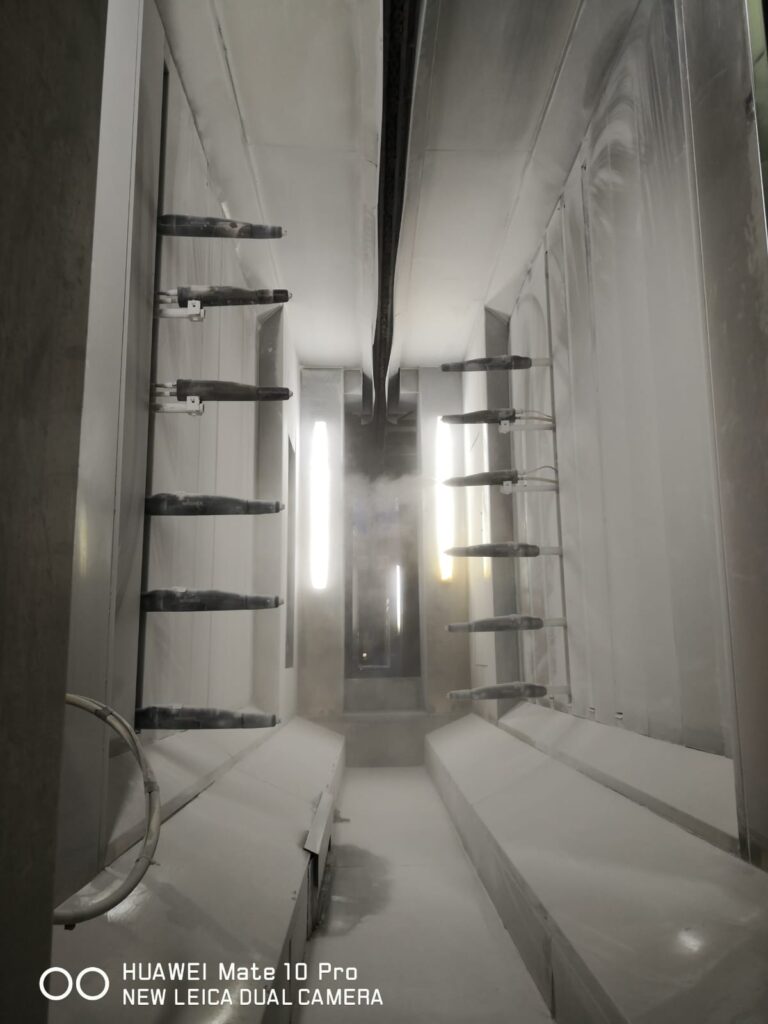
Pistola Automática: La pintura en polvo es una técnica de recubrimiento en seco que se ha convertido en una de las principales opciones en la industria para el acabado de superficies. A diferencia de los métodos tradicionales de pintura líquida, la pintura en polvo no utiliza disolventes ni componentes líquidos. En su lugar, se aplica en forma de un polvo fino que se adhiere electrostáticamente a la superficie de un objeto y se cura mediante calor para formar una capa sólida y duradera.
El desarrollo de la pintura en polvo comenzó en la década de 1950, cuando la necesidad de soluciones más ecológicas y eficientes llevó a los científicos a buscar alternativas a las pinturas líquidas convencionales. Con el tiempo, las técnicas y los materiales utilizados en la pintura en polvo han evolucionado, permitiendo una mayor versatilidad y aplicaciones en una amplia gama de industrias.
Hoy en día, la pintura en polvo se utiliza ampliamente en sectores como la automoción, la fabricación de electrodomésticos, la industria del mueble, y en la producción de componentes metálicos, entre otros. Su capacidad para proporcionar un acabado uniforme, resistente a la corrosión y a los impactos, ha hecho que sea una elección preferida en muchas aplicaciones industriales.
