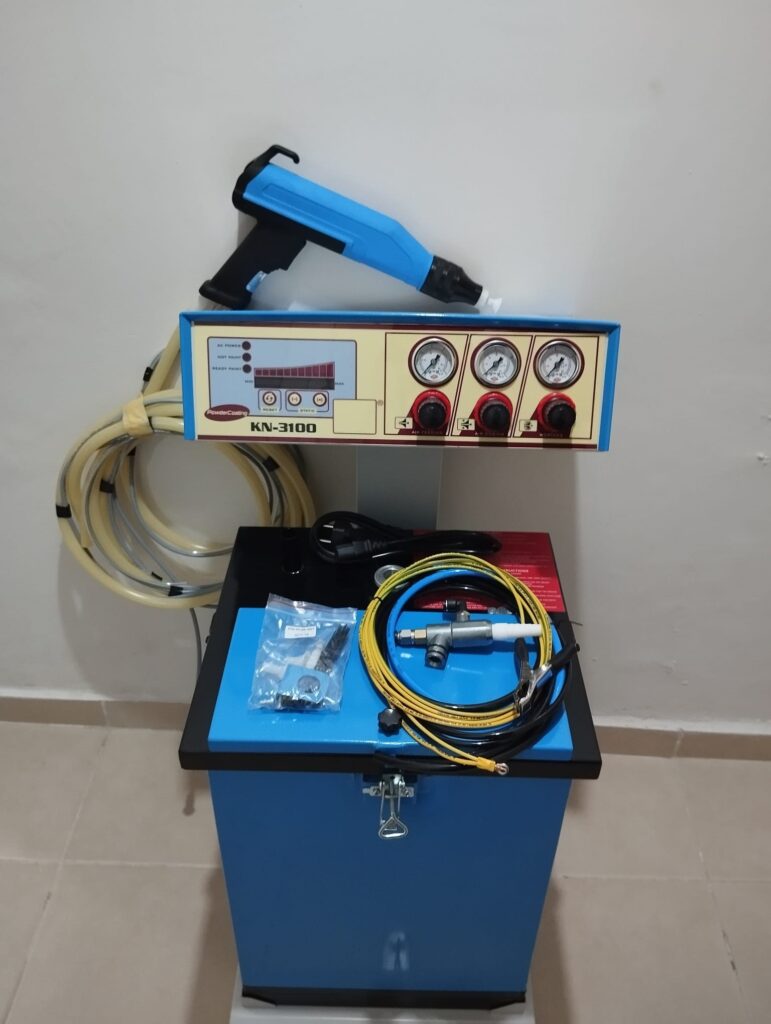
Equipos De Aplicación De Pintura Electrostática: La pintura electrostática es un proceso ampliamente utilizado en la industria para aplicar recubrimientos de alta calidad y durabilidad sobre diversas superficies. Este proceso aprovecha las propiedades electrostáticas para adherir la pintura en polvo a los sustratos, lo que resulta en un acabado uniforme y resistente. A continuación, se describen en detalle los componentes principales y el funcionamiento de los equipos utilizados en este proceso.
La pintura electrostática ha revolucionado la industria de la pintura industrial debido a su eficiencia, precisión y respeto por el medio ambiente. En el corazón de este proceso, se encuentran los equipos de aplicación de pintura electrostática, los cuales son responsables de la adherencia uniforme de la pintura en polvo sobre las superficies metálicas, lo que garantiza una excelente cobertura y acabado duradero.
Introducción a la Pintura Electrostática
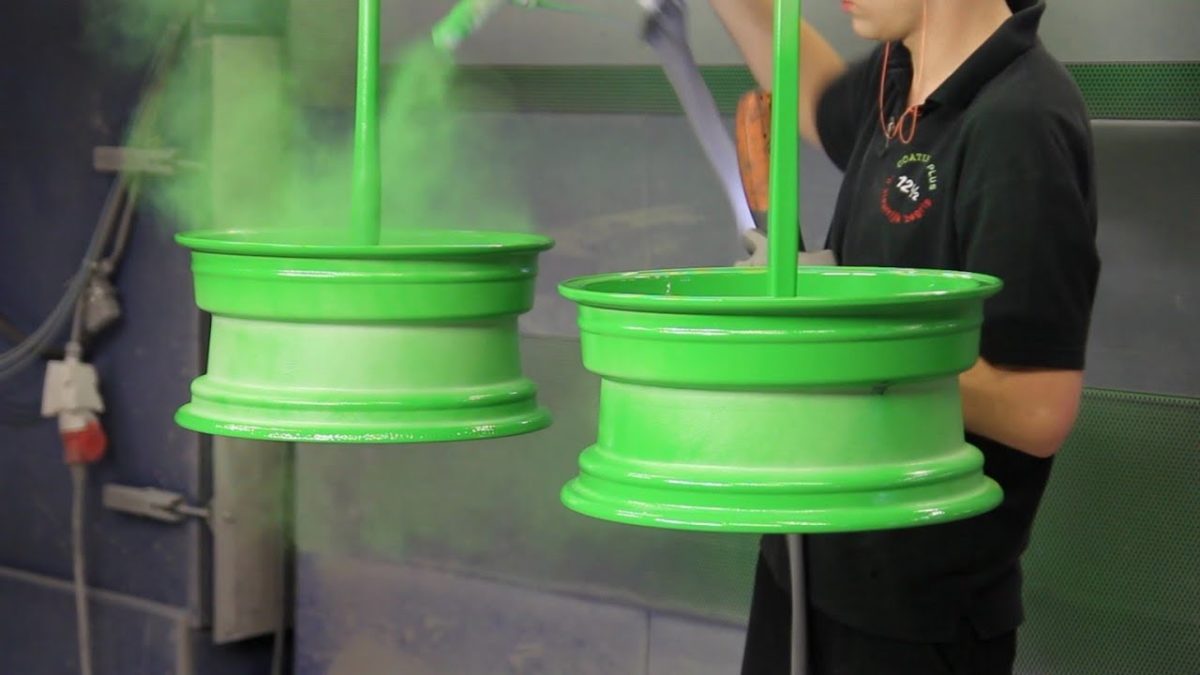
La pintura electrostática es un proceso en el que se aplica pintura en polvo a una superficie cargada eléctricamente. Los equipos de aplicación utilizan una pistola de pulverización que carga eléctricamente las partículas de polvo para que se adhieran a la superficie de manera eficiente y uniforme. Este método reduce el desperdicio de material y asegura que la cobertura sea homogénea incluso en áreas de difícil acceso.
Tipos de Equipos de Aplicación
Existen varios tipos de equipos de aplicación de pintura electrostática que se utilizan según la naturaleza del proyecto y las necesidades de la industria. Los más comunes son las pistolas manuales y automáticas.
- Pistolas Manuales de Pintura Electrostática: Son herramientas versátiles y ampliamente utilizadas en aplicaciones donde la producción es menor o donde se requiere una mayor flexibilidad. Estas pistolas permiten que los operadores ajusten la cantidad de pintura y la presión, lo que resulta útil en trabajos personalizados o en lotes pequeños.
- Pistolas Automáticas de Pintura Electrostática: Son ideales para grandes líneas de producción donde se requiere consistencia y eficiencia. Este tipo de pistola puede ser controlada por sistemas robóticos o recipricadores, lo que reduce significativamente la intervención humana, mejorando la uniformidad y reduciendo el riesgo de errores.
Ventajas de los Equipos de Aplicación de Pintura Electrostática
El uso de equipos de aplicación de pintura electrostática ofrece varias ventajas clave que lo hacen una opción preferida en la industria de recubrimientos:
- Eficiencia en el uso del material: Gracias a la carga electrostática, las partículas de polvo se adhieren mejor a la superficie del objeto, minimizando el desperdicio de material y permitiendo la reutilización del polvo sobrante.
- Calidad del acabado: Los equipos de aplicación garantizan un acabado uniforme sin defectos visibles como burbujas o marcas de pincel. Además, se logra una cobertura completa incluso en áreas difíciles de alcanzar, como esquinas y bordes complejos.
- Respetuoso con el medio ambiente: El proceso de pintura en polvo es significativamente más ecológico en comparación con los métodos tradicionales de pintura líquida. No genera VOCs (compuestos orgánicos volátiles), lo que reduce la contaminación del aire y los riesgos para la salud.
- Durabilidad: La pintura aplicada mediante estos equipos ofrece una capa resistente a la corrosión, abrasión y químicos, lo que extiende la vida útil de los productos recubiertos.
Desventajas y Desafíos
A pesar de sus numerosas ventajas, los equipos de aplicación de pintura electrostática también presentan algunos desafíos. Uno de los principales es el alto costo inicial de los equipos. Las pistolas, los sistemas automáticos y las cabinas requieren una inversión considerable, lo que puede ser prohibitivo para pequeñas empresas.
Otro desafío es la necesidad de un ambiente controlado. Para obtener los mejores resultados, los equipos de aplicación deben operarse en entornos con un control preciso de temperatura y humedad, lo que asegura que el polvo se adhiera de manera uniforme antes del curado. Además, la capacitación del personal es fundamental para manejar estos equipos de manera segura y eficiente, lo que puede implicar costes adicionales de formación y tiempo de adaptación.
Mantenimiento y Cuidado de los Equipos
El mantenimiento adecuado de los equipos de aplicación de pintura electrostática es crucial para garantizar su longevidad y eficiencia. Las pistolas deben limpiarse regularmente para evitar la acumulación de polvo que podría obstruir los conductos y afectar el rendimiento. Además, los sistemas automáticos requieren calibraciones periódicas para asegurarse de que la presión y la carga eléctrica sean correctas, lo que garantiza una aplicación uniforme del polvo.
Aplicaciones Industriales
Los equipos de aplicación de pintura electrostática se utilizan en una amplia gama de industrias, incluidas la automotriz, electrodomésticos, muebles de metal, y estructuras arquitectónicas. En la industria automotriz, por ejemplo, se utilizan para aplicar revestimientos protectores y decorativos a las carrocerías de los vehículos, proporcionando una excelente resistencia a la corrosión y un acabado de alta calidad.
En la fabricación de electrodomésticos, estos equipos se utilizan para recubrir lavadoras, secadoras y refrigeradores, lo que proporciona no solo un acabado estético, sino también una protección contra el desgaste y el óxido.
Tendencias Futuras en la Aplicación de Pintura Electrostática
La industria de la pintura electrostática está en constante evolución, y los avances tecnológicos están mejorando continuamente la eficiencia y precisión de los equipos de aplicación. En el futuro, se espera que los sistemas de aplicación sean cada vez más automatizados, utilizando inteligencia artificial y sensores avanzados para optimizar el proceso de recubrimiento. Además, las nuevas formulaciones de polvo permitirán aplicaciones más ecológicas, mejorando aún más la sostenibilidad del proceso.
Conclusión
Los equipos de aplicación de pintura electrostática son una herramienta fundamental en la industria moderna del recubrimiento. Su capacidad para proporcionar un acabado duradero, eficiente y ecológico los convierte en una elección preferida en una variedad de sectores industriales. A pesar de los desafíos relacionados con su costo inicial y la necesidad de un entorno controlado, las ventajas que ofrecen en términos de calidad y sostenibilidad los hacen indispensables en el futuro de los recubrimientos industriales.
Planta Automática de Pintura en Polvo Industrial
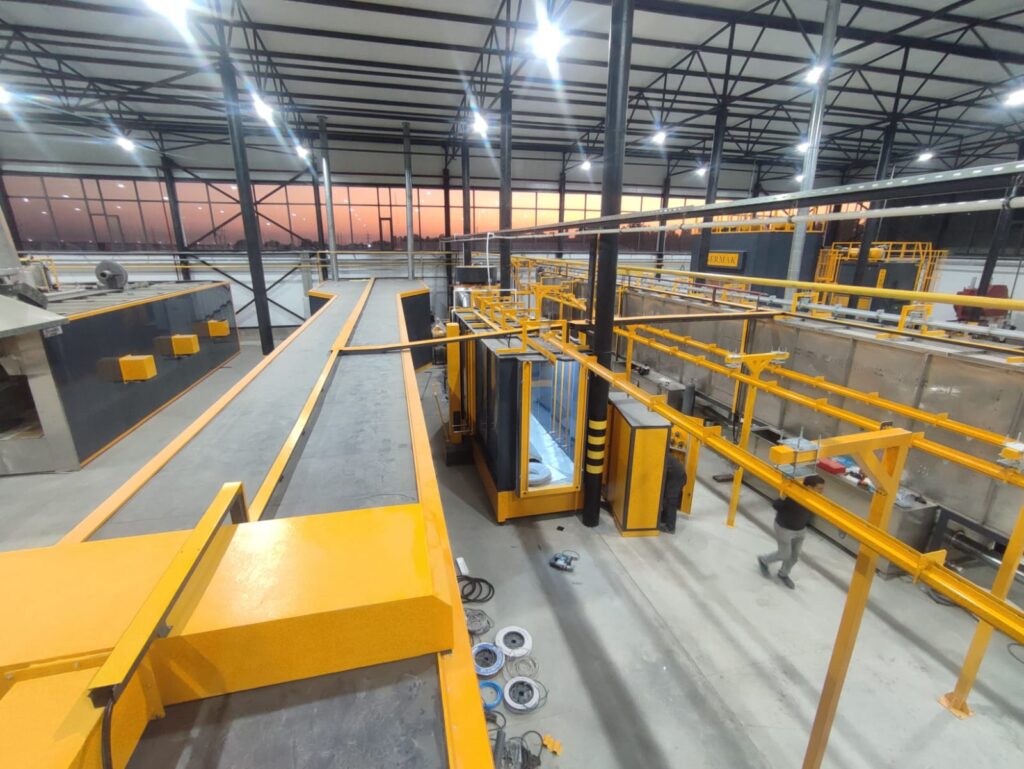
La implementación de una planta automática de pintura en polvo industrial representa un avance crucial en la producción industrial a gran escala. Estas plantas automatizadas están diseñadas para optimizar el proceso de aplicación de pintura en polvo, permitiendo una mayor eficiencia, consistencia y ahorro en recursos, lo que es especialmente útil para empresas que manejan grandes volúmenes de producción y requieren precisión en cada una de las piezas tratadas.
Introducción a las Plantas Automáticas de Pintura en Polvo
Una planta automática de pintura en polvo es un sistema integral compuesto por varios equipos interconectados, incluyendo cabinas de aplicación, pistolas automáticas, transportadores y hornos de curado. Estos sistemas son capaces de funcionar con una mínima intervención humana, lo que no solo incrementa la velocidad de producción, sino que también reduce el margen de error y asegura una aplicación más uniforme y duradera del recubrimiento en polvo.
El proceso comienza con la preparación de la superficie, seguida por la aplicación del polvo mediante pistolas automáticas, y concluye con el curado del polvo en hornos especializados. Todo el proceso está controlado por sistemas electrónicos que monitorizan la velocidad de aplicación, la carga electrostática, la temperatura de los hornos y otros parámetros clave para garantizar un acabado de alta calidad.
Componentes de una Planta Automática
Una planta automática de pintura en polvo se compone de varios elementos, cada uno desempeñando un papel crucial en el proceso:
- Cabinas de pintura en polvo: Son el área donde se aplica el polvo electrostático a las piezas. Estas cabinas pueden ser de tipo batch para lotes pequeños o continuas para producción en masa. En las plantas automáticas, las cabinas están equipadas con sistemas de recuperación de polvo, lo que permite reciclar el material no adherido, reduciendo significativamente el desperdicio.
- Pistolas automáticas: Integradas dentro de la cabina, las pistolas automáticas son controladas por sistemas electrónicos que regulan la cantidad de polvo y la carga eléctrica. Estas pistolas pueden moverse a lo largo de ejes controlados por robots o reciprocadores, asegurando una cobertura uniforme y precisa.
- Transportadores automáticos: Estos sistemas permiten el traslado de las piezas a lo largo de toda la planta. Los transportadores están programados para mover las piezas a través de las diferentes estaciones del proceso, desde la aplicación de pintura hasta el curado, asegurando tiempos de ciclo óptimos.
- Hornos de curado: Los hornos, esenciales para el proceso, son responsables de fundir el polvo sobre las superficies pintadas. La temperatura y el tiempo de curado son variables clave que deben ajustarse con precisión para garantizar que el recubrimiento se adhiera correctamente y ofrezca la resistencia deseada.
Beneficios de las Plantas Automáticas
Las plantas automáticas de pintura en polvo industrial ofrecen una serie de ventajas significativas para las industrias que buscan eficiencia y calidad en sus procesos de recubrimiento.
- Automatización completa: La automatización reduce la dependencia de la mano de obra, minimizando errores humanos y asegurando que cada pieza reciba el mismo tratamiento. Esto es particularmente útil en la producción en masa, donde la consistencia es crítica.
- Mejor aprovechamiento del material: El sistema de recuperación de polvo reduce el desperdicio de material, ya que las partículas de polvo no adheridas son recolectadas y reintroducidas en el proceso. Esto genera importantes ahorros a largo plazo y mejora la sostenibilidad del proceso.
- Incremento de la velocidad de producción: Al automatizar el proceso, las plantas pueden operar a velocidades mucho mayores que los sistemas manuales. Esto permite a las empresas aumentar su capacidad productiva y cumplir con demandas más grandes en menor tiempo.
- Control de calidad mejorado: Los sistemas electrónicos en una planta automática pueden ajustar con precisión la cantidad de polvo aplicado, la velocidad del transportador, y la temperatura del horno, asegurando un control de calidad superior y minimizando defectos.
Desafíos de la Implementación
A pesar de las numerosas ventajas, la implementación de una planta automática de pintura en polvo industrial también conlleva ciertos desafíos:
- Inversión inicial elevada: El costo de instalar una planta automatizada es considerablemente más alto que el de un sistema manual. Esto incluye no solo la compra de equipos de alta tecnología, sino también el costo de instalación, calibración, y capacitación del personal para operar y mantener el sistema.
