos de materiales, sino que también mejora la sostenibilidad general del proceso.
Una de las tendencias emergentes en la industria de la pintura en polvo es el aumento de la demanda de soluciones de recubrimiento más ecológicas. Las cabinas continuas para pintura en polvo juegan un papel esencial en este aspecto, al eliminar el uso de disolventes y productos químicos nocivos para el medio ambiente, que suelen estar presentes en los recubrimientos líquidos convencionales. Además, la capacidad de reciclar el polvo sobrante y minimizar los desechos contribuye a la economía circular, un modelo de negocio sostenible que se está implementando en diversas industrias. Este tipo de enfoque también favorece a las empresas que buscan cumplir con las estrictas regulaciones ambientales que se están implementando a nivel mundial.
El futuro también apunta a la mejora continua de la eficiencia energética de las cabinas continuas. El curado de la pintura es una de las etapas más intensivas en energía del proceso de pintura en polvo, por lo que los avances en la tecnología de hornos, como la incorporación de sistemas de curado por infrarrojos o la optimización de la temperatura y el tiempo de curado mediante controles automatizados, pueden generar ahorros significativos de energía. Esto no solo beneficia a las empresas en términos de costos operativos, sino que también reduce su huella de carbono, alineándose con las crecientes expectativas de sostenibilidad.
Además, la integración de la robótica en las cabinas de pintura en polvo está aumentando. Los robots pueden automatizar tareas como la manipulación de las piezas, la carga y descarga de productos y la limpieza de las pistolas de pulverización. Los robots colaborativos (cobots) están siendo cada vez más utilizados en entornos de producción, ya que pueden trabajar de manera conjunta con los operarios, optimizando el flujo de trabajo y mejorando la ergonomía y la seguridad de los trabajadores. Esta combinación de robótica, automatización y procesos de control inteligente está llevando a las cabinas continuas para pintura en polvo a una nueva era de eficiencia y productividad.
En cuanto a la seguridad, las cabinas continuas se están equipando con sistemas avanzados de protección contra incendios y monitoreo de calidad del aire. Aunque la pintura en polvo es menos inflamable que los recubrimientos líquidos, sigue siendo fundamental garantizar que no haya acumulación de polvo combustible en el entorno de trabajo. Los sistemas de detección de chispas y los sistemas de extinción automáticos, junto con el monitoreo constante de la calidad del aire para detectar cualquier presencia de polvo suspendido, contribuyen a crear un ambiente de trabajo más seguro para los operarios.
Por último, el enfoque hacia la digitalización y la conectividad está permitiendo que las cabinas continuas para pintura en polvo se integren en redes de producción inteligentes. Estos sistemas pueden compartir datos con otras máquinas y procesos dentro de la planta de fabricación, lo que permite una mejor planificación, control y trazabilidad de la producción. Al tener acceso a datos detallados sobre el rendimiento de la cabina, los responsables de producción pueden tomar decisiones informadas sobre el mantenimiento, el uso de materiales y la mejora de la calidad.
En resumen, las cabinas continuas para pintura en polvo están evolucionando constantemente gracias a las innovaciones tecnológicas, la automatización y la digitalización. Estas mejoras no solo optimizan la eficiencia operativa y reducen costos, sino que también contribuyen a la sostenibilidad ambiental y la seguridad en el lugar de trabajo. Con una mayor capacidad de personalización, un enfoque más ecológico y una integración cada vez más profunda con la Industria 4.0, las cabinas continuas para pintura en polvo siguen siendo una parte esencial de la manufactura moderna y desempeñarán un papel clave en el futuro de la producción industrial.
Cabinas para Pintura en Polvo
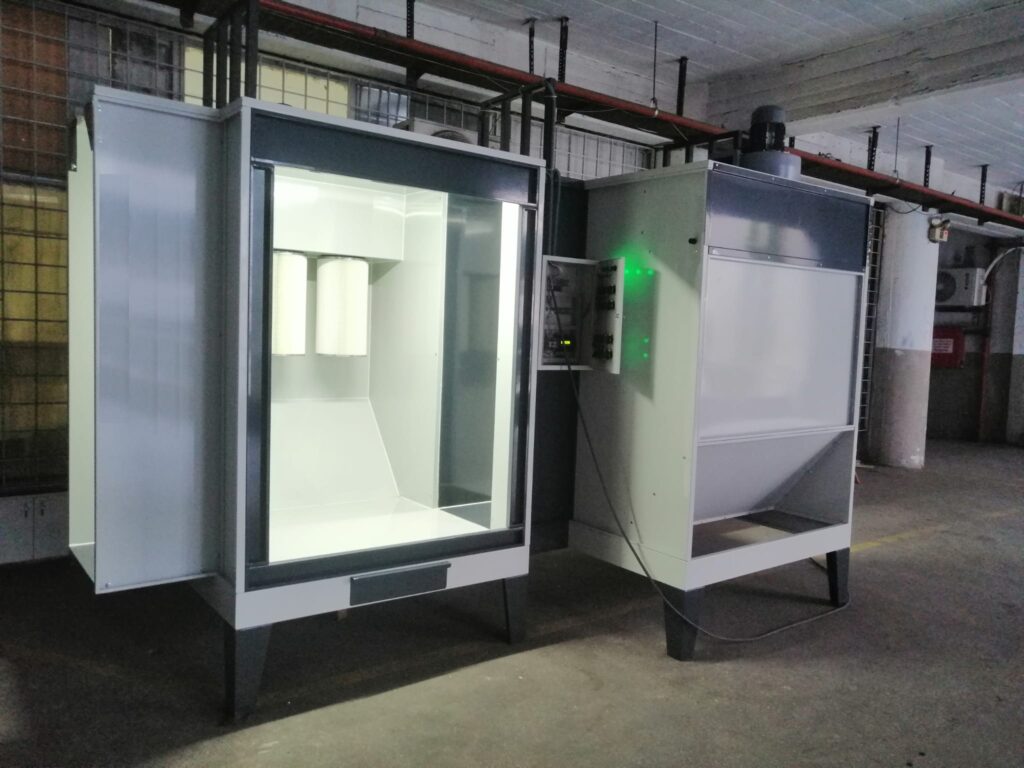
Las cabinas para pintura en polvo son sistemas altamente especializados que se utilizan en la aplicación de recubrimientos en polvo sobre diversas superficies, como metales, plásticos y otros materiales. Estos sistemas se destacan por su eficiencia, versatilidad y sostenibilidad, lo que los convierte en una opción preferida en múltiples industrias, incluyendo la automotriz, la fabricación de electrodomésticos, la industria del mueble y muchas otras. A diferencia de los métodos de pintura líquidos tradicionales, las cabinas para pintura en polvo operan utilizando polvo de pintura que es electrostáticamente cargado, permitiendo que se adhiera de manera eficiente y uniforme a las superficies de las piezas.
El funcionamiento básico de una cabina para pintura en polvo se basa en la aplicación del recubrimiento mediante pistolas electrostáticas. Estas pistolas cargan las partículas de polvo de pintura con una carga negativa, lo que las hace adherirse a las superficies de las piezas, que generalmente están conectadas a tierra, lo que les da una carga positiva. Este proceso de electrostática asegura que la pintura se distribuya uniformemente, proporcionando un acabado suave y duradero. El polvo sobrante no utilizado puede ser recolectado y reciclado, lo que contribuye a una mayor eficiencia en el uso de los materiales.
Las cabinas para pintura en polvo tienen un diseño cerrado que minimiza la dispersión de polvo en el ambiente, asegurando tanto la calidad del recubrimiento como la seguridad de los operarios. Estas cabinas están equipadas con sistemas de ventilación y filtración que capturan el polvo en exceso, evitando que se liberen partículas al aire. Estos sistemas de filtrado de alta eficiencia ayudan a mantener el ambiente limpio y cumplen con las regulaciones ambientales al reducir las emisiones de polvo y otros contaminantes. Además, muchos de estos sistemas de filtrado son reutilizables, lo que mejora la sostenibilidad del proceso.
Una de las principales ventajas de las cabinas para pintura en polvo es su capacidad para ofrecer una alta calidad en el acabado de las piezas, ya que el recubrimiento es más uniforme y duradero que en los métodos tradicionales de pintura líquida. La pintura en polvo tiene una mayor resistencia a factores como la corrosión, la abrasión, las manchas y los daños por exposición a los rayos UV. Esto la convierte en una opción ideal para aplicaciones industriales y productos que deben resistir condiciones extremas.
El proceso de aplicación en las cabinas para pintura en polvo también tiene importantes ventajas en términos de eficiencia operativa y ahorro de recursos. Dado que el polvo sobrante puede ser reciclado, el desperdicio de material es mínimo. Esto no solo reduce los costos de producción, sino que también contribuye a la reducción de desechos, lo que hace que este proceso sea más sostenible desde el punto de vista ambiental. Además, las cabinas para pintura en polvo son más eficientes energéticamente que los sistemas tradicionales de pintura líquida, ya que no requieren el uso de solventes y los hornos de curado pueden ser diseñados para utilizar menos energía.
El proceso de curado, que es fundamental para que el recubrimiento de polvo se adhiera correctamente a las piezas, generalmente se lleva a cabo en un horno de curado. El horno calienta las piezas a una temperatura controlada, que permite que la pintura en polvo se derrita y se fusione, creando una capa dura y resistente. Las cabinas para pintura en polvo están diseñadas para garantizar que este proceso de curado se realice de manera eficiente, con la temperatura y el tiempo controlados para obtener el mejor acabado posible.
A nivel de mantenimiento, las cabinas para pintura en polvo son sistemas relativamente fáciles de mantener, pero requieren atención regular para garantizar un funcionamiento óptimo. Los filtros deben limpiarse o reemplazarse periódicamente para mantener la eficacia del sistema de recolección de polvo. También es importante realizar un mantenimiento de las pistolas de pulverización y verificar el funcionamiento de los sistemas de ventilación y recirculación de aire. Este mantenimiento regular ayuda a evitar fallos en el equipo y garantiza la calidad constante del recubrimiento.
En términos de seguridad, las cabinas para pintura en polvo están equipadas con varias medidas para proteger a los operarios. Aunque la pintura en polvo no es inflamable de manera significativa, las cabinas están diseñadas con sistemas de ventilación adecuados para evitar la acumulación de polvo combustible en el aire. También se utilizan sistemas de filtrado avanzados para eliminar el polvo que no se utiliza, lo que reduce los riesgos asociados con la exposición a altas concentraciones de partículas finas en el ambiente de trabajo.
Una característica importante de las cabinas para pintura en polvo es su flexibilidad en cuanto a las aplicaciones y el tipo de piezas que pueden pintar. Estas cabinas pueden adaptarse para manejar piezas de diferentes tamaños y formas, lo que las hace ideales para una amplia variedad de industrias. Por ejemplo, en la industria automotriz, las cabinas para pintura en polvo son utilizadas para recubrir tanto piezas grandes, como partes del chasis de los vehículos, como piezas pequeñas y complejas, como los componentes de los sistemas eléctricos.
La versatilidad de las cabinas para pintura en polvo también se extiende a la gama de acabados que pueden producir. El polvo utilizado en las cabinas puede variar en función de las necesidades del cliente, incluyendo opciones como recubrimientos mate, brillantes, texturizados o con efectos especiales. Además, algunos recubrimientos en polvo pueden tener propiedades adicionales, como resistencia a altas temperaturas, resistencia a productos químicos o propiedades antimicrobianas, lo que las hace útiles en una amplia gama de aplicaciones industriales.
En cuanto a la sostenibilidad, las cabinas para pintura en polvo son una opción respetuosa con el medio ambiente en comparación con los métodos de pintura líquidos tradicionales. La eliminación de solventes y compuestos volátiles orgánicos (COV) en la pintura en polvo contribuye a la reducción de las emisiones tóxicas, mejorando la calidad del aire y reduciendo el impacto ambiental del proceso de pintura. Además, la posibilidad de reciclar el polvo sobrante contribuye a la economía circular y reduce la necesidad de adquirir materiales nuevos constantemente.
En resumen, las cabinas para pintura en polvo representan una solución avanzada y eficiente para la aplicación de recubrimientos en diversas industrias. Gracias a su capacidad para ofrecer un acabado uniforme, duradero y de alta calidad, junto con sus ventajas en términos de eficiencia de materiales, energía y sostenibilidad, estas cabinas están ganando terreno frente a los sistemas de pintura líquida tradicionales. Con la continua evolución de la tecnología y las mejoras en el diseño de las cabinas y los sistemas de control, el futuro de la pintura en polvo promete ser aún más eficiente, flexible y respetuoso con el medio ambiente.
Además de las ventajas previamente mencionadas, las cabinas para pintura en polvo están experimentando avances tecnológicos que amplían aún más sus capacidades y aplicaciones. La integración de tecnologías de automatización y control inteligente está permitiendo que estas cabinas sean más eficientes, precisas y fáciles de operar. La implementación de sistemas de monitoreo digital, que permiten un seguimiento en tiempo real de los parámetros críticos del proceso, como la cantidad de polvo aplicado, la velocidad de las piezas y las condiciones de curado, mejora la consistencia y calidad del recubrimiento.
Los sistemas de control avanzados pueden ajustar automáticamente los parámetros operativos en función de los cambios en las condiciones de producción, lo que optimiza los tiempos de ciclo y mejora la eficiencia general. Esto permite que las cabinas para pintura en polvo se adapten a diferentes tipos de piezas o variaciones en el proceso de fabricación sin necesidad de intervención manual frecuente, lo que reduce la posibilidad de errores humanos y mejora la capacidad de respuesta a las demandas del mercado.
La integración con robots y otros sistemas automatizados también ha mejorado la capacidad de las cabinas para manejar una mayor variedad de piezas y tamaños, así como la velocidad de producción. Los robots colaborativos (cobots), que trabajan junto con los operarios, son capaces de realizar tareas de manipulación, carga y descarga de piezas, lo que no solo aumenta la productividad, sino que también mejora la ergonomía en el lugar de trabajo. Además, los robots pueden realizar estas tareas de manera constante y precisa, lo que asegura que las piezas estén correctamente alineadas para la aplicación del polvo y optimiza el proceso de recubrimiento.
El uso de sensores avanzados en las cabinas también permite la mejora en el reciclaje del polvo. Los sensores pueden detectar el exceso de polvo y ajustan la cantidad que se recircula para asegurar un proceso de pintura más eficiente. Esto también reduce el desperdicio de material y ayuda a minimizar los costos operativos a largo plazo. Los sistemas de reciclaje de polvo, que recuperan y reutilizan el material no aplicado, se han perfeccionado para aumentar su efectividad, lo que no solo mejora la eficiencia, sino que también reduce el impacto ambiental al minimizar la cantidad de polvo desperdiciado.
Otra tendencia en la evolución de las cabinas para pintura en polvo es la mejora en los sistemas de curado. Los avances en la tecnología de hornos de curado, como los hornos de infrarrojos o los de curado rápido, están permitiendo una mayor eficiencia energética. Estos hornos utilizan menos energía y alcanzan las temperaturas necesarias para el curado de la pintura en menos tiempo, lo que reduce el consumo de energía y los tiempos de producción. Este tipo de hornos también es más respetuoso con el medio ambiente, ya que generan menos emisiones y desperdicio.
La personalización de los recubrimientos es otro aspecto en el que las cabinas para pintura en polvo están avanzando. La capacidad de utilizar diferentes tipos de polvo con propiedades específicas, como recubrimientos con mayor resistencia al desgaste, recubrimientos de alta temperatura o acabados estéticos especiales, está permitiendo a las empresas satisfacer una amplia variedad de requisitos. Esto es especialmente importante en industrias como la automotriz, la aeroespacial y la fabricación de maquinaria, donde los productos deben cumplir con especificaciones técnicas rigurosas y, al mismo tiempo, mantener altos estándares estéticos.
En el contexto de la sostenibilidad, las cabinas para pintura en polvo continúan siendo una de las opciones más respetuosas con el medio ambiente. La reducción de la emisión de compuestos orgánicos volátiles (COV) es uno de los principales beneficios ambientales de este proceso de recubrimiento. El uso de pintura en polvo elimina la necesidad de disolventes, lo que reduce significativamente las emisiones de sustancias químicas nocivas y mejora la calidad del aire en el entorno de trabajo.
El diseño modular de las cabinas para pintura en polvo también está ganando popularidad, ya que permite a las empresas adaptar sus sistemas de pintura a sus necesidades específicas. Las cabinas modulares pueden ser ampliadas o modificadas fácilmente para ajustarse a las demandas cambiantes de producción. Este enfoque modular también facilita la integración de nuevas tecnologías y actualizaciones sin necesidad de reemplazar completamente el sistema de pintura, lo que hace que las cabinas para pintura en polvo sean una inversión a largo plazo.
El monitoreo y control de la calidad en tiempo real también se ha vuelto cada vez más accesible gracias a la integración de sistemas de visión artificial y análisis de datos. Las cámaras y sensores de visión artificial pueden verificar el acabado de las piezas mientras son pintadas, asegurando que cumplan con los estándares de calidad establecidos. Estos sistemas también pueden detectar defectos en el recubrimiento, como irregularidades en la capa de pintura, y notificar a los operarios para que tomen medidas correctivas inmediatamente. Esto no solo mejora la calidad del producto final, sino que también reduce el desperdicio al evitar que piezas defectuosas lleguen a la etapa de curado.
Además, el avance en los sistemas de ventilación y filtración ha permitido que las cabinas para pintura en polvo sean más eficientes en la recolección de partículas finas de polvo. Los nuevos filtros HEPA y sistemas de recolección están diseñados para garantizar que el polvo no se disperse en el aire, reduciendo los riesgos de exposición para los trabajadores y mejorando las condiciones de trabajo en general. Esto también contribuye al cumplimiento de las normativas de seguridad y medioambientales, asegurando que las empresas operen dentro de los estándares requeridos.
En términos de economía, las cabinas para pintura en polvo siguen siendo una opción atractiva debido a su eficiencia en el uso de recursos y su capacidad para reducir los costos de operación. La posibilidad de reciclar el polvo y la reducción de desperdicios permite a las empresas minimizar la cantidad de materiales utilizados, lo que resulta en un ahorro significativo a largo plazo. Además, la eficiencia energética de los sistemas de curado y la reducción del tiempo de producción también contribuyen a una reducción de los costos operativos.
Finalmente, las cabinas para pintura en polvo están evolucionando para ofrecer soluciones aún más sostenibles, eficientes y flexibles. Con avances en automatización, reciclaje de materiales, curado eficiente, personalización y control de calidad, estos sistemas están transformando la industria de la pintura y recubrimientos. Las empresas que adoptan estas tecnologías se benefician de una mayor productividad, menores costos operativos, productos de alta calidad y un impacto ambiental reducido, lo que las posiciona para competir de manera más eficaz en un mercado global cada vez más exigente y orientado hacia la sostenibilidad.
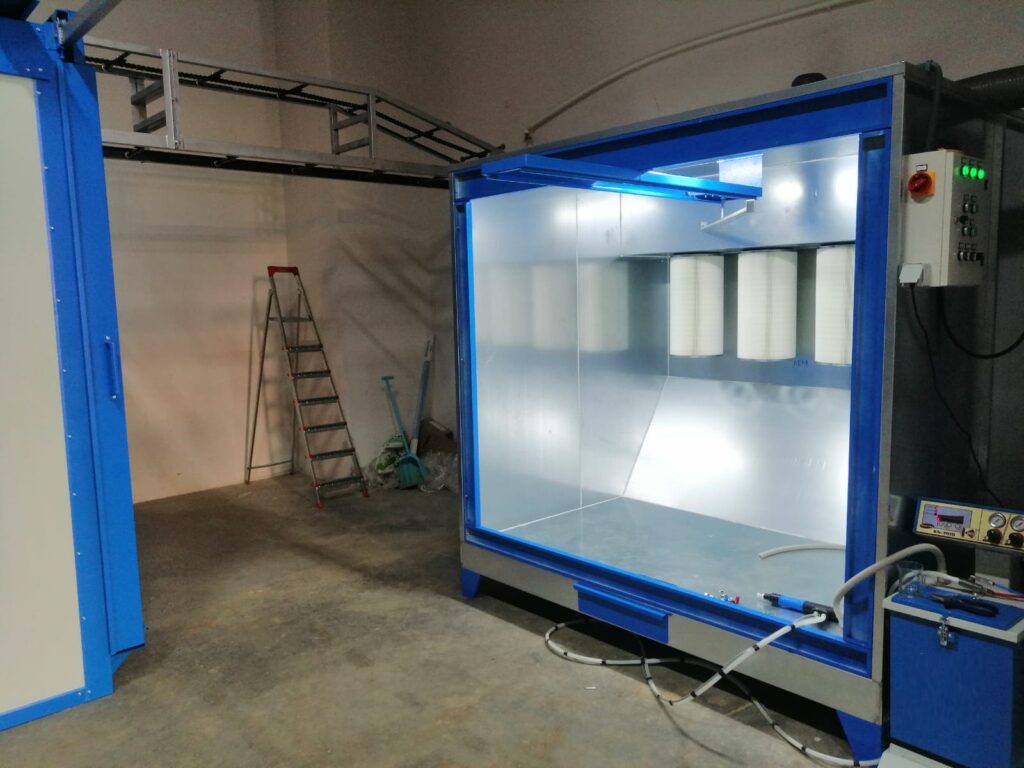
El futuro de las cabinas para pintura en polvo sigue orientándose hacia la innovación y la optimización de cada uno de los procesos involucrados. La integración de la inteligencia artificial (IA) y el aprendizaje automático (machine learning) está abriendo nuevas posibilidades para mejorar la eficiencia y la calidad del recubrimiento, así como para predecir y prevenir posibles fallos en el sistema. Estos avances en la tecnología permitirán a las cabinas para pintura en polvo adaptarse a condiciones cambiantes de producción de manera más inteligente, previendo necesidades de mantenimiento antes de que se presenten problemas graves y ajustando los parámetros en tiempo real para garantizar siempre la mejor calidad.
Por ejemplo, el uso de algoritmos de IA puede predecir las variaciones en la calidad del recubrimiento debido a factores como la humedad o la temperatura ambiente, y ajustar automáticamente los parámetros de pulverización, curado y velocidad para mantener una consistencia perfecta. Este tipo de optimización también puede ayudar a reducir el consumo de materiales al evitar la sobreaplicación de polvo y asegurar que se utilicen solo las cantidades necesarias.
A su vez, la implementación de tecnologías de big data está transformando la forma en que se gestionan los datos generados por las cabinas para pintura en polvo. Al recopilar y analizar grandes volúmenes de datos sobre cada proceso, las empresas pueden identificar patrones y tendencias, lo que les permite mejorar el control de calidad, optimizar el uso de los recursos y reducir el tiempo de inactividad de la maquinaria. Este enfoque de gestión de datos también facilita la trazabilidad completa de las piezas pintadas, lo que es esencial en industrias como la automotriz y la aeroespacial, donde la precisión y la calidad son fundamentales.
Los avances en las tecnologías de ventilación y filtrado también seguirán mejorando en el futuro, aumentando la eficacia de los sistemas de captación de polvo y reduciendo aún más los riesgos asociados con la acumulación de partículas peligrosas. Además, los filtros más avanzados y eficientes podrían prolongar la vida útil de los sistemas de ventilación, reduciendo los costos de mantenimiento y aumentando la eficiencia general de las cabinas.
La sostenibilidad seguirá siendo un factor clave en la evolución de las cabinas para pintura en polvo. Las regulaciones medioambientales más estrictas, combinadas con un aumento en la conciencia global sobre el impacto del cambio climático, están impulsando el desarrollo de soluciones más ecológicas. En el futuro, podríamos ver el uso de tecnologías de recubrimiento aún más sostenibles, como pinturas en polvo basadas en materiales reciclados o biodegradables, y la integración de tecnologías de captura de carbono en el proceso de pintura para reducir aún más la huella de carbono de la industria.