Pistola Automática para Pintura
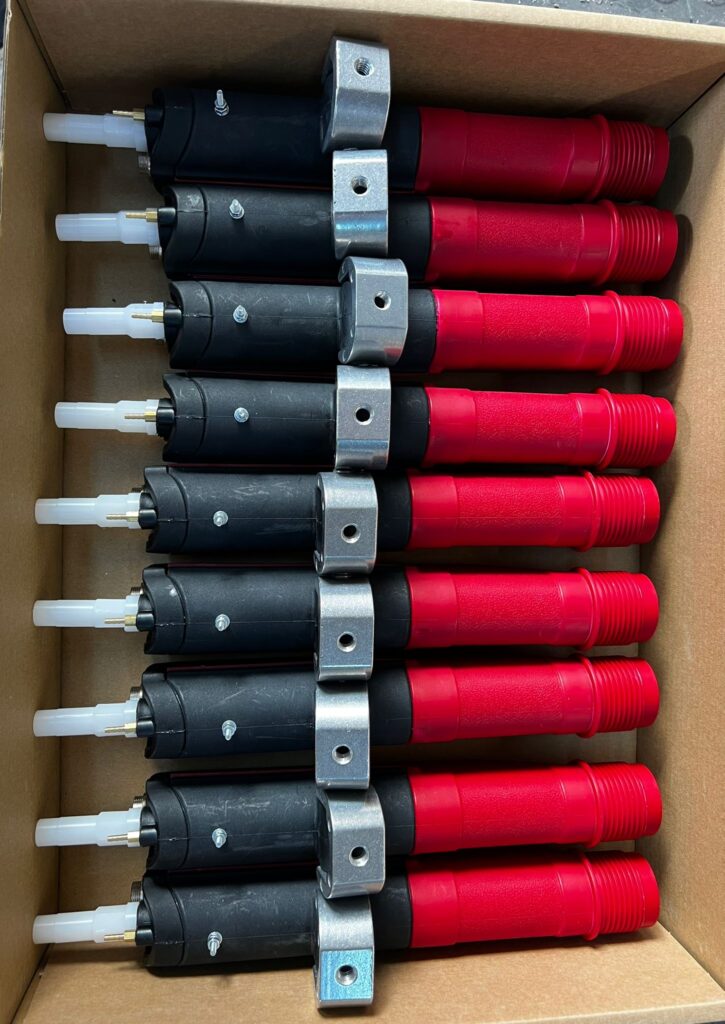
La pintura en polvo ofrece varias ventajas significativas sobre los recubrimientos líquidos tradicionales:
- Eficiencia del Material: Al no utilizar disolventes, casi el 100% del polvo aplicado puede ser recuperado y reutilizado, lo que reduce el desperdicio de material y los costos asociados.
- Calidad del Acabado: La aplicación electrostática asegura una cobertura uniforme incluso en superficies complejas, eliminando problemas comunes como las corridas o el goteo de la pintura líquida.
- Durabilidad: Los recubrimientos en polvo son extremadamente duraderos y ofrecen una excelente resistencia al desgaste, la corrosión, y los productos químicos, lo que prolonga la vida útil de los productos recubiertos.
- Impacto Ambiental: Dado que la pintura en polvo no contiene disolventes, no emite compuestos orgánicos volátiles (COV) durante su aplicación, lo que la convierte en una opción más ecológica en comparación con las pinturas líquidas.
- Seguridad: La ausencia de disolventes también reduce los riesgos de incendio y explosión, haciendo que el proceso sea más seguro tanto para los operarios como para el medio ambiente.
La pintura electrostática ha revolucionado la industria de la pintura industrial debido a su eficiencia, precisión y respeto por el medio ambiente. En el corazón de este proceso, se encuentran los equipos de aplicación de pintura electrostática, los cuales son responsables de la adherencia uniforme de la pintura en polvo sobre las superficies metálicas, lo que garantiza una excelente cobertura y acabado duradero.