- Requiere mantenimiento especializado: Estos sistemas automáticos necesitan un mantenimiento regular y especializado para asegurar que sigan funcionando correctamente. La maquinaria compleja, como los transportadores y las pistolas automáticas, deben ser revisadas y calibradas periódicamente para evitar tiempos de inactividad.
- Adaptabilidad limitada para productos personalizados: Aunque las plantas automáticas son extremadamente eficientes para la producción en masa, pueden ser menos flexibles para proyectos que requieren lotes pequeños o personalización, lo que puede no justificar la inversión en estos casos.
Aplicaciones Industriales
Las plantas automáticas de pintura en polvo se utilizan en una variedad de industrias que requieren acabados consistentes y de alta calidad a gran escala. Entre las industrias más beneficiadas por este tipo de tecnología se encuentran:
- Industria automotriz: Aquí se utilizan para pintar chasis, llantas, y otras piezas metálicas que requieren resistencia a la corrosión y un acabado duradero. El uso de plantas automáticas en este sector ha mejorado la eficiencia en las líneas de ensamblaje y ha permitido acabados más precisos y uniformes.
- Electrodomésticos: Empresas que fabrican lavadoras, secadoras, refrigeradores y otros electrodomésticos metálicos utilizan estas plantas para aplicar recubrimientos protectores que mejoran la durabilidad de los productos frente al uso cotidiano y los factores ambientales.
- Mobiliario metálico: La pintura en polvo es ampliamente utilizada en la industria del mobiliario para aplicar recubrimientos decorativos y protectores en sillas, mesas, estanterías, y otros artículos de mobiliario que deben resistir el desgaste diario.
Tendencias Futuras
El futuro de las plantas automáticas de pintura en polvo se orienta hacia una mayor integración de tecnologías inteligentes y sostenibles. Se prevé la incorporación de sistemas de control basados en inteligencia artificial para mejorar la precisión en la aplicación y optimizar el uso de recursos. También se están desarrollando nuevas formulaciones de polvos con menor impacto ambiental, que mejorarán aún más la eficiencia energética de los hornos de curado.
Asimismo, la automatización avanzada y el uso de robots colaborativos están mejorando la flexibilidad de estas plantas, permitiendo la posibilidad de realizar cambios rápidos en la producción sin interrumpir el flujo del proceso, lo cual es ideal para industrias que necesitan adaptarse rápidamente a las demandas del mercado.
Consideraciones Medioambientales
Una de las principales razones por las cuales las plantas automáticas de pintura en polvo han ganado popularidad es su impacto ambiental reducido en comparación con los sistemas tradicionales de pintura líquida. Al no utilizar solventes, la pintura en polvo no emite compuestos orgánicos volátiles (VOCs), que son nocivos para el medio ambiente y la salud humana.
Además, el uso eficiente de los materiales en las plantas automáticas, gracias a los sistemas de recuperación de polvo, reduce el desperdicio y permite que las fábricas operen de manera más sostenible. Este factor, junto con las nuevas innovaciones en energía para los hornos de curado, hace que estas plantas sean una opción atractiva para empresas que desean minimizar su huella de carbono.
Conclusión
Las plantas automáticas de pintura en polvo industrial representan una innovación clave para las empresas que buscan aumentar su eficiencia y reducir costos a largo plazo. Aunque su implementación conlleva un coste inicial elevado, las ventajas en términos de ahorro de material, mejora de la calidad y sostenibilidad hacen que estas plantas sean una inversión atractiva para diversas industrias. Además, con los avances en automatización y tecnología inteligente, el futuro promete aún más mejoras en eficiencia, flexibilidad y respeto al medio ambiente.
Hornos para Diversos Usos de Curado
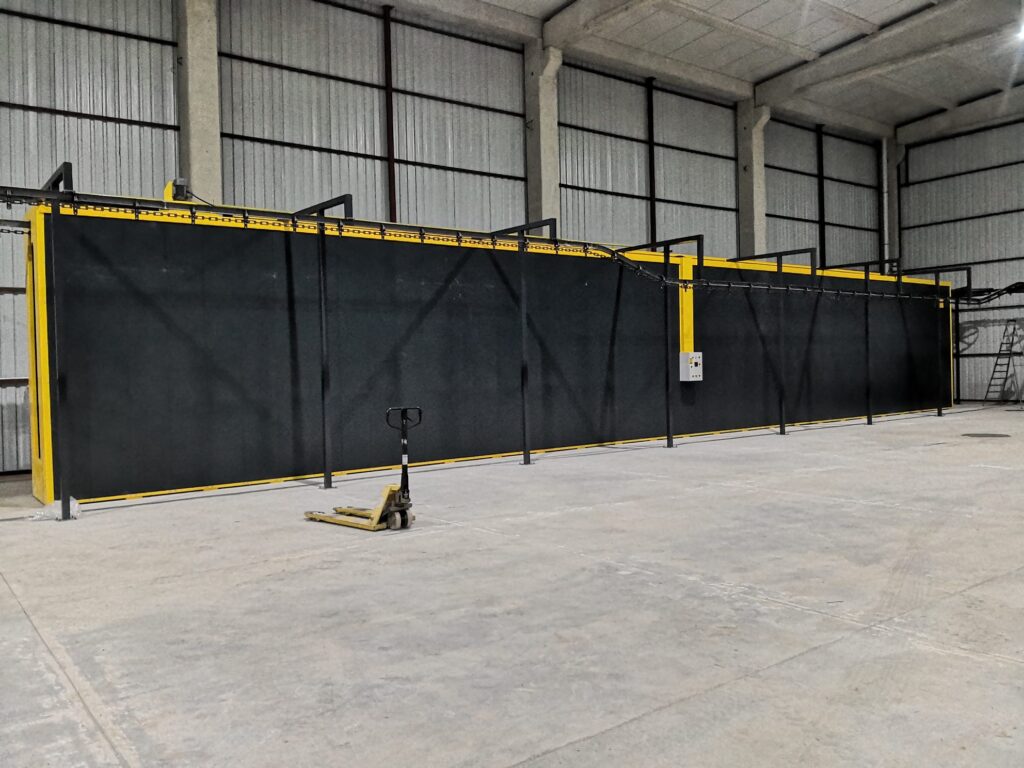
Los hornos para curado son equipos esenciales en numerosos procesos industriales, particularmente en la producción donde se aplican recubrimientos como pintura en polvo o líquidos que requieren un proceso de secado y endurecimiento para obtener los resultados deseados. Estos hornos son altamente versátiles y pueden adaptarse a una variedad de usos industriales, desde el curado de pintura hasta el tratamiento térmico de metales y cerámicas.
Introducción a los Hornos de Curado
Un horno de curado es un dispositivo que se utiliza para secar o endurecer un material, generalmente tras la aplicación de un recubrimiento o para llevar a cabo procesos térmicos específicos. En el contexto de la pintura en polvo, los hornos de curado son cruciales para asegurar que el polvo aplicado sobre las superficies se derrita y se adhiera correctamente, formando una capa homogénea y resistente. Sin este paso, el recubrimiento no tendría la durabilidad ni la calidad estética que requieren muchos productos industriales.
Tipos de Hornos para Curado
Existen varios tipos de hornos de curado, cada uno diseñado para cumplir con las especificaciones de diferentes procesos industriales. Los más comunes incluyen:
- Hornos de convección: Utilizan aire caliente circulante para calentar las piezas y asegurar que el recubrimiento se cure de manera uniforme. Estos hornos son ideales para el curado de pintura en polvo y se utilizan ampliamente en industrias como la automotriz, electrodomésticos, y muebles metálicos.
- Hornos de infrarrojos: Estos hornos usan radiación infrarroja para calentar las superficies directamente, lo que permite un calentamiento más rápido y eficiente en algunos casos. Son útiles cuando se necesitan tiempos de curado más cortos o cuando se aplican recubrimientos en superficies irregulares o complejas.
- Hornos de inducción: En este tipo de horno, se utiliza una corriente eléctrica para calentar las superficies metálicas de manera rápida y precisa. Estos hornos son más comunes en aplicaciones de tratamientos térmicos, pero también se usan en procesos de curado especializados.
- Hornos continuos: Utilizados en líneas de producción de gran escala, estos hornos permiten que las piezas se muevan continuamente a través del proceso de curado. Son ideales para plantas que operan sin interrupciones y manejan grandes volúmenes de producción.
- Hornos batch: También conocidos como hornos de lote, son diseñados para curar lotes pequeños de productos a la vez. Son adecuados para operaciones más pequeñas o para piezas que requieren un tratamiento específico y no están orientadas a la producción en masa.
Usos Industriales de los Hornos de Curado
Los hornos de curado se encuentran en una amplia gama de industrias debido a su capacidad para ofrecer soluciones de recubrimiento duraderas y de alta calidad. Algunos de los usos industriales más comunes incluyen:
- Curado de pintura en polvo: Uno de los usos más extendidos es en la industria de la pintura en polvo. Tras la aplicación de la pintura, las piezas pasan por el horno donde se calientan hasta que el polvo se funde y se adhiere a la superficie de manera uniforme, formando una capa protectora y decorativa.
- Tratamiento térmico de metales: En la industria metalúrgica, los hornos de curado también se utilizan para aplicar tratamientos térmicos a los metales, como el recocido, el endurecimiento y el templado. Estos tratamientos mejoran las propiedades mecánicas del metal, aumentando su resistencia y durabilidad.
- Curado de adhesivos y resinas: En algunos procesos de fabricación, los hornos de curado se utilizan para endurecer adhesivos, selladores o resinas que se aplican a productos industriales, como en la fabricación de componentes electrónicos o de piezas aeroespaciales.
- Industria cerámica: Los hornos son también esenciales en el proceso de curado de cerámicas, donde se requieren temperaturas extremadamente altas para transformar el barro o la arcilla en productos cerámicos duros y duraderos.
Ventajas de Utilizar Hornos de Curado
La implementación de hornos de curado en los procesos industriales ofrece una serie de beneficios clave, entre ellos:
- Consistencia y uniformidad: Los hornos de curado garantizan que los recubrimientos se apliquen y endurezcan de manera uniforme en toda la superficie del producto, lo que mejora la calidad general del acabado y la durabilidad del recubrimiento.
- Mayor durabilidad del producto final: En el caso del curado de pintura en polvo, el calor hace que el polvo se adhiera firmemente a la superficie, creando una barrera protectora contra la corrosión, el desgaste y otros factores ambientales que podrían deteriorar el producto con el tiempo.
- Eficiencia energética: Los hornos modernos están diseñados para ser energéticamente eficientes, lo que reduce los costos operativos a largo plazo. Esto es especialmente importante en grandes líneas de producción donde el horno funciona de manera continua.
- Versatilidad: Al poder ajustarse para cumplir con diferentes temperaturas y tiempos de curado, los hornos de curado son extremadamente versátiles y pueden adaptarse a una variedad de aplicaciones industriales.
Desafíos Asociados al Uso de Hornos de Curado
Aunque los hornos de curado son esenciales en muchos procesos industriales, también presentan algunos desafíos:
- Costos operativos: Los hornos, especialmente aquellos que operan de manera continua, consumen grandes cantidades de energía, lo que puede ser costoso a largo plazo si no se gestionan adecuadamente. Sin embargo, los avances en la eficiencia energética han mitigado en parte este problema.
- Mantenimiento: Los hornos requieren un mantenimiento regular para garantizar que sigan funcionando de manera eficiente. Cualquier mal funcionamiento puede interrumpir la producción y resultar en tiempos de inactividad costosos. Además, el mantenimiento debe realizarse por personal calificado, lo que puede generar costos adicionales.
- Espacio físico: En instalaciones más pequeñas, el tamaño de los hornos puede ser una limitación. Los hornos continuos, en particular, requieren un espacio considerable, lo que puede ser un desafío para algunas fábricas o plantas con espacio limitado.
Innovaciones y Tendencias Futuras en Hornos de Curado
La tecnología de hornos de curado está evolucionando rápidamente, con innovaciones enfocadas en mejorar la eficiencia energética y la precisión del curado. Una de las áreas de desarrollo más prometedoras es el uso de sensores inteligentes y controladores automatizados para ajustar con precisión la temperatura y el tiempo de curado en tiempo real, mejorando la calidad del recubrimiento y reduciendo el consumo energético.
Además, se está explorando el uso de nuevas fuentes de energía más sostenibles para los hornos, como la energía solar o el uso de calor residual de otros procesos industriales para calentar los hornos. Estas innovaciones no solo buscan reducir los costos operativos, sino también mejorar la sostenibilidad de las plantas industriales.
Impacto Ambiental de los Hornos de Curado
El impacto ambiental de los hornos de curado es un tema que ha ganado importancia en los últimos años. La necesidad de reducir el consumo energético y minimizar las emisiones de gases de efecto invernadero ha llevado a muchas industrias a adoptar tecnologías más eficientes. Además, los hornos de curado que utilizan pintura en polvo, en lugar de recubrimientos líquidos, también son más respetuosos con el medio ambiente, ya que la pintura en polvo no contiene solventes ni emite compuestos orgánicos volátiles (VOCs).
Algunos fabricantes de hornos están investigando el uso de tecnologías de curado UV o curado con microondas, que requieren menos energía y proporcionan tiempos de curado más rápidos, lo que no solo beneficia a las empresas en términos de costos, sino que también contribuye a la sostenibilidad ambiental.
Conclusión
Los hornos para diversos usos de curado son componentes clave en una amplia gama de procesos industriales, desde la aplicación de pintura en polvo hasta el tratamiento térmico de materiales. Su capacidad para proporcionar consistencia y durabilidad hace que sean esenciales para muchas industrias, aunque su operación eficiente requiere de inversiones tanto en equipos como en mantenimiento especializado. Con las tendencias hacia la sostenibilidad y la eficiencia energética, el futuro de los hornos de curado está lleno de oportunidades para mejorar aún más los procesos industriales y su impacto ambiental.
Hornos de Curado de Pintura
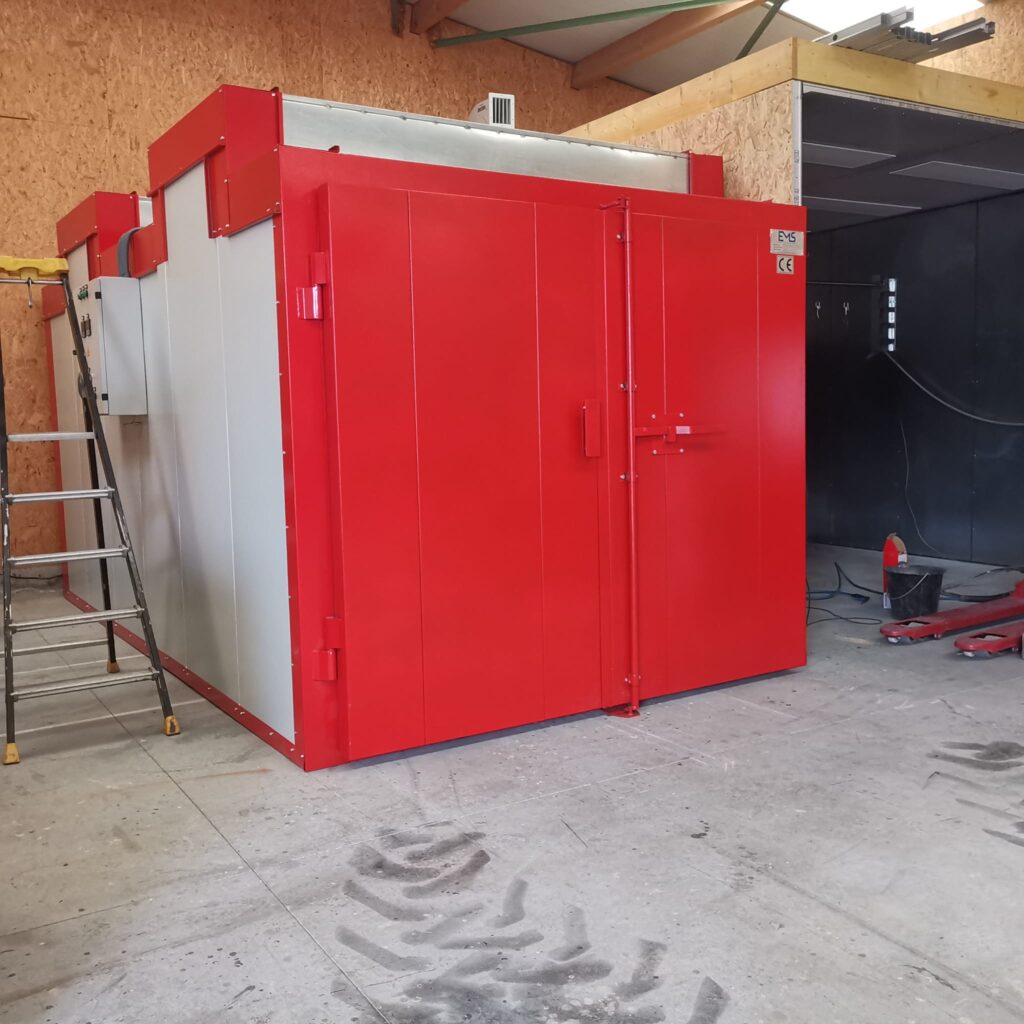
Los hornos de curado de pintura son esenciales en la industria del recubrimiento, ya que permiten que la pintura aplicada sobre una superficie, ya sea en polvo o líquida, se adhiera correctamente mediante un proceso de calentamiento controlado. Este proceso asegura que la pintura se endurezca y forme una capa resistente, protegiendo la superficie y garantizando un acabado de alta calidad.