Además, la creciente presión para reducir el uso de recursos naturales y mejorar la eficiencia de los procesos de producción llevará a las cabinas para pintura en polvo a incorporar fuentes de energía renovables. El uso de energía solar o eólica para alimentar los hornos de curado y otros sistemas de la cabina podría convertirse en una práctica común, ayudando a las empresas a reducir su consumo energético y a operar de manera más sostenible.
En términos de ergonomía y seguridad laboral, las cabinas para pintura en polvo están adoptando cada vez más tecnologías que mejoran la experiencia de trabajo para los operarios. Los sistemas de realidad aumentada (AR) y realidad virtual (VR) están comenzando a utilizarse en los entrenamientos y mantenimiento de las cabinas, permitiendo que los operarios reciban instrucciones visuales y simulen escenarios de trabajo de manera segura antes de enfrentarse a ellos en el mundo real. Además, los sistemas de monitoreo de salud y seguridad basados en sensores biométricos podrían ayudar a los empleadores a garantizar que los trabajadores estén operando dentro de límites seguros en todo momento, minimizando los riesgos de exposición al polvo y otros peligros.
La conectividad también jugará un papel crucial en el futuro de las cabinas para pintura en polvo. La adopción de la tecnología 5G y otras soluciones de conectividad de alta velocidad permitirá que las cabinas estén más interconectadas dentro de la planta de producción, facilitando la comunicación en tiempo real entre diferentes sistemas de producción y mejorando la colaboración entre departamentos. Este nivel de conectividad permitirá a las empresas mejorar la trazabilidad de los productos, gestionar el inventario de manera más eficiente y realizar ajustes en el proceso de pintura desde cualquier ubicación, mejorando la flexibilidad y la agilidad operativa.
El diseño modular, que ya es una tendencia popular en las cabinas para pintura en polvo, también evolucionará hacia configuraciones aún más personalizables. Las cabinas modulares podrán integrarse más fácilmente con otros sistemas de producción, y las empresas podrán ajustar su tamaño, capacidad y características según las necesidades cambiantes del mercado. Esto permitirá a las fábricas de producción escalar rápidamente sus operaciones o adaptarse a nuevas demandas de productos sin necesidad de realizar inversiones significativas en nuevos equipos.
Además, con el aumento de la demanda de personalización de productos, las cabinas para pintura en polvo podrían estar equipadas con sistemas avanzados de personalización de acabados. Por ejemplo, las cabinas podrían incorporar tecnologías que permiten cambiar rápidamente entre diferentes tipos de polvo, colores o acabados, lo que sería ideal para la producción de lotes pequeños o para aplicaciones que requieran una atención especial al detalle, como en la industria de la moda o en la fabricación de dispositivos electrónicos de consumo.
Por último, el enfoque hacia la reducción de los costos operativos seguirá impulsando la adopción de tecnologías de bajo mantenimiento y fácil operación. Las cabinas para pintura en polvo podrían integrar sistemas de autodiagnóstico que alerten a los operarios sobre posibles fallos antes de que afecten a la producción, lo que reducirá los tiempos de inactividad y mejorará la eficiencia general de la planta. Asimismo, la incorporación de tecnologías de mantenimiento predictivo permitirá a las empresas planificar con anticipación las intervenciones de mantenimiento, evitando costosos paros no planificados y extendiendo la vida útil de las cabinas.
En resumen, el futuro de las cabinas para pintura en polvo está marcado por un enfoque hacia la eficiencia, sostenibilidad, flexibilidad y tecnología avanzada. Las empresas que adopten estas innovaciones podrán no solo mejorar su rendimiento operativo, sino también satisfacer las demandas del mercado actual, cada vez más centrado en la calidad, la personalización y el respeto por el medio ambiente. Las cabinas para pintura en polvo seguirán siendo una parte esencial de la fabricación moderna, evolucionando para enfrentar los desafíos de un mundo industrial cada vez más automatizado y sostenible.
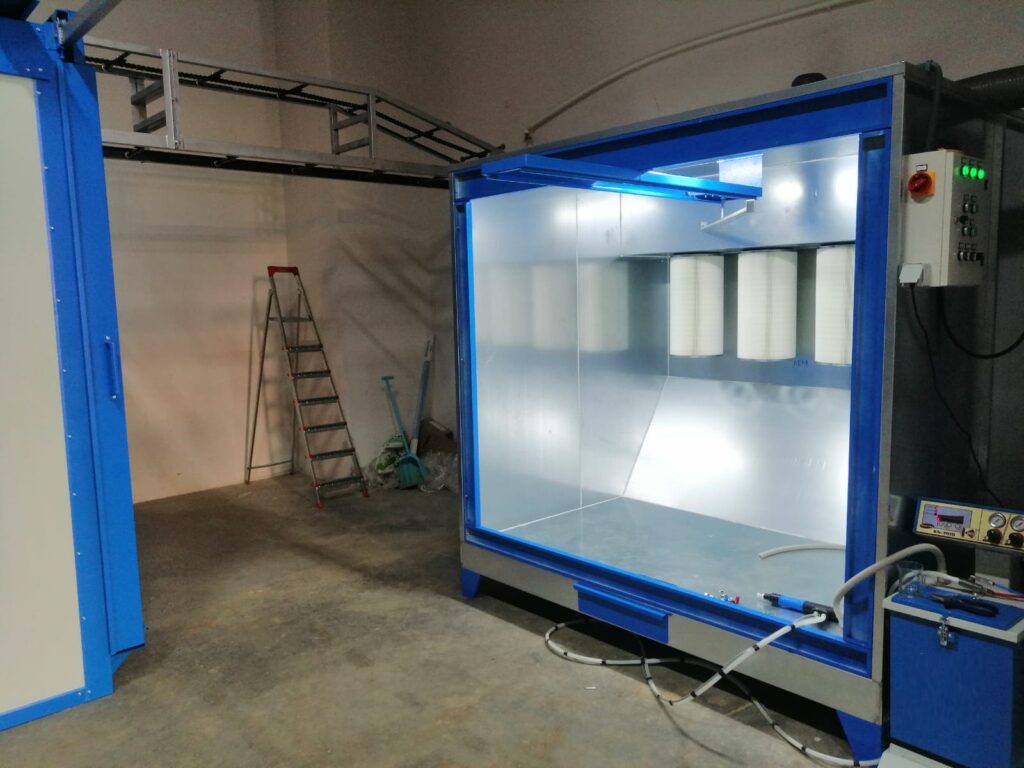
En el futuro, también se prevé una evolución en la forma en que las cabinas para pintura en polvo se integran dentro de los sistemas de producción más amplios. La industria 4.0, caracterizada por la automatización avanzada, el internet de las cosas (IoT), y el intercambio de datos en tiempo real, transformará las cabinas de pintura en parte esencial de una planta de producción inteligente. A medida que las cabinas para pintura en polvo se conecten con otros dispositivos y maquinaria en la línea de producción, se podrán coordinar con precisión los tiempos de ciclo, el flujo de materiales, y los cambios en la demanda de productos.
El uso del IoT en las cabinas permitirá que estos sistemas se comuniquen entre sí y con las plataformas de gestión de producción. Los sensores instalados en las cabinas pueden monitorear variables clave, como la temperatura, la humedad y la presión, para garantizar que el proceso de pintura se realice dentro de los parámetros óptimos. Además, estos sensores pueden enviar datos a una plataforma centralizada, donde los analistas pueden supervisar el rendimiento de la cabina, detectar patrones inusuales y realizar ajustes en tiempo real para mantener la calidad y la eficiencia.
Con el avance del IoT, los operarios podrán recibir información instantánea sobre el estado de las cabinas, como el nivel de polvo disponible, el estado de los filtros o si se requieren tareas de mantenimiento, sin necesidad de inspección manual constante. Esta conectividad no solo facilita la gestión remota, sino que también permite a los operarios estar más enfocados en la supervisión general del proceso y en la resolución de problemas, en lugar de realizar tareas repetitivas de monitoreo.
La evolución de la conectividad también permitirá una mayor personalización de las cabinas para pintura en polvo en función de las necesidades de los clientes. Por ejemplo, los sistemas podrían ajustarse automáticamente para adaptarse a diferentes tipos de recubrimientos o cambios en los procesos de producción, lo que brindaría a las empresas una flexibilidad mucho mayor en sus operaciones. Estos avances permitirán a las cabinas para pintura en polvo adaptarse rápidamente a los requisitos específicos de cada proyecto, sin necesidad de rediseñar todo el sistema.
Otra tendencia que se está consolidando es la adopción de la simulación y modelado digital para la optimización de las cabinas. El uso de gemelos digitales, representaciones virtuales de las cabinas de pintura, permitirá a los ingenieros y operadores predecir el comportamiento del sistema en diferentes condiciones y realizar ajustes sin interrumpir la producción. Esto también facilitará el diseño de nuevas cabinas, ya que las simulaciones podrán predecir su rendimiento antes de su implementación física, reduciendo el tiempo de desarrollo y optimizando los costos.
Por otro lado, el concepto de economía circular, cada vez más importante en el ámbito industrial, también impactará el diseño y operación de las cabinas para pintura en polvo. En lugar de simplemente enfocarse en la eficiencia de la producción y el reciclaje del polvo sobrante, se buscará un enfoque integral para maximizar el aprovechamiento de todos los recursos involucrados en el proceso. Las cabinas podrían integrarse con sistemas de gestión de residuos más eficientes, que no solo reciclen el polvo sobrante, sino también otros materiales utilizados en el proceso, como los filtros, los componentes del sistema de ventilación y otros elementos consumibles. Además, los materiales reciclados o reutilizados podrían ser procesados y reincorporados en el ciclo de producción de manera más eficiente.
Asimismo, las cabinas para pintura en polvo se beneficiarán del desarrollo de nuevos materiales y tecnologías en la industria de recubrimientos. Los avances en la formulación de polvo de pintura permitirán una mayor variedad de colores, acabados y propiedades especiales, como recubrimientos de mayor resistencia al fuego, a la corrosión o incluso a la contaminación. La investigación y el desarrollo de nuevos tipos de polvo pueden permitir aplicaciones más específicas para diversas industrias, ampliando aún más las posibilidades de uso de las cabinas para pintura en polvo.
Además, la creciente conciencia sobre la responsabilidad social corporativa (RSC) y la sostenibilidad obligará a las empresas a adoptar prácticas más transparentes y responsables en todos sus procesos, incluida la pintura en polvo. Las cabinas para pintura en polvo, al ser sistemas más ecológicos que otros métodos de recubrimiento, continuarán ganando popularidad en sectores donde la sostenibilidad es clave. Las empresas podrán demostrar su compromiso con el medio ambiente, no solo al utilizar tecnologías más limpias y reciclables, sino también al garantizar que todo el proceso de producción, desde la aplicación hasta el reciclaje, se realice con la mayor eficiencia posible.
El impacto de la sostenibilidad también se reflejará en la normativa y la legislación que regula el uso de materiales y procesos industriales. Las cabinas para pintura en polvo seguirán evolucionando para cumplir con las estrictas regulaciones medioambientales que se están implementando en todo el mundo. Esto incluirá no solo las restricciones sobre las emisiones de polvo y compuestos tóxicos, sino también en términos de eficiencia energética y el uso de materiales que sean lo menos perjudiciales posible para el medio ambiente.
Por último, las cabinas para pintura en polvo también se beneficiarán de una mayor accesibilidad gracias a los avances en la fabricación aditiva (impresión 3D). Esta tecnología permitirá la creación de piezas personalizadas para los sistemas de pintura, mejorando la eficiencia y reduciendo los costos de producción. La fabricación aditiva también permitirá el desarrollo de nuevas configuraciones para las cabinas, adaptadas a las necesidades específicas de cada cliente y proceso, y facilitando la reparación o sustitución de componentes más rápidamente.
En resumen, el futuro de las cabinas para pintura en polvo está marcado por la innovación continua en áreas como la automatización, la conectividad, la sostenibilidad y la personalización. A medida que la tecnología sigue avanzando, estas cabinas se convertirán en un componente aún más crucial de las fábricas inteligentes, capaces de adaptarse a las demandas del mercado, optimizar la eficiencia y reducir el impacto ambiental. Con el tiempo, las cabinas para pintura en polvo seguirán desempeñando un papel fundamental en la transformación de la industria de recubrimientos, brindando soluciones más eficientes, ecológicas y rentables para las empresas de todo el mundo.
Equipos para Pintura Electrostática
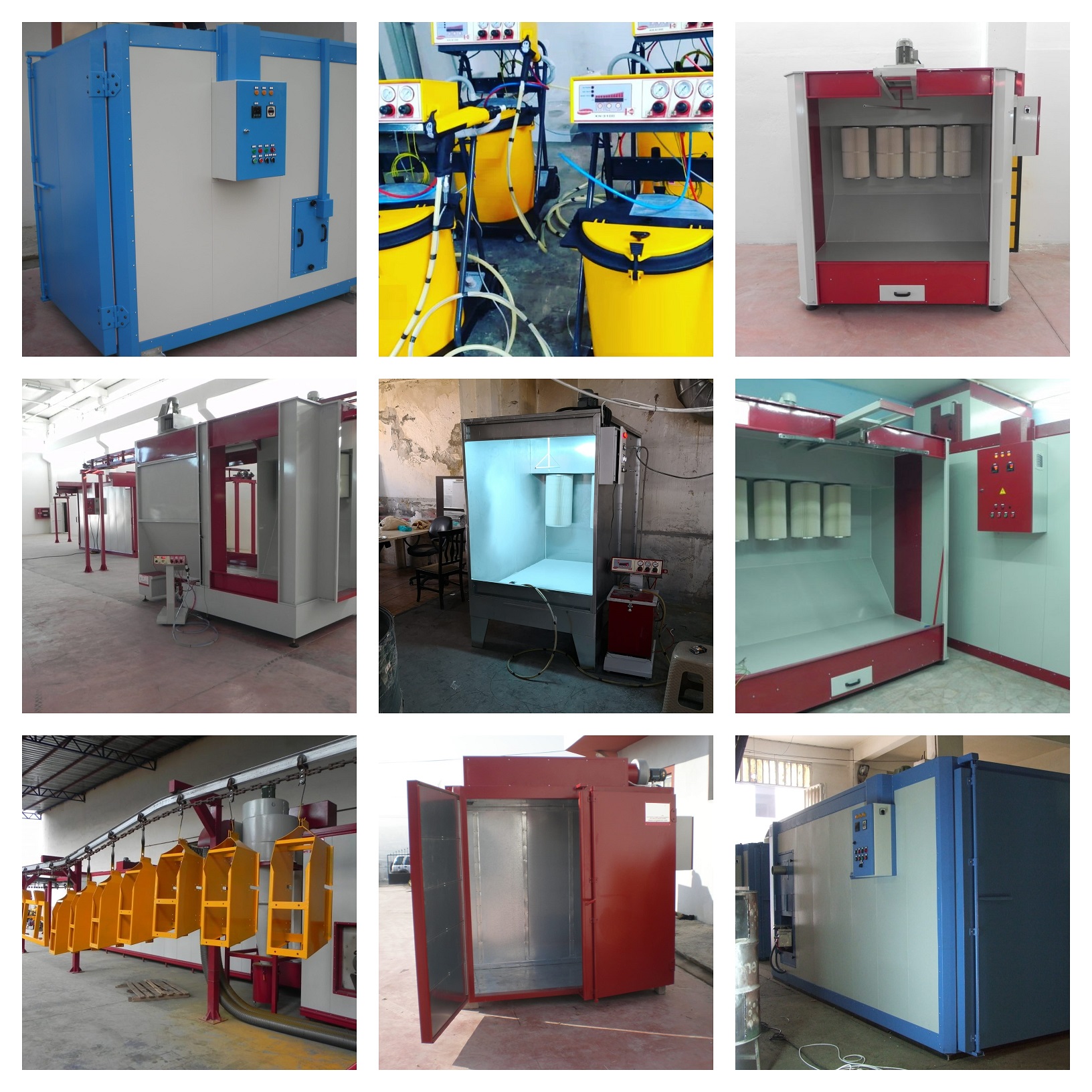
Los equipos para pintura electrostática están evolucionando rápidamente para adaptarse a las demandas de la industria moderna, caracterizada por la eficiencia, la sostenibilidad y la personalización de los productos. Estos sistemas utilizan la fuerza electromagnética para aplicar pintura a una superficie, lo que permite una aplicación más eficiente y precisa, reduciendo el desperdicio de material y mejorando la calidad del recubrimiento. A lo largo de los años, los equipos de pintura electrostática han experimentado avances significativos en tecnología, diseño y control, y continúan siendo una opción preferida en una amplia variedad de industrias, como la automotriz, la electrodoméstica, la metalúrgica y la fabricación de muebles.
Uno de los principales beneficios de la pintura electrostática es su capacidad para ofrecer un acabado uniforme y consistente. La aplicación de pintura se realiza mediante la carga eléctrica del polvo de pintura, lo que asegura que las partículas sean atraídas por la superficie de la pieza a pintar, cubriéndola de manera homogénea. Esto se traduce en una capa de pintura más duradera y resistente, con menos posibilidad de defectos como goteos o irregularidades en la cobertura. Este proceso también permite una mayor eficiencia en el uso del material, ya que la pintura sobrante puede ser recuperada y reutilizada, lo que reduce los costos y el desperdicio.
La tecnología de los equipos para pintura electrostática ha avanzado significativamente en términos de control y automatización. Los sistemas modernos permiten un ajuste preciso de los parámetros operativos, como el voltaje, la velocidad de aplicación y la distancia entre la pistola de pintura y la pieza, lo que garantiza una aplicación de alta calidad en todas las condiciones. Además, la integración con sistemas de monitoreo digital ha facilitado la supervisión en tiempo real de los procesos de pintura, lo que permite realizar ajustes inmediatos y asegurar la calidad del recubrimiento durante toda la producción. Estos sistemas inteligentes pueden detectar variaciones en la calidad de la pintura y hacer correcciones automáticas, mejorando la consistencia y reduciendo los errores humanos.
Uno de los avances más notables en los equipos de pintura electrostática es la mejora en los sistemas de control de polvo. Los sistemas de recirculación de polvo y los filtros avanzados permiten recuperar el polvo que no se ha adherido a la pieza, lo que no solo optimiza el uso del material, sino que también minimiza los riesgos ambientales y mejora la eficiencia operativa. El uso de sistemas de filtración HEPA y otros dispositivos avanzados para capturar partículas finas ha mejorado significativamente la calidad del aire en las plantas de pintura y ha reducido la exposición de los trabajadores a materiales peligrosos. Además, estos sistemas de filtración contribuyen a mantener el ambiente de trabajo más limpio y seguro, lo que es especialmente importante en aplicaciones donde la salud y la seguridad son prioritarias.
La sostenibilidad es otro aspecto clave en el desarrollo de los equipos para pintura electrostática. El proceso de pintura electrostática, al no requerir disolventes líquidos como en la pintura convencional, reduce significativamente la emisión de compuestos orgánicos volátiles (COV), lo que contribuye a una menor contaminación del aire y un menor impacto ambiental. Además, el reciclaje del polvo de pintura sobrante ayuda a reducir el desperdicio de material y mejora la eficiencia del proceso. La industria está adoptando cada vez más normativas estrictas en términos de sostenibilidad, y los fabricantes de equipos para pintura electrostática están respondiendo a esta demanda desarrollando tecnologías más limpias y eficientes.
En cuanto a la eficiencia energética, los equipos de pintura electrostática continúan mejorando en términos de consumo de energía. Los avances en la tecnología de pistolas electrostáticas y los sistemas de curado de la pintura permiten un uso más eficiente de la energía, lo que reduce los costos operativos a largo plazo. Los sistemas de curado, como los hornos de curado rápido y de infrarrojos, están diseñados para alcanzar las temperaturas necesarias en menos tiempo, lo que reduce el consumo de energía y acelera el proceso de producción. Estos hornos también son más respetuosos con el medio ambiente, ya que generan menos emisiones y requieren menos tiempo de funcionamiento.
Otro aspecto relevante en la evolución de los equipos para pintura electrostática es la mejora en la flexibilidad y la capacidad de personalización de los acabados. Con el aumento de la demanda de productos personalizados, los sistemas de pintura electrostática ahora permiten aplicar una amplia variedad de colores y acabados con mayor rapidez y precisión. La capacidad de cambiar rápidamente entre diferentes tipos de polvo y colores, sin necesidad de largos tiempos de limpieza o ajustes, es una ventaja clave para las empresas que requieren flexibilidad en su producción. Además, la mayor variedad de polvo de pintura disponible en el mercado permite a las empresas ofrecer recubrimientos especiales con propiedades mejoradas, como resistencia a la corrosión, a los rayos UV o a temperaturas extremas.
La automatización y la robótica están desempeñando un papel cada vez más importante en los sistemas de pintura electrostática. La integración de robots en las líneas de pintura ha permitido aumentar la eficiencia, reducir los tiempos de ciclo y mejorar la calidad del recubrimiento. Los robots son capaces de realizar movimientos más precisos y consistentes, lo que asegura una cobertura uniforme de las piezas, incluso en geometrías complejas. Además, los robots colaborativos (cobots) están siendo utilizados para trabajar junto con los operarios, facilitando la carga y descarga de piezas, y reduciendo la fatiga laboral y los riesgos de lesiones.
La digitalización y el uso de tecnologías como el Internet de las Cosas (IoT) y la inteligencia artificial (IA) también están transformando la manera en que los equipos de pintura electrostática operan. La integración de sensores y sistemas de monitoreo avanzados permite realizar ajustes automáticos en tiempo real, optimizando el proceso y garantizando la calidad del recubrimiento. La IA también puede predecir patrones de fallos o problemas en el sistema, permitiendo a las empresas realizar un mantenimiento preventivo antes de que ocurra una falla, lo que mejora la fiabilidad y reduce el tiempo de inactividad.
La conectividad de los equipos de pintura electrostática también ha facilitado la gestión remota y el monitoreo a través de plataformas digitales. Los operarios pueden controlar el rendimiento del sistema desde cualquier lugar, lo que mejora la eficiencia y la flexibilidad. Además, la recopilación de datos en tiempo real sobre el proceso de pintura permite a las empresas tomar decisiones informadas sobre el mantenimiento, la mejora de la calidad y la optimización del uso de los recursos.
En cuanto a la personalización de los equipos, los avances en el diseño modular han permitido que los sistemas de pintura electrostática se adapten mejor a las necesidades específicas de cada cliente. Las empresas ahora pueden elegir entre una amplia gama de configuraciones y características para adaptar el equipo a los requisitos de producción y los volúmenes de trabajo. Esta flexibilidad es especialmente valiosa para las empresas que producen lotes pequeños o personalizados de productos, ya que les permite ajustar rápidamente el sistema sin tener que invertir en nuevos equipos costosos.
Finalmente, la integración de sistemas de control de calidad más avanzados ha mejorado la capacidad de los equipos de pintura electrostática para garantizar acabados de alta calidad. Los sistemas de visión artificial y sensores de calidad pueden verificar la uniformidad del recubrimiento, identificar defectos y ajustar automáticamente los parámetros de la pistola para mejorar el acabado. Esto reduce los errores y aumenta la precisión en el proceso de pintura.