Introducción a la Pintura Electrostática
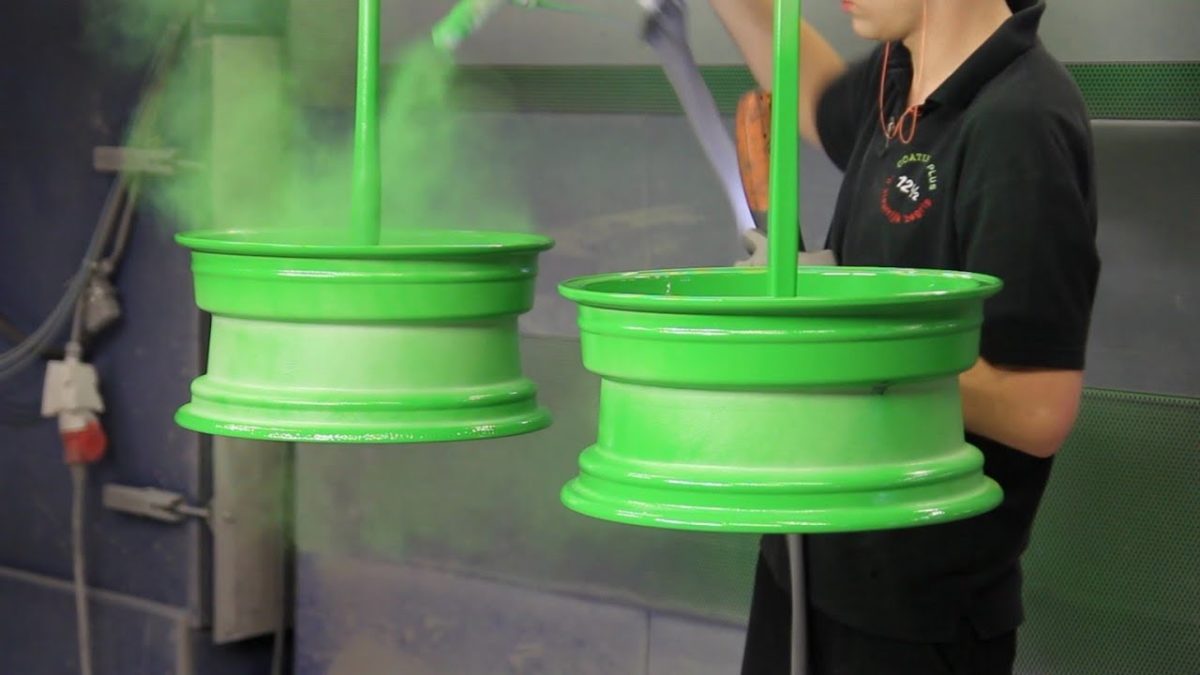
La pintura electrostática es un proceso en el que se aplica pintura en polvo a una superficie cargada eléctricamente. Los equipos de aplicación utilizan una pistola de pulverización que carga eléctricamente las partículas de polvo para que se adhieran a la superficie de manera eficiente y uniforme. Este método reduce el desperdicio de material y asegura que la cobertura sea homogénea incluso en áreas de difícil acceso.
Tipos de Equipos de Aplicación
Existen varios tipos de equipos de aplicación de pintura electrostática que se utilizan según la naturaleza del proyecto y las necesidades de la industria. Los más comunes son las pistolas manuales y automáticas.
- Pistolas Manuales de Pintura Electrostática: Son herramientas versátiles y ampliamente utilizadas en aplicaciones donde la producción es menor o donde se requiere una mayor flexibilidad. Estas pistolas permiten que los operadores ajusten la cantidad de pintura y la presión, lo que resulta útil en trabajos personalizados o en lotes pequeños.
- Pistolas Automáticas de Pintura Electrostática: Son ideales para grandes líneas de producción donde se requiere consistencia y eficiencia. Este tipo de pistola puede ser controlada por sistemas robóticos o recipricadores, lo que reduce significativamente la intervención humana, mejorando la uniformidad y reduciendo el riesgo de errores.
Ventajas de los Equipos de Aplicación de Pintura Electrostática
El uso de equipos de aplicación de pintura electrostática ofrece varias ventajas clave que lo hacen una opción preferida en la industria de recubrimientos:
- Eficiencia en el uso del material: Gracias a la carga electrostática, las partículas de polvo se adhieren mejor a la superficie del objeto, minimizando el desperdicio de material y permitiendo la reutilización del polvo sobrante.
- Calidad del acabado: Los equipos de aplicación garantizan un acabado uniforme sin defectos visibles como burbujas o marcas de pincel. Además, se logra una cobertura completa incluso en áreas difíciles de alcanzar, como esquinas y bordes complejos.
- Respetuoso con el medio ambiente: El proceso de pintura en polvo es significativamente más ecológico en comparación con los métodos tradicionales de pintura líquida. No genera VOCs (compuestos orgánicos volátiles), lo que reduce la contaminación del aire y los riesgos para la salud.
- Durabilidad: La pintura aplicada mediante estos equipos ofrece una capa resistente a la corrosión, abrasión y químicos, lo que extiende la vida útil de los productos recubiertos.
Desventajas y Desafíos
A pesar de sus numerosas ventajas, los equipos de aplicación de pintura electrostática también presentan algunos desafíos. Uno de los principales es el alto costo inicial de los equipos. Las pistolas, los sistemas automáticos y las cabinas requieren una inversión considerable, lo que puede ser prohibitivo para pequeñas empresas.
