Máquina Automática de Pintura de Tornillo Autoperforante: La Máquina de Recubrimiento en Polvo para Cabezas de Tornillos es un equipo especializado en el proceso de recubrimiento en polvo de tornillos, especialmente en sus cabezas, con el objetivo de proporcionarles una capa protectora que mejorará su resistencia a la corrosión, el desgaste y otros factores ambientales. Este tipo de recubrimiento es crucial en la industria de fabricación de tornillos, ya que ayuda a aumentar la durabilidad del producto final y a garantizar su funcionalidad a largo plazo en diversas aplicaciones industriales y comerciales.
El proceso de recubrimiento en polvo, también conocido como recubrimiento electrostático, es una técnica en la que se utiliza un polvo seco que se adhiere a la superficie del tornillo a través de cargas electrostáticas. El polvo se aplica a las cabezas de los tornillos utilizando un dispositivo pulverizador, donde el polvo cargado se atrae a la superficie metálica del tornillo. Posteriormente, el tornillo recubierto se somete a un proceso de curado en un horno a temperaturas específicas, lo que permite que el recubrimiento se adhiera de manera firme y uniforme.
Las máquinas de recubrimiento en polvo para cabezas de tornillos están diseñadas para asegurar una cobertura completa y consistente de cada tornillo. Estas máquinas cuentan con sistemas avanzados que permiten controlar la cantidad y distribución del polvo sobre las piezas, asegurando que no haya deficiencias o excesos de material. Además, los sistemas de ventilación y filtración juegan un papel clave en el proceso, evitando la dispersión del polvo fuera del área de trabajo y garantizando un entorno limpio y seguro para los operadores.
Un aspecto importante de estas máquinas es su capacidad para trabajar con diferentes tipos de recubrimientos en polvo, como epóxidos, poliésteres, nylon, y otros materiales especializados, dependiendo de las necesidades del cliente o de las especificaciones de la aplicación final del tornillo. Los recubrimientos en polvo pueden ofrecer propiedades como resistencia al calor, a productos químicos, a la abrasión o a la intemperie, lo que las hace ideales para tornillos que se utilizan en condiciones extremas.
Las máquinas modernas para recubrimiento en polvo están equipadas con controles automáticos que permiten programar y monitorear el proceso con alta precisión. Esto incluye ajustes de temperatura, tiempo de curado y la cantidad de polvo aplicada. Estos controles no solo mejoran la calidad del recubrimiento, sino que también optimizan la eficiencia del proceso de producción, reduciendo el tiempo de ciclo y los costos operativos.
El mantenimiento de una máquina de recubrimiento en polvo es fundamental para asegurar su funcionamiento adecuado y prolongar su vida útil. Esto incluye la limpieza regular de los sistemas de aplicación de polvo, la revisión de los componentes eléctricos y mecánicos, y la sustitución de las piezas que puedan desgastarse con el tiempo. La capacitación del personal es igualmente importante para garantizar que los operadores comprendan el funcionamiento de la máquina y puedan solucionar cualquier inconveniente rápidamente.
En resumen, las máquinas de recubrimiento en polvo para cabezas de tornillos son fundamentales en la producción de tornillos de alta calidad que se utilizan en una amplia gama de aplicaciones. Su capacidad para aplicar recubrimientos protectores de manera eficiente y precisa, junto con sus avanzados sistemas de control y monitoreo, las convierte en una herramienta indispensable en la industria de fabricación de tornillos y componentes metálicos.
Máquina de Recubrimiento en Polvo para Cabezas de Tornillos
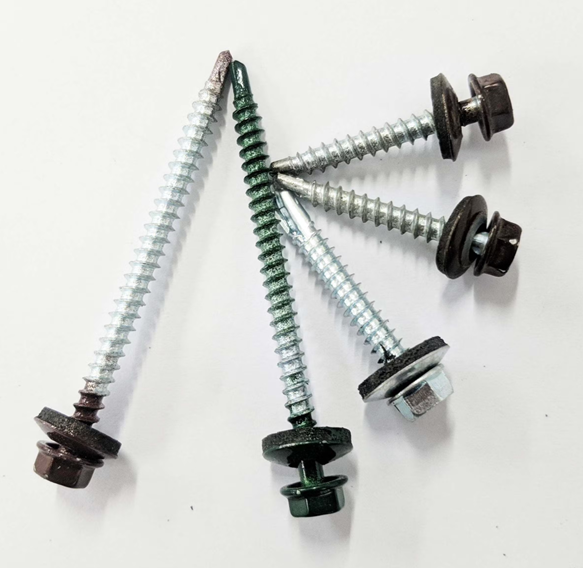
Además de la mejora de la durabilidad y resistencia de los tornillos, el recubrimiento en polvo también proporciona ventajas estéticas. Los recubrimientos pueden aplicarse en una amplia variedad de colores, lo que no solo ayuda en la identificación de las piezas, sino que también puede ser un factor importante en la presentación visual de los productos finales. Este aspecto es especialmente relevante en aplicaciones donde la estética juega un papel importante, como en la industria del diseño de interiores, muebles, y otras áreas donde los tornillos son visibles en el producto terminado.
Otra ventaja significativa del proceso de recubrimiento en polvo es su eficiencia en términos de sostenibilidad. A diferencia de los recubrimientos líquidos tradicionales, que pueden contener disolventes y otros compuestos químicos volátiles, el recubrimiento en polvo es una opción más ecológica. El polvo utilizado no contiene solventes y genera menos residuos. Además, cualquier polvo sobrante puede ser reciclado y reutilizado en el proceso, lo que minimiza el desperdicio y reduce el impacto ambiental. Este enfoque contribuye a la reducción de la huella de carbono y al cumplimiento de las normativas ambientales cada vez más estrictas que exigen la minimización de productos químicos peligrosos.
El proceso de curado, que es una parte esencial de la aplicación del recubrimiento en polvo, también juega un papel crucial en la optimización del rendimiento del recubrimiento. Al someter los tornillos recubiertos a una temperatura controlada en el horno de curado, se asegura que el recubrimiento se adhiera correctamente a la superficie metálica y se cure de manera uniforme. Esto resulta en una capa más densa y homogénea que mejora las propiedades mecánicas de la superficie, como la adherencia, la resistencia al impacto y la flexibilidad del recubrimiento.
Las máquinas de recubrimiento en polvo para cabezas de tornillos también pueden integrarse en líneas de producción automatizadas, lo que permite la fabricación a gran escala de tornillos recubiertos de manera eficiente y con mínima intervención manual. Esto es especialmente útil en plantas de producción de tornillos donde se procesan grandes volúmenes de piezas en poco tiempo. La automatización del proceso de recubrimiento no solo mejora la velocidad de producción, sino que también reduce el riesgo de errores humanos, garantizando una calidad constante y uniforme en todos los tornillos fabricados.
A medida que la demanda de tornillos recubiertos de alta calidad aumenta, las máquinas de recubrimiento en polvo continúan evolucionando para satisfacer las necesidades de la industria. Los avances tecnológicos están impulsando la mejora de estos equipos, ofreciendo capacidades adicionales como sistemas de limpieza automáticos, mejores controles de temperatura y humedad, así como interfaces de usuario más intuitivas. Estas innovaciones no solo mejoran la calidad del recubrimiento, sino que también hacen que el proceso de producción sea más eficiente y rentable.
En el contexto de la industria moderna, los tornillos recubiertos tienen aplicaciones que van más allá de la construcción y la manufactura de productos estándar. Se utilizan en sectores como la automoción, la electrónica, la industria aeroespacial, y en equipos industriales de alta precisión. En estos sectores, la resistencia a condiciones extremas como altas temperaturas, exposición a productos químicos agresivos o entornos húmedos es esencial. El recubrimiento en polvo en estos casos proporciona la solución ideal, ofreciendo una protección duradera y confiable.
Finalmente, la versatilidad de las máquinas de recubrimiento en polvo para cabezas de tornillos también radica en su capacidad para adaptarse a diferentes tamaños y formas de piezas. Aunque el proceso de recubrimiento en polvo es particularmente eficaz para tornillos, también se puede aplicar a otros componentes metálicos con geometrías complejas o irregulares. Esto hace que estas máquinas sean extremadamente versátiles y útiles en una variedad de industrias y aplicaciones que requieren recubrimientos de alta calidad.
En conclusión, las máquinas de recubrimiento en polvo para cabezas de tornillos son una parte fundamental de la producción moderna de tornillos y otros componentes metálicos, proporcionando una capa protectora que mejora la durabilidad, resistencia y apariencia de las piezas. Su tecnología avanzada, capacidad de automatización y eficiencia energética las convierte en una herramienta indispensable para industrias que demandan productos de alta calidad y desempeño superior.
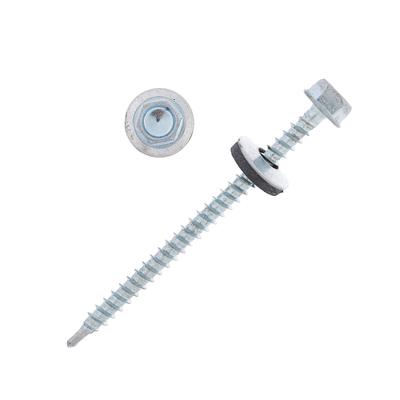
El impacto de las máquinas de recubrimiento en polvo para cabezas de tornillos no se limita únicamente a la mejora del producto final, sino que también tiene un efecto positivo en la optimización de los procesos de producción y en la reducción de costos. Estas máquinas pueden trabajar de manera continua y a gran velocidad, lo que las convierte en una solución rentable para la fabricación en serie de tornillos recubiertos. El proceso automatizado, junto con la capacidad de reciclar el polvo sobrante, ayuda a minimizar los costos operativos y maximizar la eficiencia de las instalaciones de producción.
Las máquinas de recubrimiento en polvo también ofrecen ventajas significativas en cuanto a la seguridad en el ambiente de trabajo. A diferencia de los recubrimientos líquidos, que requieren el manejo de solventes volátiles y productos químicos peligrosos, el recubrimiento en polvo elimina estos riesgos, creando un entorno de trabajo más seguro para los operarios. Además, los sistemas de ventilación y filtración incorporados en las máquinas están diseñados para prevenir la dispersión del polvo fuera del área de trabajo, garantizando que se cumplan las normativas de seguridad e higiene laboral.
Otra área en la que las máquinas de recubrimiento en polvo para cabezas de tornillos están demostrando su eficacia es en la mejora de la resistencia al desgaste de los tornillos. El recubrimiento en polvo puede aumentar significativamente la resistencia a la abrasión de la superficie de los tornillos, lo que los hace más adecuados para aplicaciones donde se someten a fricción constante, como en la industria automotriz, maquinaria pesada o equipos industriales. Este tipo de recubrimiento también ayuda a prevenir la formación de óxido, lo que alarga la vida útil de las piezas y reduce la necesidad de reemplazo frecuente.
La flexibilidad del proceso de recubrimiento en polvo también permite que las máquinas se adapten a distintos tipos de acabados. Esto incluye acabados texturizados, brillantes o mate, lo que puede ser importante dependiendo de la función o el diseño requerido del tornillo. La capacidad de ofrecer acabados visualmente atractivos a la par que funcionales ha hecho que los recubrimientos en polvo sean una opción popular para tornillos utilizados en aplicaciones de diseño más sofisticado, como en electrodomésticos de gama alta o dispositivos electrónicos.
Además, el recubrimiento en polvo es especialmente efectivo para crear superficies con propiedades de deslizamiento mejoradas. Esto es útil en aplicaciones donde los tornillos deben pasar a través de materiales con alta fricción o donde se requiere un ensamblaje rápido. La capa de polvo curado actúa como un lubricante en algunas aplicaciones, facilitando el proceso de instalación y reduciendo la posibilidad de daños en las piezas o el desgaste prematuro del tornillo.
La integración de nuevas tecnologías, como la digitalización y el Internet de las Cosas (IoT), también está permitiendo mejorar el control y la supervisión del proceso de recubrimiento en polvo. Los sistemas conectados permiten a los operadores monitorear las condiciones de la máquina en tiempo real, obtener datos sobre el rendimiento del equipo y realizar ajustes precisos sin necesidad de intervención manual. Este tipo de monitoreo constante ayuda a evitar errores y fallas en el proceso, lo que asegura una calidad de recubrimiento consistente en todos los lotes de producción.
La capacidad de realizar ajustes finos en los parámetros de temperatura, presión y velocidad durante el proceso de recubrimiento en polvo también permite a las máquinas adaptarse a las características específicas de cada lote de producción. Los fabricantes de tornillos pueden ajustar estos parámetros para adaptarse a diferentes tipos de polvo o requisitos de curado, lo que otorga una flexibilidad sin precedentes en la producción de piezas personalizadas.
El futuro de las máquinas de recubrimiento en polvo para cabezas de tornillos está ligado a la innovación constante. A medida que avanzan las tecnologías de recubrimiento, las máquinas continúan mejorando en términos de velocidad, precisión y sostenibilidad. El desarrollo de nuevos tipos de polvo, como los que incorporan partículas de materiales nanométricos, promete abrir nuevas posibilidades para mejorar aún más las propiedades de los recubrimientos, como la conductividad térmica, la resistencia a la corrosión y las características antiestáticas.
En conclusión, las máquinas de recubrimiento en polvo para cabezas de tornillos desempeñan un papel crucial en la fabricación de productos de alta calidad, proporcionando una capa protectora duradera y eficiente que mejora las propiedades mecánicas y estéticas de los tornillos. Además de sus beneficios funcionales, estas máquinas también contribuyen a la sostenibilidad y eficiencia de los procesos de producción, reduciendo costos, residuos y riesgos asociados con el uso de químicos peligrosos. Con la constante evolución de la tecnología, el futuro de estas máquinas parece aún más prometedor, con nuevas innovaciones que seguirán mejorando la calidad, la versatilidad y la rentabilidad de los recubrimientos en polvo.
1. Proceso de Recubrimiento en Polvo
El proceso de recubrimiento en polvo para cabezas de tornillos comienza con la preparación de la superficie. Antes de aplicar el recubrimiento, es esencial limpiar adecuadamente las cabezas de los tornillos para eliminar cualquier contaminante, como aceites, suciedad o óxido, que podría afectar la adherencia del recubrimiento. Este proceso se realiza mediante diferentes técnicas, como el granallado, el uso de limpiadores químicos o mediante tratamientos térmicos.
Una vez que la superficie está limpia, el tornillo se carga en una máquina de recubrimiento en polvo, donde el polvo cargado electrostáticamente se adhiere a la superficie del tornillo. Este polvo puede ser una mezcla de resinas, pigmentos y otros aditivos que proporcionan las propiedades deseadas en el recubrimiento, como la durabilidad, resistencia a la corrosión o un acabado estético específico. Después de la aplicación, el tornillo recubierto se pasa por un horno de curado donde el polvo se funde y se adhiere de manera permanente a la pieza, formando una capa sólida y resistente.
2. Tipos de Recubrimientos en Polvo
Existen diversos tipos de recubrimientos en polvo que se pueden aplicar a las cabezas de los tornillos, dependiendo de los requisitos específicos de la aplicación final. Entre los más comunes se incluyen:
- Epóxidos: Son conocidos por su excelente adherencia y resistencia a la corrosión, siendo ideales para aplicaciones donde se requiere una alta resistencia a ambientes húmedos o corrosivos.
- Poliésteres: Ofrecen una buena resistencia a la intemperie y a los rayos UV, lo que los hace ideales para aplicaciones exteriores o en ambientes con exposición al sol.