En resumen, los equipos para pintura electrostática están en constante evolución, adoptando tecnologías más avanzadas, sostenibles y eficientes. A medida que la industria continúa exigiendo una mayor personalización, flexibilidad y sostenibilidad, los equipos de pintura electrostática se adaptarán para ofrecer soluciones más precisas, rápidas y respetuosas con el medio ambiente. La automatización, el uso de tecnologías avanzadas de control y monitoreo, y la mejora de la eficiencia energética y la sostenibilidad serán los pilares que definan el futuro de estos equipos, haciendo que sigan siendo una herramienta esencial en una amplia gama de industrias.
El futuro de los equipos para pintura electrostática está marcado por una serie de tendencias que no solo mejorarán la eficiencia y la calidad del proceso de pintura, sino que también contribuirán a la sostenibilidad y la flexibilidad de la producción. A medida que las demandas de la industria continúan evolucionando, estos equipos se adaptarán para enfrentar nuevos desafíos y aprovechar las oportunidades que la tecnología ofrece.
Una de las áreas más prometedoras en el desarrollo de equipos para pintura electrostática es la integración de tecnologías de inteligencia artificial (IA) y aprendizaje automático. Los sistemas de IA pueden ayudar a predecir posibles fallos en el equipo antes de que ocurran, lo que reduce la necesidad de intervenciones de emergencia y mejora la fiabilidad del sistema. Además, la IA puede optimizar automáticamente los parámetros del proceso de pintura, como la velocidad, el voltaje y el tipo de polvo, para adaptarse a diferentes condiciones y materiales. Esta capacidad de ajustar en tiempo real las variables operativas sin intervención manual garantiza un acabado de mayor calidad y una mayor eficiencia operativa.
La automatización de los procesos de pintura sigue siendo una tendencia clave. Los robots colaborativos, o cobots, están ganando terreno en la industria de la pintura electrostática, ya que ofrecen la capacidad de trabajar de manera más flexible junto con los operarios. Estos robots pueden realizar tareas repetitivas y peligrosas de manera más eficiente, lo que no solo aumenta la productividad, sino que también reduce el riesgo de lesiones laborales. La automatización avanzada, combinada con tecnologías de visión artificial, puede mejorar aún más la precisión del recubrimiento y garantizar que los acabados sean perfectos, incluso en superficies complejas.
En cuanto a la sostenibilidad, los equipos para pintura electrostática seguirán evolucionando para cumplir con las normativas ambientales más estrictas. Las regulaciones cada vez más rigurosas sobre las emisiones y el uso de materiales ecológicos están impulsando el desarrollo de tecnologías que minimizan el impacto ambiental. Por ejemplo, se espera que los sistemas de pintura electrostática integren aún más soluciones para reducir el consumo de energía y los residuos generados. Además, el uso de polvo de pintura reciclado continuará ganando aceptación, ya que no solo es una opción más ecológica, sino que también contribuye a la reducción de costos operativos.
En paralelo, la mejora de los sistemas de recuperación de polvo permitirá una mayor eficiencia en el uso del material. Los equipos de pintura electrostática están siendo diseñados con sistemas avanzados de recirculación de polvo y filtración, lo que permite recuperar y reutilizar una mayor cantidad de pintura sobrante. Este proceso no solo reduce el desperdicio, sino que también contribuye a la reducción de los costos operativos y al cumplimiento de las regulaciones ambientales, al limitar la cantidad de polvo que se emite al aire.
La conectividad también está remodelando el panorama de los equipos para pintura electrostática. A través de la adopción del Internet de las Cosas (IoT), los equipos de pintura pueden estar conectados a plataformas de gestión centralizada que permiten a los operarios monitorear en tiempo real el estado de las máquinas y el proceso de pintura. Los sensores y las tecnologías de monitoreo remoto también permiten realizar diagnósticos preventivos, lo que facilita la detección de posibles fallos antes de que afecten a la producción. Esto no solo mejora la eficiencia, sino que también minimiza el tiempo de inactividad y reduce los costos de mantenimiento.
Otro aspecto relevante es la evolución hacia una mayor personalización en los procesos de pintura. Los equipos para pintura electrostática están mejorando su capacidad para adaptarse rápidamente a cambios en los colores, acabados o tipos de materiales. Esto es particularmente importante en sectores como la automoción, la fabricación de electrodomésticos y la industria de la electrónica, donde la personalización y los pequeños lotes de producción son cada vez más comunes. Los sistemas de pintura electrostática pueden ahora cambiar fácilmente entre diferentes tipos de polvo y colores, lo que permite a las empresas adaptarse rápidamente a las demandas del mercado y ofrecer una mayor variedad de productos sin comprometer la calidad o la eficiencia.
La tecnología de curado también experimentará avances importantes. Los sistemas de curado más rápidos y eficientes, como los hornos de curado por infrarrojos y los sistemas de curado ultravioleta (UV), seguirán ganando popularidad. Estos sistemas permiten acelerar el proceso de curado, lo que reduce el tiempo de producción y el consumo de energía. La implementación de tecnologías de curado más sostenibles también contribuirá a la mejora de la eficiencia energética de los equipos de pintura electrostática, lo que permitirá a las empresas reducir sus costos operativos y su huella de carbono.
Además, los avances en la fabricación aditiva o impresión 3D también influirán en el diseño de los equipos de pintura electrostática. La capacidad de imprimir piezas personalizadas permitirá a los fabricantes de equipos de pintura desarrollar componentes más eficientes y optimizados, adaptados a las necesidades específicas de cada cliente. Esta tecnología podría reducir los tiempos de desarrollo de nuevos equipos y permitir una mayor flexibilidad en la configuración de las líneas de pintura.
Los equipos para pintura electrostática también seguirán mejorando en términos de ergonomía y facilidad de uso. El diseño de los sistemas está orientado a facilitar el trabajo de los operarios, reduciendo la fatiga y mejorando la seguridad. Los controles más intuitivos, las interfaces más fáciles de usar y la implementación de sistemas de realidad aumentada (AR) para la capacitación y el mantenimiento permitirán a los operarios realizar su trabajo de manera más eficiente y con menos esfuerzo.
En resumen, los equipos para pintura electrostática seguirán avanzando hacia una mayor automatización, conectividad, sostenibilidad y personalización. Los sistemas serán más inteligentes, eficientes y respetuosos con el medio ambiente, lo que permitirá a las empresas mejorar su productividad, reducir costos y cumplir con las estrictas regulaciones medioambientales. A medida que la tecnología sigue evolucionando, estos equipos desempeñarán un papel clave en la transformación de las industrias de fabricación y pintura, proporcionando soluciones más flexibles y eficientes para satisfacer las demandas del mercado actual y futuro.
El futuro de los equipos para pintura electrostática también se verá influenciado por el creciente enfoque en la industria circular y la reutilización de recursos. A medida que las prácticas de economía circular se implementan más ampliamente en la industria manufacturera, los equipos para pintura electrostática se adaptarán para garantizar un uso más eficiente de los recursos y una reducción drástica de los residuos. Este enfoque no solo se refiere a la recuperación del polvo de pintura sobrante, sino también a la optimización del uso de materiales, la eficiencia en el consumo de energía y la gestión de los residuos generados durante el proceso de pintura. Los sistemas de recuperación de materiales mejorados permitirán una mayor reutilización de los residuos de pintura, lo que reducirá la necesidad de nuevas materias primas y contribuirá al ahorro en costos y la sostenibilidad de la operación.
En este contexto, los avances en la digitalización también jugarán un papel crucial. El análisis de datos en tiempo real permitirá no solo el monitoreo de los procesos de pintura, sino también la predicción de las necesidades de mantenimiento y el ajuste dinámico de los parámetros de operación para maximizar la eficiencia. Los sistemas de pintura electrostática, integrados en plataformas digitales y sistemas de gestión empresarial, podrán intercambiar información entre máquinas, operarios y el software de control centralizado para optimizar la producción. Esta capacidad de tomar decisiones en tiempo real basada en grandes volúmenes de datos (Big Data) permitirá a las empresas mejorar sus tiempos de ciclo, reducir el desperdicio y aumentar la eficiencia operativa.
Además, los sistemas avanzados de diagnóstico y mantenimiento predictivo, habilitados por sensores inteligentes, permitirán detectar problemas de funcionamiento antes de que afecten la producción. Gracias a la conectividad IoT, los operarios podrán recibir alertas y notificaciones sobre el estado de los equipos y sus componentes, lo que reducirá los tiempos de inactividad no planificados y permitirá un mantenimiento más eficiente y menos costoso. Este tipo de mantenimiento preventivo es crucial para minimizar el desgaste de los equipos y garantizar su funcionamiento óptimo durante un mayor período de tiempo, lo que, a su vez, reduce la necesidad de reemplazos de piezas y disminuye los costos operativos a largo plazo.
Otro aspecto relevante será la continua mejora en la integración de los equipos de pintura electrostática con otras tecnologías emergentes, como la robótica avanzada y la inteligencia artificial. La automatización de las líneas de pintura electrostática permitirá a las empresas mejorar la precisión de la aplicación de pintura, eliminar errores humanos y mejorar la seguridad laboral. Los robots podrán realizar tareas repetitivas, como el ajuste de la pistola de pintura o la supervisión de la calidad del recubrimiento, liberando a los operarios de tareas físicas y permitiéndoles centrarse en el control del proceso y la resolución de problemas complejos.
La integración de la pintura electrostática con los procesos de fabricación aditiva (impresión 3D) también tendrá un impacto significativo. Los avances en esta tecnología permitirán la creación de piezas personalizadas y optimizadas para el proceso de pintura, lo que reducirá los costos de producción y los tiempos de fabricación. Los equipos de pintura electrostática podrán adaptar sus procesos a las complejidades de las geometrías creadas por impresión 3D, lo que aumentará la flexibilidad y la personalización de los productos terminados. Además, las capacidades de la impresión 3D permitirán a las empresas fabricar piezas de repuesto a medida para sus equipos de pintura electrostática, lo que reducirá el tiempo de inactividad y los costos de mantenimiento.
La adaptación a diferentes tipos de recubrimientos especializados también será una característica clave de los equipos de pintura electrostática del futuro. A medida que la demanda de recubrimientos con propiedades específicas, como resistencia a la corrosión, a los productos químicos o a las condiciones climáticas extremas, aumenta en sectores como la automoción, la aviación y la fabricación de maquinaria industrial, los equipos para pintura electrostática serán capaces de manejar una mayor variedad de materiales. La capacidad de aplicar una amplia gama de recubrimientos de forma eficiente y sin comprometer la calidad será esencial para mantener la competitividad en estos sectores.
Por otro lado, la mejora continua en la seguridad de los operarios será un objetivo clave en el diseño de los equipos para pintura electrostática. A medida que la automatización y la robótica aumentan en las líneas de producción, los operarios estarán cada vez menos expuestos a riesgos laborales. Sin embargo, en las áreas donde los humanos siguen trabajando, los fabricantes continuarán mejorando la seguridad de los sistemas. Esto incluirá el desarrollo de sistemas de monitoreo de la salud y el bienestar de los operarios, el diseño de interfaces de usuario más intuitivas y la implementación de tecnologías de realidad aumentada (AR) para la capacitación y la supervisión.
La mejora de la experiencia del usuario, a través de interfaces más amigables y herramientas de control más accesibles, también será una prioridad. Las pantallas táctiles, las interfaces con inteligencia artificial y la implementación de sistemas de control remoto y en la nube permitirán a los operarios gestionar los equipos de manera más eficiente. Los avances en la tecnología de visualización permitirán un seguimiento más preciso de los procesos de pintura y facilitarán la identificación de problemas en tiempo real.
Además, la tendencia hacia la personalización en las aplicaciones industriales también afectará a los equipos de pintura electrostática. La demanda de soluciones de pintura más específicas y adaptadas a las necesidades del cliente impulsará la evolución de los equipos, que serán más modulares y configurables. Esto permitirá a las empresas adaptar sus sistemas de pintura a proyectos de diferentes tamaños, volúmenes y tipos de acabados, maximizando la flexibilidad de producción.
En conclusión, el futuro de los equipos para pintura electrostática se orienta hacia un modelo más automatizado, inteligente y flexible. Con el crecimiento de la digitalización, la robótica, la inteligencia artificial y la sostenibilidad, estos equipos no solo mejorarán la eficiencia y la calidad del proceso de pintura, sino que también ofrecerán soluciones más personalizadas y adaptadas a las necesidades del mercado. Las empresas que adopten estas tecnologías avanzadas podrán mantenerse a la vanguardia de la industria, mejorando su competitividad, reduciendo costos y cumpliendo con los estrictos estándares de calidad y sostenibilidad que el mercado exige.
Hornos de Curado
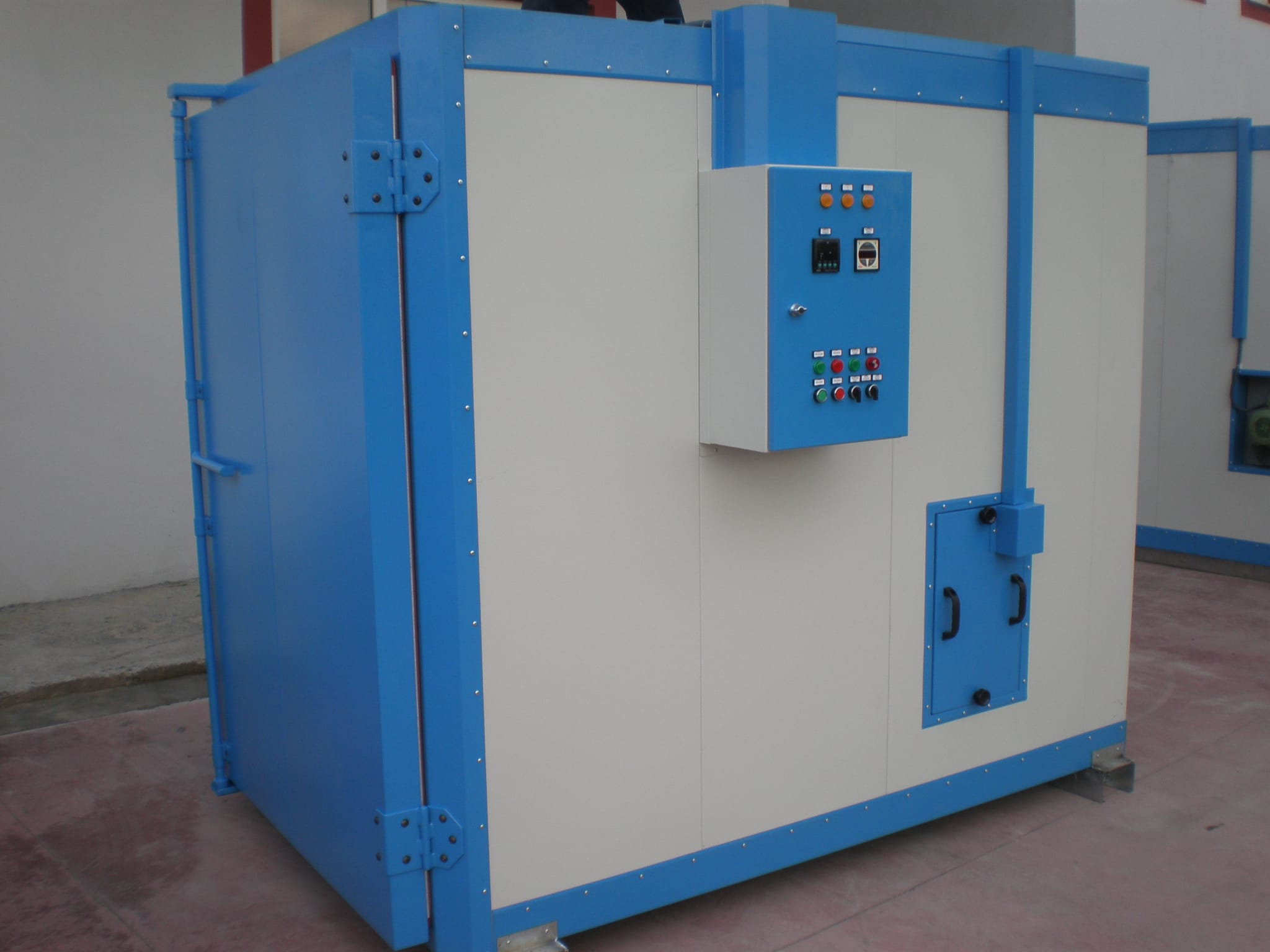
Después de que la pintura ha sido aplicada, es necesario un proceso de curado para fundir y fijar la pintura al material. Los hornos de curado son esenciales en este paso, proporcionando el calor necesario para completar el proceso.
Características Principales:
- Control de Temperatura: Los hornos están equipados con sistemas de control de temperatura precisos que garantizan que el curado se realice a la temperatura óptima para el tipo de pintura y material.
- Distribución Uniforme del Calor: Los hornos están diseñados para asegurar una distribución uniforme del calor, lo que es crucial para evitar defectos en el recubrimiento.
- Tipos de Hornos:
- Hornos Convencionales: Utilizan aire caliente para curar la pintura. Son los más comunes debido a su versatilidad y eficacia.
- Hornos Infrarrojos: Utilizan radiación infrarroja para calentar directamente la superficie pintada. Son más rápidos y eficientes energéticamente, especialmente para piezas más pequeñas o procesos de alta velocidad.
Ventajas de los Hornos de Curado:
- Durabilidad del Recubrimiento: El curado adecuado asegura que la pintura tenga una fuerte adherencia y resistencia a factores externos.
- Versatilidad: Pueden ajustarse para diferentes tipos de pintura y sustratos.
Sistemas de Recuperación de Polvo
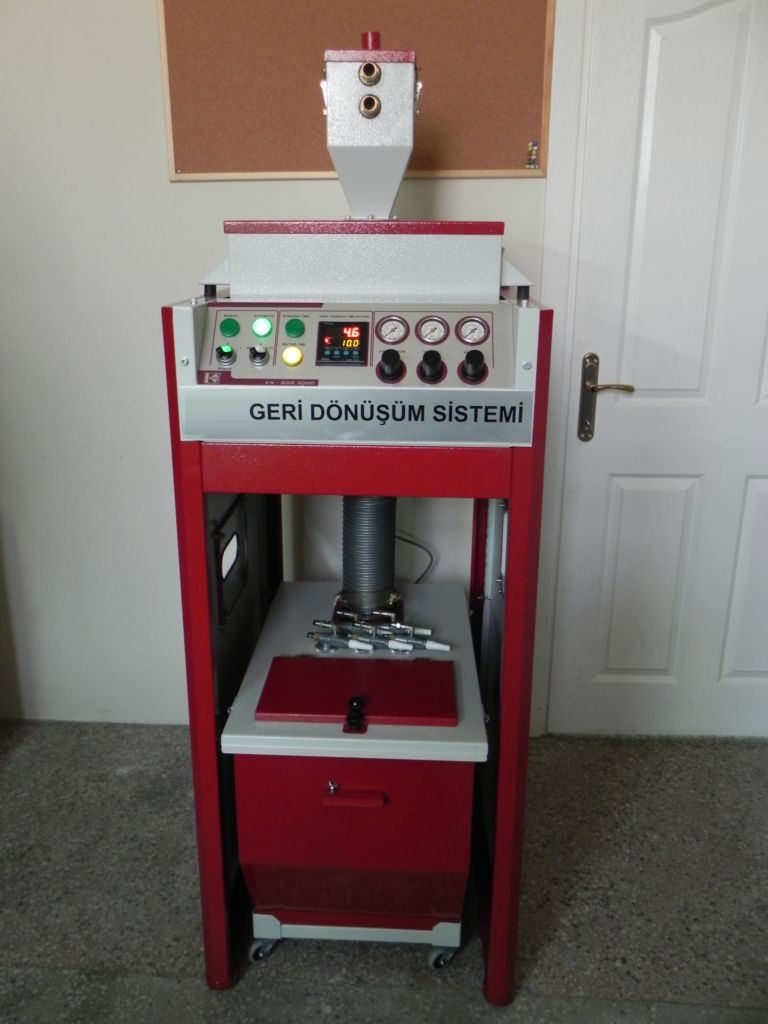
Uno de los aspectos más destacados de la pintura electrostática es su capacidad para recuperar y reutilizar el polvo de pintura no adherido. Los sistemas de recuperación de polvo son fundamentales para mantener la eficiencia y la sostenibilidad del proceso.
Características Principales:
- Filtración y Separación: Los sistemas de recuperación utilizan filtros y separadores para capturar el polvo en el aire y separarlo de otras partículas.
- Recirculación del Material: El polvo recuperado se recircula al sistema de aplicación, reduciendo la necesidad de nuevo material y disminuyendo los costos.
- Tipos de Sistemas de Recuperación:
- Recuperación por Filtros: Utilizan filtros de aire para capturar el polvo. Son comunes en instalaciones donde se manejan grandes volúmenes de material.
- Recuperación por Ciclón: Separan el polvo del aire mediante un sistema de ciclón, que utiliza la fuerza centrífuga. Son eficientes y permiten la recuperación de una mayor cantidad de material.
Beneficios de los Sistemas de Recuperación:
- Reducción de Residuos: Minimizan el desperdicio de pintura, lo que se traduce en ahorros significativos.
- Sostenibilidad Ambiental: Al recuperar y reutilizar el material, se reduce el impacto ambiental del proceso.
Fuentes de Poder y Controladores
Las fuentes de poder y controladores son esenciales para regular la carga eléctrica en las partículas de pintura y asegurar la estabilidad del proceso.
Características Principales:
- Generadores de Alta Tensión: Proveen la carga eléctrica necesaria para las partículas de pintura.
- Controladores de Proceso: Permiten ajustar y monitorear parámetros como el voltaje, la corriente, y la velocidad de pulverización, lo que asegura un control preciso del proceso.
- Integración con Sistemas Automatizados: En las instalaciones industriales modernas, estos controladores están integrados con sistemas automatizados que permiten un control remoto y una mayor precisión en la aplicación de la pintura.
Ventajas de las Fuentes de Poder y Controladores:
- Precisión: Permiten un control exacto de las condiciones de pulverización, mejorando la calidad del recubrimiento.
- Eficiencia: Contribuyen a optimizar el proceso, reduciendo errores y maximizando la productividad.