Otro desafío es la necesidad de un ambiente controlado. Para obtener los mejores resultados, los equipos de aplicación deben operarse en entornos con un control preciso de temperatura y humedad, lo que asegura que el polvo se adhiera de manera uniforme antes del curado. Además, la capacitación del personal es fundamental para manejar estos equipos de manera segura y eficiente, lo que puede implicar costes adicionales de formación y tiempo de adaptación.
Mantenimiento y Cuidado de los Equipos
El mantenimiento adecuado de los equipos de aplicación de pintura electrostática es crucial para garantizar su longevidad y eficiencia. Las pistolas deben limpiarse regularmente para evitar la acumulación de polvo que podría obstruir los conductos y afectar el rendimiento. Además, los sistemas automáticos requieren calibraciones periódicas para asegurarse de que la presión y la carga eléctrica sean correctas, lo que garantiza una aplicación uniforme del polvo.
Aplicaciones Industriales
Los equipos de aplicación de pintura electrostática se utilizan en una amplia gama de industrias, incluidas la automotriz, electrodomésticos, muebles de metal, y estructuras arquitectónicas. En la industria automotriz, por ejemplo, se utilizan para aplicar revestimientos protectores y decorativos a las carrocerías de los vehículos, proporcionando una excelente resistencia a la corrosión y un acabado de alta calidad.
En la fabricación de electrodomésticos, estos equipos se utilizan para recubrir lavadoras, secadoras y refrigeradores, lo que proporciona no solo un acabado estético, sino también una protección contra el desgaste y el óxido.
Tendencias Futuras en la Aplicación de Pintura Electrostática
La industria de la pintura electrostática está en constante evolución, y los avances tecnológicos están mejorando continuamente la eficiencia y precisión de los equipos de aplicación. En el futuro, se espera que los sistemas de aplicación sean cada vez más automatizados, utilizando inteligencia artificial y sensores avanzados para optimizar el proceso de recubrimiento. Además, las nuevas formulaciones de polvo permitirán aplicaciones más ecológicas, mejorando aún más la sostenibilidad del proceso.
Conclusión
Los equipos de aplicación de pintura electrostática son una herramienta fundamental en la industria moderna del recubrimiento. Su capacidad para proporcionar un acabado duradero, eficiente y ecológico los convierte en una elección preferida en una variedad de sectores industriales. A pesar de los desafíos relacionados con su costo inicial y la necesidad de un entorno controlado, las ventajas que ofrecen en términos de calidad y sostenibilidad los hacen indispensables en el futuro de los recubrimientos industriales.
Planta Automática de Pintura en Polvo Industrial
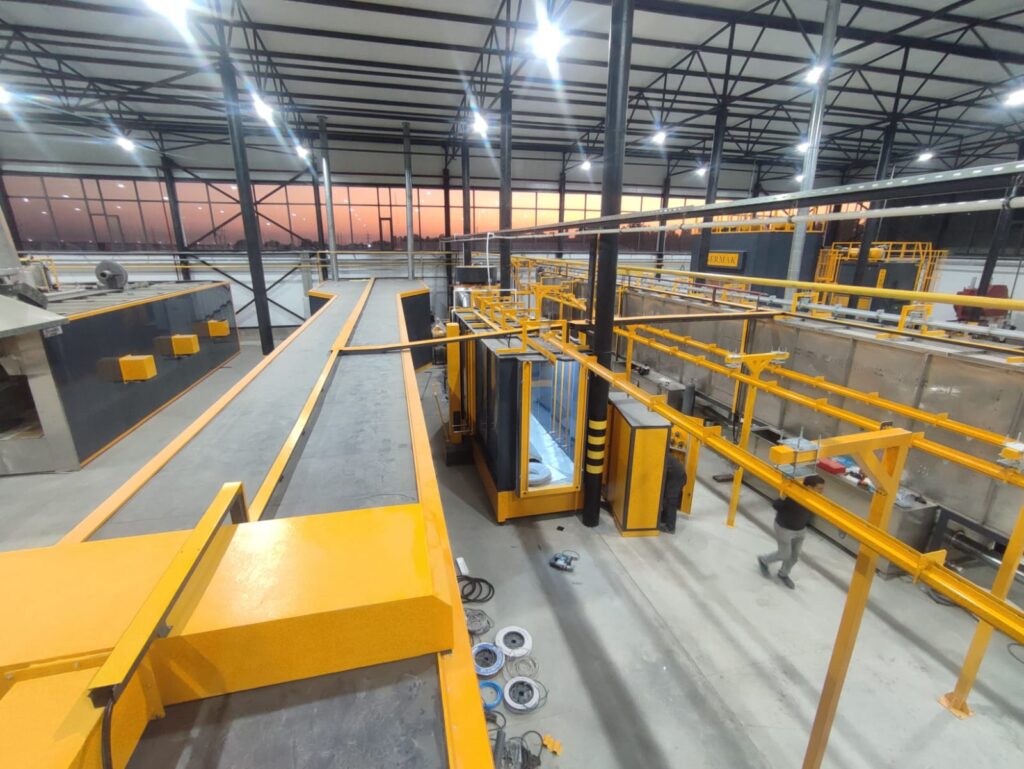
La implementación de una planta automática de pintura en polvo industrial representa un avance crucial en la producción industrial a gran escala. Estas plantas automatizadas están diseñadas para optimizar el proceso de aplicación de pintura en polvo, permitiendo una mayor eficiencia, consistencia y ahorro en recursos, lo que es especialmente útil para empresas que manejan grandes volúmenes de producción y requieren precisión en cada una de las piezas tratadas.