- Nylon: Utilizados en aplicaciones donde se requiere una alta resistencia al desgaste y a los productos químicos.
- Pudrizados metálicos: Se utilizan para crear recubrimientos decorativos o de alta resistencia térmica, comunes en aplicaciones donde el tornillo necesita soportar altas temperaturas.
3. Ventajas del Recubrimiento en Polvo
El recubrimiento en polvo ofrece varias ventajas sobre los métodos tradicionales de recubrimiento, como los recubrimientos líquidos. Entre estas ventajas se incluyen:
- Mayor durabilidad: Los recubrimientos en polvo proporcionan una capa más densa y resistente, lo que aumenta la durabilidad y la vida útil de los tornillos.
- Mejor resistencia a la corrosión: Los recubrimientos en polvo son altamente efectivos para prevenir la formación de óxido, lo que los hace ideales para aplicaciones en ambientes húmedos o agresivos.
- Eficiencia y menor desperdicio: El proceso de recubrimiento en polvo genera menos residuos y permite reciclar el polvo sobrante, lo que lo convierte en una opción más ecológica.
- Versatilidad estética: Los recubrimientos en polvo pueden aplicarse en una amplia gama de colores y acabados, ofreciendo tanto protección como un valor estético adicional.
4. Sostenibilidad y Eficiencia Energética
El recubrimiento en polvo es una opción más ecológica en comparación con otros métodos de recubrimiento. Al no requerir disolventes ni químicos peligrosos, el proceso es más limpio y produce menos emisiones de compuestos orgánicos volátiles (COV). Además, el polvo sobrante se puede recolectar y reutilizar, lo que reduce el desperdicio de materiales y mejora la eficiencia del proceso. Las máquinas modernas también están diseñadas para consumir menos energía, lo que contribuye a reducir los costos operativos y la huella de carbono de las instalaciones de producción.
5. Automatización y Control del Proceso
Las máquinas de recubrimiento en polvo para cabezas de tornillos están equipadas con sistemas automatizados que permiten controlar con precisión el proceso de aplicación. Esto incluye el ajuste de parámetros como la velocidad de aplicación, la cantidad de polvo, la temperatura del horno de curado y el tiempo de curado. Estos sistemas automatizados no solo mejoran la calidad del recubrimiento, sino que también optimizan la producción, permitiendo la fabricación en serie de tornillos recubiertos de manera consistente y sin intervención manual.
Además, la integración de tecnologías como el Internet de las Cosas (IoT) permite a los operadores monitorear las máquinas en tiempo real, lo que facilita la identificación de posibles fallos o ineficiencias antes de que afecten la producción. Este tipo de monitoreo remoto también ayuda a reducir el tiempo de inactividad de las máquinas y a mejorar el mantenimiento predictivo, lo que asegura que las máquinas sigan funcionando de manera óptima.
6. Aplicaciones de Tornillos Recubiertos en Polvo
Los tornillos recubiertos en polvo tienen una amplia variedad de aplicaciones, que van más allá de la industria de la construcción. Algunos de los sectores clave en los que se utilizan incluyen:
- Industria automotriz: Los tornillos recubiertos son ideales para aplicaciones en vehículos, donde se requieren propiedades como la resistencia a la corrosión, la abrasión y la alta temperatura.
- Electrónica: En dispositivos electrónicos, donde los tornillos deben ser resistentes a la corrosión y al desgaste, especialmente en equipos de alta precisión.
- Aeroespacial: En la fabricación de componentes aeroespaciales, donde la durabilidad y la resistencia a las condiciones extremas son fundamentales.
- Equipos industriales: En maquinaria pesada o equipos industriales que operan en condiciones de alta fricción o exposición a productos químicos.
7. Mantenimiento y Cuidado de las Máquinas de Recubrimiento
El mantenimiento regular de las máquinas de recubrimiento en polvo es crucial para asegurar su rendimiento óptimo y prolongar su vida útil. Esto incluye la limpieza periódica de los sistemas de aplicación de polvo, la inspección y reemplazo de piezas desgastadas, y la revisión de los sistemas de control y ventilación. La capacitación adecuada del personal es esencial para garantizar que los operadores comprendan el funcionamiento de las máquinas y puedan identificar rápidamente cualquier problema.
El mantenimiento preventivo ayuda a evitar costosos tiempos de inactividad y asegura que las máquinas sigan funcionando a su máxima eficiencia, lo que contribuye a una producción más rentable.
8. Innovación y Futuro de las Máquinas de Recubrimiento en Polvo
El futuro de las máquinas de recubrimiento en polvo para cabezas de tornillos está marcado por avances tecnológicos que continúan mejorando tanto la calidad del recubrimiento como la eficiencia del proceso de fabricación. Los desarrollos en la tecnología de polvo, como el uso de recubrimientos de partículas nanométricas, están abriendo nuevas posibilidades para mejorar las propiedades de los recubrimientos, como la resistencia a la temperatura, la conductividad térmica o la resistencia a los productos químicos.
Además, las tendencias hacia la automatización avanzada, el uso de inteligencia artificial y el monitoreo de la salud de la máquina permitirán una mayor personalización de los recubrimientos y una reducción aún mayor de los costos operativos. Esto contribuirá a un futuro en el que las máquinas de recubrimiento en polvo sean aún más rápidas, eficientes y sostenibles, manteniendo un papel clave en la fabricación de tornillos y componentes metálicos de alta calidad.
Conclusión
Las máquinas de recubrimiento en polvo para cabezas de tornillos representan una tecnología esencial en la fabricación moderna, ofreciendo una solución eficiente y rentable para mejorar las propiedades de los tornillos y otros componentes metálicos. Con su capacidad para proporcionar recubrimientos duraderos, resistentes y estéticamente atractivos, junto con su contribución a la sostenibilidad y la eficiencia de los procesos de producción, estas máquinas continúan siendo una herramienta fundamental en diversas industrias. Con el continuo avance de la tecnología, su capacidad para adaptarse a las demandas del mercado seguirá siendo un factor clave en el éxito de la fabricación de tornillos y otros productos recubiertos.
Proceso de Recubrimiento en Polvo
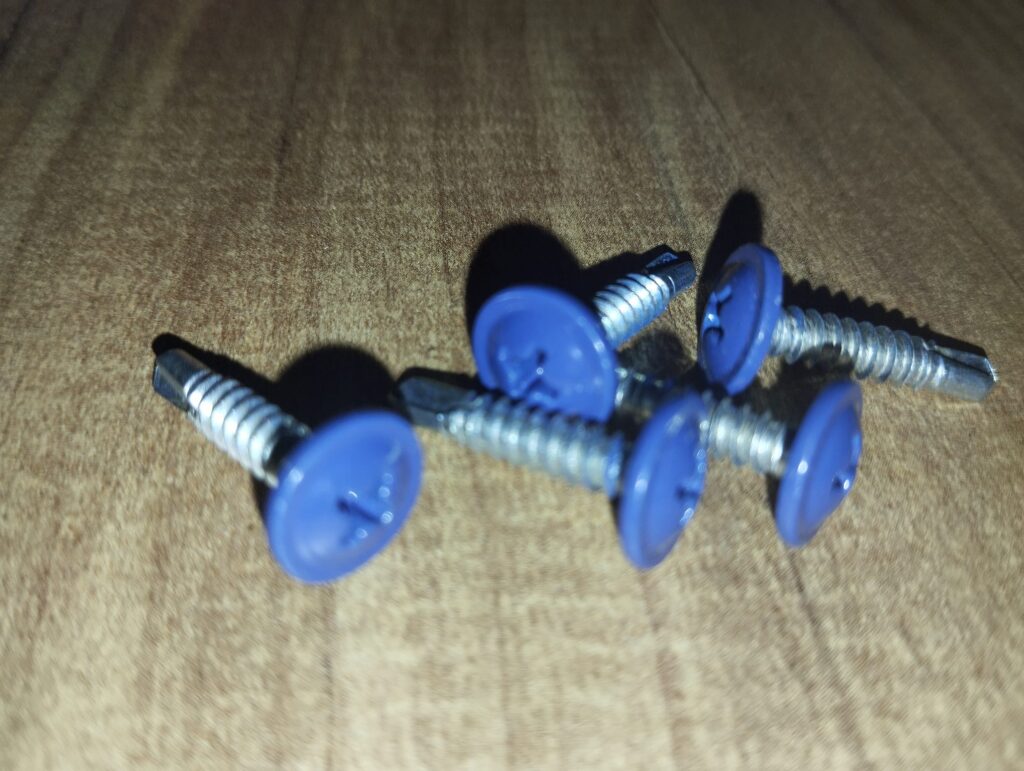
La máquina de recubrimiento en polvo para cabezas de tornillos es una tecnología avanzada utilizada para aplicar una capa de polvo seco sobre las superficies de los tornillos, proporcionando una protección adicional que mejora su durabilidad y rendimiento. Este tipo de recubrimiento es esencial para incrementar la resistencia a la corrosión, al desgaste y a otros factores ambientales que pueden afectar la vida útil de los tornillos en diversas aplicaciones industriales.
El recubrimiento en polvo se aplica a través de un proceso electrostático, en el que el polvo cargado es atraído hacia las cabezas de los tornillos, formando una capa uniforme sobre la superficie. Luego, los tornillos recubiertos son sometidos a un proceso de curado en un horno, donde el polvo se fusiona y se adhiere de manera permanente a la pieza, creando una capa resistente y duradera.
Existen varios tipos de recubrimientos en polvo, cada uno diseñado para satisfacer necesidades específicas según las condiciones a las que estarán expuestos los tornillos. Los recubrimientos epóxicos, por ejemplo, son ideales para proporcionar una alta resistencia a la corrosión, lo que los hace adecuados para ambientes húmedos o corrosivos. Por otro lado, los recubrimientos de poliéster son efectivos para proteger contra los daños causados por la intemperie y los rayos UV, mientras que los recubrimientos de nylon ofrecen una mayor resistencia al desgaste y la abrasión, lo cual es útil en aplicaciones que requieren alta fricción.
Una de las principales ventajas del recubrimiento en polvo es su capacidad para proporcionar una capa de protección más gruesa y duradera en comparación con los recubrimientos líquidos tradicionales. Esto no solo mejora las propiedades mecánicas de los tornillos, sino que también proporciona una mejor resistencia al desgaste, lo que alarga la vida útil de las piezas y reduce la necesidad de reemplazos frecuentes. Además, el proceso de recubrimiento en polvo no requiere el uso de solventes o productos químicos peligrosos, lo que lo convierte en una opción más ecológica y segura para el medio ambiente y los operadores.
Las máquinas de recubrimiento en polvo también son altamente eficientes en términos de consumo de material. Cualquier polvo que no se adhiera a las piezas se puede reciclar y reutilizar, lo que minimiza el desperdicio y reduce los costos operativos. Además, los sistemas avanzados de control y automatización presentes en las máquinas modernas permiten monitorear y ajustar el proceso de recubrimiento en tiempo real, garantizando una calidad uniforme y constante en todos los lotes de producción.
Otro aspecto importante de las máquinas de recubrimiento en polvo es su capacidad para trabajar con tornillos de diferentes tamaños y formas, lo que les otorga una gran versatilidad. Estas máquinas no solo están diseñadas para aplicar recubrimientos a las cabezas de los tornillos, sino también a otras partes de la pieza, según las necesidades del cliente. Además, el recubrimiento en polvo puede aplicarse en una variedad de colores y acabados, lo que añade una capa estética al producto final, lo que es especialmente relevante en sectores donde la apariencia también es importante.
La automatización de las máquinas de recubrimiento en polvo ha permitido una mejora significativa en la velocidad y eficiencia de la producción. En instalaciones donde se fabrican grandes volúmenes de tornillos recubiertos, la automatización reduce los tiempos de ciclo y minimiza la intervención humana, lo que resulta en un proceso más rápido y económico. Además, las tecnologías emergentes como el Internet de las Cosas (IoT) y la inteligencia artificial permiten la monitorización remota de las máquinas, facilitando el diagnóstico de posibles fallos y optimizando el mantenimiento preventivo.
El recubrimiento en polvo también presenta una serie de ventajas frente a otros métodos de recubrimiento, como los recubrimientos líquidos. Además de ser más duradero, el recubrimiento en polvo es menos propenso a las fisuras y desprendimientos, lo que mejora las propiedades de la pieza durante su ciclo de vida. Asimismo, la falta de disolventes hace que el proceso sea más seguro y menos perjudicial para la salud de los trabajadores, lo que contribuye a un ambiente de trabajo más limpio y seguro.
En cuanto al mantenimiento, las máquinas de recubrimiento en polvo requieren un cuidado regular para asegurar su buen funcionamiento. Esto incluye la limpieza de los sistemas de aplicación de polvo, la revisión de los hornos de curado y la inspección periódica de los componentes mecánicos y eléctricos. Un mantenimiento adecuado asegura que las máquinas sigan funcionando de manera eficiente, lo que contribuye a la reducción de los costos de operación y prolonga la vida útil del equipo.
El futuro de las máquinas de recubrimiento en polvo está marcado por una continua innovación en las técnicas de aplicación y los materiales utilizados. Los avances en la tecnología del polvo, como el desarrollo de recubrimientos especiales que incorporan nanopartículas o materiales compuestos, prometen mejorar aún más las propiedades de los recubrimientos, como la conductividad térmica, la resistencia a la abrasión o la protección contra los productos químicos agresivos. Estos avances permitirán que las máquinas de recubrimiento en polvo sigan evolucionando para satisfacer las necesidades de una amplia gama de industrias.
En resumen, las máquinas de recubrimiento en polvo para cabezas de tornillos juegan un papel crucial en la producción de tornillos de alta calidad, ofreciendo una capa de protección que mejora tanto la funcionalidad como la estética de las piezas. La tecnología continua avanzando para hacer estos procesos más eficientes, sostenibles y rentables, lo que hace que estas máquinas sean una inversión valiosa para las empresas que buscan optimizar sus procesos de fabricación y ofrecer productos duraderos y de alta calidad.
Tipos de Recubrimientos en Polvo
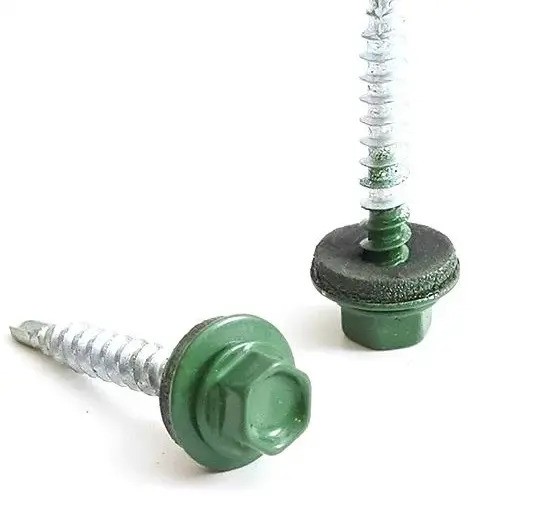
La máquina de recubrimiento en polvo para cabezas de tornillos es una herramienta fundamental en la producción moderna, utilizada para aplicar una capa de polvo seco sobre la superficie de los tornillos, lo que mejora sus propiedades mecánicas y estéticas. Este proceso es crucial para garantizar una mayor durabilidad y resistencia de los tornillos, especialmente en aplicaciones donde están expuestos a condiciones extremas, como alta humedad, fricción o exposición a productos químicos.