Aplicaciones de la Pintura Electrostática
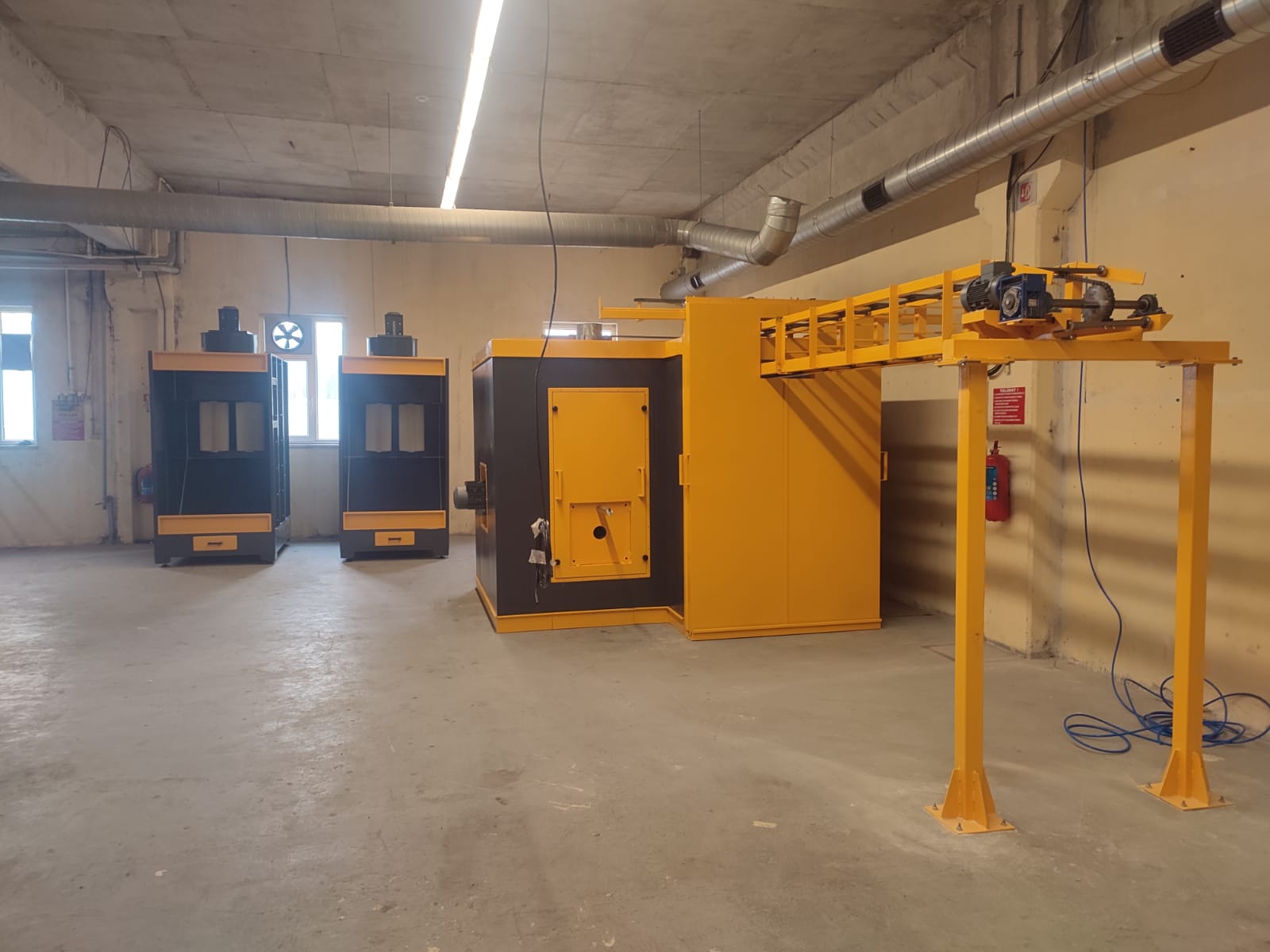
La pintura electrostática ha encontrado aplicaciones en una amplia variedad de industrias debido a su capacidad para proporcionar acabados duraderos y de alta calidad. Este método es especialmente valorado en sectores donde la resistencia a la corrosión, la durabilidad del recubrimiento y la estética son esenciales. A continuación, se exploran algunas de las principales industrias que utilizan la pintura electrostática, junto con ejemplos específicos y casos de éxito.
Industria Automotriz
La industria automotriz es uno de los sectores que más ha adoptado la pintura electrostática debido a los rigurosos estándares de calidad que se requieren para los vehículos. Desde la pintura de carrocerías hasta componentes internos, la pintura electrostática asegura un acabado uniforme, duradero y resistente a las inclemencias del tiempo.
Aplicaciones Específicas:
- Carrocerías: La carrocería de un vehículo debe resistir la corrosión y mantener su aspecto estético durante años. La pintura electrostática es ideal para esta tarea, ya que proporciona una cobertura uniforme y un acabado resistente al desgaste y la corrosión.
- Componentes Metálicos Internos: Piezas como chasis, soportes y piezas estructurales internas también se benefician de este tipo de recubrimiento, que les otorga una protección adicional contra el óxido y otros factores ambientales.
Caso de Éxito:
- Fabricante de Automóviles de Lujo: Una conocida marca de automóviles de lujo adoptó la pintura electrostática en sus líneas de producción para asegurar que cada vehículo que sale de la fábrica cumpla con los más altos estándares de calidad. El resultado ha sido una notable reducción en los defectos de pintura y una mejora en la durabilidad de los vehículos, lo que ha fortalecido la reputación de la marca en el mercado global.
Industria de Electrodomésticos
En la fabricación de electrodomésticos, la pintura electrostática se utiliza ampliamente para recubrir superficies metálicas y plásticas, protegiéndolas contra el desgaste y mejorando su apariencia estética. Desde lavadoras hasta refrigeradores, la durabilidad y el acabado uniforme son esenciales para asegurar la satisfacción del cliente.
Aplicaciones Específicas:
- Refrigeradores y Congeladores: Las superficies exteriores de estos electrodomésticos deben ser resistentes a los golpes, arañazos y la oxidación, lo que hace de la pintura electrostática la elección ideal.
- Lavadoras y Secadoras: Estas unidades requieren recubrimientos que no solo sean estéticamente agradables, sino también resistentes al agua y al uso continuo.
Caso de Éxito:
- Empresa de Electrodomésticos: Un importante fabricante de electrodomésticos implementó la pintura electrostática en su línea de producción de lavadoras, resultando en un aumento significativo en la durabilidad del producto y una disminución en las reclamaciones de garantía relacionadas con la corrosión.
Industria del Mobiliario Metálico
El mobiliario metálico, utilizado tanto en entornos domésticos como comerciales, debe tener un acabado que sea estéticamente agradable y resistente a factores como la humedad y el uso diario. La pintura electrostática ofrece una solución que cumple con estos requisitos.
Aplicaciones Específicas:
- Mobiliario de Oficina: Escritorios, sillas, estanterías y otros muebles de oficina metálicos se benefician de recubrimientos electrostáticos que aseguran durabilidad y resistencia al desgaste.
- Mobiliario Exterior: Mesas, sillas y estructuras metálicas para exteriores deben resistir la exposición a los elementos. La pintura electrostática proporciona una barrera eficaz contra la corrosión y los daños causados por la intemperie.
Caso de Éxito:
- Fabricante de Muebles: Un fabricante de muebles metálicos para exteriores implementó la pintura electrostática en su proceso de producción, lo que resultó en productos más duraderos y un incremento en la satisfacción del cliente. La empresa reportó una reducción significativa en las devoluciones por daños relacionados con la corrosión.
Industria de la Construcción
En la construcción, la pintura electrostática se utiliza para recubrir una amplia variedad de componentes metálicos, desde puertas y ventanas hasta barandillas y estructuras arquitectónicas. La resistencia a la intemperie y la durabilidad del recubrimiento son cruciales en este sector.
Aplicaciones Específicas:
- Puertas y Ventanas de Metal: Estos elementos deben tener un recubrimiento resistente que no solo sea estéticamente atractivo, sino que también proteja contra la corrosión y el desgaste.
- Barandillas y Pasamanos: En edificios comerciales y residenciales, las barandillas metálicas deben ser duraderas y resistentes al contacto frecuente, así como a las condiciones climáticas.
Caso de Éxito:
- Proyecto de Edificación Comercial: En un importante proyecto de construcción comercial, la pintura electrostática fue elegida para el recubrimiento de todas las barandillas metálicas y puertas exteriores, lo que resultó en una notable reducción en los costos de mantenimiento a largo plazo debido a la durabilidad del acabado.
Industria del Equipamiento Deportivo
La pintura electrostática también es ampliamente utilizada en la fabricación de equipos deportivos, especialmente aquellos que están expuestos a condiciones climáticas adversas o que requieren una durabilidad extrema.
Aplicaciones Específicas:
- Bicicletas: Los marcos de las bicicletas, especialmente aquellos destinados a uso en exteriores o en condiciones extremas, requieren un recubrimiento que sea ligero, resistente y capaz de soportar golpes y arañazos.
- Equipos de Gimnasio: Las máquinas y pesos utilizados en gimnasios deben tener un acabado resistente que soporte el uso intensivo y el sudor, sin deteriorarse con el tiempo.
Caso de Éxito:
- Fabricante de Bicicletas de Montaña: Un fabricante líder de bicicletas de montaña adoptó la pintura electrostática para los marcos de sus bicicletas, logrando una mayor resistencia al impacto y a la corrosión. Esta mejora en la durabilidad ha sido un factor clave en la lealtad de los clientes y en la reputación de la marca.
Industria de Componentes Electrónicos
La industria de componentes electrónicos utiliza la pintura electrostática para proteger piezas sensibles contra la corrosión, el desgaste y los daños físicos, asegurando que los dispositivos tengan una vida útil prolongada.
Aplicaciones Específicas:
- Carcasas de Equipos Electrónicos: Las carcasas metálicas de computadoras, servidores y otros dispositivos electrónicos requieren una protección robusta que también sea estéticamente agradable.
- Componentes Internos: Algunos componentes internos, como chasis y soportes, también se benefician de un recubrimiento electrostático para evitar la corrosión y mejorar la durabilidad.
Caso de Éxito:
- Fabricante de Equipos Informáticos: Un fabricante de equipos informáticos implementó la pintura electrostática en la producción de sus carcasas metálicas, resultando en productos más duraderos y resistentes al desgaste, lo que ha mejorado la percepción de calidad entre los consumidores.
Selección de Equipos: Factores a Considerar
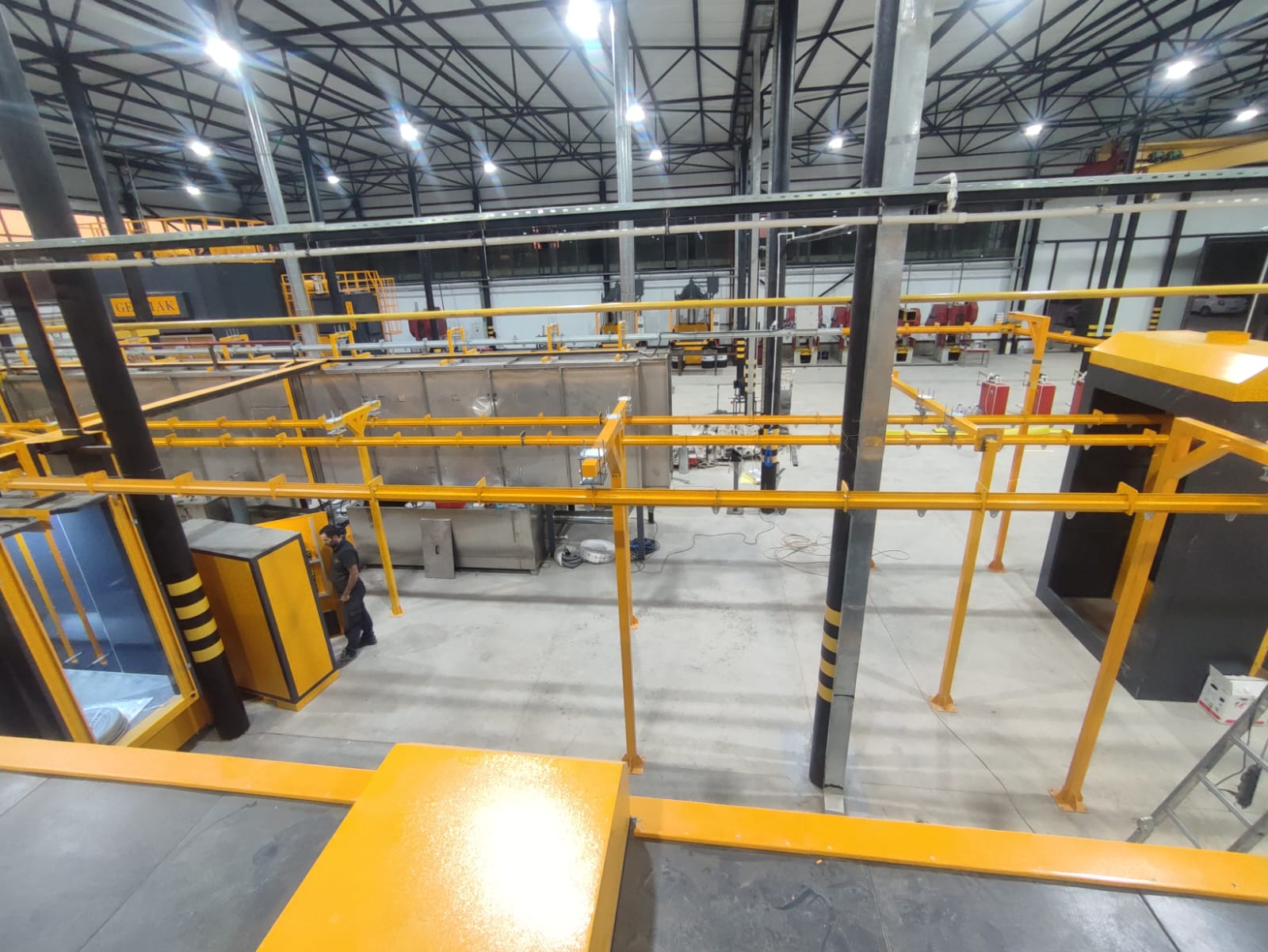
La selección de los equipos adecuados para la pintura electrostática es crucial para garantizar un proceso eficiente, de alta calidad y rentable. Al elegir entre las distintas opciones disponibles en el mercado, es esencial considerar varios factores que influirán en el rendimiento y la viabilidad a largo plazo de la inversión. A continuación, se detallan los aspectos más importantes a tener en cuenta.
Tamaño y Escala de la Producción
Uno de los primeros factores a considerar es el tamaño y la escala de la producción. Dependiendo del volumen de trabajo y la frecuencia con la que se utilizarán los equipos, las necesidades pueden variar considerablemente.
Consideraciones Clave:
- Producción a Pequeña Escala: Para operaciones de bajo volumen, como talleres de personalización o pequeñas fábricas, puede ser suficiente una configuración básica con pistolas de pulverización manuales y un horno de curado de tamaño reducido.
- Producción a Gran Escala: En operaciones industriales de gran volumen, como en la fabricación automotriz o de electrodomésticos, se requiere un sistema completamente automatizado que incluya múltiples pistolas automáticas, cabinas de gran capacidad y hornos de curado que puedan manejar grandes lotes de productos simultáneamente.
Consejo: Es importante analizar el crecimiento proyectado de la producción. Invertir en equipos que puedan escalar según las necesidades futuras puede ahorrar costos y complicaciones a largo plazo.
Tipo de Material a Recubrir
El tipo de material que se va a recubrir es otro factor crucial. Los equipos de pintura electrostática deben ser seleccionados en función de la compatibilidad con los materiales predominantes en la producción.
Consideraciones Clave:
- Metales Ferrosos y No Ferrosos: Los equipos diseñados para trabajar con metales suelen ser los más comunes. Sin embargo, es importante asegurarse de que los equipos sean compatibles con los tipos específicos de metales que se utilizan, ya que diferentes metales pueden requerir diferentes configuraciones de temperatura y voltaje.
- Plásticos y Materiales Compuestos: Aunque la pintura electrostática es menos común en plásticos, existen sistemas especializados que pueden manejar este tipo de materiales. Estos sistemas generalmente requieren ajustes en la carga electrostática y en el proceso de curado para evitar el daño al material base.
Consejo: Consultar con el proveedor del equipo sobre la adaptabilidad de los sistemas para diferentes materiales es esencial para asegurar que la inversión cubra todas las necesidades productivas.
Calidad del Acabado Deseado
El estándar de calidad requerido para el acabado final puede variar según la industria y el producto. Es fundamental seleccionar equipos que ofrezcan la precisión y consistencia necesarias para cumplir con estos estándares.
Consideraciones Clave:
- Requisitos Estéticos: Si el acabado estético es una prioridad, como en productos de consumo o automotrices, los equipos deben ser capaces de proporcionar una aplicación uniforme sin defectos como burbujas, motas o irregularidades.
- Resistencia y Durabilidad: En industrias donde la resistencia a la corrosión y la durabilidad son primordiales, es esencial que el equipo proporcione un recubrimiento suficientemente grueso y bien adherido, lo que a menudo implica un control preciso del proceso de curado.
Consejo: Realizar pruebas preliminares con diferentes equipos puede ayudar a determinar cuál ofrece el mejor rendimiento en términos de acabado final.
Presupuesto Disponible
El costo de los equipos es un factor determinante en el proceso de selección. Es importante equilibrar la necesidad de equipos de alta calidad con el presupuesto disponible, considerando tanto el costo inicial como los costos operativos y de mantenimiento a largo plazo.
Consideraciones Clave:
- Inversión Inicial: Los sistemas automatizados y de alta capacidad suelen tener un costo inicial más elevado. Sin embargo, esta inversión puede justificarse por los ahorros a largo plazo en eficiencia y costos de operación.
- Costo Operativo: Es fundamental considerar los costos operativos asociados, como el consumo de energía, los costos de mantenimiento y las necesidades de personal. Los sistemas más avanzados pueden ser más eficientes en términos de energía, lo que reduce los costos a largo plazo.
Consejo: Solicitar un análisis de costo-beneficio a los proveedores de equipos puede ofrecer una visión clara de las implicaciones financieras a corto y largo plazo.
Mantenimiento y Soporte Técnico
El mantenimiento regular y el soporte técnico son esenciales para asegurar la longevidad y el rendimiento óptimo de los equipos de pintura electrostática. Por lo tanto, es crucial considerar la disponibilidad de servicios de mantenimiento y el nivel de soporte técnico ofrecido por el fabricante o proveedor del equipo.
Consideraciones Clave:
- Frecuencia de Mantenimiento: Los equipos de pintura electrostática requieren mantenimiento regular para funcionar correctamente. Es importante conocer los requisitos de mantenimiento y asegurarse de que el personal esté capacitado para realizar estas tareas.
- Soporte Técnico: Un buen soporte técnico puede marcar la diferencia en la resolución rápida de problemas y en la minimización del tiempo de inactividad. Asegurarse de que el proveedor ofrece un soporte técnico robusto y disponible es un factor clave en la elección del equipo.
Consejo: Evaluar la reputación del proveedor en términos de soporte técnico y servicio postventa es una medida prudente para evitar problemas futuros.
Consideraciones de Seguridad
La seguridad es un aspecto fundamental en cualquier operación industrial. La pintura electrostática, al involucrar cargas eléctricas y polvo potencialmente inflamable, requiere equipos que cumplan con altos estándares de seguridad.
Consideraciones Clave:
- Cumplimiento Normativo: Es vital asegurarse de que los equipos cumplan con las normativas locales e internacionales de seguridad. Esto incluye la correcta ventilación, sistemas de control de polvo y protección contra descargas eléctricas.
- Capacitación del Personal: Los operarios deben recibir una formación adecuada para manejar los equipos de forma segura, entender los riesgos y saber cómo reaccionar ante posibles emergencias.
Consejo: Incluir un plan de capacitación en el paquete de compra de los equipos puede garantizar que el personal esté preparado para operar de manera segura desde el primer día.
Comparación de Marcas y Modelos
Finalmente, la comparación de diferentes marcas y modelos es un paso crucial en el proceso de selección. Existen múltiples proveedores en el mercado, cada uno con sus propias ventajas y características distintivas.
Consideraciones Clave:
- Reputación del Fabricante: La reputación y la experiencia del fabricante en el sector son indicativos de la calidad y fiabilidad del equipo. Es recomendable investigar las opiniones de otros usuarios y casos de éxito asociados con la marca.
- Características Especiales: Algunos modelos pueden ofrecer características adicionales que mejoran la eficiencia o la facilidad de uso, como interfaces digitales, control de procesos automatizado, o capacidades de personalización.
Consejo: Realizar visitas a instalaciones donde ya se estén utilizando los equipos considerados puede proporcionar información valiosa y práctica sobre su rendimiento.
Beneficios de Usar Equipos de Pintura Electrostática
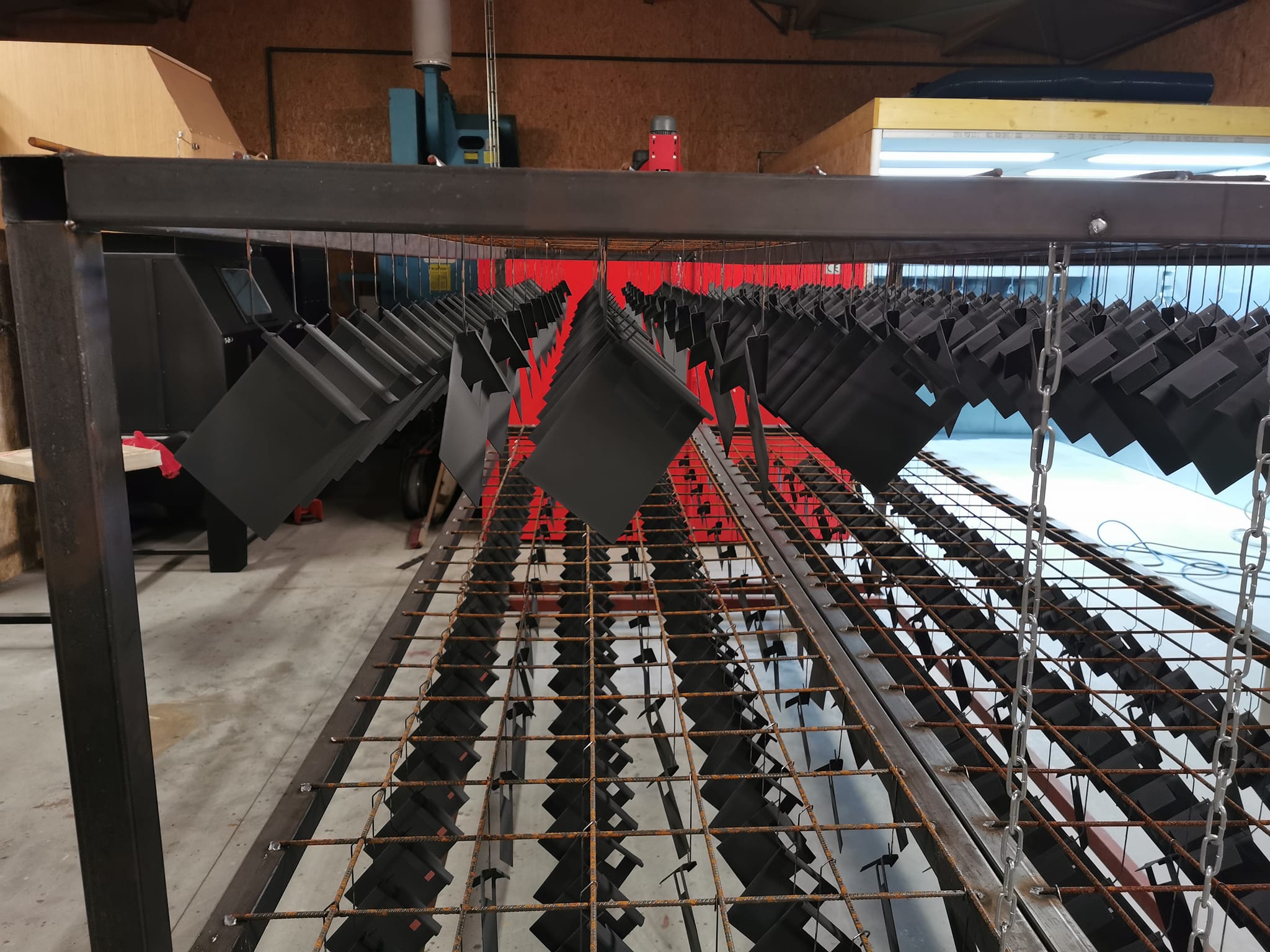
El uso de equipos de pintura electrostática ofrece múltiples beneficios que los hacen una opción preferida en diversas industrias. Estos beneficios no solo se reflejan en la calidad del producto final, sino también en la eficiencia del proceso, la reducción de costos y el impacto ambiental. A continuación, se analizan las principales ventajas de utilizar esta tecnología.
Eficiencia en el Uso de Materiales
Uno de los beneficios más notables de la pintura electrostática es su alta eficiencia en el uso de materiales. Este proceso permite que un mayor porcentaje de la pintura aplicada se adhiera a la superficie del objeto, reduciendo significativamente el desperdicio.