Introducción a las Plantas Automáticas de Pintura en Polvo
Una planta automática de pintura en polvo es un sistema integral compuesto por varios equipos interconectados, incluyendo cabinas de aplicación, pistolas automáticas, transportadores y hornos de curado. Estos sistemas son capaces de funcionar con una mínima intervención humana, lo que no solo incrementa la velocidad de producción, sino que también reduce el margen de error y asegura una aplicación más uniforme y duradera del recubrimiento en polvo.
El proceso comienza con la preparación de la superficie, seguida por la aplicación del polvo mediante pistolas automáticas, y concluye con el curado del polvo en hornos especializados. Todo el proceso está controlado por sistemas electrónicos que monitorizan la velocidad de aplicación, la carga electrostática, la temperatura de los hornos y otros parámetros clave para garantizar un acabado de alta calidad.
Componentes de una Planta Automática
Una planta automática de pintura en polvo se compone de varios elementos, cada uno desempeñando un papel crucial en el proceso:
- Cabinas de pintura en polvo: Son el área donde se aplica el polvo electrostático a las piezas. Estas cabinas pueden ser de tipo batch para lotes pequeños o continuas para producción en masa. En las plantas automáticas, las cabinas están equipadas con sistemas de recuperación de polvo, lo que permite reciclar el material no adherido, reduciendo significativamente el desperdicio.
- Pistolas automáticas: Integradas dentro de la cabina, las pistolas automáticas son controladas por sistemas electrónicos que regulan la cantidad de polvo y la carga eléctrica. Estas pistolas pueden moverse a lo largo de ejes controlados por robots o reciprocadores, asegurando una cobertura uniforme y precisa.
- Transportadores automáticos: Estos sistemas permiten el traslado de las piezas a lo largo de toda la planta. Los transportadores están programados para mover las piezas a través de las diferentes estaciones del proceso, desde la aplicación de pintura hasta el curado, asegurando tiempos de ciclo óptimos.
- Hornos de curado: Los hornos, esenciales para el proceso, son responsables de fundir el polvo sobre las superficies pintadas. La temperatura y el tiempo de curado son variables clave que deben ajustarse con precisión para garantizar que el recubrimiento se adhiera correctamente y ofrezca la resistencia deseada.
Beneficios de las Plantas Automáticas
Las plantas automáticas de pintura en polvo industrial ofrecen una serie de ventajas significativas para las industrias que buscan eficiencia y calidad en sus procesos de recubrimiento.
- Automatización completa: La automatización reduce la dependencia de la mano de obra, minimizando errores humanos y asegurando que cada pieza reciba el mismo tratamiento. Esto es particularmente útil en la producción en masa, donde la consistencia es crítica.
- Mejor aprovechamiento del material: El sistema de recuperación de polvo reduce el desperdicio de material, ya que las partículas de polvo no adheridas son recolectadas y reintroducidas en el proceso. Esto genera importantes ahorros a largo plazo y mejora la sostenibilidad del proceso.
- Incremento de la velocidad de producción: Al automatizar el proceso, las plantas pueden operar a velocidades mucho mayores que los sistemas manuales. Esto permite a las empresas aumentar su capacidad productiva y cumplir con demandas más grandes en menor tiempo.