El recubrimiento en polvo se aplica mediante un proceso electrostático, donde el polvo cargado se adhiere a la superficie del tornillo. Después de la aplicación, los tornillos recubiertos se curan en un horno a temperaturas específicas, lo que permite que el polvo se fusione y forme una capa sólida, dándole propiedades como mayor resistencia a la corrosión, al desgaste y mejor adherencia. Este proceso resulta en una capa mucho más duradera y resistente que los recubrimientos líquidos tradicionales.
Una de las principales ventajas del recubrimiento en polvo es su durabilidad superior en comparación con los métodos convencionales. Las piezas recubiertas tienen una mayor resistencia al desgaste y la corrosión, lo que extiende su vida útil y reduce la frecuencia de reemplazo. Además, el recubrimiento en polvo es ideal para aplicaciones en las que los tornillos se encuentran expuestos a condiciones ambientales rigurosas, como en la industria automotriz, la construcción o la maquinaria pesada.
El proceso de recubrimiento en polvo también es más ecológico que los recubrimientos líquidos tradicionales, ya que no utiliza solventes ni químicos peligrosos. Esto no solo hace que el proceso sea más seguro para los trabajadores, sino que también reduce las emisiones de compuestos orgánicos volátiles (COV), que pueden ser perjudiciales para la salud y el medio ambiente. Además, cualquier polvo que no se adhiera a la pieza puede ser reciclado y reutilizado, lo que disminuye el desperdicio de material y mejora la eficiencia del proceso.
Una de las características más destacadas de las máquinas de recubrimiento en polvo es su capacidad de automatización. Esto permite que el proceso se realice de manera más rápida y precisa, con mínima intervención manual. Las máquinas modernas están equipadas con sistemas avanzados de control de temperatura, velocidad y cantidad de polvo aplicado, lo que garantiza una cobertura uniforme y consistente en todas las piezas. Esto es especialmente importante en líneas de producción de tornillos en grandes volúmenes, donde la eficiencia y la calidad del recubrimiento deben ser constantes.
Otro beneficio clave del recubrimiento en polvo es su versatilidad. Las máquinas de recubrimiento en polvo pueden trabajar con una amplia gama de tamaños y formas de tornillos, lo que las hace adecuadas para diferentes tipos de productos y aplicaciones. Además, el recubrimiento en polvo se puede aplicar en una variedad de acabados, como texturizados, brillantes o mates, lo que agrega valor estético a los tornillos. Esto es especialmente importante en sectores donde la apariencia de las piezas también es un factor decisivo, como en electrodomésticos de gama alta o en productos de diseño.
Las máquinas de recubrimiento en polvo también contribuyen a la mejora de la seguridad en el entorno de trabajo. Al eliminar la necesidad de manejar solventes tóxicos o químicos peligrosos, se crea un ambiente de trabajo más limpio y seguro para los operarios. Además, los sistemas de ventilación y filtración de aire en las máquinas ayudan a evitar que el polvo se disperse fuera de las áreas de trabajo, cumpliendo con las normativas de seguridad y minimizando el riesgo de inhalación de polvo.
La eficiencia del proceso de recubrimiento en polvo también se traduce en ahorros en los costos operativos. La automatización y el reciclaje del polvo sobrante permiten que las empresas reduzcan los desperdicios y optimicen los recursos, lo que puede reducir significativamente los costos asociados con el consumo de materiales y la mano de obra. Las máquinas de recubrimiento en polvo también tienen una vida útil prolongada si se mantienen adecuadamente, lo que contribuye a un retorno de inversión positivo a largo plazo.
En términos de mantenimiento, es fundamental que las máquinas de recubrimiento en polvo sean objeto de un cuidado regular para asegurar su funcionamiento eficiente. Esto incluye la limpieza de los sistemas de aplicación de polvo, la inspección y calibración de los hornos de curado, así como la revisión periódica de los componentes mecánicos y eléctricos. Un buen mantenimiento ayuda a reducir tiempos de inactividad no planificados y a garantizar que el proceso de recubrimiento se realice de manera continua y sin problemas.
El futuro de las máquinas de recubrimiento en polvo está impulsado por la innovación tecnológica. Los avances en los recubrimientos y las mejoras en las máquinas, como el uso de sensores inteligentes y sistemas de monitoreo en tiempo real, prometen hacer estos procesos aún más eficientes y precisos. Las tecnologías emergentes, como los recubrimientos basados en nanopartículas o los avances en la automatización y la inteligencia artificial, permitirán una mayor personalización y optimización de los recubrimientos según las necesidades específicas de los clientes.
En conclusión, las máquinas de recubrimiento en polvo para cabezas de tornillos juegan un papel crucial en la fabricación moderna de piezas de alta calidad. Ofrecen una solución eficaz y rentable para mejorar las propiedades de los tornillos, brindando una capa protectora que mejora tanto su durabilidad como su apariencia. Gracias a su capacidad de automatización, su eficiencia y su sostenibilidad, las máquinas de recubrimiento en polvo continúan siendo una herramienta indispensable para las industrias que requieren tornillos y otros componentes metálicos de alto rendimiento.
Ventajas del Recubrimiento en Polvo
La máquina de recubrimiento en polvo para cabezas de tornillos es una herramienta esencial para la mejora de las propiedades de los tornillos, proporcionando una capa protectora duradera y resistente a factores como la corrosión, el desgaste y las condiciones ambientales extremas. Este proceso de recubrimiento en polvo, realizado mediante un sistema electrostático, permite que el polvo cargado se adhiera a la superficie del tornillo antes de ser curado a altas temperaturas en un horno, formando una capa sólida y unificada.
El recubrimiento en polvo mejora considerablemente las características del tornillo, al ofrecerle una resistencia superior en comparación con otros métodos tradicionales de recubrimiento. Esta tecnología es especialmente útil en aplicaciones industriales donde los tornillos deben soportar condiciones adversas como alta humedad, exposición a productos químicos agresivos, o altas temperaturas. El recubrimiento también puede proporcionar una mejor adherencia y mayor durabilidad de las piezas, prolongando su vida útil y reduciendo la necesidad de reemplazo frecuente.
El proceso de recubrimiento en polvo es eficiente en cuanto al consumo de material, ya que el polvo que no se adhiere a la pieza puede ser reciclado y reutilizado. Esto no solo reduce los desperdicios, sino que también optimiza los costos operativos. Además, al eliminar la necesidad de solventes y productos químicos peligrosos, el recubrimiento en polvo es una opción más ecológica, menos dañina para el medio ambiente y para la salud de los trabajadores, en comparación con los recubrimientos líquidos tradicionales.
Las máquinas de recubrimiento en polvo están diseñadas para ser altamente automatizadas, lo que permite realizar el proceso de manera más rápida y con menos intervención manual. Estas máquinas son capaces de garantizar una cobertura uniforme y consistente en todas las piezas, lo que es crucial cuando se fabrican grandes volúmenes de tornillos. Los sistemas de control de temperatura, velocidad y cantidad de polvo aplicado ayudan a asegurar que los recubrimientos sean de alta calidad y cumplan con los estándares requeridos.
Otra característica importante de estas máquinas es su versatilidad. Pueden trabajar con tornillos de diversos tamaños y formas, adaptándose a las necesidades de producción de diferentes sectores. Además, el recubrimiento en polvo se puede aplicar en una variedad de acabados y colores, lo que añade valor estético a los tornillos, algo que es relevante en productos donde la apariencia también es un factor importante, como en la industria de electrodomésticos o en productos de diseño de alta gama.
A medida que la tecnología de recubrimiento en polvo continúa avanzando, se espera que las máquinas de recubrimiento en polvo se vuelvan aún más eficientes. El uso de tecnologías emergentes, como la inteligencia artificial y el Internet de las Cosas (IoT), permitirá un monitoreo en tiempo real de las máquinas y del proceso de recubrimiento, lo que mejorará aún más la calidad, la precisión y la eficiencia operativa. La integración de sensores inteligentes en las máquinas permitirá a los operadores identificar problemas potenciales antes de que afecten la producción, optimizando el tiempo de operación y reduciendo los costos asociados con el mantenimiento no planificado.
Además, el recubrimiento en polvo está ganando popularidad en diversas industrias debido a sus beneficios tanto en términos de rendimiento como de sostenibilidad. Sectores como la automoción, la fabricación de maquinaria pesada, la industria electrónica y la aeroespacial están utilizando cada vez más esta tecnología para mejorar la resistencia y la fiabilidad de los componentes metálicos. En particular, el recubrimiento en polvo es una excelente opción para productos que deben soportar ambientes agresivos o condiciones extremas, como los tornillos utilizados en el ensamblaje de vehículos, equipos industriales o en aplicaciones aeroespaciales.
En términos de mantenimiento, es fundamental que las máquinas de recubrimiento en polvo sean sometidas a un cuidado regular para garantizar que sigan funcionando de manera eficiente a lo largo del tiempo. Esto incluye la limpieza periódica de los sistemas de aplicación de polvo, la inspección de los hornos de curado y la verificación de los componentes mecánicos y eléctricos. Un mantenimiento adecuado ayuda a evitar tiempos de inactividad inesperados y a asegurar que el proceso de recubrimiento se mantenga de alta calidad.
El futuro del recubrimiento en polvo se perfila como una de las tecnologías más importantes para la mejora de los productos industriales. La innovación continua en los materiales de recubrimiento y en las máquinas de recubrimiento, así como la adopción de tecnologías avanzadas, permitirá a las industrias beneficiarse de recubrimientos cada vez más resistentes y eficientes. Las máquinas de recubrimiento en polvo seguirán siendo esenciales para la fabricación de tornillos y otros componentes metálicos de alta calidad, proporcionando un rendimiento superior en comparación con los recubrimientos tradicionales.
En resumen, las máquinas de recubrimiento en polvo para cabezas de tornillos ofrecen una solución efectiva para mejorar la durabilidad, resistencia y apariencia de los tornillos. Con sus beneficios de eficiencia, sostenibilidad y calidad, el proceso de recubrimiento en polvo sigue siendo una de las opciones preferidas en diversas industrias, especialmente en aplicaciones que requieren componentes duraderos y de alto rendimiento.
Automatización y Control del Proceso
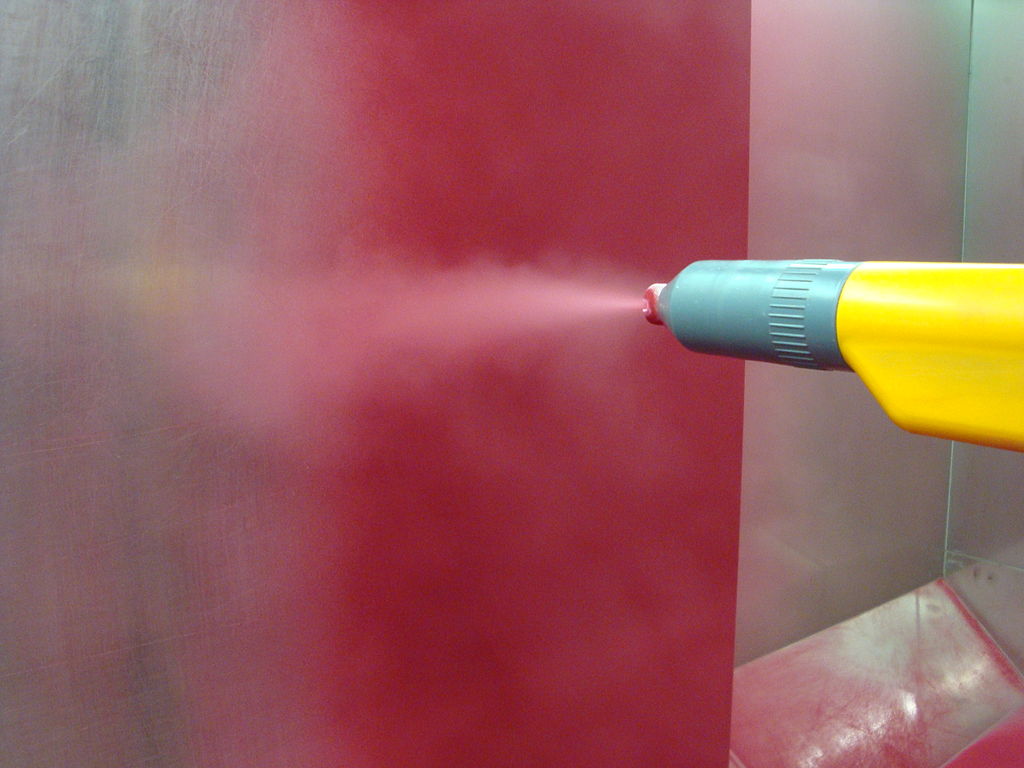
La máquina de recubrimiento en polvo para cabezas de tornillos es una herramienta clave en la producción moderna, diseñada para aplicar una capa uniforme de polvo sobre las piezas de metal. Este proceso mejora las propiedades mecánicas de los tornillos, incrementando su resistencia a la corrosión, al desgaste y otros factores ambientales. A través de un sistema electrostático, el polvo cargado se adhiere a la superficie del tornillo antes de ser curado en un horno a temperaturas específicas. El resultado es un recubrimiento sólido y duradero que proporciona mayor longevidad a las piezas.
El proceso de recubrimiento en polvo es notable por su eficiencia. El recubrimiento es más duradero y resistente que los recubrimientos líquidos tradicionales, lo que hace que los tornillos sean ideales para aplicaciones en ambientes extremos. Esta tecnología es especialmente útil en sectores como la automoción, la maquinaria pesada y la electrónica, donde las piezas metálicas están expuestas a condiciones adversas.
Una de las grandes ventajas de este proceso es la posibilidad de reciclar el polvo sobrante que no se adhiere a la pieza. Este reciclaje de material contribuye a reducir los costos operativos y el desperdicio de recursos, lo que hace que el proceso de recubrimiento en polvo sea más económico y sostenible. Además, al no utilizar disolventes ni productos químicos peligrosos, el recubrimiento en polvo es una opción más ecológica, minimizando el impacto ambiental y los riesgos para la salud de los trabajadores.
El recubrimiento en polvo también mejora la estética de los tornillos. La capa de polvo se puede aplicar en una variedad de acabados, como texturizados, brillantes o mates, y en diferentes colores. Esto es especialmente importante para productos donde la apariencia también juega un papel relevante, como en el caso de tornillos para electrodomésticos, dispositivos electrónicos o productos de diseño.
Las máquinas de recubrimiento en polvo están diseñadas para adaptarse a diferentes tipos y tamaños de tornillos, lo que las hace extremadamente versátiles. Estas máquinas pueden manejar piezas de diversas formas y dimensiones, lo que les permite ser útiles en una amplia variedad de aplicaciones industriales. Además, el proceso de recubrimiento es altamente automatizado, lo que permite que el proceso sea más rápido y eficiente, con menos intervención manual y mayor precisión.
El proceso automatizado también asegura una cobertura uniforme en todas las piezas, lo que es crucial cuando se produce en grandes volúmenes. Las máquinas modernas están equipadas con sistemas avanzados de control de temperatura, velocidad y cantidad de polvo aplicado, lo que garantiza que las piezas recubiertas mantengan un estándar de calidad constante. Esta automatización permite que el proceso sea más consistente, con menos variabilidad entre los lotes de producción.