Ventajas Clave:
- Alta Tasa de Transferencia: La atracción electrostática asegura que hasta el 95% de la pintura pulverizada se adhiera a la superficie, lo que es considerablemente superior a los métodos tradicionales de aplicación de pintura.
- Reducción del Desperdicio: El polvo de pintura que no se adhiere durante la primera aplicación puede ser recuperado y reutilizado, minimizando la pérdida de material y reduciendo los costos de producción.
Ejemplo Práctico: En una línea de producción automotriz, la eficiencia en el uso de materiales se traduce en un ahorro considerable en los costos de pintura, especialmente cuando se maneja un alto volumen de producción. Este ahorro, a su vez, puede mejorar la rentabilidad general de la operación.
Calidad Superior del Acabado
La pintura electrostática es conocida por proporcionar un acabado de alta calidad que es difícil de igualar con otros métodos de pintura. Este acabado es tanto estéticamente atractivo como duradero, lo que resulta en productos que no solo se ven mejor, sino que también tienen una mayor vida útil.
Ventajas Clave:
- Cobertura Uniforme: La atracción electrostática garantiza que la pintura se distribuya uniformemente sobre la superficie, eliminando problemas comunes como corrimientos, manchas o áreas sin cubrir.
- Durabilidad del Recubrimiento: Los recubrimientos aplicados mediante pintura electrostática son altamente resistentes a la abrasión, la corrosión y los impactos, lo que los hace ideales para productos que estarán expuestos a condiciones adversas.
Ejemplo Práctico: En la fabricación de electrodomésticos, un acabado uniforme y duradero es esencial para asegurar que los productos no solo cumplan con los estándares estéticos, sino que también resistan el uso diario sin deteriorarse. Esto reduce las reclamaciones de garantía y mejora la satisfacción del cliente.
Ahorro de Costos a Largo Plazo
Aunque la inversión inicial en equipos de pintura electrostática puede ser mayor que en métodos tradicionales, los ahorros a largo plazo son significativos debido a la reducción de costos operativos y de material.
Ventajas Clave:
- Menor Consumo de Pintura: La alta eficiencia del proceso significa que se requiere menos pintura para lograr una cobertura completa, lo que reduce los costos de materia prima.
- Reducción de Residuos y Costos de Eliminación: Con menos desperdicio de pintura y la capacidad de recuperar el polvo no adherido, los costos asociados con la eliminación de residuos se reducen considerablemente.
- Menos Tiempo de Inactividad: Los sistemas automatizados de pintura electrostática suelen requerir menos mantenimiento y son menos propensos a fallas, lo que minimiza el tiempo de inactividad y mejora la productividad general.
Ejemplo Práctico: Una empresa que fabrica componentes metálicos puede ver una reducción significativa en sus costos operativos al cambiar a un sistema de pintura electrostática, recuperando la inversión inicial en equipos en un plazo relativamente corto gracias a los ahorros en material y mantenimiento.
Impacto Ambiental Reducido
La sostenibilidad es una preocupación creciente en todas las industrias, y la pintura electrostática se destaca como una opción más ecológica en comparación con otros métodos de pintura. Este proceso no solo reduce el desperdicio de material, sino que también minimiza las emisiones de compuestos orgánicos volátiles (COVs).
Ventajas Clave:
- Menos Emisiones de COVs: A diferencia de la pintura líquida tradicional, que puede liberar grandes cantidades de COVs durante el proceso de secado, la pintura electrostática, especialmente en polvo, genera emisiones mínimas, lo que contribuye a un entorno de trabajo más seguro y a la reducción del impacto ambiental.
- Reducción de Residuos Peligrosos: La capacidad de recuperar y reutilizar el polvo de pintura no adherido significa que se generan menos residuos peligrosos, lo que simplifica el cumplimiento de las regulaciones ambientales y reduce los costos de manejo de residuos.
Ejemplo Práctico: Un fabricante de muebles metálicos que adopta la pintura electrostática no solo mejora la eficiencia del proceso, sino que también reduce su huella ambiental, lo que puede ser un factor clave en la obtención de certificaciones ecológicas y en el atractivo de sus productos para los consumidores conscientes del medio ambiente.
Flexibilidad y Adaptabilidad
Los sistemas de pintura electrostática son altamente flexibles y pueden ser adaptados para una amplia variedad de aplicaciones y tipos de materiales. Esta versatilidad hace que sean adecuados para una amplia gama de industrias, desde la automotriz hasta la electrónica.
Ventajas Clave:
- Compatibilidad con Diversos Materiales: Aunque la pintura electrostática es más comúnmente utilizada en metales, los sistemas avanzados pueden ser ajustados para trabajar con plásticos y otros materiales, ampliando el rango de aplicaciones posibles.
- Personalización del Acabado: Los sistemas permiten un control preciso de parámetros como el grosor del recubrimiento y el tipo de acabado (mate, brillante, texturizado), lo que facilita la personalización según las especificaciones del cliente o los requisitos del producto.
Ejemplo Práctico: Un proveedor de servicios de recubrimiento que trabaja con una variedad de industrias puede beneficiarse enormemente de la flexibilidad de los sistemas de pintura electrostática, permitiéndole ofrecer soluciones personalizadas para diferentes tipos de productos y clientes.
Mejora de la Seguridad Laboral
Finalmente, la pintura electrostática, al generar menos residuos y emisiones peligrosas, también contribuye a un entorno de trabajo más seguro y saludable para los operarios.
Ventajas Clave:
- Reducción de Exposición a Sustancias Tóxicas: La menor emisión de COVs y la reducción del polvo en suspensión durante el proceso de pintura disminuyen la exposición de los trabajadores a sustancias potencialmente peligrosas.
- Entorno de Trabajo Limpio: Los sistemas de recuperación de polvo y las cabinas de pintura bien ventiladas ayudan a mantener un entorno de trabajo más limpio, lo que reduce los riesgos de accidentes y mejora el confort de los trabajadores.
Ejemplo Práctico: En una planta de fabricación de componentes electrónicos, la adopción de la pintura electrostática no solo mejora la eficiencia del proceso, sino que también contribuye a un entorno de trabajo más seguro, lo que puede reducir las tasas de ausentismo y mejorar la moral de los empleados.
Seguiré con la sección sobre Mantenimiento y Seguridad en el Uso de Equipos de Pintura Electrostática. Esta parte se centrará en las prácticas recomendadas para el mantenimiento de los equipos, así como en las medidas de seguridad necesarias para operar de manera segura y eficiente.
Mantenimiento y Seguridad en el Uso de Equipos de Pintura Electrostática
El mantenimiento adecuado y las prácticas de seguridad son esenciales para garantizar el funcionamiento óptimo de los equipos de pintura electrostática. Dado que estos equipos operan con cargas eléctricas y polvo de pintura, es crucial que los operarios sigan procedimientos estrictos para evitar accidentes y asegurar la longevidad del equipo.
Procedimientos de Mantenimiento Regular
El mantenimiento regular es fundamental para evitar problemas operativos y prolongar la vida útil de los equipos. La frecuencia y el tipo de mantenimiento dependerán del uso y de las especificaciones del equipo, pero algunas prácticas comunes incluyen:
Mantenimiento de Pistolas de Pulverización:
- Limpieza Regular: Las pistolas de pulverización deben limpiarse regularmente para evitar la acumulación de polvo de pintura, lo que puede obstruir las boquillas y afectar la calidad del rociado.
- Inspección de Componentes Eléctricos: Es importante revisar periódicamente los componentes eléctricos de la pistola, como los cables y conectores, para detectar signos de desgaste o daño que podrían afectar la carga electrostática.
- Reemplazo de Boquillas: Las boquillas deben ser reemplazadas según las recomendaciones del fabricante, ya que el desgaste puede afectar la precisión y la uniformidad del rociado.
Mantenimiento de Cabinas de Pintura:
- Limpieza de Filtros: Los filtros de las cabinas deben ser limpiados o reemplazados regularmente para mantener una ventilación adecuada y evitar la acumulación de polvo.
- Inspección de Sellos y Juntas: Los sellos y juntas deben ser revisados para asegurar que la cabina esté correctamente sellada, evitando la fuga de polvo hacia el exterior y garantizando un entorno de trabajo seguro.
- Verificación del Sistema de Ventilación: Es crucial asegurarse de que el sistema de ventilación funcione correctamente para mantener el aire limpio y libre de contaminantes.
Mantenimiento de Hornos de Curado:
- Control de Temperatura: Los sensores de temperatura y los sistemas de control deben ser calibrados regularmente para asegurar que el horno mantenga las condiciones óptimas de curado.
- Limpieza Interna: El interior del horno debe mantenerse limpio para evitar la acumulación de polvo y residuos que podrían afectar la calidad del curado.
- Inspección de Elementos de Calentamiento: Los elementos de calentamiento deben ser revisados y reemplazados según sea necesario para asegurar un calentamiento uniforme.
Normas de Seguridad y Uso Adecuado
La seguridad es una prioridad en cualquier operación que involucre equipos de pintura electrostática. Dado que el proceso utiliza cargas eléctricas y maneja materiales inflamables, es esencial seguir normas de seguridad rigurosas.
Seguridad en la Operación de Pistolas de Pulverización:
- Protección Personal: Los operarios deben utilizar equipos de protección personal (EPP), incluyendo guantes, máscaras de respiración, y ropa antiestática, para protegerse de las partículas de polvo y las descargas eléctricas.
- Prevención de Descargas Eléctricas: Es fundamental asegurarse de que los equipos estén correctamente conectados a tierra para evitar la acumulación de cargas eléctricas que puedan causar descargas peligrosas.
- Uso Adecuado del Equipo: Los operarios deben estar capacitados en el uso correcto de las pistolas, incluyendo cómo ajustar el voltaje y la presión para diferentes aplicaciones.
Seguridad en las Cabinas de Pintura:
- Control de Polvo: Las cabinas deben estar equipadas con sistemas de extracción de polvo que mantengan el aire limpio y prevengan la acumulación de partículas inflamables.
- Ventilación Adecuada: Es crucial mantener una ventilación adecuada para evitar la concentración de vapores que puedan ser inflamables o tóxicos.
- Acceso Restringido: Solo el personal autorizado y capacitado debe tener acceso a las cabinas de pintura para minimizar el riesgo de accidentes.
Seguridad en el Uso de Hornos de Curado:
- Control de Temperatura: Los operarios deben estar entrenados para monitorear y controlar las temperaturas del horno, evitando sobrecalentamientos que puedan causar incendios o daños al equipo.
- Monitoreo de Gases: Es importante contar con sistemas que monitoreen la concentración de gases peligrosos dentro del horno y en el área circundante.
- Procedimientos de Emergencia: Deben existir procedimientos claros para la evacuación y la respuesta en caso de incendios o fallos en el sistema.
Capacitación del Personal y Cumplimiento Normativo
La capacitación continua del personal es crucial para asegurar que los equipos se utilicen de manera segura y eficiente. Además, el cumplimiento de las normativas locales e internacionales es indispensable para operar dentro de los estándares legales y de seguridad.
Capacitación del Personal:
- Formación Inicial: Todos los operarios deben recibir una formación exhaustiva antes de utilizar los equipos de pintura electrostática. Esta formación debe incluir tanto la operación del equipo como las medidas de seguridad específicas.
- Capacitación Continua: Es importante ofrecer sesiones de actualización periódicas para asegurar que el personal esté al día con las mejores prácticas y cualquier cambio en las normativas.
- Simulacros de Emergencia: La realización de simulacros de emergencia permite que el personal esté preparado para responder rápidamente a situaciones críticas, como incendios o derrames de productos químicos.
Cumplimiento Normativo:
- Normativas de Seguridad: Los equipos y procedimientos deben cumplir con normativas específicas como las de la OSHA (Occupational Safety and Health Administration) en Estados Unidos, o las equivalentes en otros países, que regulan la seguridad en el trabajo con equipos eléctricos y sustancias químicas.
- Certificaciones de Calidad: Las instalaciones deben estar certificadas bajo normas de calidad, como ISO 9001, que aseguran que los procesos cumplen con los estándares internacionales de gestión y seguridad.
- Inspecciones Regulares: Las autoridades locales pueden realizar inspecciones para asegurar el cumplimiento de las normativas de seguridad. Estar preparado para estas inspecciones es fundamental para evitar sanciones y mantener la licencia operativa.
Innovaciones y Tendencias en la Pintura Electrostática
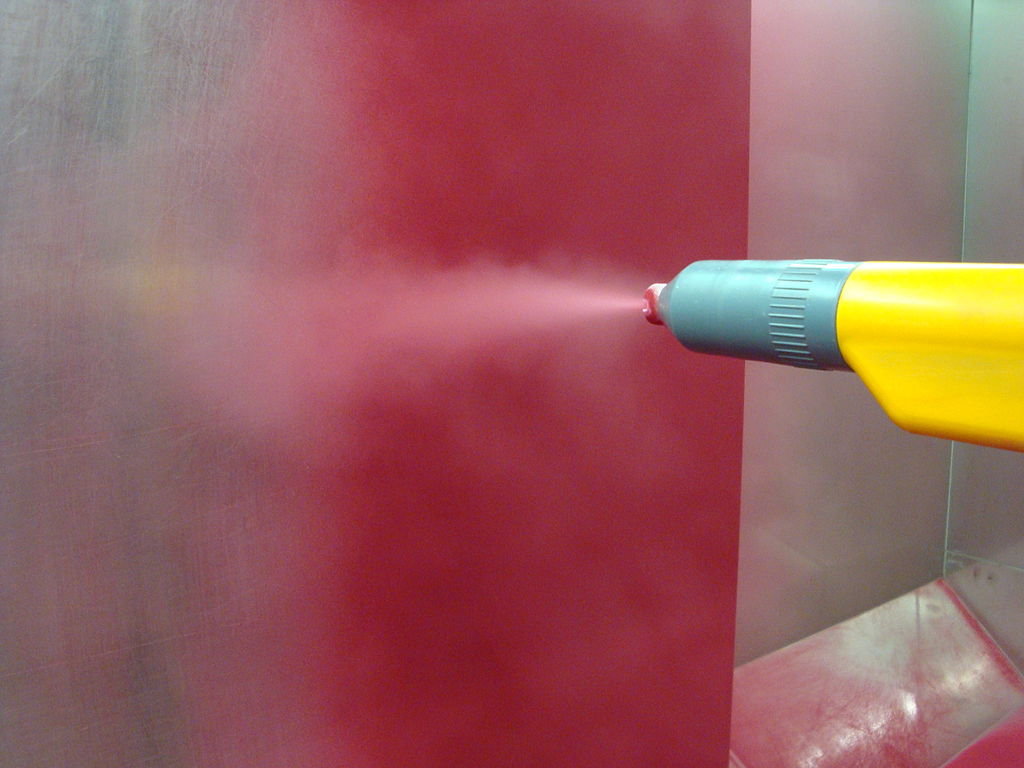
La pintura electrostática ha evolucionado significativamente desde sus inicios, impulsada por avances tecnológicos y la necesidad de mejorar la eficiencia, la sostenibilidad y la calidad en los procesos industriales. A medida que la industria se adapta a nuevas demandas y retos, surgen innovaciones y tendencias que prometen llevar la pintura electrostática a un nuevo nivel. A continuación, se describen algunas de las principales tendencias e innovaciones que están moldeando el futuro de este campo.
Automatización y Control Inteligente
La automatización es una tendencia creciente en la industria de la pintura electrostática, con un enfoque particular en mejorar la precisión y la eficiencia del proceso. Los sistemas automatizados permiten un control más preciso de los parámetros de pulverización, reduciendo el error humano y mejorando la consistencia del recubrimiento.
Aspectos Clave:
- Robots de Pintura: Los robots equipados con pistolas de pulverización electrostática son capaces de realizar aplicaciones de pintura con una precisión y consistencia que superan a los métodos manuales. Estos robots pueden programarse para seguir trayectorias específicas y ajustar los parámetros en tiempo real según las características de cada pieza.
- Sistemas de Control Inteligente: La integración de sistemas de control basados en inteligencia artificial y aprendizaje automático permite ajustar automáticamente los parámetros del proceso, como el voltaje, la presión y la velocidad de pulverización, en respuesta a las condiciones del entorno y las características del material. Esto no solo mejora la calidad del recubrimiento, sino que también optimiza el uso de material y energía.
Ejemplo de Innovación: En la industria automotriz, algunos fabricantes han implementado líneas de pintura completamente automatizadas donde los robots y los sistemas de control inteligente trabajan en conjunto para aplicar recubrimientos con una precisión y eficiencia sin precedentes, lo que resulta en una reducción significativa de los desperdicios y una mejora en la calidad del producto final.
Tecnologías de Pintura en Polvo de Baja Temperatura
Tradicionalmente, la pintura en polvo ha requerido altas temperaturas de curado, lo que limitaba su uso a ciertos materiales, especialmente metales. Sin embargo, las nuevas tecnologías están desarrollando recubrimientos en polvo que pueden curarse a temperaturas más bajas, lo que amplía las posibilidades de aplicación a materiales más sensibles al calor.
Aspectos Clave:
- Curado a Baja Temperatura: Los nuevos recubrimientos en polvo están formulados para curar a temperaturas significativamente más bajas, lo que permite su uso en plásticos y otros materiales compuestos que no podrían soportar los métodos tradicionales de curado.
- Ahorro Energético: Al requerir menos energía para alcanzar las temperaturas de curado necesarias, estas tecnologías también contribuyen a la reducción de costos operativos y al impacto ambiental.
Ejemplo de Innovación: Un fabricante de productos electrónicos ha adoptado tecnologías de curado a baja temperatura para aplicar recubrimientos electrostáticos a carcasas de plástico, logrando un acabado duradero y resistente sin comprometer la integridad del material.
Recubrimientos Multifuncionales
La industria de la pintura electrostática también está avanzando hacia el desarrollo de recubrimientos multifuncionales que no solo protegen y embellecen, sino que también ofrecen propiedades adicionales, como la resistencia a bacterias, la conductividad eléctrica, o la capacidad de autorreparación.
Aspectos Clave:
- Recubrimientos Antibacterianos: En respuesta a la creciente demanda de superficies más higiénicas, especialmente en sectores como el de la salud y la alimentación, se están desarrollando recubrimientos electrostáticos que incorporan propiedades antimicrobianas, lo que ayuda a reducir la propagación de bacterias y otros patógenos.
- Recubrimientos Conductivos: Los recubrimientos electrostáticos que incorporan materiales conductivos están encontrando aplicaciones en la industria electrónica y en la fabricación de dispositivos que requieren disipación de cargas eléctricas.
- Recubrimientos Autorreparables: La investigación en materiales avanzados está llevando al desarrollo de recubrimientos que pueden “sanarse” a sí mismos cuando se dañan, extendiendo así la vida útil del producto recubierto.
Ejemplo de Innovación: Un hospital ha comenzado a utilizar recubrimientos electrostáticos antibacterianos en sus instalaciones, reduciendo significativamente las tasas de infección y mejorando la seguridad para los pacientes.
Sostenibilidad y Ecoeficiencia
La sostenibilidad continúa siendo una prioridad para la industria de la pintura electrostática, con un enfoque en la reducción de la huella de carbono y la mejora de la eficiencia en el uso de recursos. Las innovaciones en este campo están dirigidas a hacer que los procesos de recubrimiento sean más ecológicos y económicamente viables.
Aspectos Clave:
- Recubrimientos en Polvo Sin Disolventes: Los recubrimientos en polvo, que no requieren disolventes, están ayudando a eliminar las emisiones de compuestos orgánicos volátiles (COVs), contribuyendo a un entorno de trabajo más seguro y a la protección del medio ambiente.
- Reciclaje y Recuperación de Polvo: Las tecnologías de recuperación de polvo están mejorando constantemente, permitiendo la reutilización de un mayor porcentaje de material no adherido, lo que reduce los residuos y los costos asociados con la eliminación de desechos.
- Uso de Materiales Renovables: Se están desarrollando recubrimientos que incorporan materiales de origen biológico o reciclado, lo que reduce la dependencia de recursos no renovables y apoya la economía circular.
Ejemplo de Innovación: Una empresa de muebles metálicos ha implementado un sistema de recubrimiento en polvo completamente cerrado, donde el polvo no adherido es recuperado y reutilizado, logrando una tasa de desperdicio cercana a cero y reduciendo significativamente su impacto ambiental.
Tendencias Futuras en la Industria
Mirando hacia el futuro, la industria de la pintura electrostática está preparada para continuar su evolución a medida que surgen nuevas tecnologías y se adaptan a las cambiantes demandas del mercado.
Aspectos Clave:
- Impresión 3D Combinada con Pintura Electrostática: La integración de la impresión 3D con procesos de pintura electrostática podría permitir la fabricación de productos complejos con recubrimientos personalizados y de alta calidad en una sola etapa de producción.
- Nano Recubrimientos: Los avances en nanotecnología están permitiendo el desarrollo de recubrimientos que ofrecen propiedades excepcionales a nivel microscópico, como una resistencia extremadamente alta a la corrosión, a los arañazos, y a otros daños superficiales.
- Personalización en Masa: La capacidad de automatizar y controlar con precisión el proceso de pintura electrostática permitirá la personalización en masa, donde los productos pueden ser fabricados y recubiertos según las especificaciones exactas del cliente sin aumentar los costos de producción.
Ejemplo de Innovación: Una empresa de tecnología avanzada está explorando el uso de nano recubrimientos electrostáticos en la fabricación de dispositivos médicos, mejorando la durabilidad y la resistencia a la corrosión sin comprometer la biocompatibilidad.
La pintura electrostática continúa siendo un componente esencial en la fabricación industrial, ofreciendo beneficios que incluyen eficiencia, calidad, sostenibilidad, y seguridad. A medida que las tecnologías y las tendencias evolucionan, las empresas que adoptan estas innovaciones estarán mejor posicionadas para competir en un mercado global cada vez más exigente.
Con la automatización, los recubrimientos multifuncionales, y el enfoque en la sostenibilidad, la pintura electrostática no solo seguirá siendo relevante, sino que también jugará un papel clave en el futuro de la fabricación avanzada.
Los hornos de curado para pintura electrostática son equipos esenciales en los procesos de acabado de piezas metálicas o no metálicas que han sido recubiertas con polvo de pintura electrostática. Este tipo de pintura se aplica mediante un proceso de carga electrostática que permite que el polvo se adhiera a la superficie de la pieza, y luego, para que el recubrimiento se adhiera de manera permanente y obtenga la resistencia y durabilidad necesarias, es necesario someterlo a un proceso de curado en horno.
El horno de curado es un equipo de calefacción controlada que está diseñado para proporcionar el calor necesario para que la pintura electrostática se fusione y se cure. Estos hornos funcionan generalmente con electricidad, gas o incluso vapor. En su interior, la temperatura se mantiene dentro de un rango específico, generalmente entre 160°C y 200°C, dependiendo de las especificaciones del material y el tipo de recubrimiento utilizado. El tiempo de curado varía en función del grosor del recubrimiento y de la capacidad de absorción térmica del sustrato, pero por lo general, se encuentra en un rango de 15 a 30 minutos.
Los hornos de curado son fundamentales para asegurar que la pintura aplicada tenga las características deseadas, tales como una mayor resistencia a la abrasión, la corrosión, el calor y los productos químicos. Además, estos hornos permiten una mejora en la estética del producto final, dado que el curado asegura una superficie más uniforme y duradera.
Existen diferentes tipos de hornos de curado, dependiendo de las necesidades específicas del proceso de producción. Los hornos convencionales son los más comunes y funcionan mediante circulación de aire caliente, que se distribuye de manera uniforme en todo el interior del horno. Algunos hornos son de tipo “convencional”, en los que se utiliza un sistema de convección para calentar el aire, mientras que otros emplean la tecnología de infrarrojos, la cual ofrece una distribución de calor más rápida y eficiente.