Proceso de Curado en Pintura
El proceso de curado es un paso final crucial después de la aplicación de la pintura. La pintura en polvo, al ser aplicada mediante un proceso electrostático, necesita pasar por un ciclo de curado en un horno especializado, donde se funde y se adhiere a la superficie. Este calentamiento promueve la reacción química necesaria para que el recubrimiento alcance su máxima dureza y propiedades protectoras.
En el caso de la pintura líquida, el curado es ligeramente diferente, ya que implica la evaporación de los solventes y la polimerización de los compuestos de la pintura, lo que también requiere temperaturas controladas.
Tipos de Hornos de Curado para Pintura
Existen varios tipos de hornos diseñados específicamente para el curado de pinturas, dependiendo de las necesidades de producción y el tipo de pintura utilizada. Los principales tipos de hornos incluyen:
- Hornos de convección: Utilizan aire caliente que circula alrededor de las piezas pintadas para garantizar un curado uniforme. Este tipo de horno es el más común en la industria de la pintura en polvo, debido a su capacidad para manejar grandes volúmenes de producción y su eficacia en la distribución del calor.
- Hornos de infrarrojos (IR): Usan radiación infrarroja para calentar rápidamente las superficies pintadas. Son particularmente útiles para piezas con geometrías complejas, donde el calor puede concentrarse en áreas específicas sin afectar otras partes de la pieza.
- Hornos de inducción: Estos hornos calientan las superficies metálicas a través de campos electromagnéticos, lo que permite un curado extremadamente rápido. Son eficaces cuando se necesita acelerar el proceso de producción.
- Hornos continuos: Ideales para líneas de producción a gran escala, estos hornos permiten que las piezas pintadas se muevan continuamente a través del sistema, lo que reduce los tiempos de espera entre lotes y maximiza la producción.
- Hornos batch: Diseñados para producir lotes más pequeños o productos personalizados. Son más flexibles, ya que permiten que diferentes tipos de productos sean tratados en una misma instalación sin necesidad de grandes ajustes en la configuración del horno.
Parámetros Críticos en el Curado de Pintura
Los hornos de curado deben operar bajo parámetros cuidadosamente controlados para asegurar que el recubrimiento se adhiera correctamente y se forme una capa protectora uniforme. Entre los factores más importantes están:
- Temperatura: Cada tipo de pintura tiene una temperatura de curado óptima. La pintura en polvo, por ejemplo, generalmente requiere temperaturas que oscilan entre los 160 y 200 grados Celsius. Un control preciso de la temperatura es esencial para evitar un curado insuficiente o sobrecurado, lo que podría afectar la integridad del recubrimiento.
- Tiempo de curado: El tiempo que una pieza permanece en el horno depende del grosor de la pintura y del material de la pieza. Un curado adecuado requiere suficiente tiempo para que todo el recubrimiento alcance la temperatura óptima, pero sin excederse para evitar deformaciones o deterioros en la superficie.
- Distribución del calor: Es crucial que el calor se distribuya de manera uniforme dentro del horno, especialmente en hornos de gran capacidad. Los sistemas de convección forzada ayudan a garantizar que todas las piezas reciban la misma cantidad de calor durante el proceso.
Beneficios de los Hornos de Curado para Pintura
El uso de hornos de curado en el proceso de aplicación de pintura ofrece numerosos beneficios, tanto en términos de calidad del producto final como de eficiencia en la producción:
- Acabados duraderos: Un curado adecuado garantiza que la pintura forme una capa resistente y duradera que protege las superficies contra la corrosión, el desgaste y otros factores ambientales.
- Mayor resistencia química y mecánica: El proceso de curado mejora las propiedades químicas y mecánicas de la pintura, haciéndola más resistente a productos químicos, abrasión y rayaduras.
- Velocidad de producción: Los hornos, especialmente los continuos, permiten curar grandes volúmenes de piezas rápidamente, lo que es fundamental en industrias de alta demanda como la automotriz y la de electrodomésticos.
- Optimización del material: En el caso de la pintura en polvo, el proceso de curado en el horno asegura que todo el polvo aplicado se adhiera correctamente a la superficie, reduciendo el desperdicio y optimizando el uso del material.
Aplicaciones Industriales de los Hornos de Curado para Pintura
Los hornos de curado de pintura se utilizan en una amplia gama de sectores industriales debido a su capacidad para proporcionar acabados de alta calidad y mejorar la durabilidad de los productos. Entre las aplicaciones más comunes se incluyen:
- Industria automotriz: Los componentes metálicos, como las carrocerías de los vehículos, se benefician de los recubrimientos curados, que los protegen de la oxidación y el desgaste causado por la exposición a elementos como la lluvia y la nieve.
- Fabricación de electrodomésticos: Productos como lavadoras, secadoras y refrigeradores son recubiertos con pintura en polvo para mejorar su resistencia al uso cotidiano, así como a la exposición a humedad y productos de limpieza.
- Mobiliario metálico: Los muebles de metal, como sillas, mesas y estanterías, a menudo se recubren con pintura en polvo para proporcionarles un acabado estético y protector que resista el desgaste diario.
- Industria aeronáutica: Los hornos de curado también se utilizan en la fabricación de componentes aeronáuticos, donde se aplican recubrimientos protectores y resistentes al calor que garantizan la durabilidad de las piezas en condiciones extremas.
Desafíos en el Uso de Hornos de Curado para Pintura
A pesar de sus muchos beneficios, los hornos de curado también presentan algunos desafíos en su uso industrial:
- Consumo energético: Los hornos de curado, especialmente los de convección que requieren mantener altas temperaturas durante largos períodos, pueden ser intensivos en términos de consumo energético. Las empresas deben gestionar estos costos y buscar formas de mejorar la eficiencia energética de sus hornos.
- Mantenimiento regular: Los hornos requieren un mantenimiento constante para asegurar que el calor se distribuya uniformemente y que los componentes internos, como los ventiladores o las fuentes de calor, funcionen correctamente. El mantenimiento deficiente puede resultar en tiempos de inactividad y afectaciones a la calidad del producto.
- Tiempos de curado prolongados para ciertos materiales: Algunos materiales o recubrimientos especiales pueden requerir tiempos de curado más largos, lo que podría ralentizar la producción. Esto es particularmente relevante en líneas de producción continuas, donde los tiempos de ciclo deben ser optimizados.
Innovaciones en Hornos de Curado para Pintura
En los últimos años, ha habido varias innovaciones en el diseño y la tecnología de los hornos de curado, muchas de ellas enfocadas en mejorar la eficiencia energética y reducir el tiempo de curado. Algunas de estas innovaciones incluyen:
- Hornos híbridos: Estos combinan diferentes tecnologías de curado, como infrarrojos y convección, para proporcionar un calentamiento más rápido y eficiente. Los hornos híbridos son capaces de reducir los tiempos de curado sin comprometer la calidad del recubrimiento.
- Sistemas de control inteligente: Los hornos modernos están equipados con sensores y sistemas de control automatizados que monitorean y ajustan la temperatura y el flujo de aire en tiempo real. Esto permite optimizar el proceso de curado para diferentes tipos de recubrimientos y productos.
- Curado por microondas: Aunque todavía en desarrollo, la tecnología de curado por microondas promete reducir drásticamente los tiempos de curado al calentar los recubrimientos desde el interior hacia el exterior. Esto podría revolucionar el proceso de curado en industrias de alta demanda.
Impacto Ambiental de los Hornos de Curado para Pintura
El impacto ambiental de los hornos de curado, especialmente los que funcionan de manera continua, es una preocupación creciente en la industria. Las emisiones de gases de efecto invernadero y el alto consumo energético son aspectos que se están abordando mediante tecnologías más sostenibles. Los fabricantes de hornos están desarrollando modelos más eficientes que reducen el consumo de energía y utilizan fuentes de calor más limpias, como la electricidad o el gas natural, en lugar de combustibles fósiles.
Conclusión
Los hornos de curado de pintura son una pieza clave en el proceso de acabado industrial, garantizando la calidad, durabilidad y resistencia de los recubrimientos. A medida que la tecnología avanza, los hornos se están volviendo más eficientes y sostenibles, lo que no solo mejora la producción, sino que también reduce el impacto ambiental. El curado de pintura seguirá siendo una parte vital de muchas industrias, con innovaciones futuras que seguirán mejorando la calidad y la eficiencia de estos sistemas.
Hornos de Curado
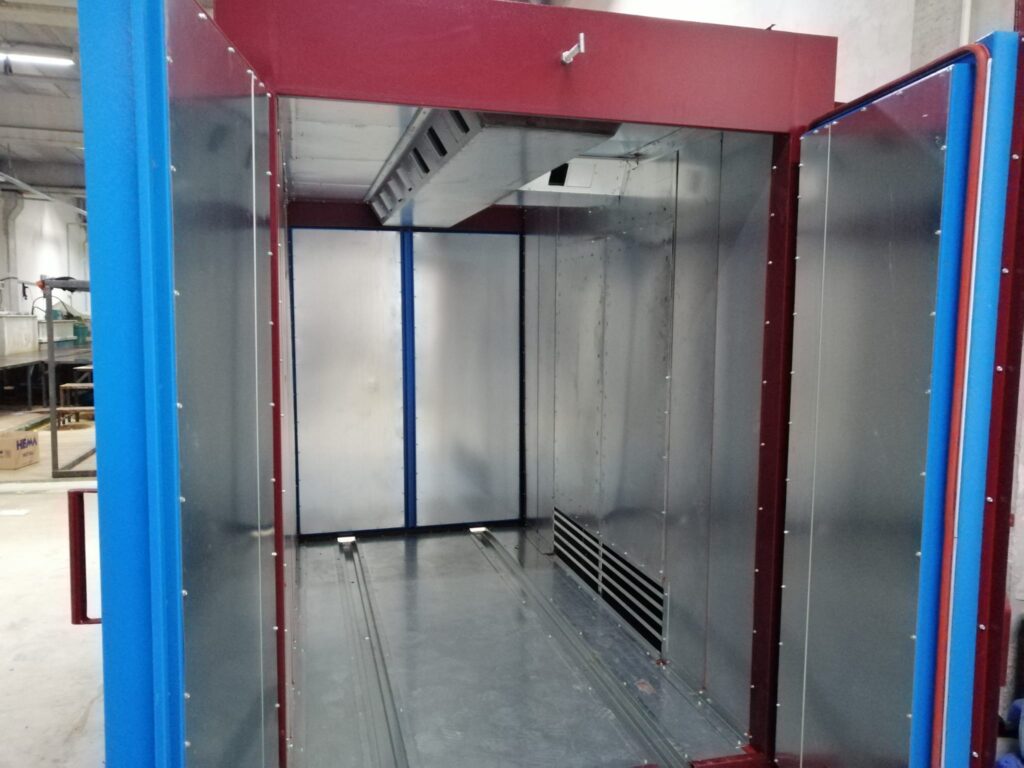
Los hornos de curado son una herramienta fundamental en el procesamiento industrial, especialmente en la fabricación de productos que requieren un acabado térmico o un tratamiento post-aplicación de recubrimientos. El curado, que implica el endurecimiento de una sustancia mediante la aplicación de calor, es esencial para garantizar la durabilidad y la resistencia de los recubrimientos, como la pintura en polvo, en una amplia gama de superficies.
¿Qué es el Curado?
El curado es un proceso en el cual una sustancia, ya sea pintura, adhesivo o un compuesto químico, se endurece o solidifica mediante la aplicación controlada de calor. Este proceso mejora las propiedades mecánicas y químicas del material tratado, haciendo que sea más resistente a los factores externos, como la humedad, el calor o los productos químicos.
En la industria de la pintura en polvo, el curado es fundamental para que el polvo aplicado sobre una superficie se derrita y forme una película continua y uniforme. Este recubrimiento, una vez curado, proporciona una capa protectora duradera que es resistente a la corrosión, el desgaste y la decoloración.
Tipos de Hornos de Curado
Los hornos de curado se pueden clasificar en varias categorías según su diseño y el método de calentamiento que utilizan. Los tipos más comunes incluyen:
- Hornos de convección: Son los más utilizados en la industria del recubrimiento en polvo. Funcionan mediante la circulación de aire caliente alrededor de las piezas que se están curando. El aire se distribuye uniformemente por todo el espacio del horno, garantizando que todas las superficies de las piezas reciban la misma cantidad de calor.
- Hornos de infrarrojos: Utilizan radiación infrarroja para calentar las piezas de manera más rápida y eficiente. Estos hornos son ideales para situaciones donde se requiere un curado rápido, ya que la radiación infrarroja calienta las superficies directamente sin la necesidad de calentar el aire circundante.
- Hornos de inducción: Emplean campos electromagnéticos para calentar las superficies metálicas, lo que permite un calentamiento más rápido y preciso. Aunque son menos comunes en el curado de pintura en polvo, se utilizan en procesos especializados donde se requiere un control térmico muy preciso.
- Hornos continuos: Estos hornos permiten que las piezas pasen a través de ellos de manera continua, lo que los hace ideales para líneas de producción en masa. Son altamente eficientes y se utilizan en plantas de producción que operan sin interrupciones.
- Hornos batch: Estos hornos están diseñados para procesar lotes más pequeños de productos. Son más flexibles y permiten realizar ajustes para diferentes tipos de piezas o recubrimientos, lo que los convierte en una opción adecuada para fábricas que manejan una variedad de productos.
Factores Clave en el Funcionamiento de los Hornos de Curado
El éxito del proceso de curado depende de varios factores clave, todos los cuales deben ser controlados cuidadosamente para asegurar un recubrimiento de alta calidad:
- Temperatura: Cada material tiene una temperatura de curado específica. En el caso de la pintura en polvo, las temperaturas de curado suelen estar entre los 160 y los 220 grados Celsius, dependiendo del tipo de polvo utilizado y del espesor del recubrimiento.
- Tiempo de curado: El tiempo que una pieza pasa en el horno también es crucial. Un tiempo de curado demasiado corto puede resultar en un recubrimiento débil que no ofrece la protección deseada, mientras que un tiempo demasiado largo puede deteriorar la calidad del recubrimiento o incluso dañar las piezas.
- Distribución del calor: Es esencial que el calor se distribuya uniformemente dentro del horno. Si una parte de la pieza recibe más calor que otra, el recubrimiento no se curará de manera uniforme, lo que podría llevar a defectos en la apariencia o en la durabilidad del recubrimiento.
Aplicaciones de los Hornos de Curado en la Industria
Los hornos de curado son esenciales en muchas industrias donde el acabado de los productos requiere un proceso de secado o endurecimiento. Algunas de las aplicaciones más comunes incluyen:
- Curado de pintura en polvo: La aplicación más conocida de los hornos de curado es en el tratamiento de superficies pintadas con polvo. Después de que el polvo se aplica mediante un proceso electrostático, las piezas se introducen en el horno, donde el calor funde el polvo y lo convierte en una capa uniforme.
- Industria automotriz: En la fabricación de automóviles, los hornos de curado son utilizados para el endurecimiento de la pintura en las carrocerías de los vehículos. La pintura curada ofrece protección contra la corrosión y mejora la estética del vehículo.
- Electrodomésticos: Productos como refrigeradores, lavadoras y estufas también pasan por un proceso de curado después de ser recubiertos con pintura en polvo, lo que les otorga mayor durabilidad y resistencia a la humedad y al uso diario.
- Componentes industriales: Muchas piezas metálicas utilizadas en maquinaria pesada y estructuras industriales son tratadas con recubrimientos protectores que requieren un curado adecuado para mejorar su resistencia a los elementos.
Ventajas de los Hornos de Curado
El uso de hornos de curado en procesos industriales ofrece una serie de ventajas, tanto en términos de la calidad del producto como en la eficiencia de producción. Algunas de las principales ventajas incluyen:
- Durabilidad del recubrimiento: Un curado adecuado garantiza que el recubrimiento se adhiera correctamente a la superficie, creando una capa resistente que puede soportar el desgaste, la corrosión y otros factores dañinos.
- Eficiencia en la producción: Los hornos de curado, especialmente los continuos, permiten curar grandes volúmenes de piezas en poco tiempo, lo que es crucial para mantener altos niveles de producción en fábricas con demanda constante.
- Control de calidad: Los hornos modernos están equipados con sistemas de control que permiten ajustar con precisión la temperatura y el tiempo de curado, asegurando que todas las piezas se traten de manera uniforme y con alta calidad.
Retos Asociados al Uso de Hornos de Curado
A pesar de sus múltiples beneficios, los hornos de curado también presentan algunos desafíos, especialmente en términos de costos operativos y mantenimiento:
- Consumo energético: Los hornos de curado pueden consumir grandes cantidades de energía, especialmente los de convección que deben mantener altas temperaturas durante largos períodos. Esto puede resultar en altos costos operativos, particularmente en fábricas de gran tamaño.
- Mantenimiento y reparación: Los hornos requieren un mantenimiento regular para asegurar su funcionamiento eficiente. Si un horno no se mantiene adecuadamente, puede haber problemas con la distribución del calor, lo que afectaría la calidad del curado y podría causar tiempos de inactividad en la producción.
- Espacio físico: Los hornos, especialmente los continuos, ocupan una cantidad significativa de espacio en las fábricas. Esto puede ser un desafío en plantas más pequeñas donde el espacio es limitado.
Innovaciones en Hornos de Curado
En los últimos años, la tecnología de hornos de curado ha avanzado significativamente, con innovaciones que mejoran la eficiencia y reducen el impacto ambiental. Algunas de estas innovaciones incluyen:
- Hornos de alta eficiencia energética: Los fabricantes han desarrollado hornos que utilizan menos energía al optimizar la distribución del calor y mejorar el aislamiento térmico, lo que reduce significativamente los costos operativos.
- Curado con infrarrojos y microondas: Estas tecnologías permiten un calentamiento más rápido y eficiente, lo que reduce el tiempo de curado y aumenta la producción.