El recubrimiento en polvo también se destaca por su capacidad para proporcionar una mayor resistencia a la abrasión y a los productos químicos en comparación con otros métodos de recubrimiento. Esto es particularmente beneficioso en aplicaciones donde los tornillos estarán en contacto con sustancias corrosivas o ambientes extremadamente abrasivos. La capa de polvo actúa como una barrera protectora que alarga la vida útil de los tornillos, reduciendo la necesidad de reemplazos y mantenimiento frecuente.
Las máquinas de recubrimiento en polvo requieren un mantenimiento regular para asegurar su buen funcionamiento. Esto incluye la limpieza de los sistemas de aplicación de polvo, la inspección de los hornos de curado y la verificación de los componentes mecánicos y eléctricos. Un mantenimiento adecuado asegura que el proceso de recubrimiento se realice de manera eficiente, lo que ayuda a evitar tiempos de inactividad inesperados y a mantener la calidad del producto final.
El futuro del recubrimiento en polvo parece prometedor, con avances tecnológicos que mejorarán aún más la eficiencia y calidad del proceso. La integración de tecnologías emergentes, como la inteligencia artificial y el Internet de las Cosas (IoT), permitirá optimizar aún más el proceso de recubrimiento, proporcionando un monitoreo en tiempo real y ajustes automáticos para garantizar la mejor calidad y consistencia posible.
En resumen, las máquinas de recubrimiento en polvo para cabezas de tornillos son fundamentales en la producción de piezas de alta calidad que necesitan ser resistentes a condiciones adversas. Su capacidad para mejorar la durabilidad, resistencia y estética de los tornillos, junto con su eficiencia y sostenibilidad, las convierte en una herramienta esencial para diversas industrias.
Máquina de Pintura de Tornillos
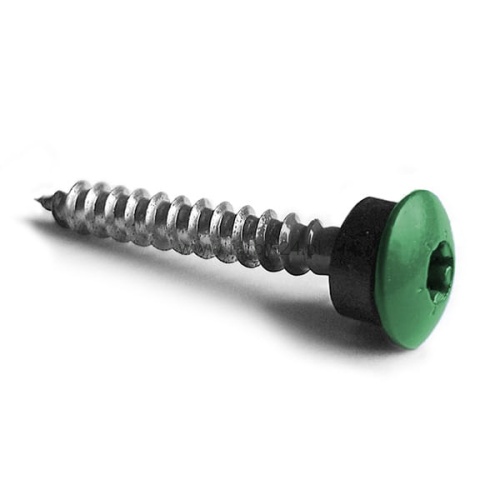
La máquina de pintura de tornillos es un equipo esencial utilizado para aplicar una capa de pintura sobre la superficie de los tornillos, mejorando su aspecto estético y proporcionándoles protección adicional contra factores como la corrosión y el desgaste. Este proceso es clave para garantizar la durabilidad de los tornillos en condiciones ambientales difíciles, como alta humedad, exposición a productos químicos o temperaturas extremas. La pintura también puede ofrecer propiedades adicionales, como resistencia a los rayos UV o protección contra la oxidación, dependiendo del tipo de pintura utilizada.
El proceso de pintura de tornillos generalmente se realiza mediante técnicas como la pulverización, el recubrimiento en baño o la inmersión, cada una de las cuales tiene ventajas específicas según el tipo de tornillo y la cantidad de producción. La pulverización es uno de los métodos más comunes, ya que permite una aplicación uniforme de la pintura sobre los tornillos. Durante este proceso, se utiliza un sistema de compresores y pistolas de pulverización para atomizar la pintura y cubrir la superficie de las piezas de manera eficiente.
Una de las principales ventajas de la pintura aplicada en tornillos es que no solo mejora la apariencia, sino que también aumenta la resistencia de los tornillos a factores ambientales que pueden afectar su funcionalidad. En aplicaciones industriales, especialmente en sectores como la construcción, la automoción o la maquinaria pesada, los tornillos pintados ofrecen una barrera protectora que puede prevenir la corrosión y el desgaste, extendiendo la vida útil de las piezas y reduciendo la necesidad de reemplazo frecuente.
La automatización juega un papel importante en la eficiencia de la máquina de pintura de tornillos. Las máquinas modernas están diseñadas para aplicar la pintura de manera uniforme y consistente en grandes volúmenes de tornillos, lo que las hace ideales para entornos de producción en serie. La automatización permite que el proceso de pintura se realice de forma rápida y con mínima intervención manual, lo que aumenta la productividad y reduce el riesgo de errores. Además, los sistemas de control avanzados permiten ajustar parámetros como la velocidad de aplicación, la cantidad de pintura y la temperatura, lo que asegura un recubrimiento de alta calidad.
Otra característica destacada de las máquinas de pintura de tornillos es su capacidad para trabajar con diferentes tipos de pinturas y acabados. Desde pinturas epóxicas y poliéster hasta pinturas en polvo o recubrimientos especiales, estas máquinas pueden adaptarse a las necesidades específicas de protección de cada tornillo. El tipo de pintura utilizado dependerá de las condiciones a las que los tornillos estarán expuestos, como la resistencia a la abrasión, la corrosión o los rayos UV. Además, las máquinas de pintura pueden aplicar la pintura en una variedad de colores y acabados, lo que no solo mejora la funcionalidad del tornillo, sino que también puede ser importante en aplicaciones donde la estética es un factor decisivo.
El proceso de pintura también se caracteriza por su eficiencia en términos de material. La pintura que no se adhiere a la pieza puede ser recuperada y reutilizada, lo que reduce el desperdicio y mejora la sostenibilidad del proceso. Esto no solo es beneficioso desde el punto de vista económico, sino que también contribuye a la reducción del impacto ambiental del proceso de fabricación. Al no utilizar solventes o productos químicos peligrosos, el proceso de pintura también es más seguro para los trabajadores y el medio ambiente.
El mantenimiento de las máquinas de pintura de tornillos es un aspecto fundamental para garantizar su funcionamiento continuo y eficiente. Las máquinas deben someterse a limpieza periódica para evitar la acumulación de pintura, lo que podría afectar la calidad del recubrimiento. Además, los componentes mecánicos y electrónicos deben ser revisados regularmente para asegurar que todo el sistema funcione correctamente. Un buen mantenimiento también ayuda a prolongar la vida útil de la máquina, lo que reduce los costos de reparación y mejora la rentabilidad a largo plazo.
En el futuro, las máquinas de pintura de tornillos seguirán evolucionando con la incorporación de tecnologías más avanzadas. La integración de sistemas de monitoreo en tiempo real y la inteligencia artificial permitirá una mayor precisión en el proceso de pintura, lo que optimizará aún más la calidad y la eficiencia. Además, los avances en los materiales de pintura, como recubrimientos más ecológicos y más resistentes, permitirán mejorar aún más las propiedades de los tornillos pintados.
En resumen, las máquinas de pintura de tornillos son esenciales en la fabricación de tornillos y piezas metálicas de alta calidad, ya que ofrecen tanto beneficios estéticos como funcionales. A través de su capacidad para aplicar recubrimientos protectores que mejoran la durabilidad de los tornillos, así como la eficiencia y precisión en su proceso de automatización, estas máquinas juegan un papel fundamental en diversas industrias. Su versatilidad, junto con la capacidad de adaptarse a diferentes tipos de pintura y acabados, las convierte en una inversión valiosa para mejorar la calidad y sostenibilidad de la producción.
El uso de máquinas de pintura de tornillos es especialmente relevante en industrias que requieren alta resistencia y fiabilidad en sus componentes metálicos. Sectores como la automoción, la construcción, la electrónica y la fabricación de maquinaria pesada dependen de tornillos pintados para garantizar que los productos puedan soportar las condiciones más exigentes. Los recubrimientos aplicados no solo protegen contra factores como la humedad y los productos químicos, sino que también pueden proporcionar una mejor adherencia y cohesión en los ensamblajes, lo que mejora la fiabilidad general de los productos terminados.
En el ámbito automotriz, por ejemplo, los tornillos pintados son esenciales para la construcción de vehículos que deben resistir condiciones climáticas extremas, como la exposición a la sal en carreteras en invierno o el calor intenso. Los recubrimientos proporcionan una capa adicional de protección que aumenta la resistencia a la corrosión, prolongando la vida útil de los tornillos y, por ende, la durabilidad de los vehículos. La pintura también mejora la apariencia estética de los tornillos, lo que es crucial para las partes visibles de los vehículos, como el interior o elementos del motor.
En la fabricación de maquinaria pesada, como equipos agrícolas o maquinaria de construcción, los tornillos pintados también son imprescindibles. Estos equipos suelen operar en condiciones extremas y deben resistir impactos, abrasión y exposición a sustancias químicas agresivas. La pintura aplicada a los tornillos contribuye a mantener su integridad estructural, incluso después de largas exposiciones a estas condiciones, lo que reduce los costos de mantenimiento y mejora la seguridad operativa.
Además de la resistencia a factores ambientales, el recubrimiento de pintura en los tornillos también puede influir en las propiedades de fricción y deslizamiento de las piezas. Dependiendo del tipo de pintura aplicada, se pueden obtener recubrimientos que favorezcan la facilidad de instalación de los tornillos, reduciendo la fricción y facilitando su inserción en otras piezas. Esto es especialmente útil en aplicaciones que requieren ensamblajes rápidos y eficientes, como en la industria de la electrónica, donde la precisión y la rapidez en la fabricación son cruciales.
El desarrollo de nuevos tipos de pintura, como recubrimientos nanoestructurados o pinturas con propiedades autolimpiantes, está abriendo nuevas oportunidades para mejorar las prestaciones de los tornillos pintados. Estos avances permiten la creación de superficies más duraderas y funcionales, capaces de resistir aún mejor las condiciones adversas y de mantener su apariencia durante más tiempo. Los recubrimientos inteligentes, que responden a cambios en el entorno, también podrían ser una opción en el futuro para hacer los tornillos aún más resistentes y adaptables a diferentes aplicaciones.
La tendencia hacia la sostenibilidad también está marcando un cambio en la forma en que se fabrican y pintan los tornillos. Las máquinas de pintura de tornillos están evolucionando para adaptarse a la creciente demanda de procesos más ecológicos. Los recubrimientos a base de agua, los procesos sin solventes y las tecnologías que minimizan el consumo de energía están ganando terreno. Estos avances contribuyen a reducir la huella de carbono de la fabricación de tornillos, lo que es un factor importante para las empresas que buscan cumplir con las normativas ambientales y mejorar su imagen corporativa en un mercado cada vez más consciente de la sostenibilidad.
A medida que la tecnología continúa avanzando, también lo hará la precisión y eficiencia de las máquinas de pintura de tornillos. Los sistemas de automatización, que incorporan inteligencia artificial, ofrecerán un mayor control sobre el proceso de pintura, optimizando variables como la cantidad de pintura, la velocidad de aplicación y la distribución del recubrimiento. Esto no solo mejorará la calidad del producto final, sino que también reducirá el desperdicio de material y mejorará la eficiencia energética, haciendo que el proceso de pintura sea más rentable y sostenible a largo plazo.
En conclusión, las máquinas de pintura de tornillos desempeñan un papel crucial en la producción de piezas metálicas que necesitan ser duraderas, funcionales y estéticamente atractivas. A través de la aplicación de recubrimientos protectores que mejoran la resistencia a la corrosión y otros factores ambientales, estas máquinas contribuyen a aumentar la vida útil de los tornillos, reduciendo los costos de mantenimiento y mejorando la fiabilidad de los productos finales. Su capacidad para adaptarse a diferentes tipos de pintura y acabados, junto con los avances en automatización y sostenibilidad, asegura que las máquinas de pintura de tornillos seguirán siendo una herramienta fundamental en la fabricación industrial en el futuro.
A medida que el mercado y las necesidades industriales continúan evolucionando, las máquinas de pintura de tornillos también están viendo mejoras en cuanto a su flexibilidad y adaptabilidad. Hoy en día, muchas de estas máquinas permiten la personalización en cuanto a los tipos de acabados y recubrimientos. Esto es importante en sectores donde la estética y la diferenciación del producto son cruciales, como en la fabricación de productos electrónicos de consumo o en equipos de diseño industrial.
El avance hacia sistemas más integrados y automatizados también ha mejorado la capacidad de las máquinas de pintura de tornillos para gestionar múltiples fases de producción de manera simultánea. Las máquinas modernas pueden integrar el proceso de pintura con sistemas de control de calidad, como cámaras de inspección y análisis de color, para asegurar que cada tornillo pintado cumpla con las especificaciones exactas requeridas. Este enfoque de “calidad en tiempo real” reduce la posibilidad de defectos y mejora la consistencia de los productos, lo cual es clave para industrias con altas demandas de precisión y fiabilidad.
Las máquinas de pintura también están experimentando avances en la conectividad. La integración con sistemas de gestión de producción a través de IoT (Internet de las Cosas) permite el monitoreo y control remoto de los procesos de pintura. Esto significa que los operadores pueden recibir información en tiempo real sobre el estado de la máquina, el nivel de pintura, el rendimiento y otros parámetros clave. Esta conectividad mejora la eficiencia operativa al permitir que los problemas se detecten y solucionen rápidamente antes de que se conviertan en fallos graves, lo que minimiza el tiempo de inactividad y optimiza los costos de mantenimiento.
Otro avance significativo es el desarrollo de tecnologías de pintura más avanzadas, como recubrimientos de base acuosa que eliminan la necesidad de solventes químicos agresivos. Estas soluciones son más respetuosas con el medio ambiente, lo que reduce los riesgos asociados con la manipulación de sustancias peligrosas y mejora las condiciones de trabajo. Además, el uso de recubrimientos ecológicos ha llevado a la creación de máquinas que no solo pintan de manera más eficiente, sino que también cumplen con las normativas ambientales más estrictas, lo que es una ventaja significativa para las empresas que buscan cumplir con las normativas ecológicas o mejorar su imagen corporativa.
El desarrollo de pinturas con propiedades mejoradas también está impulsando la evolución de las máquinas de pintura de tornillos. Por ejemplo, las pinturas con capacidades antimicrobianas o autolimpiantes están ganando popularidad en entornos donde la higiene y la facilidad de mantenimiento son esenciales. Este tipo de recubrimiento es útil en industrias como la alimentaria, farmacéutica o médica, donde los tornillos y otras piezas metálicas deben resistir la acumulación de bacterias o suciedad, y donde la limpieza constante es necesaria.
En términos de eficiencia energética, las máquinas de pintura de tornillos están mejorando continuamente para reducir el consumo de energía durante el proceso de curado. Las tecnologías de secado más rápidas y los hornos de curado de baja energía permiten que la pintura se adhiera de manera efectiva sin los altos costos energéticos asociados con métodos tradicionales. Esto no solo hace que el proceso sea más económico, sino que también contribuye a la sostenibilidad de la producción.
La versatilidad de las máquinas de pintura de tornillos se extiende a su capacidad para trabajar con tornillos de diversos tamaños y formas. Las máquinas están diseñadas para adaptarse a diferentes tipos de piezas metálicas, lo que las hace útiles para un amplio espectro de industrias. La personalización de los procesos de pintura, como la aplicación de capas más gruesas o el uso de combinaciones de colores, también es un aspecto importante para muchas empresas, que buscan no solo funcionalidad, sino también un valor estético agregado en sus productos.
El avance de las máquinas de pintura de tornillos también está permitiendo una mayor capacidad para manejar grandes volúmenes de producción, lo que es esencial en sectores que requieren una alta demanda de tornillos y otras piezas metálicas. Las líneas de producción completamente automatizadas pueden manejar miles de piezas por hora, garantizando la consistencia y la eficiencia del proceso, al tiempo que reducen la intervención manual.