Uno de los aspectos más importantes a considerar en los hornos de curado es la capacidad de mantener una temperatura uniforme durante todo el proceso. Esto no solo es vital para garantizar un curado adecuado, sino también para evitar defectos en la pintura, como la formación de burbujas, manchas o una curadura incompleta. Para lograr esto, muchos hornos modernos incorporan sistemas de control de temperatura y ventilación de alta precisión, que permiten una distribución homogénea del calor.
Los hornos de curado también deben ser diseñados de manera que optimicen el consumo de energía, ya que el proceso de curado puede consumir una gran cantidad de electricidad o combustible. Los hornos de alta eficiencia energética están equipados con sistemas de aislamiento mejorados, así como con sistemas de recuperación de calor, que ayudan a reducir el consumo energético global y a mejorar la sostenibilidad del proceso de pintura.
Además de su función principal de curado de pinturas electrostáticas, los hornos de curado también desempeñan un papel crucial en el control de la calidad de la pintura aplicada. Durante el proceso de curado, el calor aplicado permite que las moléculas de la pintura se fusionen de manera adecuada, formando una capa dura y resistente. Un curado deficiente puede resultar en una pintura frágil, que puede ser propensa a descascararse o despegarse con el tiempo.
En la industria moderna, los hornos de curado para pintura electrostática no solo se utilizan en el recubrimiento de metales, sino también en una variedad de otras aplicaciones, como en la fabricación de electrodomésticos, automóviles, electrodomésticos, muebles y componentes electrónicos. El desarrollo de hornos de curado de alta tecnología ha permitido a las empresas lograr una mayor eficiencia en sus líneas de producción, al tiempo que mantienen una alta calidad en los productos finales.
En resumen, los hornos de curado para pintura electrostática son una parte vital de los procesos industriales que requieren recubrimientos duraderos y de alta calidad. Estos hornos deben ser diseñados cuidadosamente para garantizar que se mantenga una temperatura uniforme, eficiente y controlada durante todo el proceso, para asegurar que la pintura aplicada sea duradera, resistente y estéticamente atractiva.
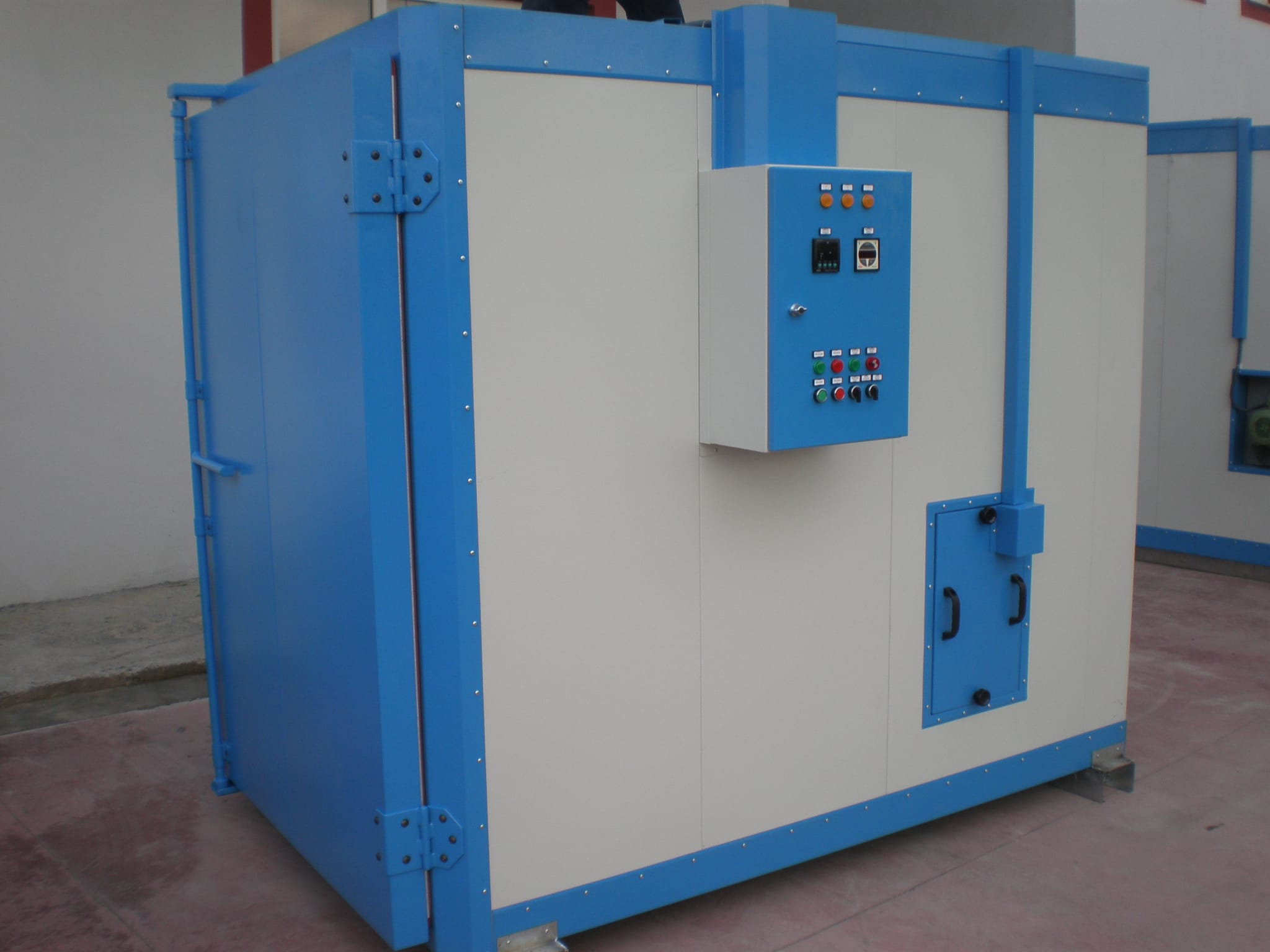
El avance en la tecnología de hornos de curado ha impulsado la mejora en la calidad y la eficiencia de los procesos industriales de pintura electrostática. Con la integración de sistemas de control de temperatura más precisos, sensores avanzados y tecnologías de monitoreo en tiempo real, los hornos modernos permiten una regulación más estricta de las condiciones del proceso de curado. Esto no solo asegura una mayor uniformidad en los recubrimientos, sino que también contribuye a la reducción de desperdicios y a un control más riguroso sobre las variables que afectan la calidad del acabado final.
Una de las innovaciones más destacadas en los hornos de curado para pintura electrostática es el uso de hornos de circulación forzada de aire, que permiten una distribución más eficiente del calor. En estos hornos, el aire caliente es movido por ventiladores de alta velocidad, lo que mejora la transferencia de calor hacia las piezas y acelera el proceso de curado. Estos sistemas también son altamente efectivos en la reducción de zonas frías dentro del horno, que podrían afectar negativamente el proceso de curado.
Por otro lado, los hornos con tecnología de infrarrojos (IR) han ganado popularidad debido a su capacidad para calentar las superficies de manera más rápida y localizada. Los rayos infrarrojos calientan directamente las piezas a través de la radiación, sin la necesidad de calentar todo el aire dentro del horno, lo que mejora la eficiencia energética y reduce los tiempos de curado. Esta tecnología es particularmente útil cuando se trabajan con piezas de geometrías complejas o cuando se requiere un control más preciso del calentamiento.
Además, el control de la atmósfera dentro del horno juega un papel fundamental en la calidad del acabado. Algunos hornos modernos están equipados con sistemas de recirculación de gases, lo que ayuda a mantener un ambiente controlado y reduce la emisión de compuestos orgánicos volátiles (COVs), mejorando la sostenibilidad ambiental del proceso. Estos sistemas no solo permiten un mejor control de la temperatura, sino que también ayudan a minimizar la contaminación y optimizar el uso de recursos energéticos.
Otro factor a considerar en los hornos de curado es la velocidad de la línea de producción. Para las aplicaciones industriales de alto volumen, es crucial que el horno pueda mantener un flujo constante de piezas a través del proceso de curado sin comprometer la calidad del recubrimiento. La automatización de la carga y descarga de piezas, así como el control automatizado de la temperatura y el tiempo de curado, son características clave que permiten a los hornos modernos adaptarse a las demandas de producción en masa.
En cuanto a la seguridad, los hornos de curado deben estar diseñados con medidas de protección que garanticen la seguridad tanto de los operarios como de las instalaciones. Los sistemas de aislamiento térmico son fundamentales para prevenir quemaduras y accidentes, mientras que las alarmas y los sistemas de control de temperatura aseguran que el proceso se realice dentro de los parámetros establecidos. Además, el monitoreo constante de las condiciones dentro del horno garantiza que cualquier fallo en el sistema pueda ser detectado y corregido rápidamente, minimizando el riesgo de daño a las piezas o de accidentes.
A lo largo de los años, la creciente preocupación por la sostenibilidad y el ahorro energético ha llevado a los fabricantes a desarrollar hornos de curado con características más ecológicas. Esto incluye el uso de materiales con mejores propiedades de aislamiento térmico, la incorporación de sistemas de recuperación de calor y la optimización de la eficiencia energética en general. Los hornos de curado de última generación están diseñados no solo para ofrecer un alto rendimiento en términos de calidad y velocidad, sino también para minimizar su huella ambiental, ajustándose a las normativas y estándares internacionales sobre emisiones y eficiencia energética.
El mantenimiento adecuado de los hornos de curado es otro aspecto crucial para garantizar su funcionamiento eficiente y prolongar su vida útil. Esto incluye la limpieza regular de los componentes, la verificación del sistema de ventilación y la calibración de los controles de temperatura y humedad. Además, es esencial realizar un seguimiento constante del estado de las piezas de recambio, como los ventiladores, las resistencias y los sensores, para evitar fallos que puedan interrumpir el proceso de producción.
En conclusión, los hornos de curado para pintura electrostática son elementos fundamentales en la fabricación moderna, no solo por su capacidad para garantizar acabados de alta calidad, sino también por su contribución a la eficiencia energética y la sostenibilidad en los procesos industriales. Con los avances tecnológicos en diseño, control y automatización, los hornos de curado continúan evolucionando para satisfacer las demandas de una industria en constante cambio, mejorando la productividad, reduciendo costos y cumpliendo con los estándares ambientales más estrictos.
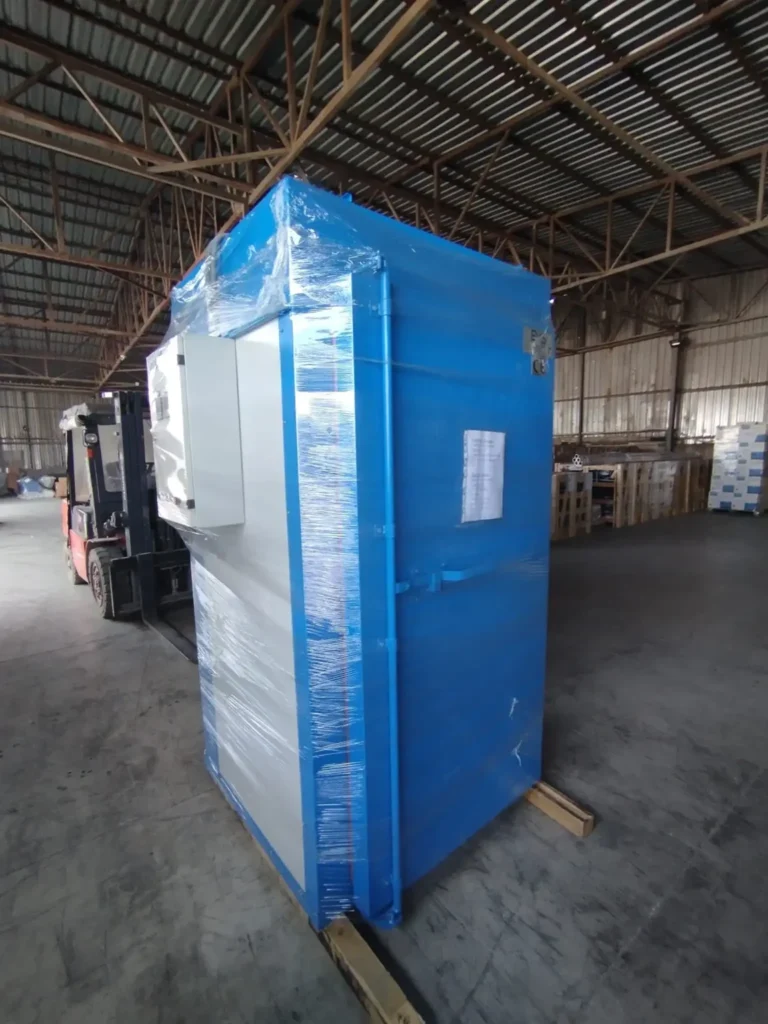
Además de los avances técnicos mencionados, el desarrollo de hornos de curado ha promovido un enfoque más integrado en los procesos de producción, contribuyendo a una mayor competitividad en sectores como la automoción, la fabricación de electrodomésticos y la industria de la construcción. La tendencia hacia la personalización y la flexibilidad en los procesos de curado ha llevado a la creación de sistemas modulares, que permiten a los fabricantes ajustar las configuraciones del horno según las necesidades específicas de cada trabajo, lo que mejora la versatilidad de la producción.
La posibilidad de ajustar de manera precisa los parámetros del horno, como la temperatura, el tiempo de curado y la velocidad de circulación del aire, permite optimizar los resultados de manera más efectiva. Esto es crucial, especialmente cuando se emplean diferentes tipos de recubrimientos o cuando las piezas tienen formas complejas que requieren un curado diferenciado. La personalización de los hornos también permite mejorar la compatibilidad con nuevos tipos de pintura electrostática, que pueden requerir condiciones de curado específicas para obtener un resultado óptimo.
El uso de tecnologías de monitoreo inteligente y la integración con sistemas de control centralizado también ha transformado la manera en que se gestionan los hornos de curado. Los sistemas avanzados de monitoreo permiten a los operadores supervisar el proceso de manera remota, asegurando que todas las variables del proceso estén dentro de los rangos preestablecidos y haciendo posible la intervención temprana en caso de que se detecten anomalías. Estas soluciones tecnológicas también permiten realizar análisis de datos en tiempo real, lo que facilita la toma de decisiones y mejora la gestión de la calidad en la producción.
En cuanto a la industria automotriz, los hornos de curado desempeñan un papel esencial en el proceso de fabricación de partes como parrillas, rines, marcos y otros componentes que requieren recubrimientos de alta durabilidad. El acabado electrostático no solo mejora la estética de estas piezas, sino que también las hace resistentes a la corrosión, lo que es fundamental en un sector donde la longevidad de los productos es un aspecto prioritario. La capacidad de los hornos de curado para adaptarse a los tiempos y ritmos de producción de la industria automotriz es clave para satisfacer la demanda de vehículos con acabados de alta calidad y resistencia.
Otro sector que se beneficia de los hornos de curado es el de la fabricación de muebles metálicos. En este ámbito, las piezas como estanterías, mesas y sillas se recubren con pintura electrostática para conseguir acabados duraderos, resistentes al desgaste y estéticamente agradables. El uso de hornos de curado en estos procesos permite lograr acabados uniformes y consistentes en productos que se utilizan en ambientes tanto domésticos como comerciales. Además, el tiempo de curado reducido que proporcionan los hornos modernos contribuye a mejorar la eficiencia de la producción, lo que es crucial para satisfacer las demandas del mercado.
Los hornos de curado también han demostrado ser fundamentales en la fabricación de electrodomésticos, como electrodomésticos de cocina, unidades de refrigeración y otros productos de consumo masivo. La pintura electrostática aplicada a estos productos no solo les proporciona un acabado atractivo, sino que también contribuye a su durabilidad, protegiéndolos de rasguños, corrosión y otros daños. En este contexto, los hornos de curado se han diseñado para trabajar de manera eficiente con componentes de diversos tamaños y materiales, lo que permite adaptarse a los distintos tipos de electrodomésticos que requieren recubrimientos de alta calidad.
Un área que ha ganado relevancia en los últimos años es la de la personalización y los acabados decorativos, donde los hornos de curado son utilizados para crear efectos especiales en la pintura, como acabados texturizados, metálicos o de alto brillo. La capacidad de controlar con precisión los parámetros de curado permite a los fabricantes ofrecer productos con acabados exclusivos y diferenciados, que se adaptan a las necesidades de los consumidores que buscan personalizar sus productos, ya sea en el ámbito del diseño de interiores, la moda o la tecnología.
Por último, la creciente preocupación por el impacto ambiental de las actividades industriales ha llevado a los fabricantes de hornos de curado a investigar y desarrollar tecnologías que minimicen las emisiones contaminantes y optimicen el uso de recursos. Algunos hornos de curado están equipados con sistemas de filtración avanzados que reducen las emisiones de compuestos volátiles, lo que contribuye a cumplir con las normativas ambientales. Además, el diseño de hornos de curado eficientes ayuda a reducir la huella de carbono, lo que es un aspecto clave para las empresas que buscan cumplir con los estándares internacionales de sostenibilidad y responsabilidad ambiental.
En conclusión, los hornos de curado para pintura electrostática se han convertido en una herramienta indispensable en una variedad de industrias debido a su capacidad para ofrecer acabados duraderos, resistentes y estéticamente atractivos. Su evolución tecnológica ha permitido mejoras significativas en eficiencia energética, control de calidad y flexibilidad de producción, lo que los hace cada vez más imprescindibles en un mercado globalizado y competitivo. Con la integración de nuevas tecnologías y un enfoque más ecológico, los hornos de curado seguirán desempeñando un papel crucial en el futuro de la fabricación industrial, contribuyendo a la mejora continua de los procesos de producción y al cumplimiento de los estándares ambientales más exigentes.
Hornos Continuos de Curado para Pintura Electrostática
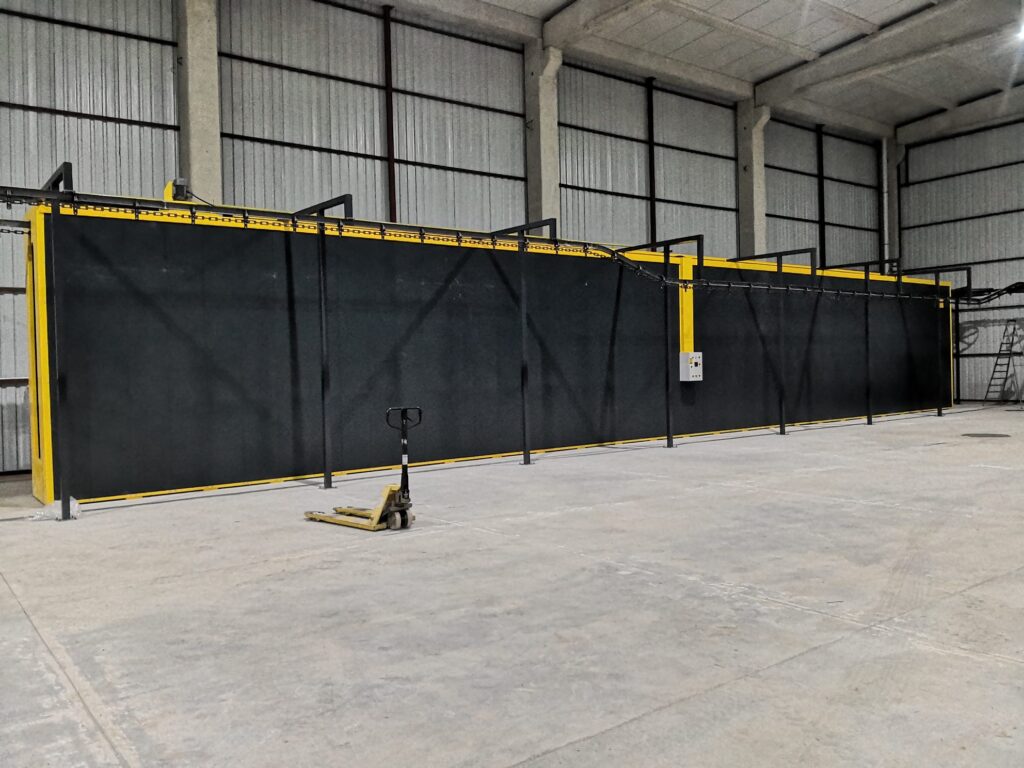
Los hornos continuos de curado para pintura electrostática son una parte esencial en el proceso industrial de recubrimiento de superficies metálicas, plásticas y otros materiales, con el objetivo de aplicar una capa de pintura electrostática que se cure de manera uniforme y eficiente. Estos hornos están diseñados para operar de manera continua, permitiendo que las piezas recubiertas con pintura electrostática pasen a través del horno de manera automática, lo que optimiza el proceso de producción y aumenta la eficiencia en la fabricación de productos con acabados duraderos.
El principio de funcionamiento de los hornos continuos de curado es similar al de los hornos convencionales, pero con la particularidad de que las piezas recubiertas con pintura electrostática se transportan de manera constante a través de una cámara de curado, generalmente en una línea de producción automatizada. Estas líneas de curado permiten el procesamiento continuo de grandes volúmenes de piezas, lo que mejora la productividad y reduce los tiempos de fabricación.
Los hornos continuos están equipados con sistemas de calefacción que pueden ser alimentados por diversas fuentes de energía, como electricidad, gas o vapor. Estos sistemas de calefacción mantienen una temperatura constante y controlada dentro del horno, generalmente en un rango de entre 160°C y 200°C, dependiendo de las especificaciones del recubrimiento y el tipo de sustrato. Este calor es necesario para fundir el polvo de pintura electrostática, permitiendo que las partículas se fusionen y curen, formando una capa sólida, resistente y duradera sobre la superficie de la pieza.
Una de las principales ventajas de los hornos continuos de curado es su capacidad para mantener un flujo constante de producción. Las piezas recubiertas de pintura electrostática se mueven a través del horno en un ciclo continuo, lo que permite una mayor eficiencia en términos de tiempo y mano de obra. Este tipo de horno es particularmente útil en industrias de alto volumen de producción, como la automotriz, la fabricación de electrodomésticos y la fabricación de componentes metálicos, donde es esencial procesar grandes cantidades de piezas de manera continua y sin interrupciones.
La configuración de los hornos continuos de curado varía según las necesidades específicas del proceso de producción. En general, estos hornos están diseñados con cámaras de calentamiento que permiten un control preciso de la temperatura y el flujo de aire. Los sistemas de circulación de aire forzado aseguran una distribución uniforme del calor dentro del horno, lo que es fundamental para evitar puntos fríos que puedan afectar la calidad del recubrimiento. Los ventiladores de alta capacidad se encargan de mover el aire caliente de manera eficiente, asegurando que todas las piezas reciban una cantidad constante de calor durante su paso por el horno.
Además, los hornos continuos de curado suelen estar equipados con sistemas de control avanzado que permiten monitorear y ajustar en tiempo real los parámetros del proceso, como la temperatura, la velocidad de la línea y la duración del curado. Estos sistemas de control son fundamentales para garantizar que el proceso de curado sea consistente y cumpla con las especificaciones requeridas para cada tipo de recubrimiento y pieza. Los sensores de temperatura, humedad y flujo de aire son componentes clave en estos sistemas, ya que permiten detectar cualquier desviación de los parámetros establecidos y ajustar automáticamente los controles para evitar defectos en la pintura.