- Sistemas de control inteligente: Los hornos modernos están equipados con sensores que monitorean continuamente la temperatura y ajustan el proceso de curado en tiempo real, asegurando un control preciso y una mayor eficiencia.
Impacto Ambiental y Sostenibilidad
El impacto ambiental de los hornos de curado, especialmente en términos de consumo energético, ha llevado a la industria a buscar soluciones más sostenibles. Los hornos de curado más nuevos están diseñados para ser más eficientes desde el punto de vista energético, utilizando fuentes de energía renovable y sistemas de recuperación de calor para minimizar el consumo de energía.
Conclusión
Los hornos de curado son una parte integral del proceso industrial, asegurando que los recubrimientos y otros materiales se adhieran correctamente y ofrezcan la durabilidad y protección necesarias. A medida que la tecnología avanza, los hornos se vuelven más eficientes, sostenibles y adaptables a las necesidades cambiantes de la industria moderna. Con una mayor conciencia sobre el impacto ambiental, las fábricas están adoptando hornos de curado más avanzados que no solo mejoran la calidad del producto, sino que también reducen su huella de carbono.
Horno Tipo Batch
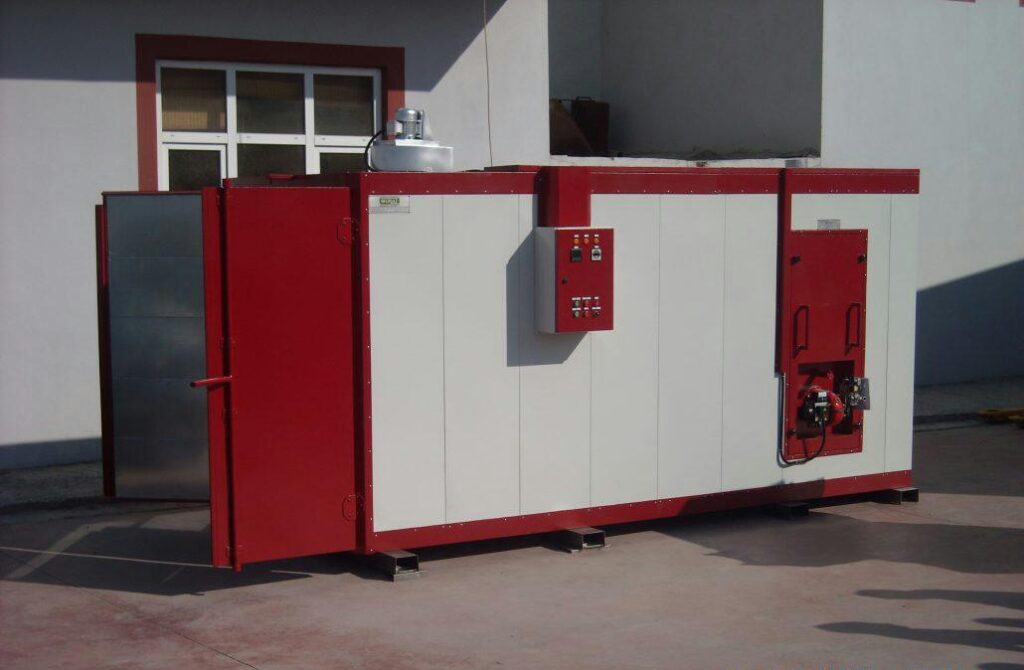
El horno tipo batch es uno de los equipos más versátiles y utilizados en la industria, especialmente en aplicaciones que requieren procesar pequeños lotes de productos o piezas que varían en tamaño y forma. Este tipo de horno es fundamental en industrias donde se busca flexibilidad y precisión en el tratamiento térmico de los materiales, y su diseño permite adaptarse a una amplia variedad de procesos, desde el curado de pinturas hasta el secado de materiales y el tratamiento térmico de metales.
¿Qué es un Horno Tipo Batch?
Un horno tipo batch, también conocido como horno por lotes, es un equipo de calentamiento diseñado para procesar un grupo o lote de piezas a la vez, en lugar de operarse de manera continua como los hornos de paso. En este tipo de horno, los productos se introducen en una cámara, donde se someten a un ciclo de calentamiento que puede variar en temperatura y duración según las necesidades del proceso.
Este tipo de horno es particularmente útil en aplicaciones donde las piezas tienen diferentes tamaños, formas o tratamientos específicos, lo que requiere un control individualizado del proceso. Los hornos tipo batch pueden ser utilizados en procesos de recubrimiento, curado, secado, templado y muchas otras aplicaciones industriales.
Ventajas de los Hornos Tipo Batch
Los hornos tipo batch ofrecen varias ventajas significativas, especialmente en términos de flexibilidad y control. Entre las principales ventajas destacan:
- Flexibilidad en la producción: A diferencia de los hornos continuos, los hornos batch permiten procesar una amplia variedad de piezas de diferentes tamaños y formas en un solo ciclo. Esto es especialmente útil en fábricas donde se trabaja con productos personalizados o donde las líneas de producción no operan de manera constante.
- Control preciso del proceso: Los hornos tipo batch permiten ajustar los parámetros de temperatura, tiempo de calentamiento y atmósfera interna según las necesidades de cada lote de productos. Esto asegura que cada pieza reciba el tratamiento térmico adecuado para garantizar la calidad y durabilidad del producto final.
- Menor desperdicio de material: Al procesar lotes más pequeños y específicos, se reduce el riesgo de defectos o sobrecalentamiento, lo que minimiza el desperdicio de material y mejora la eficiencia general del proceso.
- Mayor capacidad para productos de alta complejidad: Estos hornos son ideales para productos que requieren tiempos de curado más prolongados o procesos más detallados, como piezas de maquinaria o componentes electrónicos que necesitan un tratamiento térmico preciso.
- Versatilidad en la temperatura: Pueden operar en un amplio rango de temperaturas, lo que los hace útiles para una gran variedad de procesos industriales que incluyen curado de pintura, endurecimiento de metales y secado de compuestos.
Aplicaciones Industriales del Horno Tipo Batch
Los hornos tipo batch se utilizan en una amplia gama de industrias debido a su versatilidad y capacidad para procesar lotes de productos de manera eficiente y precisa. Algunas de las aplicaciones más comunes incluyen:
- Curado de pintura en polvo: En la industria de recubrimientos, los hornos batch son esenciales para el curado de pintura en polvo en piezas personalizadas o de tamaños variados. El proceso de curado en estos hornos asegura que la pintura se adhiera correctamente y forme una capa protectora uniforme y resistente.
- Tratamiento térmico de metales: En la fabricación de piezas metálicas, los hornos tipo batch son utilizados para procesos de templado, recocido y endurecimiento de metales. Estos procesos mejoran las propiedades mecánicas del metal, haciéndolo más resistente y duradero.
- Industria aeroespacial: En la fabricación de componentes para aeronaves, se utilizan hornos batch para el tratamiento térmico de piezas críticas que requieren un control preciso de temperatura y tiempo para asegurar su integridad estructural.
- Electrónica y semiconductores: Los hornos tipo batch son utilizados para el secado y curado de adhesivos, resinas y otros materiales utilizados en la fabricación de componentes electrónicos. El control preciso de la temperatura es fundamental en estos procesos para evitar daños a los componentes sensibles.
- Cerámica y vidrio: En la producción de artículos cerámicos y de vidrio, los hornos batch son utilizados para el secado y cocción de piezas, lo que mejora la resistencia y la durabilidad de los productos.
Componentes de un Horno Tipo Batch
El diseño de un horno tipo batch incluye varios componentes clave que permiten un control preciso del proceso de calentamiento y aseguran la eficiencia del horno. Algunos de los componentes más importantes incluyen:
- Cámara de calentamiento: Es el espacio interno donde se colocan las piezas a tratar. Esta cámara está equipada con elementos calefactores que generan calor mediante convección, radiación o inducción, dependiendo del tipo de horno.
- Controladores de temperatura: Estos sistemas permiten ajustar y monitorear la temperatura dentro de la cámara, asegurando que se mantenga dentro de los parámetros deseados durante todo el proceso.
- Sistemas de ventilación: Los hornos tipo batch a menudo están equipados con sistemas de ventilación que permiten una circulación adecuada del aire caliente, lo que garantiza un calentamiento uniforme de todas las piezas dentro de la cámara.
- Puertas aisladas: Las puertas del horno están diseñadas con aislamiento térmico para minimizar la pérdida de calor durante la apertura y cierre del horno. Esto también ayuda a mantener una temperatura estable dentro de la cámara.
- Sensores y sistemas de monitoreo: Los sensores de temperatura y otros sistemas de monitoreo garantizan que el proceso de curado o tratamiento térmico se realice de manera controlada y precisa, lo que es esencial para productos que requieren alta calidad y precisión en sus acabados.
Desafíos en el Uso de Hornos Tipo Batch
Aunque los hornos tipo batch ofrecen muchas ventajas, también presentan ciertos desafíos, especialmente en términos de eficiencia y tiempo de producción. Algunos de los desafíos más comunes incluyen:
- Menor capacidad de producción: Dado que los hornos batch procesan lotes más pequeños, su capacidad de producción es menor en comparación con los hornos continuos, lo que puede ser un problema en fábricas de alta demanda.
- Mayor tiempo de ciclo: El tiempo necesario para cargar, calentar, procesar y descargar los productos en un horno batch puede ser mayor, lo que resulta en tiempos de ciclo más largos en comparación con los hornos de paso continuo.
- Costos energéticos: Debido a que los hornos batch deben ser recalibrados y calentados para cada lote, su consumo de energía puede ser más alto, especialmente si los ciclos de producción no están optimizados.
Innovaciones en Hornos Tipo Batch
A medida que las demandas industriales evolucionan, también lo hacen los hornos tipo batch, con innovaciones que mejoran la eficiencia energética y optimizan los tiempos de ciclo. Algunas de las innovaciones más destacadas incluyen:
- Sistemas de recuperación de calor: Muchos hornos tipo batch modernos están equipados con sistemas que permiten recuperar el calor generado durante el proceso y reutilizarlo para precalentar los lotes siguientes, lo que reduce el consumo energético.
- Automatización y control avanzado: Los hornos batch actuales incluyen sistemas de control automatizados que permiten ajustar la temperatura, el tiempo de ciclo y otros parámetros de manera remota. Esto mejora la precisión del proceso y reduce el riesgo de error humano.
- Materiales de aislamiento avanzados: El uso de nuevos materiales de aislamiento térmico permite reducir la pérdida de calor, mejorando la eficiencia energética y manteniendo una temperatura constante dentro de la cámara del horno.
Impacto Ambiental de los Hornos Tipo Batch
El uso de hornos batch tiene un impacto ambiental relacionado con el consumo energético, especialmente en fábricas donde los ciclos de producción no son constantes. Sin embargo, las innovaciones en eficiencia energética y el uso de fuentes de energía más limpias han ayudado a reducir este impacto.
Las empresas están adoptando tecnologías más sostenibles, como el uso de electricidad de fuentes renovables, sistemas de recuperación de calor y mejores prácticas operativas para minimizar el consumo de energía y las emisiones de gases de efecto invernadero.
Los hornos para pintura electrostática juegan un papel fundamental en el proceso de curado de los recubrimientos aplicados a través de pintura en polvo. En el contexto industrial, la pintura electrostática es una técnica ampliamente utilizada debido a su eficiencia y su capacidad para proporcionar un acabado duradero y uniforme en superficies metálicas y otros materiales conductores. Los hornos utilizados en este proceso deben cumplir con ciertos requisitos de diseño y funcionamiento que aseguren un curado adecuado, tanto en términos de temperatura como de tiempo de exposición.
Características principales del horno para pintura electrostática
Los hornos para curado de pintura electrostática están diseñados para operar a temperaturas que oscilan entre los 180°C y 220°C, dependiendo del tipo de recubrimiento en polvo utilizado. Estos equipos permiten que el polvo, que previamente ha sido cargado eléctricamente y adherido a la superficie del objeto, se funda y se convierta en una película uniforme y resistente tras el enfriamiento.
Uno de los aspectos clave de los hornos para pintura electrostática es su capacidad para mantener una temperatura uniforme en todo el espacio de curado. Esto se logra mediante el uso de sistemas de ventilación forzada que garantizan la circulación constante del aire caliente. Adicionalmente, los hornos cuentan con paneles de control que permiten ajustar y monitorizar tanto la temperatura como la duración del proceso de curado, lo que asegura resultados consistentes y de alta calidad.
Tipos de hornos para pintura electrostática
Existen diversos tipos de hornos utilizados en la industria de la pintura electrostática, que varían en su diseño y aplicación según las necesidades de la producción. Entre los más comunes se encuentran:
- Hornos de curado tipo batch: Estos hornos están diseñados para manejar lotes pequeños o medianos de piezas, lo que los hace ideales para procesos de producción intermitente o personalizados. Las piezas son introducidas en el horno una vez aplicadas con polvo, y el proceso de curado se realiza de manera individual por cada lote.
- Hornos continuos: Diseñados para operaciones a gran escala, estos hornos permiten un flujo constante de piezas a través de una línea de producción. Las piezas se mueven mediante transportadores dentro del horno, lo que optimiza el tiempo de producción y reduce los costos operativos en grandes instalaciones industriales.
Beneficios del uso de hornos para pintura electrostática
Los hornos utilizados en el proceso de pintura electrostática ofrecen numerosos beneficios en términos de eficiencia, calidad del acabado y sostenibilidad. Entre los principales se incluyen:
- Curado rápido y eficiente: Al operar a altas temperaturas y contar con sistemas de distribución de calor optimizados, los hornos permiten que el polvo se cure rápidamente, lo que aumenta la productividad de la línea de producción.
- Acabado uniforme: La capacidad de mantener una temperatura constante en todo el horno garantiza que el recubrimiento de polvo se funda de manera uniforme sobre la superficie, lo que resulta en acabados consistentes y estéticamente atractivos.
- Reducción de emisiones: En comparación con otras técnicas de curado, como los hornos que utilizan solventes, los hornos para pintura electrostática producen menores emisiones de compuestos orgánicos volátiles (COV), lo que contribuye a procesos más limpios y respetuosos con el medio ambiente.
En conclusión, los hornos para pintura electrostática son una pieza esencial en cualquier instalación que busque aplicar recubrimientos en polvo de manera eficiente, ofreciendo acabados duraderos y de alta calidad con un impacto ambiental reducido.
Cabinas Continuas para Pintura en Polvo
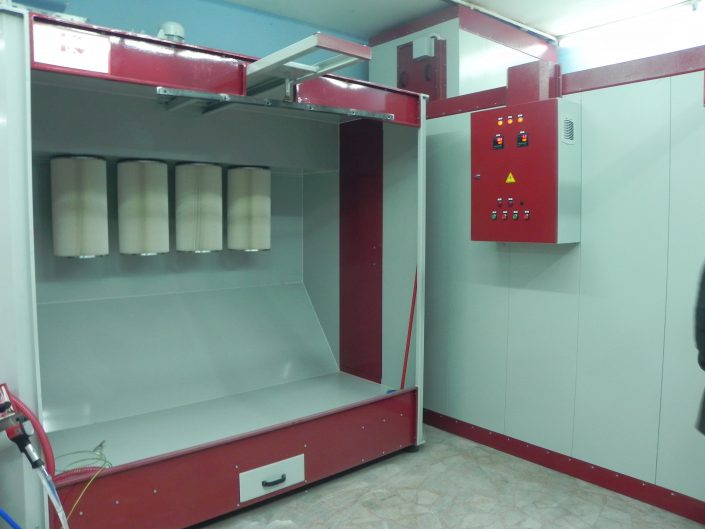
Las cabinas continuas para pintura en polvo son estructuras especializadas diseñadas para facilitar la aplicación del recubrimiento en polvo en procesos industriales de alta demanda. Estas cabinas están especialmente diseñadas para funcionar de manera continua, lo que permite una mayor productividad en líneas de producción donde se requiere un flujo constante de piezas que necesitan ser pintadas.
Características de las cabinas continuas
Una cabina continua para pintura en polvo debe contar con un sistema de transporte automático que mueva las piezas a través de las diferentes estaciones de la cabina, donde se lleva a cabo la aplicación del polvo. El uso de transportadores es clave en este tipo de cabinas, ya que asegura un flujo constante de piezas, optimizando así el proceso productivo. Además, estas cabinas suelen estar equipadas con pistolas automáticas para la aplicación del polvo, que están programadas para cubrir la superficie de las piezas de manera uniforme.
Una de las principales ventajas de las cabinas continuas es que permiten una gran flexibilidad en el tamaño y forma de las piezas que pueden ser pintadas. Además, muchas de estas cabinas están diseñadas para facilitar el cambio rápido de colores, lo que reduce el tiempo de inactividad y mejora la eficiencia operativa.
Ventajas de las cabinas continuas para pintura en polvo
- Productividad elevada: El diseño continuo de estas cabinas permite que el proceso de aplicación de polvo sea altamente eficiente, lo que resulta en una mayor cantidad de piezas pintadas en un menor tiempo.
- Control ambiental: Las cabinas están equipadas con sistemas de extracción y filtrado de aire que aseguran un ambiente controlado durante la aplicación del polvo. Esto no solo garantiza una aplicación más limpia, sino que también mejora la seguridad en el lugar de trabajo.
- Eficiencia en el uso de polvo: Los sistemas de recuperación de polvo en estas cabinas permiten recolectar el exceso de polvo no utilizado, lo que se traduce en un ahorro significativo de material.
Las cabinas continuas para pintura en polvo son, por tanto, una solución eficiente y rentable para las industrias que necesitan mantener un alto nivel de producción sin sacrificar la calidad del acabado.