Por último, el futuro de las máquinas de pintura de tornillos parece centrarse en un continuo refinamiento de los procesos y la mejora de la sostenibilidad. A medida que más industrias adoptan prácticas de fabricación más verdes y responsables, el papel de estas máquinas en la fabricación de tornillos y piezas metálicas será cada vez más crucial. Las innovaciones tecnológicas continuarán mejorando la eficiencia, la calidad y el impacto ambiental de estos procesos, lo que posicionará a las máquinas de pintura de tornillos como una herramienta fundamental en la producción industrial del futuro.
En resumen, las máquinas de pintura de tornillos están evolucionando para adaptarse a las crecientes demandas de sostenibilidad, eficiencia y calidad en la fabricación. Su capacidad para aplicar recubrimientos protectores y estéticos en los tornillos, junto con su automatización avanzada y su flexibilidad para adaptarse a diferentes tipos de pintura, asegura su relevancia en una amplia gama de industrias. Con el tiempo, estas máquinas seguirán siendo clave para mejorar la durabilidad, la funcionalidad y la apariencia de los productos, mientras que al mismo tiempo contribuyen a prácticas de producción más sostenibles y eficientes.
En la actualidad, la industria de la fabricación de tornillos continúa adoptando tecnologías avanzadas y tendencias que impulsan la evolución de las máquinas de pintura. Entre estas tendencias, la personalización y la capacidad de ofrecer acabados más complejos y resistentes son elementos clave. Las máquinas de pintura modernas permiten a los fabricantes elegir entre una variedad de recubrimientos especializados, como recubrimientos resistentes al fuego, a los productos químicos o a la abrasión, lo que proporciona a los tornillos propiedades adicionales que son esenciales para aplicaciones industriales específicas.
Además, la mejora de la tecnología de curado está acelerando la eficiencia de las máquinas de pintura. Los sistemas de curado ultravioletas (UV) y las lámparas de secado rápido están permitiendo que los recubrimientos se curen de manera más rápida y con menos consumo de energía. Este tipo de tecnología es especialmente beneficioso para la producción en serie, ya que reduce el tiempo de espera entre la aplicación de la pintura y el ensamblaje final de los productos, lo que mejora la velocidad general del proceso de fabricación.
La capacidad de las máquinas de pintura de tornillos para adaptarse a las nuevas demandas del mercado también está siendo impulsada por la innovación en la tecnología de monitoreo de procesos. Los sistemas de visión artificial, integrados con las máquinas de pintura, permiten realizar una inspección de calidad en tiempo real, verificando que cada tornillo reciba la cantidad adecuada de pintura y que el recubrimiento sea uniforme. Estos sistemas no solo mejoran la calidad del producto, sino que también permiten detectar fallos de inmediato, lo que ayuda a reducir el desperdicio de material y evita la producción de piezas defectuosas.
El sector de la automoción es un ejemplo claro de cómo las máquinas de pintura de tornillos están evolucionando para satisfacer requisitos cada vez más exigentes. Con la creciente demanda de vehículos eléctricos y de bajo impacto ambiental, la industria está buscando constantemente formas de reducir el peso de los componentes y mejorar la eficiencia energética de sus sistemas. Los tornillos pintados, que ahora incorporan tecnologías más ligeras y resistentes, juegan un papel importante en la mejora del rendimiento general de los vehículos, al mismo tiempo que contribuyen a su estética y durabilidad.
En el campo de la electrónica, donde los tornillos y otras piezas metálicas deben tener una alta resistencia a la corrosión y la oxidación, el recubrimiento de pintura se ha vuelto aún más esencial. Los avances en recubrimientos especializados para la industria electrónica, como aquellos diseñados para soportar temperaturas extremas o ambientes húmedos, están impulsando la necesidad de máquinas de pintura más sofisticadas. Estos recubrimientos no solo protegen las piezas, sino que también pueden mejorar la conductividad térmica y reducir el riesgo de fallos en los circuitos.
A medida que las empresas continúan enfocándose en la sostenibilidad y la reducción de su impacto ambiental, las máquinas de pintura de tornillos también están experimentando una evolución hacia prácticas más ecológicas. El uso de pintura en polvo libre de solventes y la adopción de métodos de recubrimiento sin compuestos orgánicos volátiles (COV) están ganando terreno. Estas innovaciones están ayudando a las empresas a cumplir con regulaciones medioambientales más estrictas, a la vez que contribuyen a la creación de un entorno de trabajo más saludable.
En términos de economía circular, las máquinas de pintura de tornillos también están optimizando los procesos para reducir el desperdicio y permitir el reciclaje de materiales. Las técnicas de aplicación de pintura más precisas y eficientes permiten recuperar el polvo o la pintura sobrante, lo que contribuye a la reducción de costos operativos y a la reutilización de los materiales. Este enfoque sostenible es cada vez más importante para las empresas que buscan cumplir con sus objetivos ambientales y mejorar la eficiencia de sus operaciones.
La digitalización es otra tendencia clave que está transformando las máquinas de pintura de tornillos. Las plataformas de gestión digital y las interfaces de usuario inteligentes permiten a los operadores y técnicos tener acceso a información detallada sobre el estado de la máquina, los parámetros del proceso y los niveles de inventario de pintura en tiempo real. Esta conectividad mejora la toma de decisiones, optimiza la programación de las tareas y permite una mayor previsibilidad en la gestión de la producción.
El futuro de las máquinas de pintura de tornillos está marcado por la integración de la inteligencia artificial (IA) y el aprendizaje automático. Estos avances permitirán a las máquinas aprender y adaptarse a los cambios en los procesos de pintura, ajustando automáticamente los parámetros para optimizar el uso de materiales, minimizar los defectos y mejorar la calidad del recubrimiento. La IA también ayudará a anticipar y prevenir fallos, lo que permitirá una producción más eficiente y menos propensa a errores.
En resumen, las máquinas de pintura de tornillos están evolucionando para convertirse en equipos aún más sofisticados, eficientes, sostenibles y flexibles. Con avances en automatización, monitoreo en tiempo real, eficiencia energética, y adaptabilidad a las necesidades del mercado, estas máquinas siguen siendo fundamentales para la producción de piezas metálicas de alta calidad. Al integrar tecnologías avanzadas, como la IA, la conectividad digital y los recubrimientos especializados, las máquinas de pintura están mejorando continuamente la funcionalidad, la estética y la durabilidad de los tornillos, lo que las convierte en una pieza clave de la industria moderna.

A medida que las máquinas de pintura de tornillos siguen evolucionando, también lo hacen las expectativas de los usuarios finales en cuanto a los estándares de calidad, sostenibilidad y costos operativos. Las empresas que fabrican tornillos y otros componentes metálicos están cada vez más conscientes de la importancia de contar con soluciones de pintura que no solo mejoren el rendimiento de sus productos, sino que también les ayuden a alcanzar sus objetivos medioambientales y económicos.
La eficiencia en el uso de recursos es uno de los principales impulsores de innovación en este campo. Las máquinas de pintura de tornillos modernas están diseñadas para optimizar el consumo de pintura y reducir al máximo el desperdicio de materiales. Esto no solo implica la recuperación de pintura sobrante, sino también la mejora de los procesos de aplicación para que la cantidad de pintura utilizada se distribuya de manera más eficiente sobre la superficie de los tornillos. Este enfoque no solo reduce los costos, sino que también tiene un impacto directo en la sostenibilidad de los procesos de fabricación, ya que disminuye la cantidad de desechos generados y mejora la huella de carbono de las operaciones.
Además, la integración de tecnologías de última generación, como los sistemas de control por visión artificial, permite a las máquinas de pintura de tornillos realizar inspecciones y ajustes en tiempo real. Estos sistemas son capaces de identificar fallos de calidad, como áreas mal cubiertas o defectos en el recubrimiento, y ajustar automáticamente los parámetros de la máquina para corregir el problema antes de que afecte a toda la producción. Esto no solo mejora la consistencia y la calidad del recubrimiento, sino que también aumenta la eficiencia del proceso al reducir el tiempo que se dedica a la inspección manual y la corrección de errores.
Otra tendencia importante es la creciente adopción de tecnologías de secado y curado más rápidas y eficientes. Los métodos tradicionales de secado requieren grandes cantidades de energía y tiempo, lo que puede ser costoso y menos sostenible. En respuesta a esto, los avances en la tecnología de secado, como el uso de hornos de curado de bajo consumo energético y la implementación de secado por infrarrojos o UV, están ayudando a reducir el impacto ambiental y a acelerar el proceso de producción. Estas soluciones permiten que los tornillos pintados se curen más rápido sin comprometer la calidad del recubrimiento, lo que mejora la productividad global.
La capacidad de las máquinas de pintura de tornillos para adaptarse a diferentes tamaños y tipos de piezas también está mejorando. En un mercado que exige mayor personalización, la flexibilidad de las máquinas para manejar una variedad de tamaños de tornillos, desde los más pequeños hasta los más grandes, es un factor clave para las empresas que desean mantenerse competitivas. Las máquinas ahora pueden ajustar fácilmente sus configuraciones para trabajar con diferentes tipos de tornillos, sin la necesidad de configuraciones complicadas o largos períodos de inactividad entre lotes. Esto no solo aumenta la eficiencia, sino que también permite una mayor personalización del recubrimiento, adaptando la pintura a las necesidades específicas de cada cliente.
En cuanto a la automatización y el control, las máquinas de pintura de tornillos están cada vez más conectadas a sistemas de gestión de la producción y bases de datos de mantenimiento predictivo. Esto permite a las empresas recopilar datos detallados sobre cada ciclo de producción y el rendimiento de las máquinas, lo que ayuda a anticipar problemas antes de que ocurran. Con el uso de tecnologías como el Internet de las Cosas (IoT) y la inteligencia artificial (IA), las máquinas pueden comunicarse entre sí y con los sistemas de control centralizado para optimizar los procesos de manera continua, ajustando parámetros de pintura, velocidad y temperatura para maximizar la eficiencia y la calidad.
La evolución de las máquinas de pintura de tornillos también se está impulsando por la necesidad de cumplir con estándares y regulaciones cada vez más estrictos en diversas industrias. La industria automotriz, por ejemplo, requiere recubrimientos que no solo ofrezcan protección contra la corrosión, sino también que sean resistentes a los productos químicos y a las condiciones climáticas extremas. Los fabricantes de maquinaria pesada necesitan recubrimientos que puedan soportar el desgaste y la abrasión, mientras que la industria electrónica exige un nivel más alto de precisión y calidad en los acabados para garantizar la fiabilidad de sus productos. Las máquinas de pintura de tornillos están diseñadas para cumplir con estos rigurosos requisitos, adaptándose a cada aplicación y asegurando que los tornillos y las piezas metálicas tengan el rendimiento adecuado para cada entorno.
Otro aspecto que impulsa la evolución de estas máquinas es la creciente demanda de soluciones de producción más rápidas y de bajo costo. Las máquinas de pintura de tornillos están siendo diseñadas para ser más rápidas y eficientes, sin sacrificar la calidad del recubrimiento. Las mejoras en la velocidad de aplicación de la pintura, la reducción de los tiempos de curado y la capacidad de realizar procesos de recubrimiento en líneas de producción de alta velocidad han permitido a los fabricantes cumplir con los crecientes plazos de entrega y las expectativas de los clientes. La mejora continua de la eficiencia operativa también ayuda a reducir los costos asociados con el mantenimiento y la operación de las máquinas.
Finalmente, la sostenibilidad y la conciencia ambiental son factores clave en el desarrollo de las máquinas de pintura de tornillos. A medida que las regulaciones medioambientales se vuelven más estrictas, las máquinas de pintura están adoptando tecnologías más ecológicas. Esto incluye el uso de recubrimientos sin solventes, la optimización del consumo de energía, y el reciclaje de pintura y materiales sobrantes. Las máquinas están diseñadas para reducir al mínimo el impacto ambiental, lo que no solo contribuye al cumplimiento de normativas, sino que también ofrece ventajas competitivas a las empresas que buscan una producción más responsable.
En resumen, las máquinas de pintura de tornillos están experimentando una evolución constante que mejora tanto la calidad del recubrimiento como la eficiencia del proceso de fabricación. Con avances en automatización, sostenibilidad y control de calidad, estas máquinas continúan desempeñando un papel esencial en la producción de componentes metálicos de alta durabilidad y funcionalidad. Su capacidad para adaptarse a las necesidades de diversas industrias, mejorar la eficiencia energética y reducir los costos operativos asegura que seguirán siendo una parte integral de la fabricación industrial en el futuro.
El futuro de las máquinas de pintura de tornillos se perfila aún más centrado en la integración de tecnologías disruptivas, la automatización avanzada y la sostenibilidad, con un enfoque en aumentar la eficiencia, reducir los costos y mejorar la calidad del producto. A medida que las industrias continúan adoptando modelos de producción más ágiles y sostenibles, la demanda por máquinas más inteligentes, flexibles y ecológicas continuará creciendo.
Uno de los principales desarrollos en curso es la expansión de la inteligencia artificial (IA) y el aprendizaje automático en los procesos de pintura. Las máquinas de pintura de tornillos están empezando a incorporar capacidades de autoajuste y adaptación, lo que les permite modificar parámetros en tiempo real según las condiciones cambiantes del proceso. Este tipo de automatización avanzada mejora la consistencia del recubrimiento, reduce el margen de error humano y optimiza la utilización de materiales. Por ejemplo, mediante el uso de IA, las máquinas pueden analizar datos sobre el grosor del recubrimiento, la adherencia y la distribución de la pintura, ajustando la aplicación para mantener un nivel constante de calidad, incluso en condiciones de producción variables.
El uso de análisis predictivo también se está convirtiendo en una tendencia importante. Las máquinas de pintura de tornillos equipadas con sensores avanzados pueden detectar y predecir problemas antes de que ocurran, como obstrucciones en los sistemas de pintura o fallos en los componentes mecánicos. A través de un sistema de mantenimiento predictivo, es posible realizar intervenciones preventivas, evitando costosos tiempos de inactividad y asegurando que las máquinas sigan operando con la máxima eficiencia. Este enfoque reduce el costo total de propiedad y mejora la productividad a largo plazo.
La mejora en los sistemas de conectividad también es clave para la evolución de estas máquinas. La conectividad en tiempo real permite que los operadores y gerentes de producción supervisen y ajusten el proceso de pintura desde cualquier lugar, mejorando la flexibilidad y la capacidad de respuesta ante problemas inesperados. Además, la integración con sistemas de gestión de la producción (MES, por sus siglas en inglés) permite coordinar las máquinas de pintura con otras fases de la cadena de montaje, optimizando los tiempos de producción y asegurando una mayor sincronización de la fabricación.
En términos de sostenibilidad, la reducción del impacto ambiental de las máquinas de pintura de tornillos sigue siendo una prioridad. Las regulaciones ambientales globales se están volviendo cada vez más estrictas, lo que impulsa la demanda de soluciones más ecológicas en el proceso de pintura. Las máquinas de pintura están adoptando tecnologías de aplicación más eficientes, como la electrostática, que minimizan el desperdicio de pintura y maximizan la cobertura, reduciendo la cantidad de material necesario. Además, los avances en los recubrimientos de base acuosa, que son menos dañinos para el medio ambiente que los recubrimientos a base de solventes, se están integrando más comúnmente en el proceso de pintura. Estas soluciones no solo cumplen con las normativas, sino que también mejoran la salud y seguridad de los trabajadores al reducir la exposición a compuestos tóxicos.