En términos de eficiencia energética, los hornos continuos de curado están diseñados para optimizar el uso de la energía. Los avances en el aislamiento térmico de los hornos y la incorporación de sistemas de recuperación de calor han permitido reducir el consumo energético y minimizar el impacto ambiental del proceso de curado. El uso de materiales con altas propiedades de aislamiento térmico reduce las pérdidas de calor y mejora la eficiencia del sistema, lo que resulta en un menor costo operativo y en una mayor sostenibilidad.
La velocidad de la línea es otro aspecto importante en los hornos continuos de curado, especialmente en las líneas de producción de alta velocidad. Estos hornos están diseñados para procesar piezas a una velocidad constante, lo que significa que el tiempo de exposición al calor es controlado para garantizar que cada pieza se cure adecuadamente sin sobrecalentarse. La velocidad de la línea debe ajustarse cuidadosamente para cumplir con las especificaciones del recubrimiento y evitar la formación de defectos, como la formación de burbujas o la falta de curado en las áreas más gruesas de la pintura.
Los hornos continuos de curado no solo son útiles en la producción de piezas metálicas, sino que también encuentran aplicaciones en una variedad de industrias que requieren acabados duraderos y estéticamente atractivos. En la industria automotriz, por ejemplo, se utilizan para el curado de piezas como chasis, componentes del motor, parrillas y otros elementos que requieren recubrimientos resistentes a la abrasión, la corrosión y el desgaste. Los hornos continuos también son comunes en la fabricación de electrodomésticos, como lavadoras, refrigeradores y hornos, así como en la producción de muebles metálicos, donde el acabado electrostático es fundamental para garantizar la durabilidad y la estética del producto final.
Un aspecto clave en el diseño de hornos continuos de curado es su capacidad para adaptarse a diferentes tipos de recubrimientos y procesos de pintura electrostática. Los hornos pueden estar equipados con tecnologías que permiten un control preciso sobre la temperatura, el tiempo de curado y la atmósfera dentro del horno, lo que es especialmente importante cuando se utilizan diferentes tipos de pintura, como recubrimientos metálicos, mate o texturizados. Además, el diseño modular de muchos hornos continuos permite realizar ajustes rápidos en función de las necesidades del proceso, lo que aumenta la flexibilidad de la línea de producción.
La automatización es otro componente crucial de los hornos continuos de curado. La carga y descarga de las piezas recubiertas de pintura electrostática se realiza generalmente mediante sistemas automáticos, lo que reduce la intervención manual y mejora la eficiencia del proceso. Los robots industriales y los transportadores automatizados permiten que las piezas se muevan de manera constante y precisa a través del horno, garantizando que cada pieza reciba el mismo tratamiento térmico y que el proceso de curado se realice de manera eficiente y uniforme.
Finalmente, el mantenimiento de los hornos continuos de curado es un factor importante para garantizar su funcionamiento óptimo a largo plazo. Los hornos deben someterse a una limpieza regular y a la verificación de componentes clave, como los sistemas de calefacción, los ventiladores y los sensores de temperatura. Los sistemas de monitoreo también ayudan a detectar posibles fallos en los componentes, lo que permite una intervención rápida antes de que se produzcan interrupciones en la producción.
En resumen, los hornos continuos de curado para pintura electrostática son una solución fundamental en los procesos de producción industrial que requieren recubrimientos de alta calidad y durabilidad. Su capacidad para operar de manera continua, junto con los avances tecnológicos en control de temperatura, eficiencia energética y automatización, los convierte en una herramienta indispensable para sectores como la automotriz, la fabricación de electrodomésticos y otros productos de alto volumen. Con su capacidad para mejorar la productividad, reducir los costos operativos y garantizar un acabado consistente, los hornos continuos seguirán siendo una pieza clave en la fabricación de productos con acabados electrostáticos.
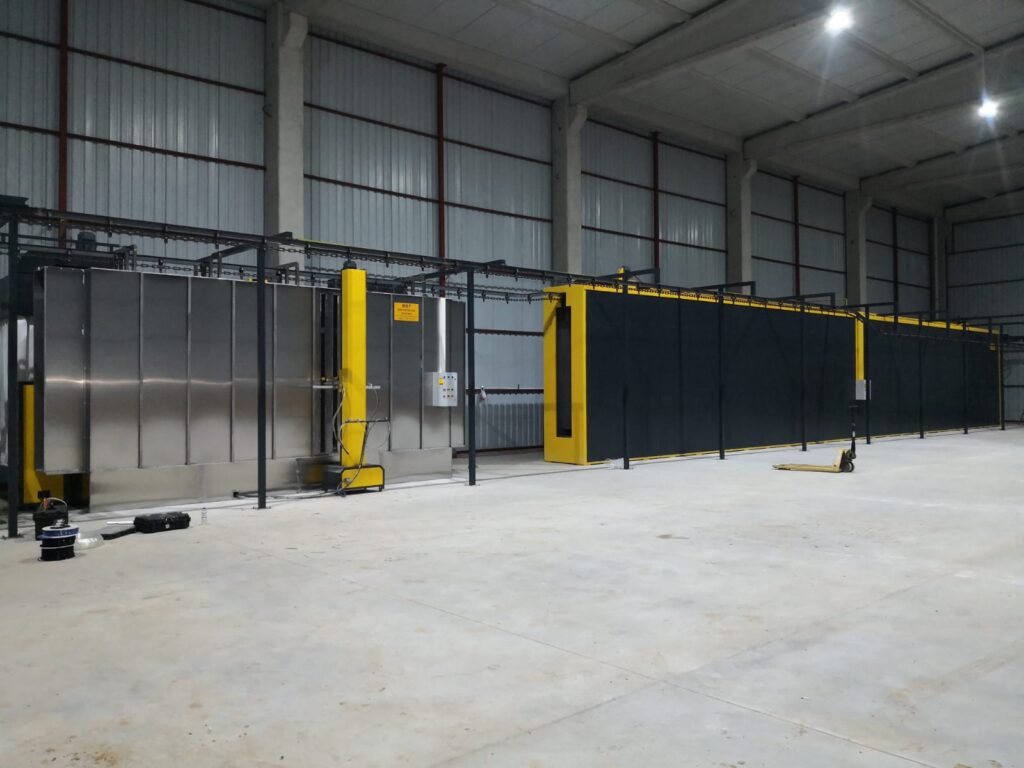
Además de las capacidades de producción continua y la eficiencia energética, los hornos continuos de curado para pintura electrostática tienen una influencia significativa en la calidad del producto final. Gracias a su diseño optimizado, estos hornos pueden garantizar una distribución uniforme del calor y una curaduría constante a lo largo del proceso, lo que es esencial para obtener recubrimientos consistentes y de alta calidad. Esta uniformidad es crucial para evitar defectos comunes en los acabados de pintura, como el agrietamiento, la formación de burbujas o la falta de adhesión de la pintura, problemas que pueden ocurrir si el calor no se distribuye de manera equilibrada.
Una de las ventajas adicionales de los hornos continuos es su capacidad para adaptarse a diversos tamaños y formas de las piezas. Dado que las líneas de producción son flexibles, los hornos pueden ajustarse para curar tanto piezas pequeñas como grandes sin comprometer la eficiencia del proceso. Esto se logra mediante la personalización de los transportadores y las cámaras de curado, lo que permite que las piezas se muevan a través del horno en función de su tamaño, peso y necesidades de curado.
La tecnología de control avanzada también juega un papel fundamental en la optimización del proceso de curado. Los hornos continuos de curado más modernos están equipados con sistemas de monitoreo que permiten a los operadores ajustar parámetros en tiempo real, como la temperatura, la velocidad del transportador y el tiempo de curado, todo a través de interfaces digitales fáciles de usar. Esto no solo mejora la precisión del proceso de curado, sino que también facilita la implementación de procedimientos de control de calidad más rigurosos, lo que reduce la posibilidad de errores y mejora la consistencia en la producción.
En cuanto a la mejora de la sostenibilidad, los hornos continuos también han sido diseñados con características que minimizan el impacto ambiental del proceso. Por ejemplo, los sistemas de recuperación de calor permiten reutilizar el calor generado durante el proceso de curado, lo que reduce la necesidad de energía adicional y contribuye a la eficiencia energética general del sistema. Además, el diseño de los hornos también está orientado a la reducción de emisiones, con sistemas de filtración de aire que capturan los compuestos orgánicos volátiles (COVs) generados durante el curado, minimizando su liberación al ambiente y cumpliendo con los estándares de calidad del aire.
Los avances en materiales de construcción también han permitido a los hornos continuos mejorar su durabilidad y resistencia. Los revestimientos resistentes a altas temperaturas y la mejora en la aislación térmica prolongan la vida útil de los hornos, reduciendo la necesidad de mantenimiento frecuente y mejorando la rentabilidad de las instalaciones. La robustez de los hornos continuos los hace aptos para operar en entornos industriales de alta demanda, como las líneas de producción automotriz, donde las condiciones de trabajo pueden ser extremas y el mantenimiento debe ser mínimo.
En el contexto de la industria automotriz, los hornos continuos de curado permiten satisfacer las crecientes demandas de producción y calidad en la fabricación de componentes de vehículos. Las piezas recubiertas con pintura electrostática deben cumplir con exigentes criterios de durabilidad, resistencia a la corrosión y estética, aspectos fundamentales para la industria automotriz. El curado uniforme de la pintura es esencial para asegurar que cada componente del vehículo no solo tenga una apariencia atractiva, sino también una protección duradera frente a las inclemencias del tiempo y el desgaste.
Por otro lado, los hornos continuos también ofrecen beneficios significativos en sectores como la fabricación de electrodomésticos. Los productos como estufas, refrigeradores y lavadoras requieren recubrimientos electrostáticos que sean resistentes al uso diario y que, al mismo tiempo, ofrezcan un acabado atractivo. Los hornos continuos pueden proporcionar el tiempo de curado necesario para lograr estas características de forma consistente y eficiente, contribuyendo a una producción más rápida y con menor margen de error.
Además de los sectores industriales tradicionales, los hornos continuos de curado también están empezando a desempeñar un papel más importante en mercados emergentes que requieren recubrimientos específicos para aplicaciones especializadas, como la industria de componentes electrónicos o la fabricación de productos personalizados. La capacidad de los hornos para adaptarse a diferentes tipos de recubrimientos, como los metálicos, brillantes, texturizados o mate, les permite ser una solución versátil en mercados donde la personalización es cada vez más demandada.
En cuanto al mantenimiento de estos hornos, aunque su diseño robusto y su integración tecnológica contribuyen a una mayor fiabilidad, es crucial implementar programas de mantenimiento preventivo para asegurar un rendimiento óptimo. La inspección regular de los sistemas de calefacción, la verificación de los sensores de temperatura y la limpieza de los componentes del horno son prácticas esenciales que garantizan la continuidad del proceso de curado sin interrupciones inesperadas. Un mantenimiento adecuado también ayuda a prevenir fallos costosos y prolonga la vida útil del equipo, lo que se traduce en ahorros a largo plazo para las empresas.
El futuro de los hornos continuos de curado para pintura electrostática está marcado por la tendencia hacia la automatización, la conectividad y la sostenibilidad. La implementación de tecnologías como el Internet de las Cosas (IoT) y la inteligencia artificial (IA) está comenzando a transformar estos sistemas, permitiendo un monitoreo y control aún más avanzados, optimizando las variables del proceso y garantizando una mayor eficiencia operativa. Los sistemas inteligentes pueden predecir y corregir fallos antes de que ocurran, lo que no solo mejora la fiabilidad del sistema, sino que también minimiza el tiempo de inactividad y mejora la productividad general.
En resumen, los hornos continuos de curado para pintura electrostática son una solución tecnológica avanzada que ofrece una gran cantidad de beneficios para diversas industrias. Su capacidad para operar de manera continua, su eficiencia energética, y su flexibilidad para adaptarse a diferentes procesos de recubrimiento los convierten en una herramienta indispensable en la producción industrial. Con la integración de tecnologías de control de última generación, mejoras en la sostenibilidad y avances en la automatización, estos hornos continúan evolucionando para satisfacer las demandas de la industria moderna, contribuyendo a productos de alta calidad, mayor rentabilidad y un menor impacto ambiental.
A medida que la tecnología avanza, los hornos continuos de curado para pintura electrostática también están experimentando una evolución en cuanto a su integración con otros sistemas de producción. La interconexión con plataformas de gestión de la fabricación, como los sistemas de ejecución de fabricación (MES, por sus siglas en inglés), permite una coordinación más fluida entre los diferentes procesos de producción. Esta conectividad no solo mejora la eficiencia operativa, sino que también facilita el seguimiento en tiempo real de los parámetros críticos del proceso, como la temperatura y la velocidad de curado, lo que garantiza que los estándares de calidad se mantengan durante toda la producción.
Además, la digitalización de los procesos de fabricación también ha permitido que los hornos continuos se integren con soluciones basadas en la nube. Esto proporciona a los fabricantes la capacidad de acceder a los datos de producción desde cualquier lugar y en cualquier momento, lo que favorece una toma de decisiones más ágil y basada en datos precisos. Con estas herramientas digitales, las empresas pueden optimizar aún más sus operaciones, realizar análisis predictivos para anticipar necesidades de mantenimiento y ajustar los procesos de curado para mejorar la calidad del producto final.
Por otro lado, la tendencia hacia la personalización de productos ha impulsado una mayor demanda de recubrimientos exclusivos, lo que ha llevado a los hornos continuos de curado a adaptarse a nuevas técnicas de acabado. La creación de efectos especiales en la pintura, como acabados de texturas complejas, colores metálicos o acabados mate de alta gama, exige un control más preciso sobre las condiciones del horno. Algunos hornos modernos incorporan sistemas de regulación automática que ajustan no solo la temperatura y la velocidad, sino también la circulación de aire, creando un ambiente que optimiza la fusión y el curado de diferentes tipos de recubrimientos. Esto permite a los fabricantes ofrecer productos con acabados más personalizados y diferenciados, sin comprometer la eficiencia del proceso.
En términos de sostenibilidad, los avances en la investigación y desarrollo de hornos continuos también se están enfocando en la reducción del consumo de recursos naturales, como el gas o la electricidad, mediante el uso de fuentes de energía renovables. Algunos fabricantes están implementando sistemas híbridos que permiten integrar fuentes de energía solar o eólica, lo que contribuye a reducir el impacto ambiental del proceso de curado. Estas innovaciones no solo son beneficiosas para el medio ambiente, sino que también ofrecen ventajas económicas a largo plazo al reducir los costos operativos.
El uso de hornos continuos también está siendo cada vez más relevante en industrias que requieren alta precisión y bajos márgenes de error, como la producción de componentes electrónicos o dispositivos médicos. En estos sectores, donde las piezas pueden ser de tamaños extremadamente pequeños o tener características técnicas complejas, el control preciso de la temperatura y el tiempo de curado es esencial para garantizar que la pintura electrostática se adhiera correctamente sin afectar las propiedades del material subyacente. La capacidad de los hornos continuos para ajustar finamente estos parámetros es vital para garantizar la integridad y funcionalidad de las piezas.
Además, la automatización y la robótica juegan un papel crucial en la evolución de los hornos continuos de curado. Los robots pueden realizar tareas como la carga y descarga de piezas, lo que reduce el riesgo de errores humanos y aumenta la velocidad de procesamiento. También se utilizan robots para inspeccionar la calidad del recubrimiento, utilizando tecnologías como visión artificial y sensores de alta precisión para detectar posibles imperfecciones en la pintura durante o después del proceso de curado. Esto permite realizar ajustes en tiempo real y asegura que solo las piezas que cumplen con los más altos estándares de calidad lleguen al cliente final.
La personalización de los hornos continuos para satisfacer las necesidades específicas de cada cliente también ha ganado relevancia. Muchos fabricantes ahora ofrecen soluciones a medida que pueden ajustarse a diferentes tipos de producción o características de las piezas a curar. Esto incluye la posibilidad de modificar el tamaño y la capacidad del horno según las demandas de producción, así como el diseño de sistemas de transporte que permitan un flujo continuo más eficiente para piezas de formas y tamaños variables. Además, los hornos continuos pueden incluir módulos adicionales, como pretratamiento o sistemas de enfriamiento rápido, lo que optimiza aún más el proceso y reduce el tiempo total de ciclo.
A medida que la tecnología en la industria de recubrimientos sigue avanzando, se espera que los hornos continuos de curado se conviertan en aún más inteligentes, con capacidades autónomas y capacidades mejoradas de autodiagnóstico. La inteligencia artificial (IA) y el aprendizaje automático tienen el potencial de revolucionar estos sistemas, ya que pueden predecir patrones de funcionamiento y optimizar dinámicamente los parámetros del proceso para mejorar la eficiencia y la calidad. Los sistemas de IA pueden, por ejemplo, ajustar automáticamente la temperatura en respuesta a las variaciones en las condiciones externas o a cambios en los materiales que se están procesando, lo que reduce la intervención humana y mejora aún más la precisión.
En el futuro, los hornos continuos de curado también podrían integrar tecnologías de fabricación aditiva o impresión 3D, lo que permitiría a las empresas producir piezas con geometrías complejas que aún puedan ser tratadas con pintura electrostática. Esta sinergia entre diferentes tecnologías de fabricación sería particularmente útil en sectores como la aeroespacial, la automotriz y la producción de maquinaria de alta precisión, donde los diseños innovadores requieren un acabado resistente y de alta calidad.
En resumen, los hornos continuos de curado para pintura electrostática seguirán evolucionando, impulsados por los avances en automatización, control de calidad, sostenibilidad y tecnologías emergentes como la inteligencia artificial. Estos hornos no solo son fundamentales para garantizar acabados de alta calidad, sino que también jugarán un papel crucial en la eficiencia de la producción, la personalización de los productos y la mejora de los procesos industriales. Con el continuo desarrollo y la integración de nuevas tecnologías, los hornos continuos de curado se consolidarán como una parte integral de las cadenas de producción modernas, adaptándose a las exigencias del mercado y contribuyendo a la creación de productos más innovadores, duraderos y sostenibles.
Hornos de Curado Tipo Batch
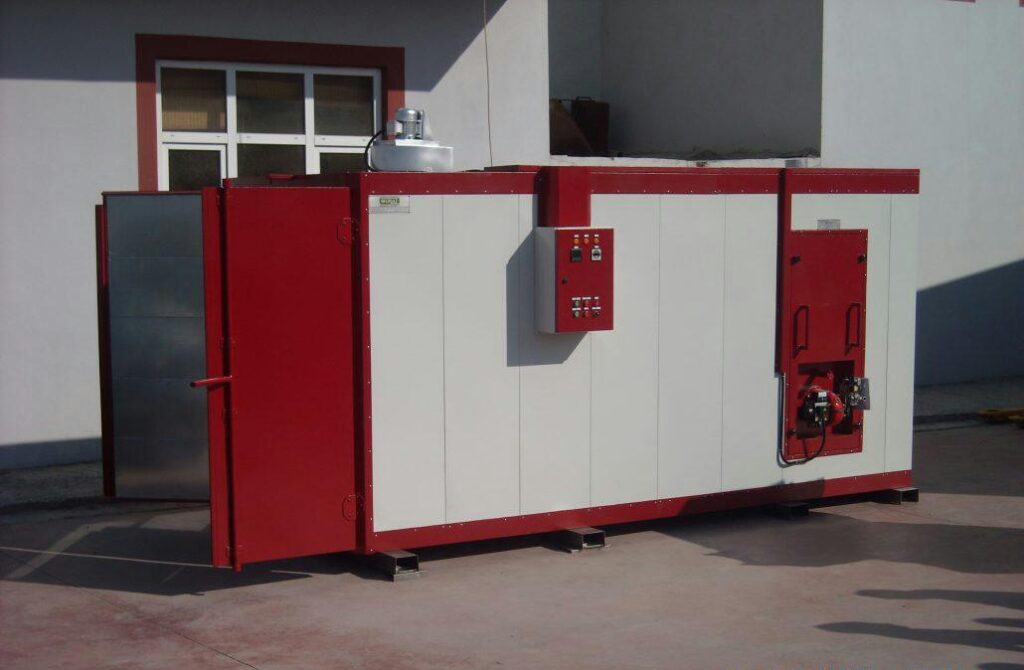
Los hornos de curado tipo batch son sistemas de curado utilizados en la industria para tratar piezas recubiertas con pintura electrostática en lotes o tandas. A diferencia de los hornos continuos, que procesan las piezas de manera continua a lo largo de un ciclo de curado, los hornos tipo batch trabajan con unidades de producción que se cargan, curan y descargan de manera discontinua. Este tipo de horno es ampliamente utilizado en aplicaciones donde se requieren lotes pequeños o procesos de curado más flexibles, especialmente en industrias de producción a menor escala o en situaciones donde se necesitan diversas configuraciones de curado para diferentes tipos de recubrimientos.
El funcionamiento de un horno de curado tipo batch se basa en el principio de calentar las piezas de manera controlada durante un periodo de tiempo específico, asegurando que el recubrimiento electrostático se cure adecuadamente. Generalmente, el proceso implica la carga de las piezas recubiertas de pintura electrostática en el horno, la aplicación de calor para fundir y curar la pintura, y luego el enfriamiento para completar el proceso. Durante este tiempo, el horno mantiene una temperatura constante y controlada, típicamente entre 160°C y 200°C, dependiendo del tipo de pintura utilizada.
La principal ventaja de los hornos de curado tipo batch es su flexibilidad. Estos hornos son ideales para procesos donde se requieren diversos tiempos de curado o temperaturas ajustables, ya que el proceso de curado se puede modificar para adaptarse a diferentes recubrimientos o características de las piezas a tratar. Esta flexibilidad los hace ideales para la producción de piezas con diferentes tamaños, formas y tipos de pintura, ya que se pueden realizar lotes de productos específicos sin necesidad de ajustar toda la línea de producción.
En términos de diseño, los hornos de curado tipo batch pueden ser de diferentes tamaños y configuraciones. Algunos modelos permiten la carga manual de las piezas, mientras que otros cuentan con sistemas automáticos de carga y descarga. Los hornos más avanzados están equipados con sistemas de control de temperatura que monitorean y ajustan la temperatura interna del horno para mantener un proceso de curado constante. En muchos casos, estos hornos incluyen sistemas de circulación de aire forzado que permiten una distribución uniforme del calor, lo que es crucial para evitar puntos fríos y asegurar un curado homogéneo de la pintura.
Los hornos de curado tipo batch suelen estar equipados con un sistema de aislamiento térmico para reducir las pérdidas de calor y mejorar la eficiencia energética del proceso. Los avances en materiales aislantes y en el diseño de cámaras de curado han permitido reducir el consumo de energía, lo que contribuye a la reducción de costos operativos y al aumento de la sostenibilidad de la producción.
El tiempo de curado en un horno de tipo batch varía según varios factores, como el grosor de la capa de pintura, el tipo de material de la pieza y las especificaciones del recubrimiento. Este tiempo puede ser controlado con precisión para garantizar que las piezas reciban el tratamiento adecuado y la pintura se adhiera de manera efectiva a la superficie. En algunos casos, el tiempo de curado se puede ajustar en función de las necesidades específicas del producto, lo que brinda un control más detallado sobre el proceso.
En cuanto a la eficiencia, los hornos de curado tipo batch suelen ser más adecuados para producciones a pequeña escala o donde la variedad de productos a procesar es amplia. En aplicaciones donde se producen grandes volúmenes de piezas del mismo tipo, los hornos continuos pueden ser más eficientes, pero los hornos tipo batch tienen la ventaja de ser más versátiles y adaptarse a cambios rápidos en el tipo de producción o en el tamaño de los lotes. Esto los convierte en una opción preferida para fábricas que producen una variedad de productos con diferentes tipos de pintura o en lugares donde la producción es más personalizada.