Cabinas para Pintura en Polvo
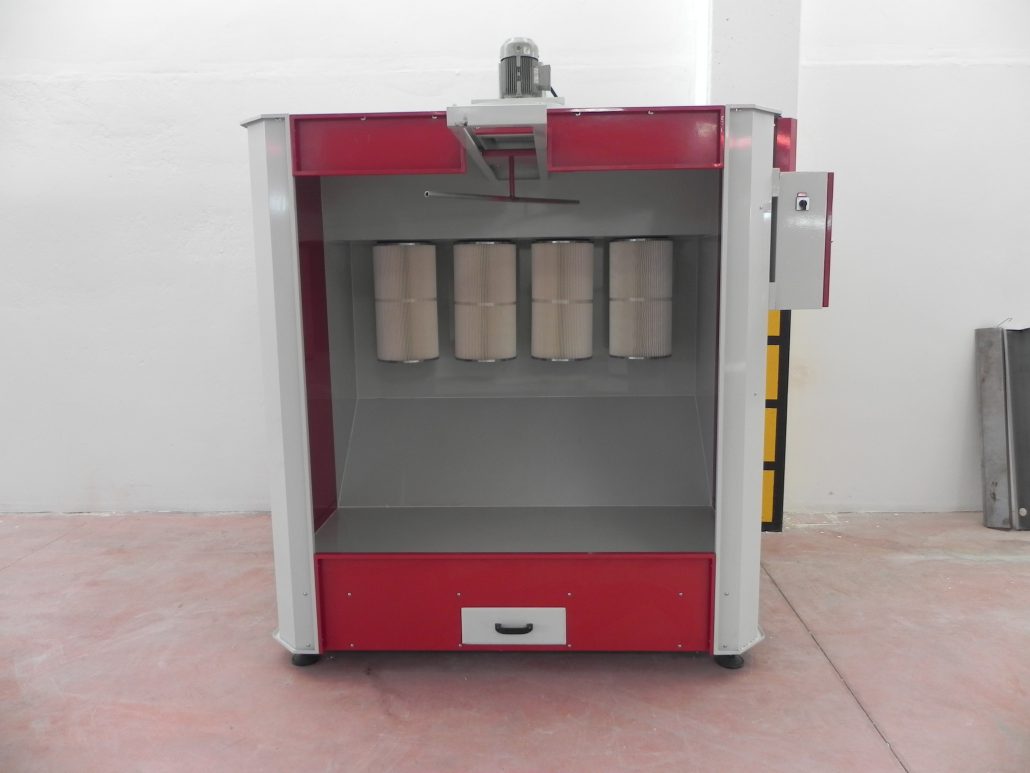
Las cabinas para pintura en polvo son espacios especialmente diseñados para la aplicación de recubrimientos en polvo en una amplia variedad de productos. Estas cabinas pueden ser tanto manuales como automáticas, dependiendo del tipo de producción y las necesidades de cada instalación industrial.
Función principal de las cabinas para pintura en polvo
Las cabinas para pintura en polvo están diseñadas para contener y controlar la aplicación del polvo, asegurando que el proceso se realice de manera eficiente y segura. Además de permitir la correcta aplicación del polvo sobre las superficies de los productos, estas cabinas también desempeñan un papel crucial en la recuperación del polvo no adherido, lo que mejora la eficiencia del proceso y reduce los costos operativos.
Hornos de Curado para Pintura Electrostática
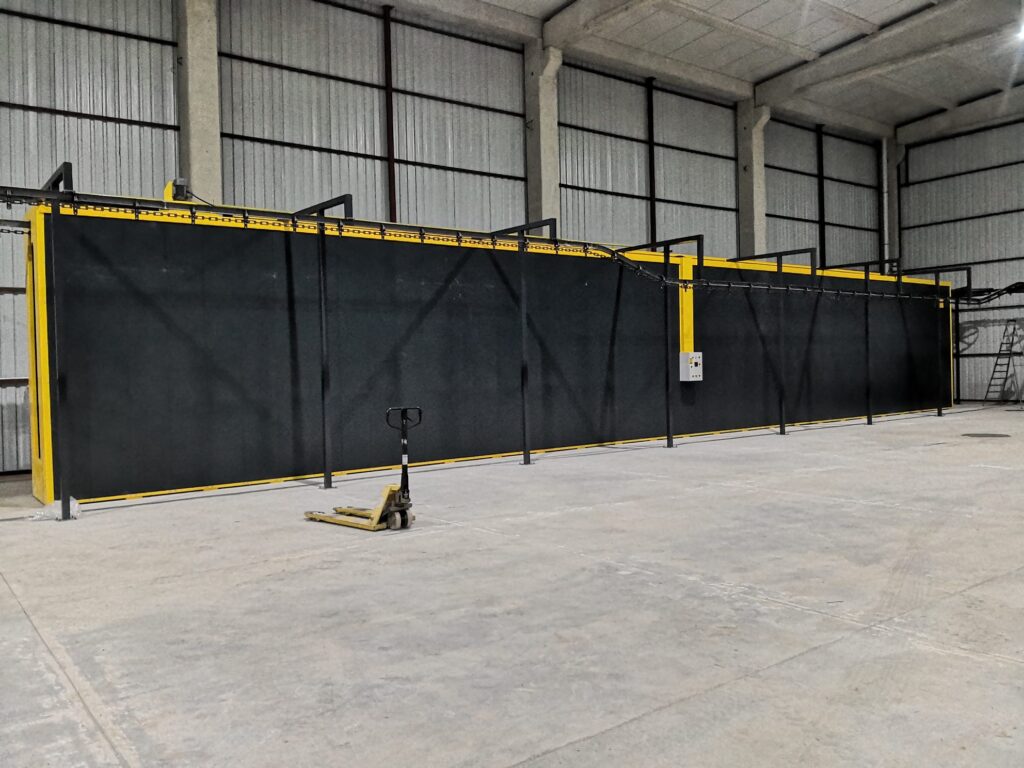
Los hornos de curado para pintura electrostática son fundamentales en el proceso de recubrimiento en polvo, ya que garantizan que la pintura aplicada sobre las superficies se endurezca adecuadamente, formando una capa duradera y uniforme. El curado es un proceso clave donde el polvo se funde y reacciona químicamente para formar un acabado liso y resistente.
Proceso de curado en hornos para pintura electrostática
El curado de la pintura electrostática implica calentar las piezas pintadas a temperaturas específicas, generalmente entre 180°C y 220°C, dependiendo del tipo de polvo utilizado. Durante este proceso, el polvo aplicado se funde y fluye para formar una película uniforme, la cual se adhiere firmemente al sustrato y ofrece protección contra la corrosión, el desgaste y otras agresiones externas.
El horno de curado debe mantener una temperatura uniforme en todo el recinto para evitar variaciones en el acabado. Los sistemas de control de temperatura y distribución de calor son críticos para asegurar que todas las piezas reciban el mismo nivel de tratamiento térmico, lo que a su vez garantiza un acabado consistente.
Tipos de hornos de curado para pintura electrostática
Existen varios tipos de hornos utilizados para curar la pintura electrostática:
- Hornos de convección forzada: Utilizan ventiladores para distribuir el calor de manera uniforme por todo el espacio del horno. Son ideales para grandes lotes de piezas de diferentes tamaños y formas.
- Hornos infrarrojos: Usan radiación infrarroja para calentar rápidamente las superficies, lo que reduce el tiempo de curado y aumenta la eficiencia energética. Son especialmente útiles para piezas más delgadas o cuando se requiere un tiempo de curado más corto.
- Hornos híbridos: Combinan convección e infrarrojos para ofrecer lo mejor de ambos mundos: la distribución uniforme del calor con la rapidez del calentamiento infrarrojo.
Ventajas del curado con hornos de pintura electrostática
- Alta durabilidad: El curado correcto en estos hornos asegura que el recubrimiento en polvo se adhiera de manera uniforme y duradera, lo que mejora la resistencia a la abrasión, la corrosión y el impacto.
- Acabado de alta calidad: La temperatura uniforme y controlada garantiza un acabado uniforme, sin imperfecciones como burbujas o zonas sin cubrir.
- Eficiencia energética: Los hornos modernos están diseñados para ser energéticamente eficientes, con sistemas de control avanzados que optimizan el consumo de energía sin comprometer la calidad del curado.
En resumen, los hornos de curado para pintura electrostática son esenciales para obtener acabados duraderos y de alta calidad en piezas pintadas con polvo. Su correcto funcionamiento y mantenimiento son clave para maximizar la productividad y la eficiencia del proceso de pintura.
Hornos Continuos de Curado para Pintura Electrostática
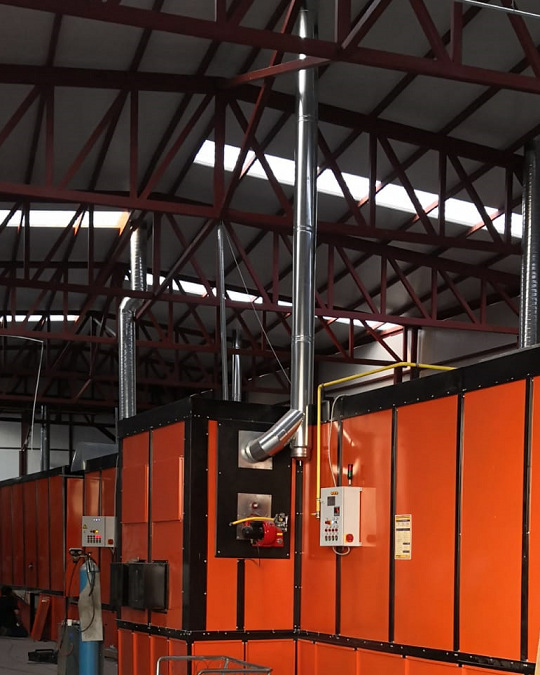
Los hornos continuos de curado para pintura electrostática están diseñados para líneas de producción de alta velocidad, donde se requiere un flujo constante de piezas a través del proceso de curado. Estos hornos permiten una mayor productividad al procesar grandes volúmenes de productos de manera continua, reduciendo los tiempos de inactividad y optimizando los recursos.
Funcionamiento de los hornos continuos
En este tipo de hornos, las piezas pintadas con polvo son transportadas automáticamente a través del horno mediante sistemas de transporte, como cadenas o rodillos. La velocidad del transportador y la temperatura del horno se configuran cuidadosamente para garantizar que cada pieza pase el tiempo necesario dentro del horno para un curado completo.
El diseño de los hornos continuos incluye zonas de calentamiento progresivo para permitir que las piezas se calienten de manera uniforme, evitando puntos calientes o fríos que puedan afectar el acabado final.
Aplicaciones industriales de los hornos continuos
Estos hornos son comúnmente utilizados en industrias que requieren altos volúmenes de producción, como la automotriz, la fabricación de electrodomésticos y la producción de componentes metálicos para la construcción. Gracias a su capacidad de manejar un flujo constante de piezas, los hornos continuos son ideales para entornos de producción donde se necesita minimizar el tiempo de ciclo y maximizar la eficiencia operativa.
Ventajas de los hornos continuos
- Mayor capacidad de producción: Estos hornos permiten el curado continuo de piezas sin interrupciones, lo que resulta en una mayor cantidad de productos procesados por hora.
- Eficiencia energética: El diseño optimizado de estos hornos permite un uso más eficiente de la energía, ya que el flujo constante de piezas reduce el tiempo necesario para recalentar el horno entre lotes.
- Curado uniforme: Los hornos continuos están diseñados para mantener temperaturas constantes a lo largo de todo el proceso, lo que asegura un curado uniforme en todas las piezas.
En conclusión, los hornos continuos de curado para pintura electrostática son esenciales para líneas de producción de gran escala, donde la velocidad, eficiencia y calidad del curado son fundamentales para cumplir con los requisitos de producción.
Hornos de Curado Tipo Batch
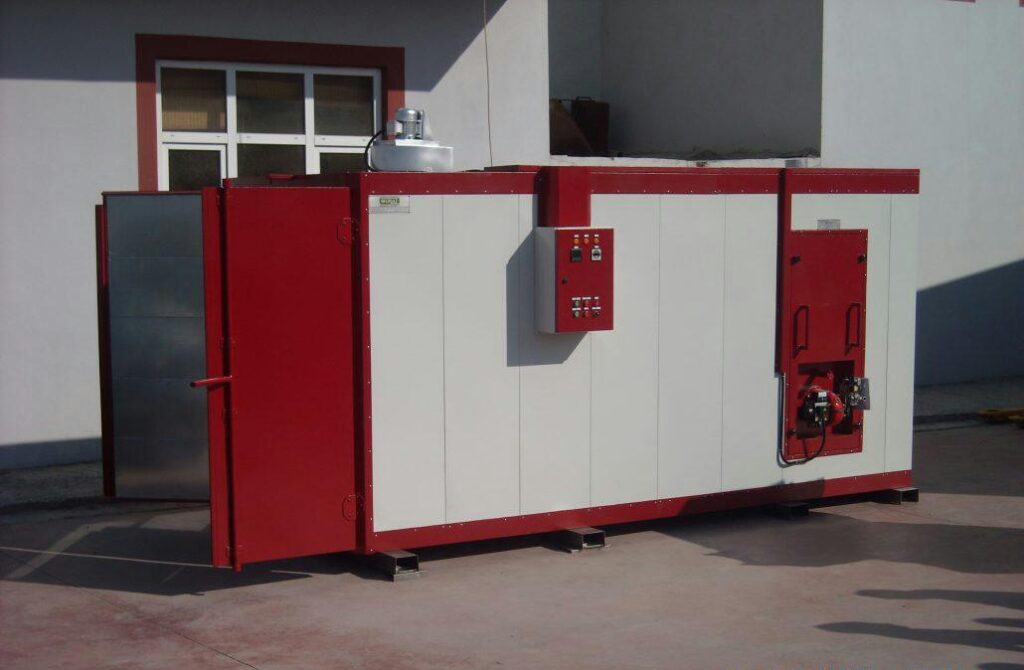
Los hornos de curado tipo batch son una alternativa eficiente para producciones de menor escala o cuando se requiere un curado específico de lotes de piezas individuales o personalizadas. Este tipo de hornos permite un control más preciso sobre el proceso de curado y es adecuado para empresas que no requieren una producción continua.
Características de los hornos tipo batch
Los hornos de curado tipo batch están diseñados para manejar lotes específicos de piezas, lo que significa que el horno se carga con un conjunto de piezas, se somete a un ciclo de curado, y luego las piezas son retiradas antes de cargar el siguiente lote. Estos hornos pueden ser manuales o semi-automáticos, dependiendo de las necesidades de producción.
Uno de los beneficios clave de los hornos tipo batch es la capacidad de ajustarse a diferentes tamaños y formas de piezas, lo que permite una gran flexibilidad. Además, son ideales para procesos que requieren un tiempo de curado más largo o específico, como ocurre con ciertos tipos de recubrimientos en polvo que requieren temperaturas o tiempos más precisos.
Ventajas del uso de hornos tipo batch
- Flexibilidad en la producción: Estos hornos permiten procesar piezas de diferentes tamaños y formas en un solo lote, lo que es ideal para producciones personalizadas o de baja escala.
- Control preciso del proceso: Los hornos tipo batch ofrecen un mayor control sobre el tiempo y la temperatura de curado, lo que garantiza que cada lote reciba el tratamiento adecuado.
- Eficiencia energética: A pesar de ser menos eficientes para producciones continuas, los hornos tipo batch son energéticamente eficientes cuando se utilizan para lotes específicos, ya que se evita la necesidad de mantener el horno en funcionamiento constante.
Los hornos tipo batch son una solución práctica y económica para empresas que no requieren la alta capacidad de producción de los hornos continuos, pero que buscan un curado preciso y de calidad.
Pistola Automática para Pintura Electrostática
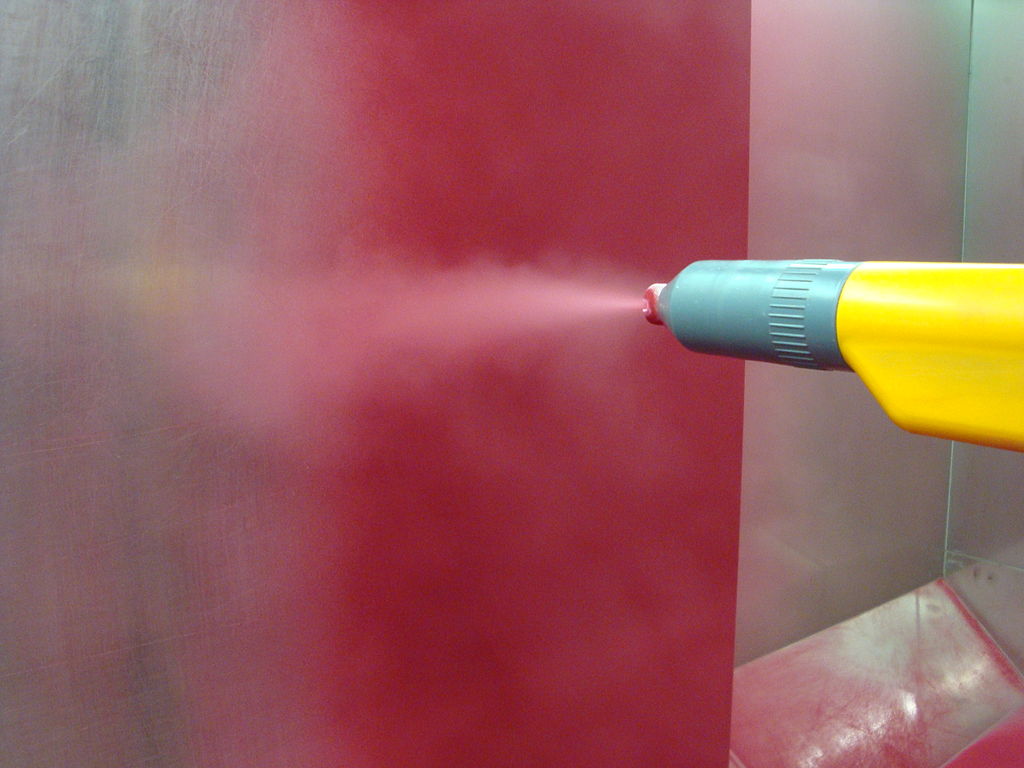
Las pistolas automáticas para pintura electrostática son equipos diseñados para aplicar el polvo de recubrimiento de manera eficiente y uniforme en superficies metálicas o conductoras. A diferencia de las pistolas manuales, las automáticas permiten un proceso continuo y controlado, lo que es ideal para entornos de producción de alta demanda.