El reciclaje de materiales, tanto de pintura sobrante como de otros componentes, se está convirtiendo en una parte integral de la producción. Las máquinas de pintura más modernas están diseñadas para permitir la recuperación de la pintura excedente, lo que no solo reduce los costos de producción, sino que también minimiza el desperdicio y mejora la sostenibilidad. Estos sistemas de reciclaje se combinan con técnicas de gestión eficiente de residuos que permiten a las empresas cumplir con las regulaciones ambientales sin sacrificar la eficiencia o la rentabilidad.
Otro aspecto que está evolucionando es la personalización de los recubrimientos. Los clientes están cada vez más interesados en tornillos y componentes pintados que no solo ofrezcan resistencia y funcionalidad, sino también una apariencia específica, adaptada a sus necesidades o requisitos estéticos. Las máquinas de pintura de tornillos están respondiendo a esta demanda mediante la integración de procesos de personalización de alta precisión, lo que permite la creación de recubrimientos con diferentes acabados, colores o texturas. Este tipo de flexibilidad es especialmente importante en sectores como la automoción y la electrónica, donde la estética y la funcionalidad a menudo deben ir de la mano.
Además, las máquinas de pintura de tornillos están facilitando la creación de recubrimientos con propiedades funcionales avanzadas. Por ejemplo, se están desarrollando recubrimientos que pueden mejorar la conductividad eléctrica, ofrecer propiedades antimicrobianas o ser resistentes a condiciones extremas, como las altas temperaturas o la exposición a productos químicos. Estos recubrimientos especializados están aumentando la versatilidad de los tornillos pintados, ampliando sus aplicaciones a áreas como la electrónica avanzada, la fabricación de equipos médicos, la aeronáutica y la industria de la energía.
El diseño modular también está ganando popularidad entre las máquinas de pintura de tornillos, permitiendo que las empresas personalicen sus líneas de producción según las necesidades específicas. Las configuraciones modulares hacen que las máquinas sean más flexibles, capaces de adaptarse rápidamente a cambios en la demanda o en los requisitos de producción. Esto no solo mejora la eficiencia operativa, sino que también permite a los fabricantes modificar y actualizar sus equipos de pintura sin tener que reemplazarlos por completo, lo que resulta en una inversión más rentable a largo plazo.
Por último, el futuro de las máquinas de pintura de tornillos se encuentra también marcado por la adopción de tecnologías emergentes, como la realidad aumentada (RA) y la realidad virtual (RV). Estas tecnologías pueden ayudar a los operadores a monitorear y controlar el proceso de pintura a través de interfaces más intuitivas, mejorando la capacitación y reduciendo los errores operativos. En el caso de la RA, los operadores pueden recibir información en tiempo real sobre las condiciones del proceso de pintura o sobre el estado de la máquina, lo que les permite tomar decisiones más informadas y mejorar la productividad.
En conclusión, las máquinas de pintura de tornillos están en una fase de constante innovación, adaptándose a las nuevas demandas de calidad, sostenibilidad, personalización y eficiencia operativa. Con el avance de la automatización, la inteligencia artificial, las soluciones ecológicas y la conectividad, estas máquinas seguirán desempeñando un papel crucial en la industria manufacturera, mejorando la producción de tornillos y componentes metálicos en términos de durabilidad, funcionalidad y apariencia. El futuro de las máquinas de pintura de tornillos está claramente dirigido a procesos más inteligentes, sostenibles y personalizados, lo que les permitirá seguir siendo una herramienta esencial en la fabricación industrial moderna.
Máquina Automática de Pintura de Tornillo Autoperforante
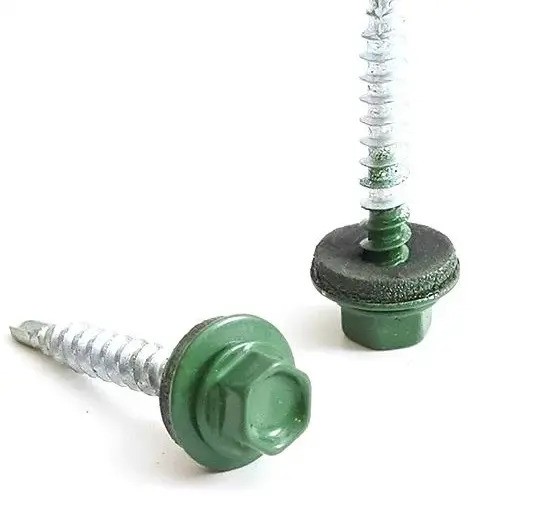
Las máquinas automáticas de pintura de tornillos autoperforantes están diseñadas para optimizar el proceso de recubrimiento de tornillos especializados que tienen la capacidad de perforar y fijarse en materiales sin necesidad de preperforación. Este tipo de tornillos, utilizado en aplicaciones que van desde la construcción hasta la industria automotriz y electrónica, requiere una pintura que no solo ofrezca protección contra la corrosión y desgaste, sino que también preserve la calidad y funcionalidad del tornillo durante su uso. Las máquinas automáticas de pintura están evolucionando para satisfacer estas demandas, integrando tecnologías avanzadas que mejoran la precisión, la eficiencia y la sostenibilidad del proceso de recubrimiento.
En primer lugar, las máquinas automáticas de pintura de tornillos autoperforantes están optimizando la aplicación del recubrimiento, garantizando una distribución uniforme de la pintura en todas las superficies del tornillo, incluidas las zonas difíciles de alcanzar como las roscas. Gracias a la automatización del proceso, estas máquinas pueden manejar grandes volúmenes de tornillos de manera constante, manteniendo una calidad uniforme en cada ciclo de producción. Esto es particularmente importante para los tornillos autoperforantes, que a menudo deben mantener propiedades específicas, como una alta resistencia al desgaste y a la corrosión, sin comprometer la funcionalidad de la rosca.
Las tecnologías avanzadas de aplicación, como la electrostática, son comunes en las máquinas de pintura automática de tornillos autoperforantes. Este método optimiza el uso de la pintura al cargar electrostáticamente las partículas de recubrimiento, lo que asegura que se adhieran de manera eficiente al tornillo. La pintura electrostática permite un acabado uniforme y una mayor adherencia, lo que es fundamental para mantener las propiedades del tornillo autoperforante a lo largo del tiempo. Además, este método reduce significativamente el desperdicio de pintura, contribuyendo a un proceso más sostenible y económico.
Una de las características destacadas de las máquinas automáticas de pintura de tornillos autoperforantes es su capacidad de adaptarse a diferentes tamaños y formas de tornillos sin la necesidad de ajustes complejos. Gracias a los sistemas modulares y de control digital, estas máquinas pueden manejar tornillos de diferentes longitudes, diámetros y configuraciones de cabeza, lo que las hace versátiles y capaces de ajustarse a las necesidades de diversos sectores. La personalización es un aspecto clave, ya que la capacidad de cambiar rápidamente entre diferentes configuraciones de tornillos permite a los fabricantes mantener la eficiencia sin sacrificar la calidad.
El proceso de secado y curado de la pintura aplicada es otro elemento esencial en el funcionamiento de estas máquinas. Los métodos tradicionales de curado, como los hornos de secado por convección o por infrarrojos, están siendo reemplazados por tecnologías de curado más rápidas y energéticamente eficientes. Las máquinas de pintura más modernas emplean técnicas de curado UV (ultravioleta) y LED, que permiten que los recubrimientos se endurezcan en cuestión de segundos. Estas tecnologías no solo aceleran el tiempo de producción, sino que también reducen el consumo de energía y mejoran la sostenibilidad del proceso.
Además de la eficiencia y la personalización, la calidad del recubrimiento es un aspecto fundamental en las máquinas de pintura automática para tornillos autoperforantes. Las máquinas de pintura más avanzadas incorporan sistemas de monitoreo en tiempo real que permiten a los operadores verificar la calidad del recubrimiento mientras se está aplicando. Mediante el uso de sensores y visión artificial, estas máquinas pueden detectar irregularidades, como la falta de pintura o la distribución desigual, y ajustar automáticamente los parámetros de aplicación para garantizar que todos los tornillos cumplan con los estándares de calidad requeridos. Esto reduce la probabilidad de errores y mejora la consistencia del producto final.
La sostenibilidad es un factor clave en la evolución de las máquinas automáticas de pintura de tornillos autoperforantes. Con las crecientes regulaciones medioambientales y la creciente demanda de procesos de producción más responsables, las máquinas están adoptando tecnologías ecológicas, como el uso de pinturas sin compuestos orgánicos volátiles (COV) y sistemas de recuperación de pintura. Los sistemas de recuperación permiten que el exceso de pintura se recoja y se reutilice, reduciendo el desperdicio y mejorando la eficiencia del proceso. Esta característica no solo ayuda a reducir los costos operativos, sino que también facilita el cumplimiento de las normativas medioambientales más estrictas.
La automatización avanzada en estas máquinas también contribuye a la reducción de costos operativos. Con la implementación de control numérico computarizado (CNC) y sistemas de monitoreo remoto, los fabricantes pueden optimizar el tiempo de producción y minimizar los errores humanos. La capacidad de ajustar automáticamente los parámetros del proceso y monitorear el desempeño de las máquinas a través de plataformas digitales permite una gestión más eficiente de la producción, lo que mejora tanto la productividad como la rentabilidad.
Otro aspecto importante es la capacidad de personalización del recubrimiento en términos de propiedades funcionales. Las máquinas automáticas de pintura están cada vez más equipadas para aplicar recubrimientos especializados que ofrecen ventajas adicionales, como resistencia a temperaturas extremas, propiedades antibacterianas o conductividad eléctrica. Estos recubrimientos personalizados son particularmente útiles en aplicaciones específicas, como la industria automotriz, donde los tornillos autoperforantes deben soportar condiciones de trabajo rigurosas, o en la industria electrónica, donde se requieren propiedades de aislamiento o conductividad.
La conectividad también es una tendencia creciente en el diseño de máquinas automáticas de pintura de tornillos autoperforantes. Con el uso de tecnologías como el Internet de las Cosas (IoT), las máquinas pueden conectarse a sistemas de gestión de la producción, permitiendo una supervisión y control centralizados. Esto facilita la integración de las máquinas en líneas de producción automatizadas, lo que mejora la eficiencia global del sistema. Además, los operadores pueden acceder a datos en tiempo real sobre el estado de la máquina, los niveles de inventario de pintura y el rendimiento del proceso, lo que permite una toma de decisiones más informada y rápida.
El diseño modular de las máquinas también permite una mayor flexibilidad, lo que facilita la adaptación a las cambiantes necesidades del mercado. Las empresas que fabrican tornillos autoperforantes pueden ajustar rápidamente su línea de producción para adaptarse a nuevas configuraciones de tornillos o cambios en los requisitos de recubrimiento sin incurrir en costos significativos de reconfiguración o tiempos de inactividad.
En resumen, las máquinas automáticas de pintura de tornillos autoperforantes están en una etapa avanzada de desarrollo, con un enfoque en mejorar la eficiencia, la sostenibilidad y la calidad del proceso de recubrimiento. Gracias a la automatización, la personalización, el uso de tecnologías de curado rápido y la integración de sistemas de monitoreo en tiempo real, estas máquinas son capaces de producir tornillos de alta calidad de manera más eficiente, con menos desperdicio y un menor impacto ambiental. Además, la flexibilidad y la conectividad permiten una mayor adaptabilidad a las necesidades cambiantes de la industria, lo que asegura que las máquinas de pintura de tornillos autoperforantes seguirán siendo una parte esencial de la fabricación moderna en diversas aplicaciones industriales.
La innovación continua en el diseño y la funcionalidad de las máquinas automáticas de pintura de tornillos autoperforantes no solo está enfocada en mejorar la eficiencia operativa y la sostenibilidad, sino también en anticipar y adaptarse a las necesidades emergentes de los mercados. A medida que los sectores de la construcción, la automoción, la electrónica y otros industriales evolucionan, las máquinas de pintura de tornillos autoperforantes deben seguir ofreciendo soluciones que no solo cumplan con los estándares de calidad, sino que también optimicen los costos, tiempos de producción y procesos logísticos.
Una tendencia clave que continúa ganando relevancia es la mejora de la personalización de los acabados de pintura para adaptarse a requisitos específicos de cada industria o cliente. Por ejemplo, la demanda de recubrimientos con propiedades adicionales como resistencia a la abrasión, anticorrosión, aislamiento térmico o conductividad eléctrica está en aumento. Para satisfacer estas necesidades, las máquinas automáticas de pintura están equipadas con sistemas avanzados de aplicación de recubrimientos que permiten la mezcla precisa de ingredientes para crear recubrimientos especializados. Esto no solo mejora el rendimiento de los tornillos, sino que también expande sus aplicaciones a áreas más técnicas y complejas, como la fabricación de componentes electrónicos o sistemas de energía renovable.
Además, la adopción de tecnologías como la impresión 3D en la fabricación de recubrimientos ha abierto nuevas posibilidades para la personalización. Algunas máquinas avanzadas están explorando la posibilidad de aplicar patrones o marcas específicas en la superficie de los tornillos para identificar piezas o personalizarlas para aplicaciones específicas. Esto es particularmente útil en industrias como la automotriz o la aeronáutica, donde se requieren altos niveles de trazabilidad y personalización para cada componente. Con esta capacidad, los tornillos autoperforantes pueden ser fácilmente adaptados y mejorados para cumplir con las especificaciones precisas de los clientes, sin necesidad de procesos adicionales o largos plazos de espera.
El monitoreo constante y la optimización del proceso de pintura se han convertido en componentes esenciales de las máquinas de pintura de tornillos autoperforantes. Los sistemas avanzados de control y monitoreo en tiempo real no solo permiten detectar posibles fallos en el proceso de pintura, sino que también recogen datos valiosos sobre cada ciclo de producción. Estos datos pueden incluir información sobre el grosor del recubrimiento, la cantidad de pintura utilizada, la temperatura de secado y la velocidad de producción. Al analizar estos datos, las empresas pueden realizar ajustes inmediatos para mejorar la calidad y eficiencia del proceso, asegurando que cada tornillo pintado cumpla con los estándares establecidos sin necesidad de una intervención manual constante.
En paralelo, las máquinas de pintura de tornillos autoperforantes también están avanzando en términos de reducción de su huella de carbono. A medida que las regulaciones sobre el impacto ambiental de la fabricación se vuelven más estrictas, los fabricantes de estas máquinas se están enfocando en mejorar la eficiencia energética. Esto incluye la optimización del consumo de energía de los sistemas de curado, la implementación de técnicas de secado que no requieran grandes cantidades de energía y la adopción de materiales de pintura más sostenibles. Las máquinas de pintura también están utilizando tecnologías de recubrimiento que generan menos residuos, lo que contribuye a una mayor sostenibilidad del proceso.
La integración de inteligencia artificial (IA) y aprendizaje automático (ML) en las máquinas de pintura de tornillos autoperforantes ha permitido una mayor automatización y personalización del proceso de pintura. Estos sistemas no solo mejoran la precisión y consistencia del recubrimiento, sino que también optimizan la programación de la producción. La inteligencia artificial puede predecir cuándo es necesario realizar un mantenimiento preventivo, reduciendo los tiempos de inactividad y mejorando la confiabilidad de la maquinaria. Además, mediante el análisis de datos históricos y patrones de producción, las máquinas pueden predecir la mejor configuración de parámetros para cada tipo de tornillo o requerimiento de recubrimiento, lo que lleva a una mayor eficiencia operativa.