Además de la flexibilidad, los hornos de curado tipo batch tienen la capacidad de ofrecer un control preciso sobre las condiciones del proceso. Los sistemas de control de temperatura avanzados permiten una regulación más precisa, lo que garantiza que las piezas sean sometidas a las condiciones ideales para curar el recubrimiento electrostático sin riesgo de sobrecalentamiento o curado insuficiente. Los sensores de temperatura y los sistemas de monitoreo aseguran que el proceso se mantenga dentro de los parámetros adecuados, lo que resulta en un producto final consistente y de alta calidad.
El mantenimiento de los hornos de curado tipo batch también es una consideración importante, aunque suelen ser más fáciles de mantener que los hornos continuos debido a su diseño modular y su capacidad para ser desmontados y limpiados con mayor facilidad. El mantenimiento preventivo, que incluye la limpieza regular de las cámaras de curado, el ajuste de los sistemas de calefacción y la verificación de los controles de temperatura, es esencial para garantizar un rendimiento óptimo a lo largo del tiempo.
La eficiencia energética es otro aspecto crucial en los hornos de curado tipo batch. Si bien estos hornos no son tan eficientes en términos de volumen como los hornos continuos, los avances en el diseño y la tecnología de aislamiento han permitido que los hornos tipo batch sean más rentables. El uso de materiales aislantes de alta calidad, así como la incorporación de tecnologías de recuperación de calor, ha ayudado a mejorar la eficiencia energética de estos sistemas. Algunos hornos modernos también cuentan con sistemas de control que ajustan la temperatura y el tiempo de curado en función del tipo de pieza, lo que permite reducir el consumo de energía y maximizar la eficiencia del proceso.
En términos de aplicaciones, los hornos de curado tipo batch se utilizan en una variedad de sectores industriales, como la automotriz, la fabricación de electrodomésticos, la producción de componentes electrónicos y la fabricación de muebles metálicos. Estos hornos son ideales para procesos donde el volumen de producción es menor o más variable, o cuando se requieren cambios frecuentes en el tipo de recubrimiento o las características de las piezas. En la industria automotriz, por ejemplo, los hornos tipo batch se utilizan para curar piezas como parrillas, molduras y componentes internos del vehículo, que pueden tener diferentes tipos de pintura y acabados.
Otra de las ventajas de los hornos de curado tipo batch es su capacidad para adaptarse a la producción de piezas de formas complejas o tamaños inusuales. Los hornos pueden configurarse para procesar piezas con geometrías no estándar o con características que requieren tiempos de curado específicos. Esto los convierte en una solución ideal para la producción de piezas personalizadas o de edición limitada, donde la flexibilidad es clave.
En cuanto a las tendencias futuras, los hornos de curado tipo batch están evolucionando hacia una mayor automatización y conectividad. Los sistemas de control avanzados, como los que incorporan tecnología de la Industria 4.0, están empezando a integrarse en estos hornos, permitiendo una monitorización y control más detallado a través de plataformas digitales. Esto no solo mejora la precisión del proceso, sino que también facilita la implementación de prácticas de mantenimiento predictivo y la optimización del consumo de energía. Además, el uso de la inteligencia artificial en estos sistemas podría permitir ajustes automáticos en tiempo real, mejorando la eficiencia y la calidad del curado.
En resumen, los hornos de curado tipo batch ofrecen una solución altamente flexible y precisa para el curado de recubrimientos electrostáticos en una amplia variedad de aplicaciones industriales. Su capacidad para procesar lotes de tamaño variable, adaptarse a diferentes tipos de recubrimientos y proporcionar un control detallado sobre el proceso los hace una opción ideal para fábricas que manejan una producción diversificada o personalizada. Con avances en eficiencia energética, automatización y conectividad, los hornos de curado tipo batch seguirán desempeñando un papel clave en la industria del recubrimiento, ayudando a las empresas a mejorar la calidad de sus productos, reducir costos operativos y cumplir con las demandas de sostenibilidad y flexibilidad del mercado moderno.
Además de los avances en automatización, los hornos de curado tipo batch están viendo una integración cada vez mayor con tecnologías de monitoreo avanzado y análisis de datos. Estas mejoras permiten que las fábricas puedan recopilar y analizar datos de manera más eficiente, facilitando la toma de decisiones informadas sobre el proceso de curado. Al integrar sensores de alta precisión y sistemas de recopilación de datos en tiempo real, los operadores pueden monitorear el estado de las piezas dentro del horno, como la temperatura interna y la circulación de aire, para garantizar que el recubrimiento se cure de manera uniforme y con la máxima calidad.
En términos de sostenibilidad, uno de los enfoques que está ganando terreno es la optimización de la eficiencia energética en los hornos de curado tipo batch. Los fabricantes están implementando tecnologías avanzadas que permiten una mejor distribución del calor, minimizando las pérdidas de energía. Los hornos modernos pueden incorporar sistemas de recuperación de calor que reutilizan el aire caliente generado durante el proceso de curado, lo que reduce el consumo de energía y contribuye a una operación más ecológica. Estos sistemas permiten que el calor residual se recircule a través del sistema de calefacción, mejorando la eficiencia global del horno y reduciendo la huella de carbono de las operaciones.
Otro aspecto importante en el futuro de los hornos de curado tipo batch es la mejora de los materiales de aislamiento utilizados en su construcción. Los nuevos materiales cerámicos y compuestos de aislamiento de alta temperatura permiten que los hornos mantengan un ambiente interno más estable, reduciendo la necesidad de energía adicional para alcanzar y mantener las temperaturas de curado. Además, estos materiales mejoran la durabilidad del horno, lo que disminuye la necesidad de reparaciones y aumenta la vida útil de los equipos. El aislamiento mejorado no solo reduce el consumo de energía, sino que también ayuda a mantener un ambiente de trabajo más seguro y cómodo, minimizando las pérdidas de calor hacia el exterior y manteniendo las superficies del horno más frescas.
La facilidad de mantenimiento es otra característica que hace que los hornos de curado tipo batch sigan siendo populares en diversas aplicaciones industriales. Aunque su diseño modular ya simplifica el mantenimiento, los avances en tecnología de monitoreo remoto están permitiendo a los fabricantes supervisar las condiciones del horno sin tener que estar presentes físicamente. Esto no solo facilita la detección temprana de posibles problemas, sino que también permite realizar ajustes desde ubicaciones remotas, reduciendo tiempos de inactividad y mejorando la eficiencia operativa. Además, los sistemas de monitoreo de desgaste de piezas clave, como los calentadores o los elementos de circulación de aire, pueden alertar a los operadores sobre la necesidad de reemplazar piezas antes de que fallen por completo, lo que previene daños costosos y prolonga la vida útil del equipo.
La capacidad de los hornos de curado tipo batch para adaptarse a productos de tamaños y formas variables también es una característica clave que impulsa su uso en industrias que requieren una producción flexible. Por ejemplo, en la industria de la automoción, donde las piezas a pintar pueden ser de formas irregulares o muy grandes, los hornos tipo batch pueden ser configurados para acomodar lotes personalizados sin necesidad de realizar ajustes costosos en el equipo. Esto es particularmente importante en la fabricación de piezas personalizadas o limitadas, donde la variabilidad del tamaño y la forma de las piezas puede ser alta. Además, algunos hornos tipo batch cuentan con sistemas de transporte automatizados que permiten mover las piezas dentro del horno de manera eficiente, asegurando que cada lote se trate correctamente sin perder tiempo ni calidad.
La tendencia hacia una mayor personalización de productos también está impulsando la demanda de hornos de curado tipo batch en sectores como el de la decoración interior, la fabricación de muebles metálicos y la industria de la electrónica. En estos sectores, donde los acabados deben ser a menudo únicos o muy específicos, los hornos tipo batch ofrecen la flexibilidad necesaria para curar recubrimientos especializados, como pinturas metálicas, acabados texturizados o recubrimientos en múltiples capas. El control detallado sobre el proceso de curado, en términos de tiempo y temperatura, permite que los fabricantes logren efectos estéticos precisos y duraderos sin comprometer la calidad o la funcionalidad del producto final.
El uso de hornos de curado tipo batch también está tomando relevancia en sectores emergentes, como la fabricación de componentes electrónicos de alto rendimiento, en donde los recubrimientos deben ofrecer propiedades específicas como resistencia a la corrosión, aislamiento eléctrico o resistencia térmica. Estos sectores requieren hornos de curado altamente controlados para garantizar que los recubrimientos cumplan con las estrictas normativas de calidad y rendimiento. Los hornos de tipo batch, debido a su capacidad para realizar ajustes finos en el proceso, son ideales para satisfacer estas necesidades de precisión y personalización.
En términos de costos operativos, uno de los principales desafíos de los hornos de curado tipo batch es que pueden ser más lentos en comparación con los hornos continuos, lo que puede llevar a un mayor tiempo de inactividad entre los lotes. Sin embargo, la eficiencia en el uso de recursos, como el control de temperatura y la circulación de aire, puede ayudar a reducir los costos generales del proceso. Además, los hornos tipo batch suelen ser más económicos de adquirir y mantener en comparación con los hornos continuos, lo que los convierte en una opción atractiva para empresas que no requieren altos volúmenes de producción, pero que aún necesitan una flexibilidad considerable en su proceso de curado.
De cara al futuro, la evolución de los hornos de curado tipo batch parece orientada a la integración de soluciones más inteligentes y conectadas, que aprovechan tecnologías como el Internet de las Cosas (IoT) y la inteligencia artificial (IA) para optimizar los procesos en tiempo real. La implementación de algoritmos predictivos podría permitir a los hornos ajustar automáticamente las condiciones de curado en función de factores como la humedad ambiental, la temperatura externa o las características específicas de cada lote. Estos avances tecnológicos no solo mejorarán la eficiencia operativa y la calidad del curado, sino que también proporcionarán a los fabricantes una ventaja competitiva al reducir costos y tiempos de producción.
En resumen, los hornos de curado tipo batch continúan siendo una solución flexible y eficaz para una variedad de industrias que requieren un control preciso sobre el proceso de curado de pintura electrostática. Su capacidad para adaptarse a diferentes tamaños y tipos de piezas, junto con la mejora constante en la eficiencia energética, la automatización y la conectividad, los convierte en una herramienta clave para el futuro de la producción industrial. Con la integración de tecnologías avanzadas y la personalización de los procesos de curado, los hornos de tipo batch seguirán desempeñando un papel importante en la fabricación de productos de alta calidad, sostenibles y rentables.
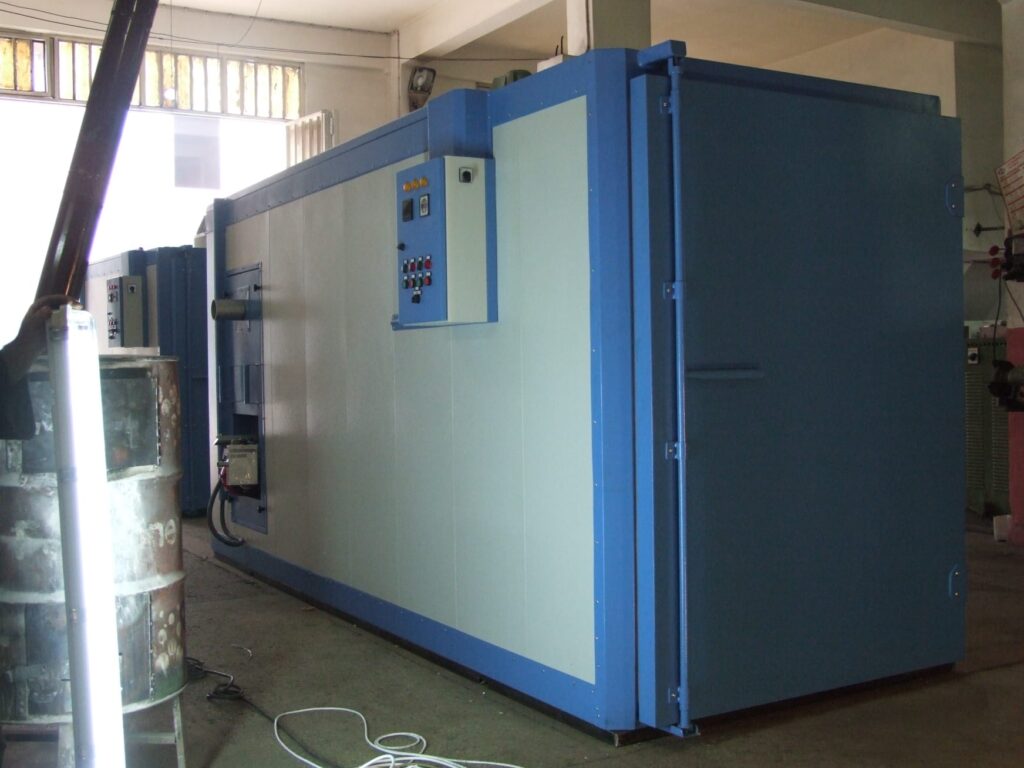
La evolución de los hornos de curado tipo batch continúa consolidándose con la introducción de nuevas tecnologías que mejoran aún más su eficiencia, flexibilidad y sostenibilidad. Uno de los avances más destacados es la implementación de sistemas de control avanzados que permiten la optimización automática del proceso de curado en función de diversos parámetros. Esto incluye el uso de sensores y actuadores que ajustan automáticamente las condiciones del horno, como la temperatura, la velocidad del aire y la distribución del calor, para garantizar que cada lote se cure de manera óptima. Estos sistemas, alimentados por inteligencia artificial (IA) y análisis de datos, pueden predecir las necesidades de curado basándose en datos históricos, lo que permite una mayor precisión y consistencia en la calidad del recubrimiento.
Además, los avances en el monitoreo remoto y la conectividad a la nube han transformado la forma en que se gestionan los hornos de curado tipo batch. Con la incorporación de plataformas de análisis de datos basadas en la nube, los fabricantes pueden acceder a información en tiempo real sobre el rendimiento de los hornos, lo que les permite tomar decisiones informadas sobre el mantenimiento, las configuraciones de temperatura y los tiempos de curado. Esta conectividad también facilita la implementación de prácticas de mantenimiento predictivo, lo que significa que los problemas potenciales pueden detectarse antes de que afecten la producción, minimizando el tiempo de inactividad y reduciendo los costos operativos.
La sostenibilidad sigue siendo una prioridad clave en el diseño de hornos de curado tipo batch. Los fabricantes están adoptando tecnologías que permiten un uso más eficiente de los recursos, como el reciclaje de calor y la reducción de la huella de carbono. Los sistemas de recuperación de calor permiten que el aire caliente generado durante el proceso de curado se recircule dentro del horno, reduciendo la necesidad de generar calor adicional. Esto no solo mejora la eficiencia energética, sino que también reduce la emisión de gases de efecto invernadero. Los hornos más modernos también incorporan materiales aislantes de última generación que minimizan las pérdidas de calor y mejoran la eficiencia térmica general.
Otro aspecto importante en la mejora de la sostenibilidad de los hornos tipo batch es la reducción del consumo de productos químicos y materiales consumibles. Algunos hornos están diseñados para ser más amigables con el medio ambiente, utilizando materiales reciclables en sus componentes y reduciendo el uso de sustancias peligrosas en sus procesos. La implementación de sistemas de filtración más eficientes también ayuda a reducir la emisión de compuestos orgánicos volátiles (COV) durante el proceso de curado, contribuyendo a la mejora de la calidad del aire en las instalaciones de producción.
En términos de adaptabilidad, los hornos de curado tipo batch están avanzando para adaptarse mejor a las necesidades de los diferentes sectores industriales. En particular, sectores como la automoción, la aeroespacial y la fabricación de maquinaria pesada están viendo un aumento en la demanda de hornos más especializados que puedan manejar piezas grandes o de formas complejas, sin comprometer la calidad del curado. Los hornos de curado tipo batch ahora incluyen soluciones personalizadas para manejar estos tipos de piezas, con sistemas de carga y descarga automatizados que optimizan la eficiencia del proceso.
Además, en industrias donde se requiere una alta precisión en los acabados, como la producción de componentes electrónicos o productos de lujo, los hornos tipo batch ofrecen el nivel de control necesario para asegurar que los recubrimientos sean aplicados con la mayor uniformidad y durabilidad posibles. Las nuevas tecnologías permiten ajustar los tiempos de curado con una precisión milimétrica, lo que asegura que los recubrimientos se curen de manera uniforme, incluso en piezas de formas irregulares o en acabados de varias capas.
Los hornos de curado tipo batch también están evolucionando en términos de la gestión de la seguridad. Con la incorporación de sistemas de seguridad mejorados, como controles automáticos de temperatura y monitoreo de gases, estos hornos están diseñados para garantizar un entorno de trabajo más seguro para los operarios. Los sistemas de monitoreo en tiempo real pueden detectar anomalías, como temperaturas demasiado altas o niveles peligrosos de gases, y activar medidas de seguridad de forma inmediata, evitando accidentes y protegiendo tanto a los trabajadores como a la calidad del producto final.
Por otro lado, los hornos tipo batch tienen una ventaja competitiva en aplicaciones de producción donde la versatilidad y la capacidad de manejar una amplia gama de productos con características específicas son esenciales. Por ejemplo, en la fabricación de productos decorativos o artículos personalizados, los hornos de curado tipo batch pueden ajustarse para curar recubrimientos especializados que requieren tiempos de secado más largos o temperaturas más bajas para garantizar que los acabados sean perfectos. Esta flexibilidad es una ventaja clave frente a los hornos continuos, que son más adecuados para producciones en masa pero menos aptos para la diversidad de lotes pequeños.
La evolución del diseño de estos hornos también ha permitido una mejora en la eficiencia del espacio. Los hornos de curado tipo batch más modernos están siendo diseñados para maximizar el uso del espacio dentro de las instalaciones de producción. Esto incluye opciones de diseño más compactas y módulos adicionales, como sistemas de enfriamiento rápido o unidades de pretratamiento, que permiten una mayor integración y flexibilidad en el proceso de curado.
En resumen, los hornos de curado tipo batch seguirán desempeñando un papel clave en la industria, especialmente en entornos donde se requiere flexibilidad, control preciso y producción de lotes pequeños o personalizados. A medida que avanzan en términos de automatización, conectividad, sostenibilidad y control de calidad, estos hornos seguirán siendo esenciales para la fabricación de productos de alta calidad en una variedad de industrias. Con la constante mejora en la eficiencia energética, el control preciso de los procesos y la capacidad de adaptarse a una variedad de aplicaciones, los hornos de curado tipo batch se mantendrán como una opción valiosa para empresas que buscan mejorar su capacidad de producción, reducir costos operativos y cumplir con los requisitos cada vez más exigentes del mercado global.
No solo fabricamos nuestros equipos de recubrimiento en polvo, sino que también los enviamos a sus instalaciones con cuidado en todo el mundo.
No somos sólo los fabricantes de su equipo de recubrimiento en polvo, también somos sus socios de entrega en todo el mundo.
En Equipo de recubrimiento en polvo EMS, entendemos que entregarle su equipo de recubrimiento en polvo de manera rápida y segura es tan importante como fabricarlo con los más altos estándares. Es por eso que ofrecemos servicios de entrega en todo el mundo a todos nuestros clientes.
Trabajamos con una red de socios de envío experimentados y confiables para garantizar que su equipo llegue a tiempo y en perfectas condiciones. También ofrecemos una variedad de opciones de envío que se adaptan a su presupuesto y necesidades.
Ya sea que necesite que le envíen su equipo a una dirección local o a un destino internacional, podemos ayudarlo. Trabajaremos con usted para elegir la mejor opción de envío para sus necesidades y para mantenerlo actualizado sobre el estado de su envío en cada paso del camino.
Entonces, cuando elige EMS para su equipo de recubrimiento en polvo, no solo obtiene los mejores productos del mercado, sino que también obtiene la mejor experiencia de entrega posible.
Contáctenos hoy para obtener más información sobre nuestros servicios de entrega en todo el mundo.
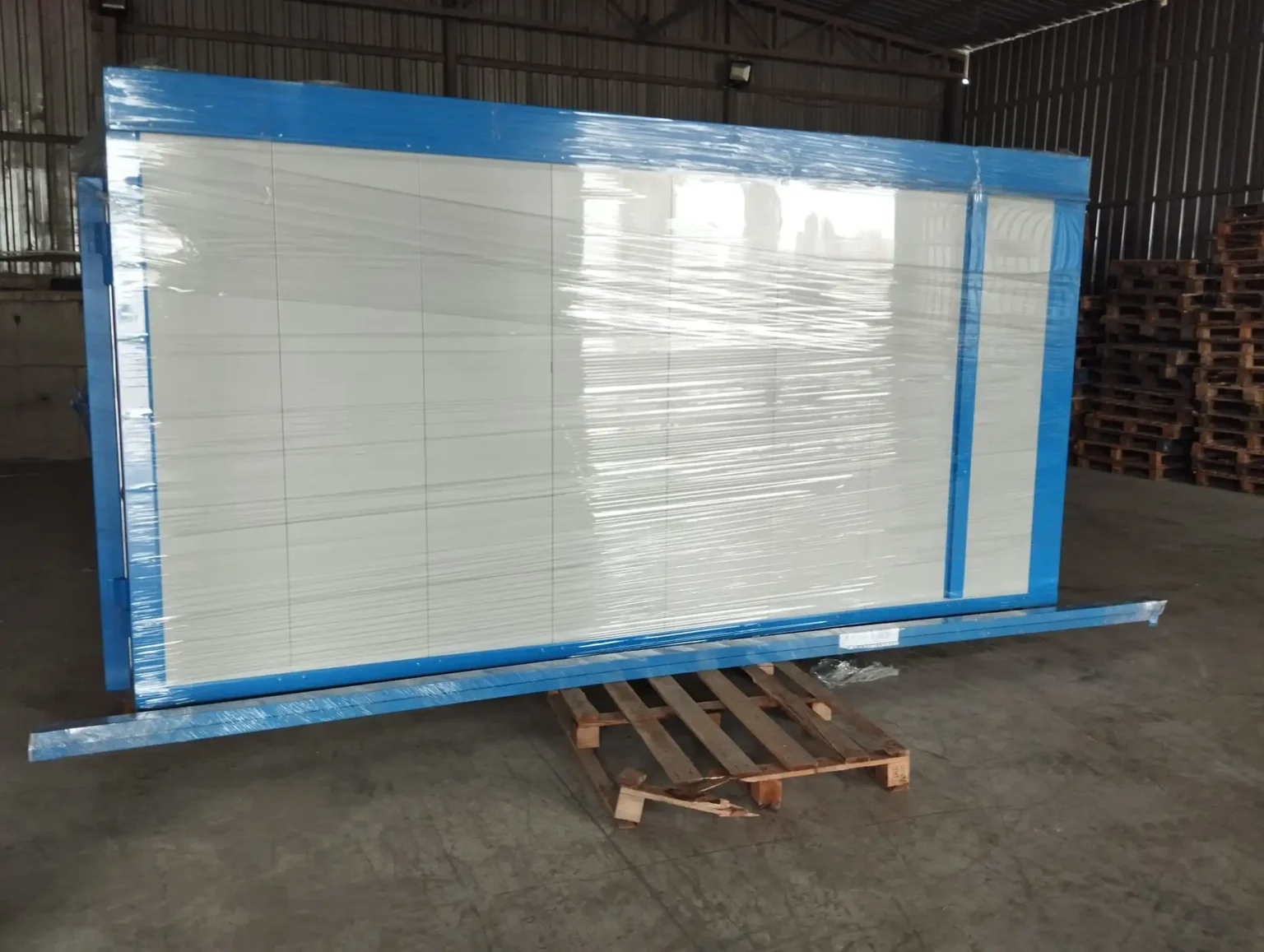