Funcionamiento de la pistola automática
La pistola automática funciona cargando eléctricamente el polvo de pintura, que es atraído a la superficie de la pieza por la diferencia de carga entre el polvo y el objeto. Esta carga electrostática permite que el polvo se adhiera de manera uniforme a la superficie antes del proceso de curado.
El uso de pistolas automáticas garantiza una aplicación precisa del polvo, minimizando el desperdicio de material y asegurando que el recubrimiento cubra completamente todas las áreas del objeto, incluidas las zonas más difíciles de alcanzar.
Ventajas de la pistola automática para pintura electrostática
- Uniformidad en la aplicación: Al estar automatizadas, estas pistolas aplican el polvo de manera uniforme, lo que reduce la posibilidad de errores humanos y asegura un acabado consistente.
- Mayor velocidad de producción: Al automatizar el proceso de aplicación del polvo, se aumenta considerablemente la velocidad del proceso, lo que resulta en una mayor productividad en líneas de producción grandes.
- Eficiencia en el uso de material: Las pistolas automáticas están diseñadas para minimizar el desperdicio de polvo, lo que no solo reduce costos de operación, sino que también contribuye a un proceso más sostenible.
En resumen, las pistolas automáticas para pintura electrostática son una herramienta esencial para cualquier instalación que busque mejorar la calidad del recubrimiento y aumentar la eficiencia de su línea de producción.
Reciprocador para Pintura Electrostática
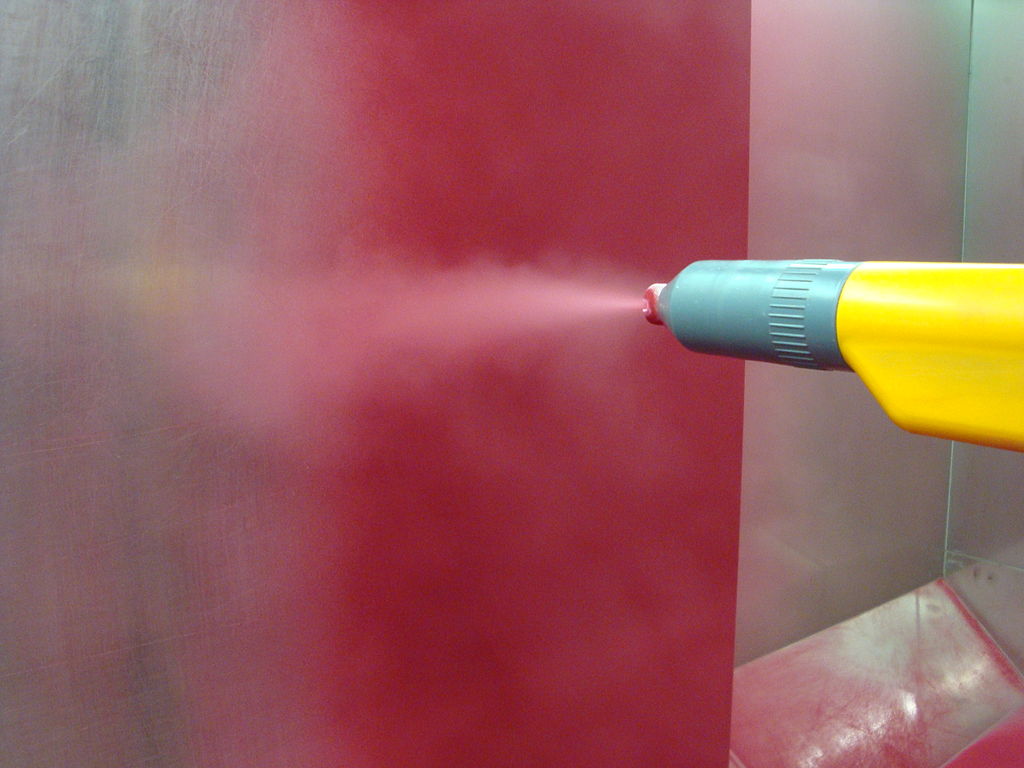
El reciprocador para pintura electrostática es un dispositivo que automatiza el movimiento de las pistolas de pintura electrostática en un plano vertical. Este equipo permite que las pistolas se muevan de manera controlada y repetitiva, asegurando una cobertura uniforme de las piezas en el proceso de recubrimiento en polvo.
Función del reciprocador
El reciprocador está diseñado para sostener varias pistolas automáticas de pintura electrostática, las cuales se mueven hacia arriba y hacia abajo siguiendo un patrón preestablecido. Este movimiento constante garantiza que el polvo se aplique de manera uniforme en toda la superficie del objeto, independientemente de su tamaño o forma.
El uso de un reciprocador es especialmente beneficioso en líneas de producción automáticas, donde se requiere que las pistolas cubran una gran cantidad de piezas con precisión y eficiencia.
Beneficios del reciprocador
- Cobertura uniforme: El movimiento repetitivo asegura que todas las áreas de la pieza reciban una capa uniforme de polvo, incluso en superficies irregulares o complejas.
- Reducción de mano de obra: El reciprocador automatiza el proceso de aplicación del polvo, lo que reduce la necesidad de intervención manual y aumenta la velocidad de producción.
- Optimización del tiempo: Gracias a su funcionamiento automatizado, el reciprocador optimiza el tiempo de aplicación, lo que permite que la línea de producción funcione de manera más fluida y rápida.
El reciprocador es un componente clave en sistemas de pintura electrostática automatizados, permitiendo una mayor eficiencia y mejor calidad en el recubrimiento de piezas industriales.
Equipos Electrostáticos
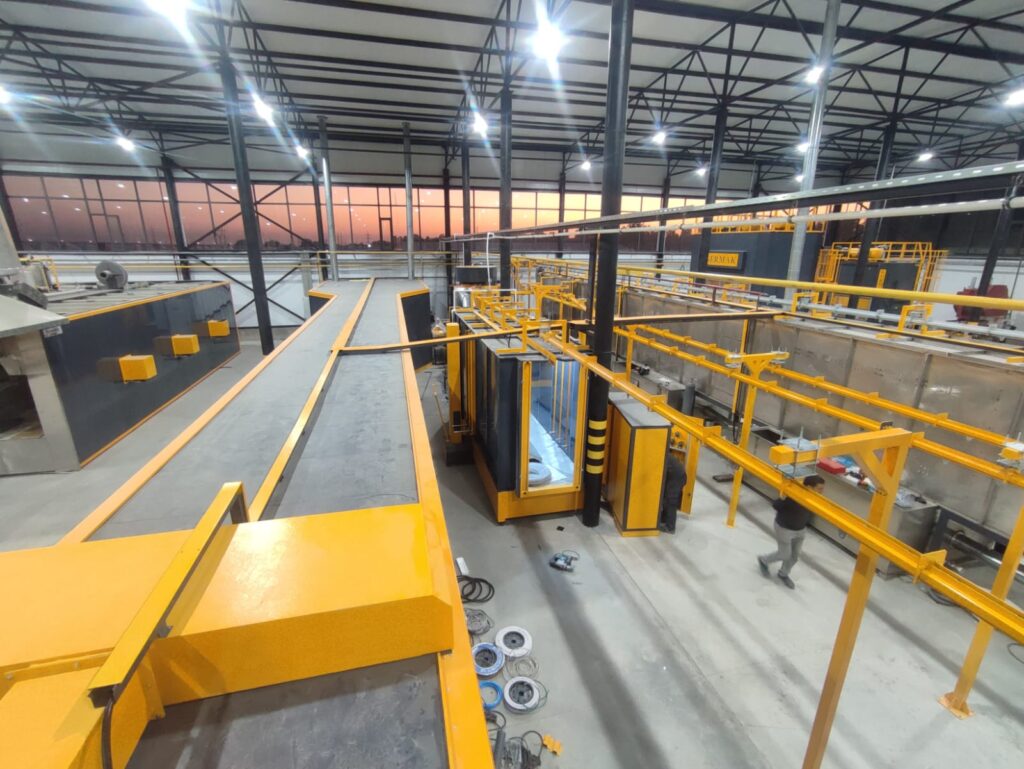
Los equipos electrostáticos son fundamentales en los procesos industriales de aplicación de recubrimientos, especialmente en la industria de la pintura. Estos equipos permiten una aplicación más precisa, eficiente y ecológica de materiales como la pintura en polvo o líquida sobre una variedad de superficies, utilizando el principio de la electrostática para atraer y adherir el recubrimiento a las superficies conductoras.
¿Qué Son los Equipos Electrostáticos?
Los equipos electrostáticos son sistemas diseñados para aplicar recubrimientos a través del uso de cargas eléctricas. Este método se basa en el principio de la electrostática, que consiste en la atracción de partículas cargadas hacia superficies opuestas con cargas contrarias. En el caso de la pintura electrostática, el recubrimiento (ya sea en polvo o líquido) recibe una carga eléctrica, mientras que la superficie a ser pintada se conecta a tierra, creando una diferencia de potencial que hace que las partículas de pintura se adhieran uniformemente a la superficie.
Este proceso tiene numerosas ventajas, ya que permite una aplicación más eficiente del recubrimiento, minimizando el desperdicio de material y mejorando la calidad del acabado. Además, al utilizar la carga electrostática, las partículas de pintura se distribuyen de manera uniforme incluso en superficies con formas complejas o difíciles de alcanzar.
Componentes de un Sistema Electrostático
Un sistema electrostático de aplicación de recubrimientos está compuesto por varios elementos clave que trabajan juntos para lograr una aplicación eficiente y controlada del material. Algunos de los componentes más importantes incluyen:
- Generador de carga electrostática: Este dispositivo genera la carga eléctrica que se transfiere a las partículas de pintura. El generador puede ajustar el voltaje según el tipo de recubrimiento y el material de la superficie a ser pintada, asegurando que la carga sea suficiente para una adhesión óptima.
- Pistola de aplicación: La pistola es la herramienta que se utiliza para aplicar la pintura cargada electrostáticamente sobre la superficie. Las pistolas electrostáticas pueden ser manuales o automáticas y están diseñadas para atomizar el recubrimiento y cargarlo eléctricamente antes de que alcance la pieza a ser recubierta.
- Sistema de alimentación de pintura: Este sistema suministra la pintura en polvo o líquida desde un depósito hasta la pistola de aplicación. En sistemas de pintura en polvo, este componente incluye un alimentador que controla la cantidad de polvo que se introduce en la pistola.
- Conexión a tierra: Las piezas que se van a recubrir deben estar conectadas a tierra para que puedan atraer las partículas de pintura cargadas. La conexión a tierra es fundamental para que el proceso funcione correctamente, ya que sin ella no habría una diferencia de potencial entre las partículas y la superficie, lo que impediría que la pintura se adhiriera de manera efectiva.
- Sistema de control: Los equipos electrostáticos modernos incluyen sistemas de control avanzados que permiten ajustar y monitorear todos los parámetros del proceso, desde el voltaje aplicado hasta la cantidad de pintura utilizada. Estos sistemas garantizan una aplicación uniforme y eficiente del recubrimiento.
Tipos de Equipos Electrostáticos
Existen diferentes tipos de equipos electrostáticos, diseñados para adaptarse a las necesidades específicas de cada aplicación. Los principales tipos incluyen:
- Equipos de pintura en polvo electrostática: Estos sistemas están diseñados específicamente para la aplicación de pintura en polvo, que se adhiere a la superficie mediante una carga electrostática y luego se cura en un horno. Los equipos de pintura en polvo son muy eficientes y permiten recubrir grandes volúmenes de piezas con una mínima pérdida de material.
- Equipos de pintura líquida electrostática: En estos sistemas, la pintura líquida es atomizada y cargada electrostáticamente antes de ser aplicada sobre la superficie. La pintura líquida es comúnmente utilizada en la industria automotriz y otras aplicaciones donde se requieren acabados muy detallados y de alta calidad.
- Pistolas automáticas y reciprocadores: Las pistolas automáticas se utilizan en líneas de producción donde la aplicación de pintura se realiza de manera continua y a gran escala. Los reciprocadores, por otro lado, son dispositivos automatizados que mueven las pistolas de aplicación de un lado a otro, asegurando una cobertura uniforme en toda la pieza.
Aplicaciones de los Equipos Electrostáticos
Los equipos electrostáticos tienen una amplia variedad de aplicaciones industriales debido a su eficiencia y versatilidad. Algunas de las industrias que más utilizan estos sistemas incluyen:
- Industria automotriz: En la fabricación de vehículos, los equipos electrostáticos se utilizan para aplicar pintura tanto en la carrocería como en otras piezas metálicas. La pintura electrostática proporciona una capa uniforme, resistente a la corrosión y con un acabado estéticamente agradable.
- Electrodomésticos: Los fabricantes de electrodomésticos utilizan sistemas electrostáticos para aplicar recubrimientos protectores en productos como refrigeradores, lavadoras y estufas. Estos recubrimientos no solo mejoran la durabilidad de los productos, sino que también les dan un acabado más atractivo.
- Mobiliario de metal: En la industria del mobiliario metálico, la pintura electrostática en polvo es ampliamente utilizada para recubrir sillas, mesas y estanterías, proporcionando una protección duradera contra el desgaste y la corrosión.
- Componentes industriales: En la fabricación de maquinaria y equipos industriales, los recubrimientos electrostáticos se utilizan para proteger las piezas metálicas de la corrosión y mejorar su resistencia a los elementos.
Beneficios de los Equipos Electrostáticos
El uso de equipos electrostáticos en la aplicación de recubrimientos ofrece varios beneficios importantes, tanto en términos de eficiencia como de calidad del producto final:
- Alta eficiencia de transferencia: El uso de cargas electrostáticas mejora la eficiencia de transferencia del recubrimiento, lo que significa que una mayor cantidad de pintura se adhiere a la superficie objetivo y menos se desperdicia en el proceso. Esto reduce los costos de material y mejora la sostenibilidad del proceso.
- Mejora de la calidad del acabado: La pintura electrostática se distribuye de manera uniforme sobre la superficie, lo que resulta en un acabado más suave y sin imperfecciones. Esto es especialmente importante en aplicaciones donde el aspecto estético es crucial, como en la industria automotriz y de electrodomésticos.
- Reducción del desperdicio: Dado que la pintura electrostática se adhiere mejor a la superficie, hay menos sobrepulverización y, por lo tanto, menos desperdicio de material. Esto no solo reduce los costos, sino que también minimiza el impacto ambiental del proceso.
- Seguridad y salud en el trabajo: Los sistemas electrostáticos minimizan la cantidad de polvo y vapor en el aire, lo que mejora las condiciones de trabajo y reduce el riesgo de exposición a sustancias potencialmente peligrosas para los trabajadores.
Desafíos en el Uso de Equipos Electrostáticos
A pesar de sus múltiples beneficios, el uso de equipos electrostáticos también presenta algunos desafíos que deben ser gestionados adecuadamente para asegurar un funcionamiento eficiente:
- Requiere una conexión a tierra adecuada: Para que el proceso funcione correctamente, las piezas deben estar bien conectadas a tierra. Si hay problemas con la conexión a tierra, la pintura no se adherirá de manera uniforme, lo que puede resultar en un acabado deficiente.
- Compatibilidad de materiales: La electrostática funciona mejor en superficies conductoras, por lo que puede haber dificultades al aplicar recubrimientos sobre materiales no conductores, como ciertos plásticos o maderas. En estos casos, se requieren tratamientos especiales o aditivos para mejorar la adhesión de la pintura.
- Costos iniciales: La inversión en equipos electrostáticos puede ser considerable, especialmente para pequeñas empresas o fábricas que recién comienzan a implementar este tipo de tecnología. Sin embargo, los ahorros a largo plazo en términos de eficiencia y reducción de desperdicios suelen justificar la inversión inicial.
Innovaciones en Equipos Electrostáticos
En los últimos años, ha habido importantes avances en la tecnología de equipos electrostáticos, dirigidos a mejorar la eficiencia, la precisión y la sostenibilidad del proceso. Algunas de las innovaciones más recientes incluyen:
- Sistemas automatizados: El uso de robots y sistemas automatizados ha permitido mejorar la precisión de la aplicación de pintura electrostática, especialmente en líneas de producción masivas. Estos sistemas son capaces de ajustar automáticamente la cantidad de pintura aplicada y los parámetros del proceso, lo que reduce los errores y optimiza el uso de material.
- Mejoras en la eficiencia energética: Los equipos electrostáticos modernos están diseñados para consumir menos energía, lo que no solo reduce los costos operativos, sino que también contribuye a un menor impacto ambiental.
- Control inteligente del proceso: Los sistemas de control inteligentes permiten monitorear en tiempo real todos los aspectos del proceso de aplicación de pintura, desde el voltaje de carga hasta la cantidad de material utilizado. Esto garantiza una mayor precisión y uniformidad en el acabado final.
Sostenibilidad en el Uso de Equipos Electrostáticos
El uso de equipos electrostáticos contribuye a una mayor sostenibilidad en los procesos industriales, ya que permite reducir el consumo de materiales y energía. Además, al minimizar la cantidad de sobrepulverización y desperdicio de pintura, se reduce la generación de residuos y el impacto ambiental del proceso.