Las máquinas automáticas de pintura también están facilitando la integración en cadenas de producción más grandes y complejas, gracias a su capacidad para interactuar con otros equipos de fabricación. Por ejemplo, las líneas de ensamblaje automatizadas pueden incluir máquinas de pintura que operan en sincronización con otros procesos, como la perforación, el ensamblaje o el empaquetado, para crear un flujo de trabajo continuo y altamente eficiente. Esta integración no solo mejora la productividad general, sino que también reduce los tiempos de espera y los costos asociados con la manipulación de materiales.
La evolución de la conectividad también está llevando a las máquinas automáticas de pintura de tornillos autoperforantes hacia una mayor centralización y control remoto. Las plataformas de monitoreo y control permiten a los operadores supervisar múltiples máquinas de pintura de manera remota, asegurando una respuesta más rápida ante cualquier eventualidad o ajuste necesario. Esto se traduce en una mayor flexibilidad para gestionar operaciones de gran escala sin sacrificar la calidad del proceso de pintura. Los avances en la conectividad 5G y otras tecnologías de comunicación también están impulsando esta tendencia, permitiendo una supervisión y control más rápidos y eficientes a nivel global.
La investigación y el desarrollo en el campo de las máquinas automáticas de pintura de tornillos autoperforantes también se enfocan en la mejora continua de los sistemas de limpieza y mantenimiento. El mantenimiento de los sistemas de pintura es una parte crítica para asegurar su funcionamiento continuo y eficiente. Las nuevas soluciones incluyen sistemas automáticos de limpieza que eliminan la pintura residual de las boquillas y otros componentes sin la intervención manual, lo que reduce el tiempo de inactividad y mejora la productividad. Además, las máquinas más modernas están diseñadas con componentes más duraderos y de fácil reemplazo, lo que facilita las reparaciones y la reducción de costos operativos.
En cuanto a la capacitación de los operadores, las máquinas automáticas de pintura también están implementando interfaces de usuario más intuitivas y sistemas de diagnóstico avanzados que ayudan a los operadores a comprender mejor el funcionamiento de la máquina y a resolver problemas de manera más eficiente. Estos avances, combinados con simuladores y tecnologías de realidad aumentada (RA), pueden acelerar el proceso de formación, reducir errores operativos y asegurar una mayor consistencia en la calidad de producción.
En resumen, las máquinas automáticas de pintura de tornillos autoperforantes están evolucionando rápidamente para abordar los desafíos de una industria que exige mayor personalización, eficiencia, sostenibilidad y calidad. La automatización avanzada, la conectividad, la inteligencia artificial y las tecnologías ecológicas continúan impulsando la innovación, permitiendo a estas máquinas ofrecer soluciones más rápidas, flexibles y rentables para la fabricación de tornillos autoperforantes. Estas mejoras no solo benefician a los fabricantes, sino que también contribuyen al cumplimiento de los estándares medioambientales y de calidad que exigen las industrias modernas. Con un futuro marcado por la digitalización, la sostenibilidad y la personalización, las máquinas de pintura de tornillos autoperforantes seguirán desempeñando un papel crucial en la producción industrial a medida que las demandas de los mercados evolucionan.
El continuo avance en la tecnología de las máquinas automáticas de pintura de tornillos autoperforantes está abriendo nuevas posibilidades tanto para los fabricantes como para los usuarios finales de estos tornillos. Las máquinas de pintura no solo están mejorando en términos de eficiencia y reducción de costos, sino que también están permitiendo la creación de tornillos con características altamente especializadas que mejoran su desempeño y extendieron su vida útil en condiciones extremas.
Uno de los desarrollos más prometedores en este campo es la capacidad de aplicar recubrimientos funcionales con características avanzadas, como la protección contra los rayos UV, la resistencia al fuego o la capacidad de repeler contaminantes. Estas propiedades no solo agregan valor al producto final, sino que también amplían las aplicaciones de los tornillos autoperforantes, haciéndolos adecuados para sectores donde las condiciones son particularmente exigentes. Por ejemplo, en la construcción de estructuras expuestas a la intemperie, como tejados o fachadas, o en aplicaciones electrónicas, donde las propiedades de aislamiento y resistencia a la corrosión son cruciales.
A medida que las industrias se mueven hacia la digitalización, la máquina de pintura de tornillos autoperforantes se integra cada vez más en la Industria 4.0. Este concepto no solo implica la automatización de los procesos de producción, sino también la integración de las máquinas con sistemas de gestión inteligente que optimizan todo el ciclo de producción, desde el abastecimiento de materiales hasta el control de calidad final. Gracias a las tecnologías de comunicación en la nube y la integración con sistemas ERP (Enterprise Resource Planning) y MES (Manufacturing Execution Systems), las máquinas pueden conectarse a plataformas de gestión que permiten monitorear y controlar el proceso desde cualquier lugar. Este tipo de integración proporciona una visión completa del rendimiento de la maquinaria y del estado de los lotes de producción en tiempo real, lo que facilita la toma de decisiones informadas y mejora la capacidad de respuesta ante imprevistos.
El uso de plataformas basadas en la nube también está transformando la forma en que se gestionan los datos relacionados con el proceso de pintura. Las máquinas automáticas de pintura de tornillos autoperforantes están ahora equipadas con sensores avanzados que recopilan grandes cantidades de datos sobre parámetros críticos, como la temperatura, la velocidad de aplicación, el grosor del recubrimiento y los tiempos de curado. Estos datos se pueden almacenar y analizar de manera centralizada, proporcionando una valiosa retroalimentación que se utiliza para ajustar y mejorar continuamente los procesos de producción. El análisis de estos datos no solo mejora la calidad y la eficiencia del recubrimiento, sino que también permite predecir patrones de desgaste en las máquinas y programar mantenimientos preventivos de manera más precisa.
Otro desarrollo clave es la integración de capacidades de aprendizaje automático (machine learning) en las máquinas automáticas de pintura. A medida que las máquinas recogen más datos sobre las condiciones de operación y los resultados de los recubrimientos, el aprendizaje automático permite que las máquinas ajusten automáticamente los parámetros del proceso para maximizar la eficiencia y la calidad. Este tipo de inteligencia adaptativa es especialmente útil en ambientes de producción dinámicos, donde las condiciones de operación pueden cambiar rápidamente y la capacidad de adaptación en tiempo real es fundamental. El uso de algoritmos de aprendizaje también ayuda a identificar posibles problemas en las fases tempranas, permitiendo que las máquinas tomen decisiones autónomas para corregir los errores antes de que afecten la producción.
La implementación de tecnologías avanzadas no solo está mejorando la capacidad de las máquinas para producir tornillos autoperforantes de alta calidad, sino que también está mejorando la sostenibilidad del proceso. Con la creciente presión por reducir el impacto ambiental de la fabricación, las máquinas de pintura están adoptando prácticas más ecológicas. Esto incluye el uso de sistemas de reciclaje de pintura, la implementación de tecnologías que reducen el uso de solventes y la adopción de recubrimientos de base acuosa. Estos recubrimientos no solo son más respetuosos con el medio ambiente, sino que también ofrecen ventajas adicionales, como una menor emisión de compuestos orgánicos volátiles (COV), que son nocivos tanto para la salud de los trabajadores como para el medio ambiente. Además, el uso de estos recubrimientos puede reducir el riesgo de contaminación del aire, lo que permite a los fabricantes cumplir con las estrictas regulaciones ambientales sin sacrificar la calidad del producto.
En términos de mejora de la eficiencia energética, los avances en las tecnologías de curado también juegan un papel fundamental. Las máquinas automáticas de pintura de tornillos autoperforantes están adoptando métodos de curado más rápidos y eficientes, como el curado por rayos ultravioleta (UV) o por LED. Estos métodos no solo aceleran los tiempos de secado, sino que también consumen menos energía que los hornos tradicionales, lo que contribuye a la reducción del consumo general de energía durante el proceso de pintura. Esta reducción en el consumo de energía no solo reduce los costos operativos, sino que también contribuye a los esfuerzos de sostenibilidad a largo plazo.
La mejora de la calidad del recubrimiento también implica una mayor precisión en la aplicación de la pintura, lo que es esencial para mantener las propiedades funcionales del tornillo autoperforante. Las máquinas automáticas de pintura más avanzadas incorporan sistemas de visión artificial y sensores de alta resolución para monitorear y ajustar la aplicación de pintura en tiempo real. Esto no solo garantiza una distribución uniforme del recubrimiento, sino que también detecta imperfecciones de manera temprana, lo que permite realizar correcciones inmediatas y evita que los tornillos defectuosos lleguen a la etapa final de producción. Los sistemas de visión artificial también pueden realizar inspecciones de calidad automatizadas, mejorando aún más el control de calidad y reduciendo el riesgo de defectos en los productos terminados.
La mejora en la interacción con los operadores es otro aspecto clave en la evolución de las máquinas automáticas de pintura de tornillos autoperforantes. Los paneles de control intuitivos y las interfaces de usuario mejoradas facilitan la operación, permitiendo a los trabajadores gestionar el proceso de pintura con mayor facilidad y menor probabilidad de cometer errores. Además, las nuevas soluciones incluyen capacidades de diagnóstico remoto, lo que permite que los operadores y técnicos realicen ajustes y resuelvan problemas sin tener que estar físicamente presentes en la máquina. Esto no solo mejora la eficiencia operativa, sino que también reduce la necesidad de intervenciones manuales, lo que permite que los procesos sean más rápidos y precisos.
En resumen, las máquinas automáticas de pintura de tornillos autoperforantes están atravesando una transformación significativa, impulsada por avances en automatización, inteligencia artificial, sostenibilidad y conectividad. Estos desarrollos están permitiendo a los fabricantes de tornillos producir piezas de alta calidad de manera más eficiente, sostenible y personalizada. Las máquinas de pintura más modernas no solo están optimizando el proceso de recubrimiento, sino que también están facilitando la integración con sistemas de producción más amplios, lo que permite una mayor flexibilidad y control en la producción. Con el aumento de la demanda de tornillos con propiedades específicas y la presión para reducir el impacto ambiental, las máquinas de pintura de tornillos autoperforantes seguirán desempeñando un papel crucial en la fabricación industrial, mejorando tanto la calidad como la sostenibilidad de los productos.
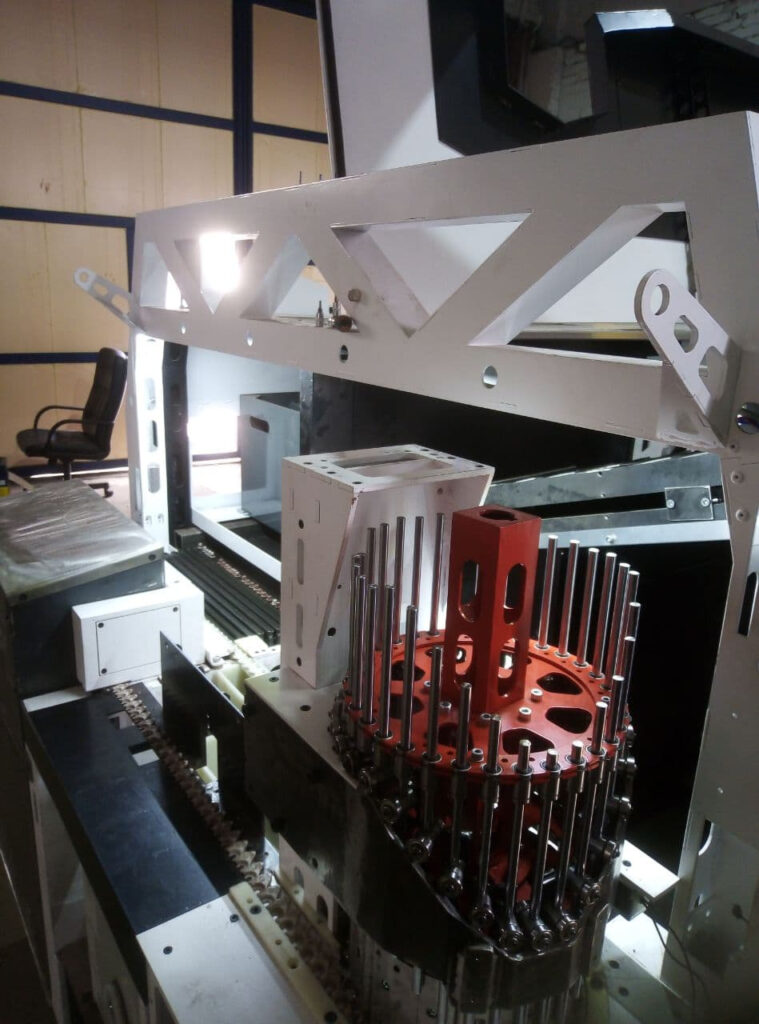
A medida que la industria sigue evolucionando, las máquinas automáticas de pintura de tornillos autoperforantes están entrando en una nueva era donde la digitalización y la automatización inteligente desempeñan un papel cada vez más importante. La capacidad de adaptarse a las exigencias del mercado global y las tendencias tecnológicas emergentes es crucial para garantizar que las máquinas no solo se mantengan competitivas, sino que también ofrezcan un valor significativo a los fabricantes y sus clientes. Estos avances continuarán contribuyendo a una mayor eficiencia, flexibilidad y calidad en la producción de tornillos autoperforantes.
Una de las áreas clave de innovación es la mejora en la adaptabilidad y personalización de las máquinas de pintura. Las soluciones modulares y escalables están permitiendo que los fabricantes ajusten las máquinas a sus necesidades específicas sin comprometer el rendimiento. Esto es especialmente importante en un mercado donde los requisitos de los clientes pueden variar ampliamente. Las máquinas de pintura ahora pueden ser configuradas para manejar diferentes tipos de tornillos autoperforantes, con diversas formas de cabezas, tamaños, longitudes y tipos de recubrimiento, adaptándose a las demandas de sectores como la automoción, la construcción, la electrónica y muchos otros.
El futuro de las máquinas automáticas de pintura también está marcado por el uso de tecnologías emergentes, como el Internet de las Cosas (IoT) y la inteligencia artificial (IA), que se integran más profundamente en el proceso de producción. El IoT permite que las máquinas se conecten y comuniquen entre sí, lo que facilita la creación de sistemas de producción completamente interconectados. Esto no solo permite una mayor automatización, sino que también optimiza los flujos de trabajo y mejora la coordinación entre las distintas etapas de la producción, lo que reduce los tiempos de inactividad y mejora la eficiencia general de la planta de fabricación.
La IA, por su parte, está revolucionando la capacidad de las máquinas para aprender y adaptarse. Las máquinas automáticas de pintura de tornillos autoperforantes equipadas con algoritmos de aprendizaje automático pueden analizar grandes volúmenes de datos generados durante el proceso de producción. Estos algoritmos permiten a las máquinas predecir patrones de falla, optimizar los parámetros de aplicación de pintura, e incluso ajustar automáticamente las configuraciones para maximizar la calidad del recubrimiento. Esto no solo mejora la consistencia del producto final, sino que también reduce los errores humanos y aumenta la vida útil de las máquinas al reducir el desgaste innecesario de los componentes.