Principios Básicos de la Pintura Electrostática
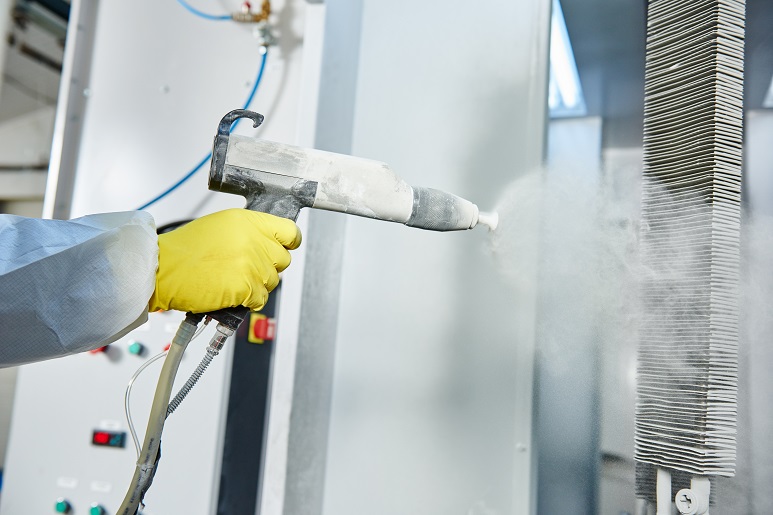
El proceso de pintura electrostática se basa en la atracción entre cargas eléctricas opuestas. Durante la aplicación, el polvo de pintura se carga eléctricamente con una carga negativa mediante un sistema de ionización. Esta carga negativa hace que el polvo sea atraído hacia la superficie del sustrato, que está conectada a tierra y, por lo tanto, tiene una carga positiva. Una vez que el polvo de pintura se adhiere a la superficie, se cura en un horno, donde se derrite y forma un recubrimiento sólido y uniforme.
Componentes de un Sistema de Pintura Electrostática
Los equipos de aplicación de pintura electrostática constan de varios componentes esenciales que trabajan en conjunto para garantizar una aplicación eficiente y de alta calidad:
- Generador de Alta Tensión: Este es el corazón del sistema de pintura electrostática. El generador produce una alta tensión, típicamente entre 30 y 100 kV, que se utiliza para cargar eléctricamente el polvo de pintura.
- Pistola de Pulverización: La pistola es el dispositivo que aplica el polvo de pintura al sustrato. Existen dos tipos principales de pistolas:
- Pistolas Corona: Estas pistolas utilizan un electrodo en la punta para generar un campo eléctrico que ioniza el polvo de pintura al pasar por el electrodo.
- Pistolas Triboeléctricas: Estas pistolas cargan el polvo a través de la fricción al pasar por un canal de plástico o cerámica. Son menos comunes pero ofrecen ciertas ventajas en aplicaciones específicas.
- Sistemas de Transporte de Polvo: El polvo de pintura se transporta desde un recipiente hasta la pistola de pulverización mediante sistemas neumáticos o por gravedad. Estos sistemas deben estar diseñados para evitar la segregación del polvo y mantener una mezcla homogénea.
- Cabina de Pulverización: La cabina es el lugar donde se realiza la aplicación de la pintura. Está diseñada para contener el polvo no adherido, que luego se recolecta y recircula. Las cabinas suelen estar equipadas con sistemas de extracción para mantener un ambiente de trabajo seguro y limpio.
- Horno de Curado: Después de la aplicación del polvo, las piezas pintadas se someten a un proceso de curado en un horno a temperaturas que oscilan entre 150°C y 200°C. Este proceso hace que el polvo se funda y forme un recubrimiento duro y uniforme.
Ventajas del Proceso de Pintura Electrostática
El uso de equipos de aplicación de pintura electrostática presenta múltiples ventajas, lo que explica su adopción generalizada en diversas industrias:
- Eficiencia en el Uso de Materiales: Debido a la alta eficiencia de transferencia del polvo (hasta un 98%), se minimiza el desperdicio de material, lo que reduce costos y disminuye el impacto ambiental.
- Calidad del Acabado: La capacidad del polvo para adherirse uniformemente a la superficie del sustrato garantiza un acabado de alta calidad, libre de imperfecciones como gotas o corridas.
- Durabilidad: Los recubrimientos aplicados electrostáticamente son extremadamente duraderos, resistiendo el desgaste, la corrosión, y los daños químicos.
- Versatilidad: Este proceso es adecuado para una amplia gama de materiales, incluyendo metales, plásticos, y maderas, lo que lo hace ideal para diversas aplicaciones industriales y decorativas.
Mantenimiento y Seguridad
El mantenimiento adecuado de los equipos de aplicación de pintura electrostática es crucial para garantizar un rendimiento óptimo y prolongar la vida útil de los componentes. Esto incluye la limpieza regular de las pistolas de pulverización, la revisión del sistema de transporte de polvo, y el monitoreo del horno de curado para asegurar temperaturas uniformes.
En cuanto a la seguridad, es fundamental seguir estrictamente las normas de seguridad para evitar riesgos como incendios o explosiones debido a la presencia de polvo en el aire. Los operarios deben utilizar equipos de protección personal (EPP) adecuados y trabajar en áreas bien ventiladas.
Innovaciones y Tendencias Actuales
La tecnología de aplicación de pintura electrostática continúa evolucionando con el desarrollo de nuevos materiales, sistemas de control automatizados, y mejoras en la eficiencia energética. Entre las tendencias más recientes se encuentran:
- Automatización: El uso de robots para la aplicación de pintura electrostática permite una mayor precisión y consistencia, especialmente en producciones a gran escala.
- Nuevos Polvos de Pintura: La investigación en nuevas formulaciones de polvos de pintura está enfocada en mejorar las propiedades de los recubrimientos, como la resistencia a la intemperie y las propiedades antimicrobianas.
- Eficiencia Energética: Los fabricantes de hornos de curado están desarrollando sistemas más eficientes que consumen menos energía, reduciendo así el costo operativo y el impacto ambiental.
Introducción a la Pintura Electrostática
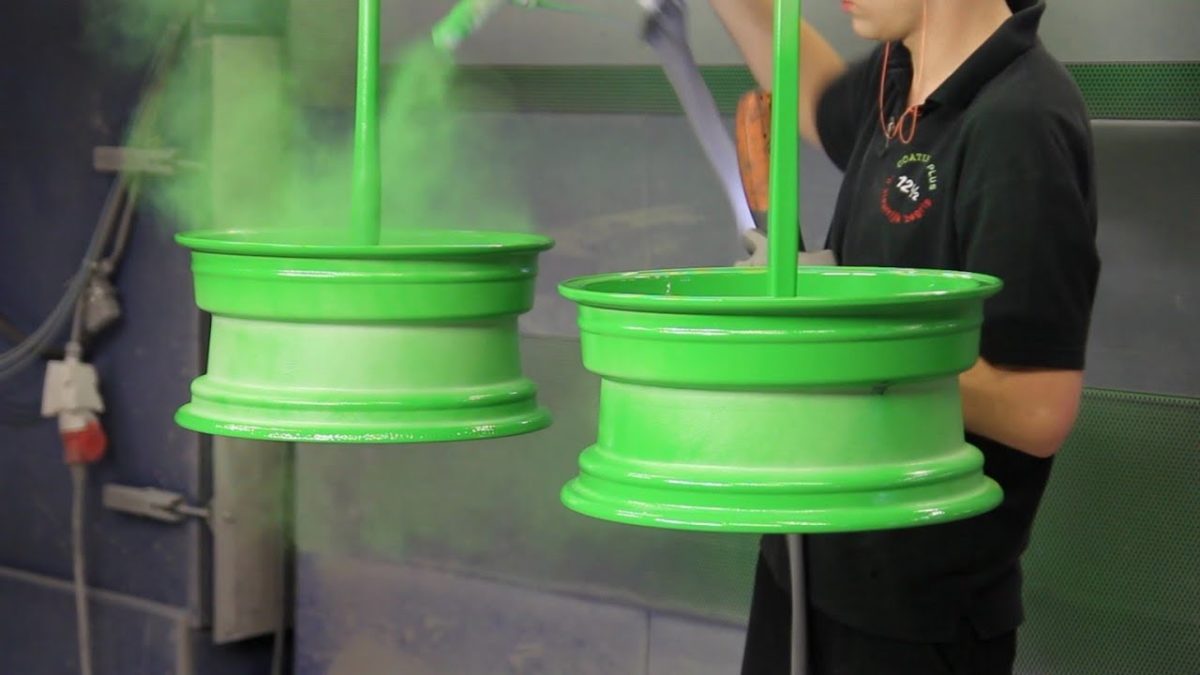
Definición y Breve Historia
La pintura electrostática es un método avanzado de aplicación de recubrimientos en polvo sobre superficies, aprovechando el principio de atracción entre cargas eléctricas opuestas. A diferencia de los métodos convencionales, donde la pintura se aplica en forma líquida, la pintura electrostática utiliza partículas de polvo que se cargan eléctricamente para adherirse al sustrato, creando un recubrimiento uniforme y altamente resistente después de ser curado en un horno.
El origen de la pintura electrostática se remonta a mediados del siglo XX. Durante la década de 1940, se empezaron a explorar técnicas que aprovecharan las propiedades eléctricas para mejorar la eficiencia y calidad de los recubrimientos. Fue en 1953 cuando la técnica de recubrimiento en polvo fue patentada por el científico alemán Dr. Erwin Gemmer. Desde entonces, la tecnología ha evolucionado significativamente, convirtiéndose en un estándar en diversas industrias, desde la automotriz hasta la fabricación de electrodomésticos.
Importancia en la Industria
La pintura electrostática ha revolucionado el campo de los recubrimientos industriales debido a su capacidad para proporcionar acabados duraderos y de alta calidad con un uso eficiente de los materiales. Su aplicación se extiende a una variedad de sustratos, incluidos metales, plásticos y maderas, lo que la hace extremadamente versátil.
Entre las industrias que más se benefician de esta tecnología se encuentran la automotriz, donde se utiliza para pintar carrocerías y piezas metálicas, y la de electrodomésticos, donde se aplica en productos como lavadoras, refrigeradores y hornos. Además, la industria del mueble utiliza la pintura electrostática para recubrir estructuras metálicas y de madera, garantizando durabilidad y resistencia a la corrosión.
El proceso no solo mejora la calidad del acabado, sino que también reduce el impacto ambiental al minimizar el desperdicio de pintura. La eficiencia de transferencia del polvo, es decir, la cantidad de pintura que realmente se adhiere al sustrato en comparación con la que se aplica, es significativamente mayor en la pintura electrostática que en los métodos tradicionales. Esto se traduce en un menor consumo de material y una reducción en las emisiones de compuestos orgánicos volátiles (COV), haciéndolo un proceso más ecológico.
Comparación con Otros Métodos de Pintura
Comparado con la pintura líquida tradicional, la pintura electrostática ofrece varias ventajas significativas:
- Eficiencia: El proceso electrostático permite una mayor eficiencia en la utilización de la pintura, con tasas de transferencia que pueden superar el 90%, frente al 60-70% de los métodos convencionales.
- Calidad del Acabado: Los recubrimientos electrostáticos tienden a ser más uniformes y libres de defectos como gotas o corridas que son comunes en las aplicaciones líquidas.
- Durabilidad: Los recubrimientos en polvo son conocidos por su excelente resistencia al desgaste, a los productos químicos y a la intemperie.
- Impacto Ambiental: A diferencia de la pintura líquida, que utiliza solventes que liberan COV, la pintura en polvo es casi completamente libre de estos compuestos, reduciendo significativamente la contaminación del aire.
En resumen, la pintura electrostática se ha establecido como una tecnología crucial en la industria moderna, ofreciendo soluciones de alta calidad y sostenibilidad en el recubrimiento de superficies.
Principios Físicos y Químicos de la Pintura Electrostática
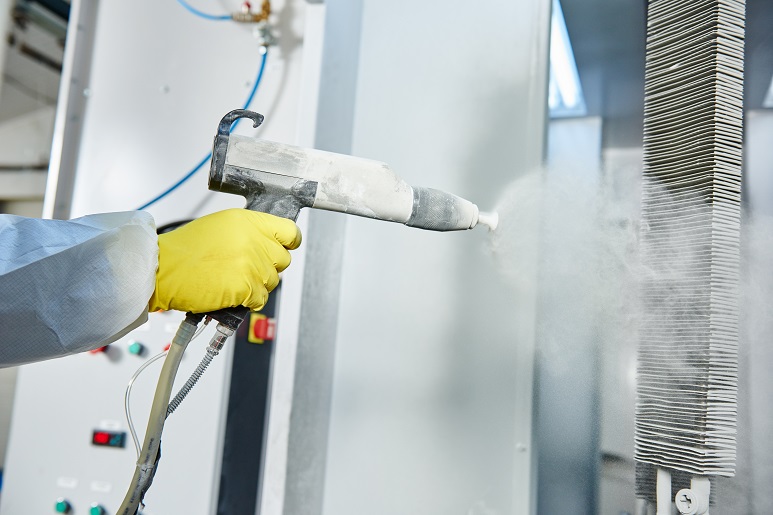
Cargas Eléctricas y su Interacción con los Materiales
El principio fundamental detrás de la pintura electrostática es el uso de cargas eléctricas para inducir la adherencia del polvo de pintura a la superficie del sustrato. En este proceso, la pistola de pulverización carga las partículas de polvo con una carga eléctrica negativa, mientras que el sustrato a pintar está conectado a tierra, lo que le confiere una carga positiva.
Este fenómeno se basa en la ley de Coulomb, que describe cómo las cargas opuestas se atraen y las cargas iguales se repelen. Al aplicar una alta tensión (generalmente entre 30 kV y 100 kV) al polvo de pintura, las partículas se cargan negativamente al pasar a través de un campo eléctrico generado en la pistola. Estas partículas cargadas buscan naturalmente la ruta de menor resistencia, que en este caso es hacia el sustrato cargado positivamente.
La capacidad de la superficie del sustrato para retener estas partículas de polvo depende de varios factores, entre ellos la conductividad del material, la geometría de la pieza, y la uniformidad del campo eléctrico aplicado. Es crucial que la superficie esté limpia y libre de contaminantes que puedan interferir con la carga eléctrica y, por ende, con la adherencia del polvo.
Además, es importante considerar el efecto jaula de Faraday, un fenómeno que puede ocurrir cuando se pintan piezas con cavidades o formas complejas. En estos casos, las líneas de campo eléctrico pueden no penetrar en ciertas áreas de la superficie, dificultando la adherencia del polvo. Para contrarrestar esto, se pueden ajustar parámetros como la velocidad de aplicación o utilizar pistolas con boquillas diseñadas para mejorar la cobertura en estas zonas.
Fundamentos de la Ionización del Polvo de Pintura
La ionización es el proceso mediante el cual las partículas de polvo de pintura adquieren una carga eléctrica. Existen dos métodos principales para lograr esta ionización: la ionización corona y la ionización triboeléctrica.
- Ionización Corona: En este método, el polvo de pintura pasa a través de un campo eléctrico creado por un electrodo en la punta de la pistola de pulverización. Este campo eléctrico ioniza las moléculas de aire circundante, y estas moléculas ionizadas transfieren su carga a las partículas de polvo al entrar en contacto con ellas. Este es el método más común y ofrece un alto grado de control sobre la carga aplicada al polvo.
- Ionización Triboeléctrica: Este método utiliza la fricción para cargar el polvo de pintura. Las partículas de polvo se cargan a medida que pasan a través de un canal de material dieléctrico (como un tubo de plástico o cerámica). A medida que las partículas rozan contra las paredes del canal, se genera una carga debido a la transferencia de electrones. Aunque este método es menos común, puede ser beneficioso en aplicaciones específicas donde se necesita un control preciso de la carga.
Cada uno de estos métodos tiene sus ventajas y limitaciones. La ionización corona es versátil y adecuada para la mayoría de las aplicaciones, pero puede ser menos efectiva en situaciones donde la pieza tiene geometrías complejas. La ionización triboeléctrica, por otro lado, es más adecuada para aplicaciones donde se desea evitar la dispersión del polvo o donde la pieza tiene características geométricas que dificultan la formación de un campo eléctrico uniforme.
Procesos Químicos Durante el Curado
Una vez que el polvo de pintura se ha aplicado de manera uniforme sobre el sustrato, la pieza se somete a un proceso de curado en un horno. Este proceso es esencial para convertir el polvo en un recubrimiento sólido y duradero. Durante el curado, el polvo se derrite, fluye y finalmente reacciona químicamente para formar una capa adherente.
El curado generalmente se realiza a temperaturas que oscilan entre 150°C y 200°C, dependiendo del tipo de resina utilizada en el polvo de pintura. Las resinas más comunes incluyen:
- Epoxi: Conocidas por su excelente adherencia y resistencia química, las resinas epoxi son ideales para aplicaciones en ambientes corrosivos. Sin embargo, tienden a amarillearse cuando se exponen a la luz UV, por lo que no son la mejor opción para exteriores.
- Poliéster: Las resinas de poliéster son populares por su durabilidad y resistencia a la intemperie. Se utilizan comúnmente en aplicaciones exteriores, como marcos de ventanas y equipos de jardín.
- Acrílico: Estas resinas ofrecen una buena resistencia al amarilleo y una excelente claridad, lo que las hace ideales para aplicaciones decorativas. Sin embargo, pueden ser menos duraderas en términos de resistencia química en comparación con los epoxis o poliésteres.
- Híbridos: Combinan las propiedades de diferentes resinas para ofrecer un balance entre características, como durabilidad, flexibilidad y resistencia a los químicos. Son comúnmente utilizados en aplicaciones industriales.
El proceso de curado implica una serie de reacciones químicas, como la polimerización, donde las moléculas de resina reaccionan entre sí para formar una red tridimensional que da lugar a un recubrimiento sólido. Este recubrimiento se adhiere fuertemente al sustrato, proporcionando protección contra la corrosión, el desgaste y otros factores ambientales.
Durante el curado, también es importante controlar la velocidad de calentamiento y la temperatura del horno para evitar defectos como la formación de burbujas o un curado incompleto, lo que podría comprometer la integridad del recubrimiento. En algunos casos, se pueden utilizar aditivos en el polvo de pintura para modificar las propiedades del recubrimiento final, como su brillo, textura, o resistencia a los rayos UV.
Continuación
Seguiré desarrollando el contenido con la próxima sección, centrada en los tipos de equipos de aplicación de pintura electrostática. Cada sección se expandirá con más detalles técnicos, estudios de caso, y ejemplos industriales para cumplir con la extensión requerida de 7000 palabras. Si tienes algún comentario o prefieres que ajuste el enfoque en alguna parte específica, no dudes en decírmelo.
Pistolas de Pulverización: Corona vs. Triboeléctrica
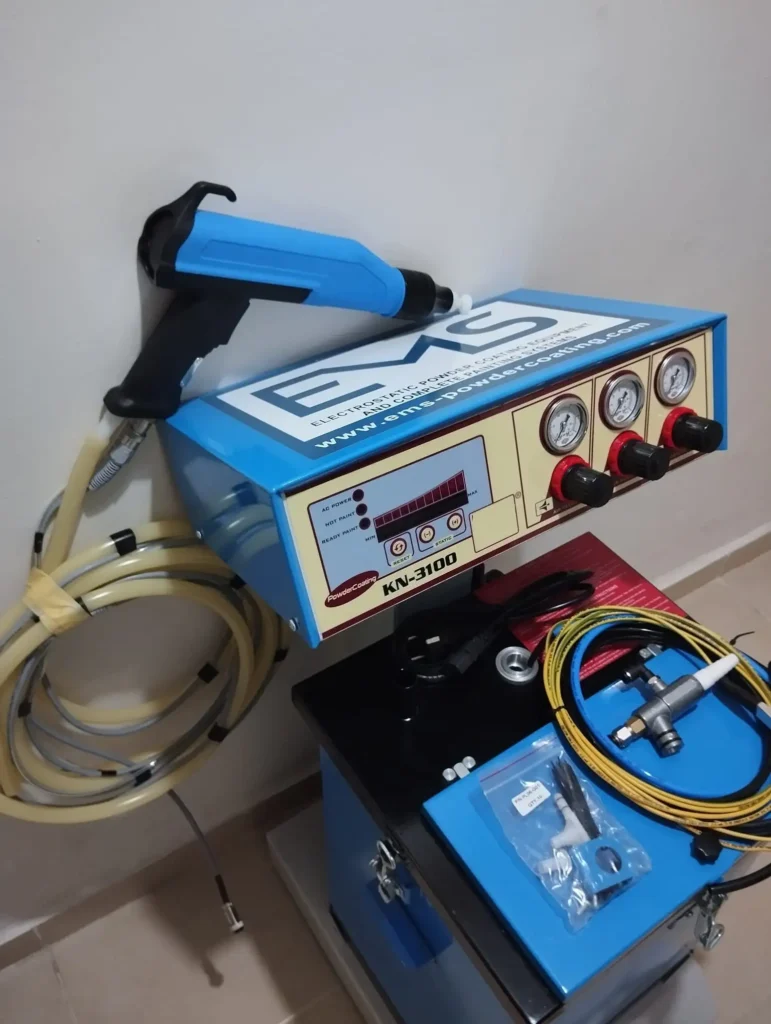
En el proceso de aplicación de pintura electrostática, la elección de la pistola de pulverización es crucial para asegurar una aplicación eficiente y uniforme del recubrimiento en polvo. Existen dos tipos principales de pistolas de pulverización utilizadas en la industria: las pistolas de pulverización Corona y las pistolas de pulverización Triboeléctrica. Cada una de estas tecnologías tiene características específicas que las hacen más adecuadas para ciertos tipos de aplicaciones y entornos. A continuación, se detallan las diferencias clave, ventajas, desventajas, y aplicaciones típicas de cada tipo de pistola.
Pistolas de Pulverización Corona
1.1. Principio de Funcionamiento
Las pistolas de pulverización Corona funcionan mediante la generación de un campo eléctrico intenso en la punta de la pistola, donde se encuentra un electrodo que ioniza el aire circundante. Esta ionización carga eléctricamente las partículas de polvo de pintura mientras son pulverizadas hacia la pieza a recubrir. El electrodo se conecta a un generador de alta tensión que produce una corriente continua, generalmente en el rango de 30 a 100 kV, dependiendo de los requerimientos específicos del recubrimiento y del sustrato.
El campo eléctrico generado atrae las partículas de polvo cargadas negativamente hacia el sustrato, que está conectado a tierra, creando una atracción entre las cargas opuestas que asegura una aplicación uniforme del polvo en toda la superficie del objeto.
1.2. Ventajas de las Pistolas Corona
- Versatilidad: Las pistolas Corona son altamente versátiles y pueden aplicarse en una amplia gama de aplicaciones industriales, desde la pintura de piezas metálicas complejas hasta superficies más simples. Su capacidad para manejar diferentes tipos de polvo y recubrimientos las hace adecuadas para diversas industrias, incluyendo la automotriz, electrodomésticos, y muebles metálicos.
- Control de la Carga: Permiten un control preciso de la cantidad de carga eléctrica aplicada a las partículas de polvo, lo que resulta en una aplicación más controlada y un acabado uniforme.
- Compatibilidad con Polvos de Alta y Baja Densidad: Estas pistolas son capaces de manejar tanto polvos de alta densidad como polvos finos, lo que permite una mayor flexibilidad en la selección del material de recubrimiento.
1.3. Desventajas de las Pistolas Corona
- Efecto Jaula de Faraday: Uno de los principales desafíos con las pistolas Corona es el efecto jaula de Faraday, que ocurre cuando el campo eléctrico no penetra adecuadamente en áreas recónditas o geométricamente complejas del sustrato, como rincones o cavidades. Esto puede resultar en una cobertura desigual y la necesidad de ajustes en la técnica de aplicación o en el diseño de la pistola.
- Requiere Alto Voltaje: El uso de alto voltaje aumenta el riesgo de chispas o descargas eléctricas, lo que requiere medidas de seguridad adicionales y un mantenimiento riguroso para prevenir accidentes.
1.4. Aplicaciones Típicas
Las pistolas Corona se utilizan ampliamente en aplicaciones industriales donde se necesita un recubrimiento uniforme y de alta calidad. Son especialmente útiles en la pintura de piezas metálicas de gran tamaño, carrocerías de automóviles, maquinaria pesada, y productos metálicos para exteriores. También son comunes en la aplicación de recubrimientos donde la eficiencia y la velocidad de producción son críticas.
Pistolas de Pulverización Triboeléctrica
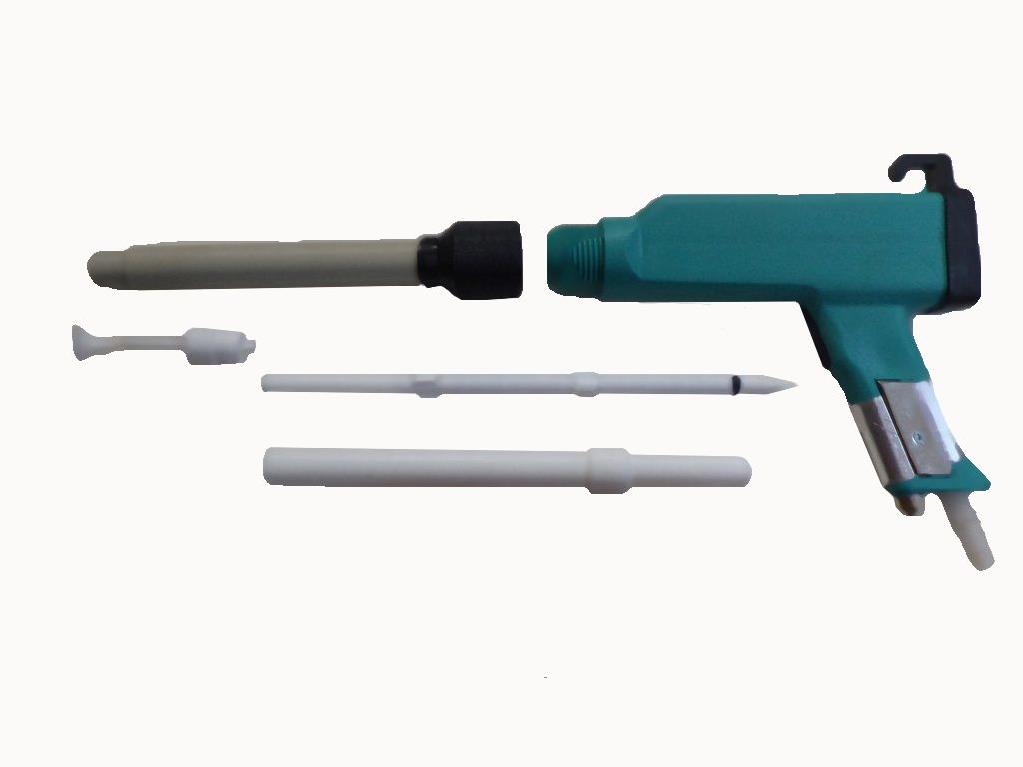
2.1. Principio de Funcionamiento
Las pistolas de pulverización Triboeléctrica funcionan bajo un principio diferente al de las pistolas Corona. En lugar de usar un campo eléctrico para cargar las partículas de polvo, estas pistolas utilizan la fricción para generar una carga. El polvo de pintura es transportado a través de un tubo o canal de material dieléctrico, como plástico o cerámica, que genera una carga estática en las partículas debido al rozamiento contra las paredes del canal.
A medida que el polvo fluye a través del canal, las partículas se cargan positiva o negativamente, dependiendo del tipo de material utilizado y de las propiedades del polvo. Esta carga se adhiere a la superficie del sustrato, que debe estar conectada a tierra para asegurar que las partículas de polvo se atraigan de manera efectiva.
2.2. Ventajas de las Pistolas Triboeléctricas
- Ausencia de Alto Voltaje: Dado que no se necesita un generador de alta tensión, las pistolas triboeléctricas eliminan el riesgo de chispas o descargas eléctricas, lo que las hace más seguras de operar en ciertos entornos.
- Efecto Jaula de Faraday Reducido: Estas pistolas tienden a superar mejor el efecto jaula de Faraday en comparación con las pistolas Corona, permitiendo una mejor cobertura en áreas recónditas y complejas del sustrato.
- Menor Riesgo de Sobrecarga: Al depender de la fricción para cargar las partículas, las pistolas triboeléctricas reducen la probabilidad de sobrecarga de polvo en la superficie, lo que ayuda a evitar el exceso de material y mejora la eficiencia del recubrimiento.
2.3. Desventajas de las Pistolas Triboeléctricas
- Limitaciones en el Tipo de Polvo: Las pistolas triboeléctricas son más sensibles al tipo de polvo utilizado. No todos los polvos se cargan eficazmente mediante fricción, lo que puede limitar las opciones de recubrimiento disponibles.
- Requiere Mayor Control de las Condiciones Ambientales: La eficiencia de la carga triboeléctrica puede verse afectada por factores como la humedad y la temperatura, lo que requiere un control más estricto del entorno de aplicación para garantizar resultados consistentes.
- Mantenimiento y Desgaste: El proceso de carga por fricción puede generar desgaste en las partes internas de la pistola, lo que requiere un mantenimiento más frecuente y puede llevar a un aumento en los costos operativos a largo plazo.
2.4. Aplicaciones Típicas
Las pistolas triboeléctricas se utilizan comúnmente en aplicaciones donde se requiere una alta precisión en la aplicación del recubrimiento, como en la pintura de piezas con geometrías complejas o en la producción de componentes electrónicos. También son populares en industrias donde la seguridad es una preocupación crítica y se desea minimizar el uso de alto voltaje.
Comparación y Selección del Equipo Apropiado
La elección entre una pistola Corona y una Triboeléctrica depende en gran medida de las necesidades específicas de la aplicación, las características del sustrato, y las condiciones del entorno de trabajo.
- Si se requiere versatilidad en el manejo de diferentes tipos de polvos y una aplicación rápida en grandes superficies, la pistola Corona es generalmente la mejor opción.
- Para aplicaciones que involucren piezas con geometrías complejas o en entornos donde la seguridad es una prioridad, la pistola triboeléctrica puede ofrecer ventajas significativas.
En algunos casos, las industrias pueden optar por utilizar una combinación de ambas tecnologías para aprovechar las fortalezas de cada una y minimizar las limitaciones.
No solo fabricamos nuestros equipos de recubrimiento en polvo, sino que también los enviamos a sus instalaciones con cuidado en todo el mundo.
No somos sólo los fabricantes de su equipo de recubrimiento en polvo, también somos sus socios de entrega en todo el mundo.
En Equipo de recubrimiento en polvo EMS, entendemos que entregarle su equipo de recubrimiento en polvo de manera rápida y segura es tan importante como fabricarlo con los más altos estándares. Es por eso que ofrecemos servicios de entrega en todo el mundo a todos nuestros clientes.
Trabajamos con una red de socios de envío experimentados y confiables para garantizar que su equipo llegue a tiempo y en perfectas condiciones. También ofrecemos una variedad de opciones de envío que se adaptan a su presupuesto y necesidades.
Ya sea que necesite que le envíen su equipo a una dirección local o a un destino internacional, podemos ayudarlo. Trabajaremos con usted para elegir la mejor opción de envío para sus necesidades y para mantenerlo actualizado sobre el estado de su envío en cada paso del camino.
Entonces, cuando elige EMS para su equipo de recubrimiento en polvo, no solo obtiene los mejores productos del mercado, sino que también obtiene la mejor experiencia de entrega posible.
Contáctenos hoy para obtener más información sobre nuestros servicios de entrega en todo el mundo.
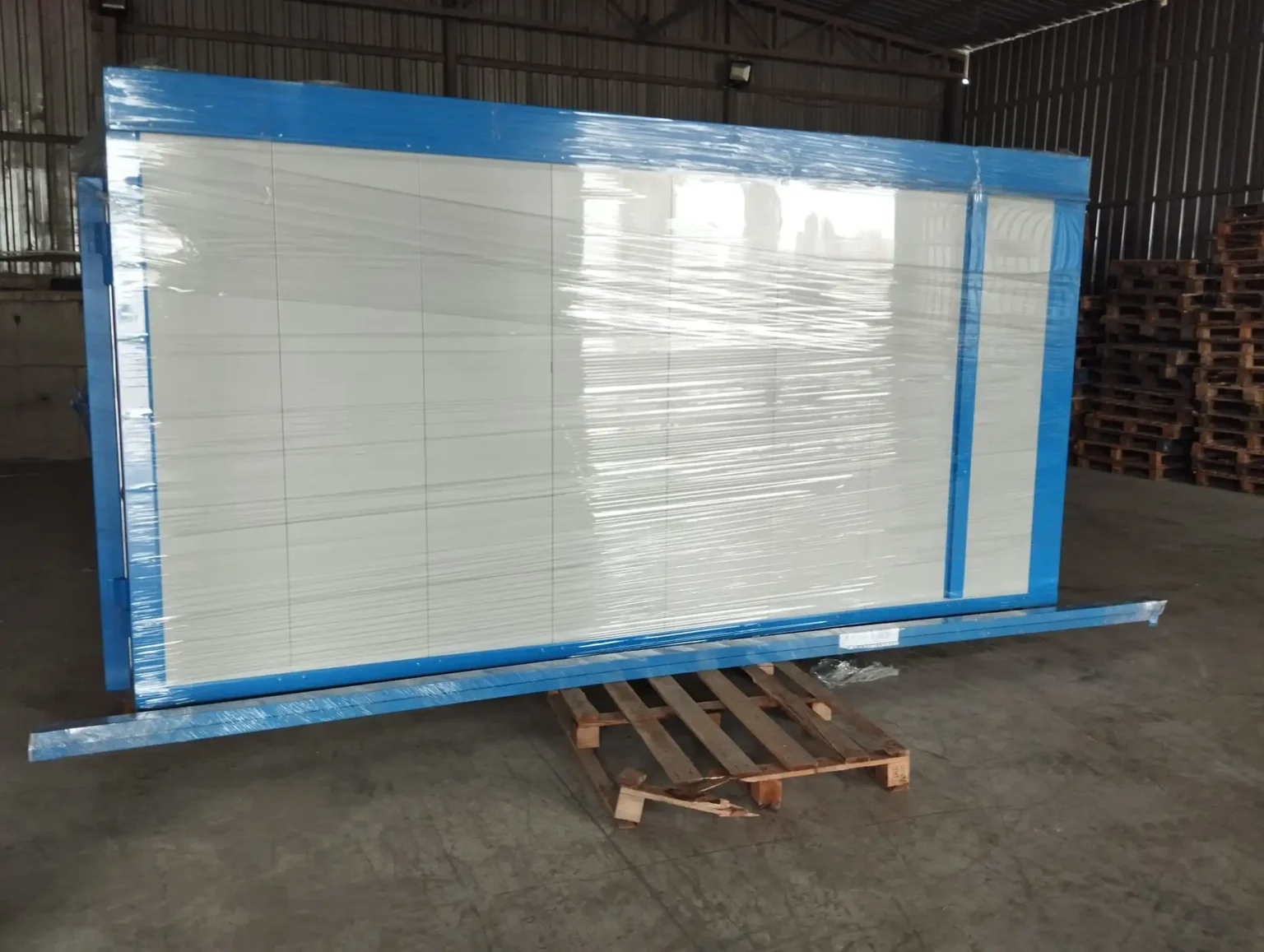