Otro aspecto importante en la evolución de las máquinas de pintura es la mayor integración con el control de calidad automatizado. Gracias a los sistemas avanzados de inspección, las máquinas pueden verificar la calidad del recubrimiento durante todo el proceso, desde la aplicación hasta el curado, asegurando que los tornillos autoperforantes cumplan con los estándares más estrictos. Los sistemas de visión artificial y cámaras de alta resolución son capaces de detectar incluso las imperfecciones más pequeñas, como manchas de pintura, áreas sin cubrir o irregularidades en el grosor del recubrimiento. Al identificar estos problemas de manera temprana, las máquinas pueden ajustar los parámetros de forma inmediata o alertar a los operadores para que tomen medidas correctivas, minimizando así el desperdicio y asegurando una mayor precisión en la producción.
La capacidad de adaptarse rápidamente a las necesidades cambiantes de la industria es una ventaja clave para las máquinas automáticas de pintura de tornillos autoperforantes. Las líneas de producción modernas son cada vez más flexibles y requieren que las máquinas sean capaces de realizar cambios rápidos sin necesidad de largos tiempos de inactividad o configuraciones complejas. Las máquinas de pintura están mejorando en cuanto a su capacidad de reconfiguración rápida, permitiendo a los fabricantes realizar ajustes sencillos y rápidos para cambiar de tipo de tornillo, color de pintura o tipo de recubrimiento sin sacrificar la eficiencia.
Además, la posibilidad de monitorear y controlar las máquinas a través de plataformas digitales ha cambiado la forma en que las empresas gestionan sus operaciones. El uso de interfaces basadas en la nube permite a los operadores y gerentes supervisar el estado de las máquinas y el rendimiento de la producción en tiempo real, incluso desde ubicaciones remotas. Esto no solo optimiza la gestión de la producción, sino que también facilita el mantenimiento preventivo y las actualizaciones del sistema, lo que reduce el riesgo de fallos imprevistos y mejora la continuidad del proceso de fabricación.
En términos de sostenibilidad, las máquinas de pintura están adoptando tecnologías que contribuyen a la economía circular y al aprovechamiento de los recursos. La recuperación de pintura y la reducción del uso de materiales nocivos para el medio ambiente son áreas donde las máquinas automáticas están haciendo avances significativos. Los sistemas de recuperación de pintura permiten que el exceso de pintura se recoja y se reutilice en lugar de ser desechado, lo que no solo reduce los costos operativos, sino que también minimiza el impacto ambiental del proceso de pintura. Además, las nuevas tecnologías de recubrimiento, como los recubrimientos sin COV (compuestos orgánicos volátiles) y a base de agua, están ganando popularidad debido a su menor impacto ambiental y su capacidad para cumplir con las regulaciones ambientales más estrictas.
En el ámbito de la sostenibilidad energética, las máquinas están implementando tecnologías que optimizan el consumo de energía durante el proceso de pintura. El uso de tecnologías de curado UV o LED ha demostrado ser una solución eficaz para reducir el consumo de energía, ya que estos métodos de curado requieren menos energía en comparación con los hornos convencionales. Además, estas tecnologías permiten un curado más rápido, lo que mejora el tiempo de ciclo de producción y reduce el tiempo de inactividad de las máquinas, contribuyendo a una mayor eficiencia operativa.
La capacidad de realizar un mantenimiento más eficiente y económico también está mejorando. Las máquinas más modernas están equipadas con sistemas de autodiagnóstico que monitorean continuamente su estado y alertan a los operadores sobre cualquier anomalía que pueda requerir mantenimiento. Esto no solo reduce el tiempo de inactividad inesperado, sino que también permite a los fabricantes realizar mantenimientos preventivos basados en datos precisos, lo que extiende la vida útil de las máquinas y reduce los costos a largo plazo.
En resumen, las máquinas automáticas de pintura de tornillos autoperforantes están experimentando una transformación impulsada por la automatización avanzada, la inteligencia artificial, la conectividad digital y la sostenibilidad. Estas innovaciones no solo están mejorando la eficiencia y la calidad de la producción, sino que también están permitiendo a los fabricantes adaptarse más rápidamente a las demandas cambiantes del mercado. Con la creciente importancia de la personalización, la sostenibilidad y la integración digital, las máquinas de pintura de tornillos autoperforantes seguirán desempeñando un papel fundamental en la evolución de la fabricación industrial, asegurando productos de alta calidad con un menor impacto ambiental y mayores beneficios operativos.
No solo fabricamos nuestros equipos de recubrimiento en polvo, sino que también los enviamos a sus instalaciones con cuidado en todo el mundo.
No somos sólo los fabricantes de su equipo de recubrimiento en polvo, también somos sus socios de entrega en todo el mundo.
En Equipo de recubrimiento en polvo EMS, entendemos que entregarle su equipo de recubrimiento en polvo de manera rápida y segura es tan importante como fabricarlo con los más altos estándares. Es por eso que ofrecemos servicios de entrega en todo el mundo a todos nuestros clientes.
Trabajamos con una red de socios de envío experimentados y confiables para garantizar que su equipo llegue a tiempo y en perfectas condiciones. También ofrecemos una variedad de opciones de envío que se adaptan a su presupuesto y necesidades.
Ya sea que necesite que le envíen su equipo a una dirección local o a un destino internacional, podemos ayudarlo. Trabajaremos con usted para elegir la mejor opción de envío para sus necesidades y para mantenerlo actualizado sobre el estado de su envío en cada paso del camino.
Entonces, cuando elige EMS para su equipo de recubrimiento en polvo, no solo obtiene los mejores productos del mercado, sino que también obtiene la mejor experiencia de entrega posible.
Contáctenos hoy para obtener más información sobre nuestros servicios de entrega en todo el mundo.
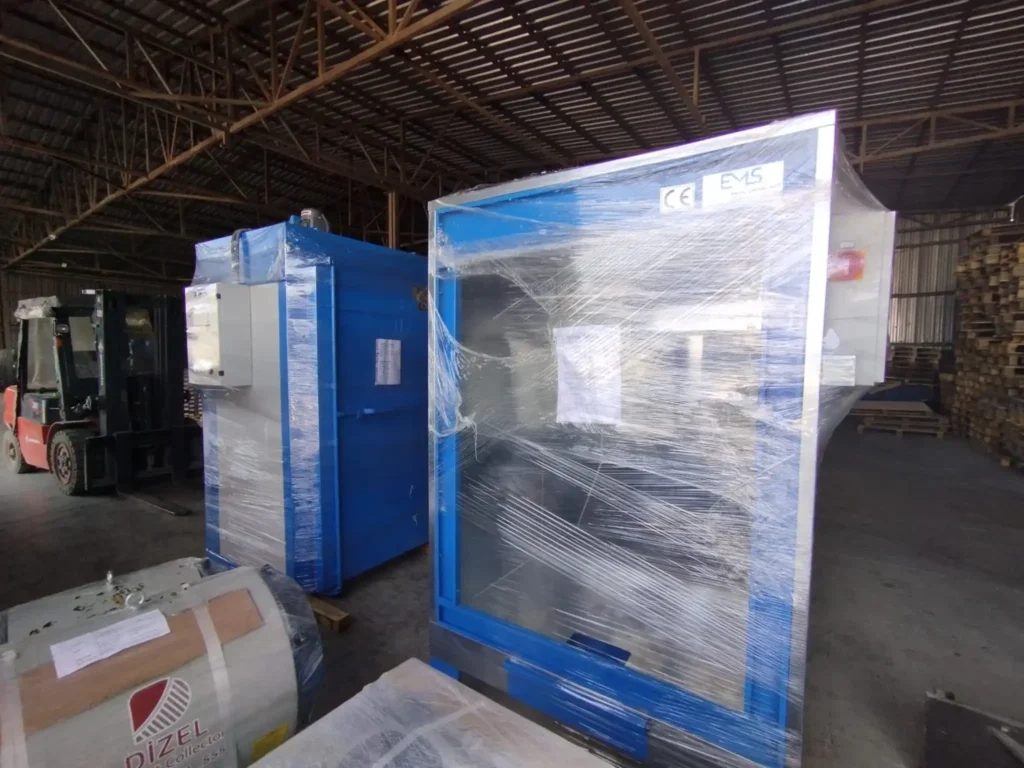
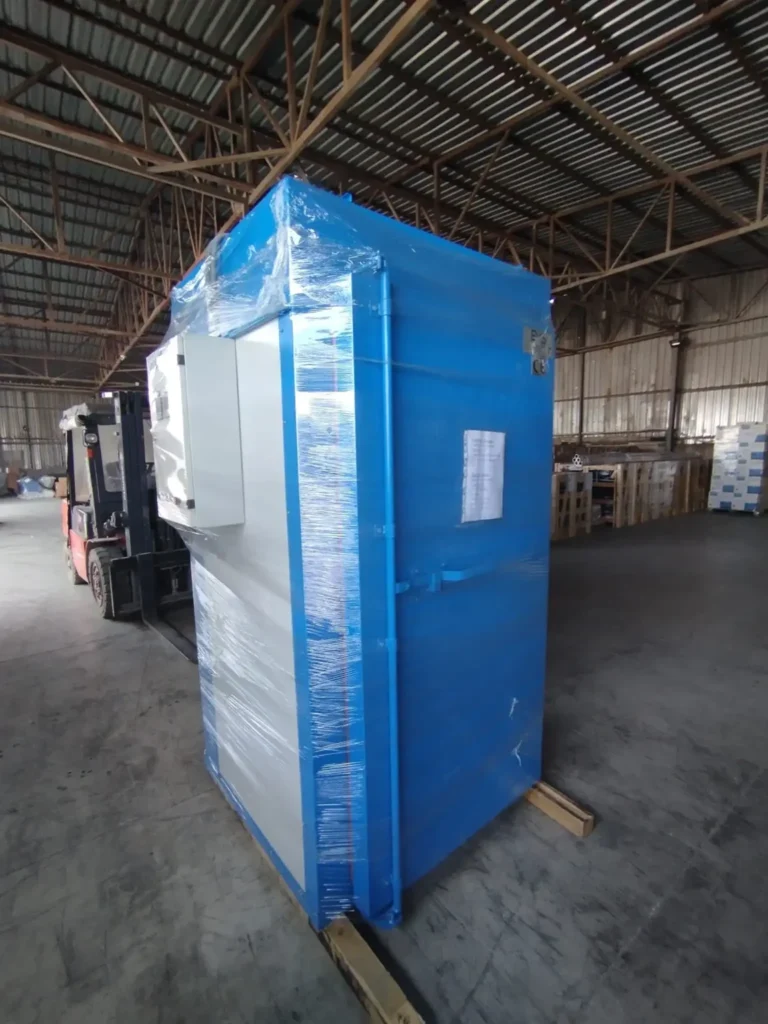
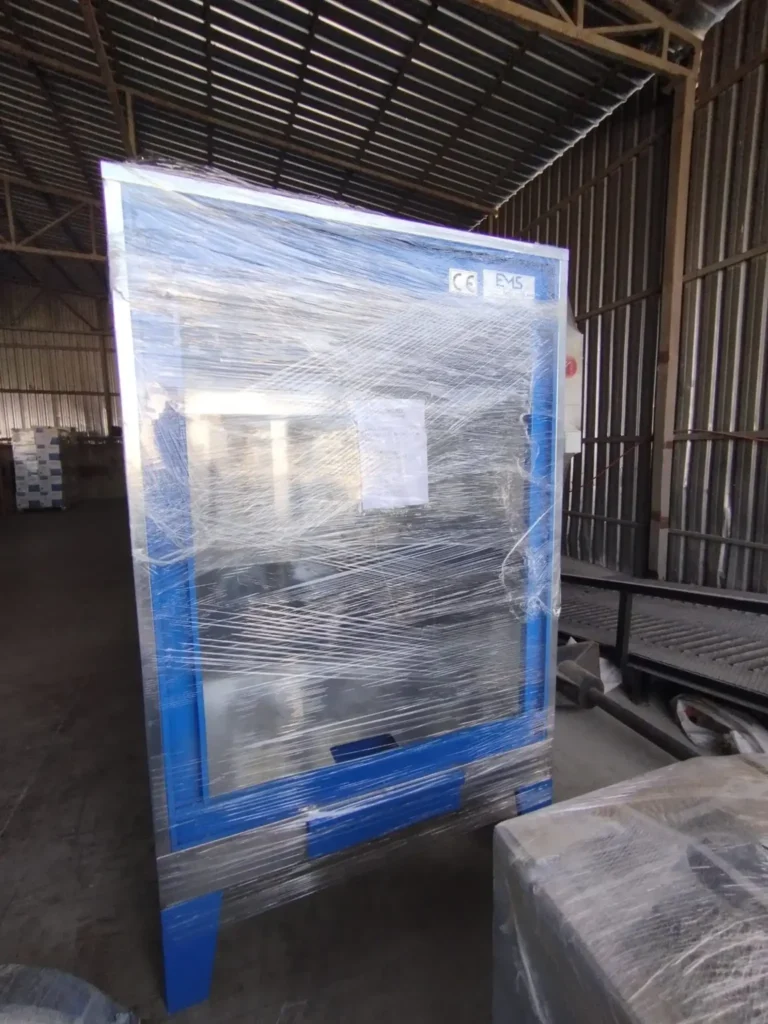
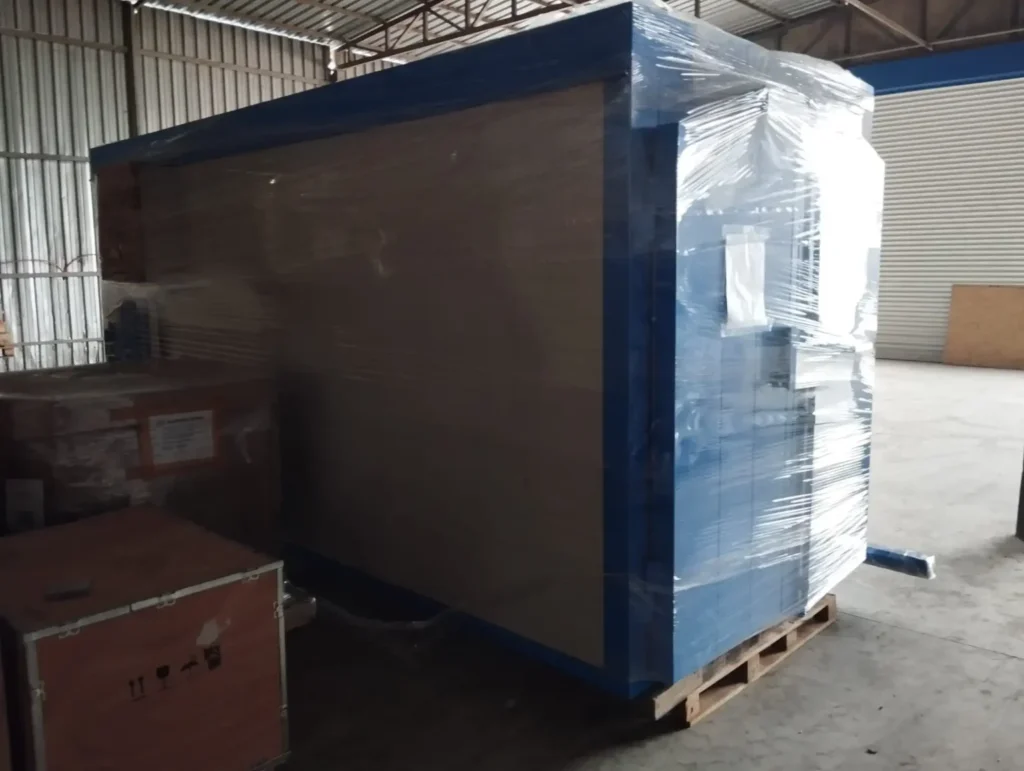