- Control de calidad mejorado: Los sistemas electrónicos en una planta automática pueden ajustar con precisión la cantidad de polvo aplicado, la velocidad del transportador, y la temperatura del horno, asegurando un control de calidad superior y minimizando defectos.
Desafíos de la Implementación
A pesar de las numerosas ventajas, la implementación de una planta automática de pintura en polvo industrial también conlleva ciertos desafíos:
- Inversión inicial elevada: El costo de instalar una planta automatizada es considerablemente más alto que el de un sistema manual. Esto incluye no solo la compra de equipos de alta tecnología, sino también el costo de instalación, calibración, y capacitación del personal para operar y mantener el sistema.
- Requiere mantenimiento especializado: Estos sistemas automáticos necesitan un mantenimiento regular y especializado para asegurar que sigan funcionando correctamente. La maquinaria compleja, como los transportadores y las pistolas automáticas, deben ser revisadas y calibradas periódicamente para evitar tiempos de inactividad.
- Adaptabilidad limitada para productos personalizados: Aunque las plantas automáticas son extremadamente eficientes para la producción en masa, pueden ser menos flexibles para proyectos que requieren lotes pequeños o personalización, lo que puede no justificar la inversión en estos casos.
Aplicaciones Industriales
Las plantas automáticas de pintura en polvo se utilizan en una variedad de industrias que requieren acabados consistentes y de alta calidad a gran escala. Entre las industrias más beneficiadas por este tipo de tecnología se encuentran:
- Industria automotriz: Aquí se utilizan para pintar chasis, llantas, y otras piezas metálicas que requieren resistencia a la corrosión y un acabado duradero. El uso de plantas automáticas en este sector ha mejorado la eficiencia en las líneas de ensamblaje y ha permitido acabados más precisos y uniformes.
- Electrodomésticos: Empresas que fabrican lavadoras, secadoras, refrigeradores y otros electrodomésticos metálicos utilizan estas plantas para aplicar recubrimientos protectores que mejoran la durabilidad de los productos frente al uso cotidiano y los factores ambientales.
- Mobiliario metálico: La pintura en polvo es ampliamente utilizada en la industria del mobiliario para aplicar recubrimientos decorativos y protectores en sillas, mesas, estanterías, y otros artículos de mobiliario que deben resistir el desgaste diario.
Tendencias Futuras
El futuro de las plantas automáticas de pintura en polvo se orienta hacia una mayor integración de tecnologías inteligentes y sostenibles. Se prevé la incorporación de sistemas de control basados en inteligencia artificial para mejorar la precisión en la aplicación y optimizar el uso de recursos. También se están desarrollando nuevas formulaciones de polvos con menor impacto ambiental, que mejorarán aún más la eficiencia energética de los hornos de curado.
Asimismo, la automatización avanzada y el uso de robots colaborativos están mejorando la flexibilidad de estas plantas, permitiendo la posibilidad de realizar cambios rápidos en la producción sin interrumpir el flujo del proceso, lo cual es ideal para industrias que necesitan adaptarse rápidamente a las demandas del mercado.
Consideraciones Medioambientales
Una de las principales razones por las cuales las plantas automáticas de pintura en polvo han ganado popularidad es su impacto ambiental reducido en comparación con los sistemas tradicionales de pintura líquida. Al no utilizar solventes, la pintura en polvo no emite compuestos orgánicos volátiles (VOCs), que son nocivos para el medio ambiente y la salud humana.
Además, el uso eficiente de los materiales en las plantas automáticas, gracias a los sistemas de recuperación de polvo, reduce el desperdicio y permite que las fábricas operen de manera más sostenible. Este factor, junto con las nuevas innovaciones en energía para los hornos de curado, hace que estas plantas sean una opción atractiva para empresas que desean minimizar su huella de carbono.
Conclusión
Las plantas automáticas de pintura en polvo industrial representan una innovación clave para las empresas que buscan aumentar su eficiencia y reducir costos a largo plazo. Aunque su implementación conlleva un coste inicial elevado, las ventajas en términos de ahorro de material, mejora de la calidad y sostenibilidad hacen que estas plantas sean una inversión atractiva para diversas industrias. Además, con los avances en automatización y tecnología inteligente, el futuro promete aún más mejoras en eficiencia, flexibilidad y respeto al medio ambiente.
Hornos para Diversos Usos de Curado
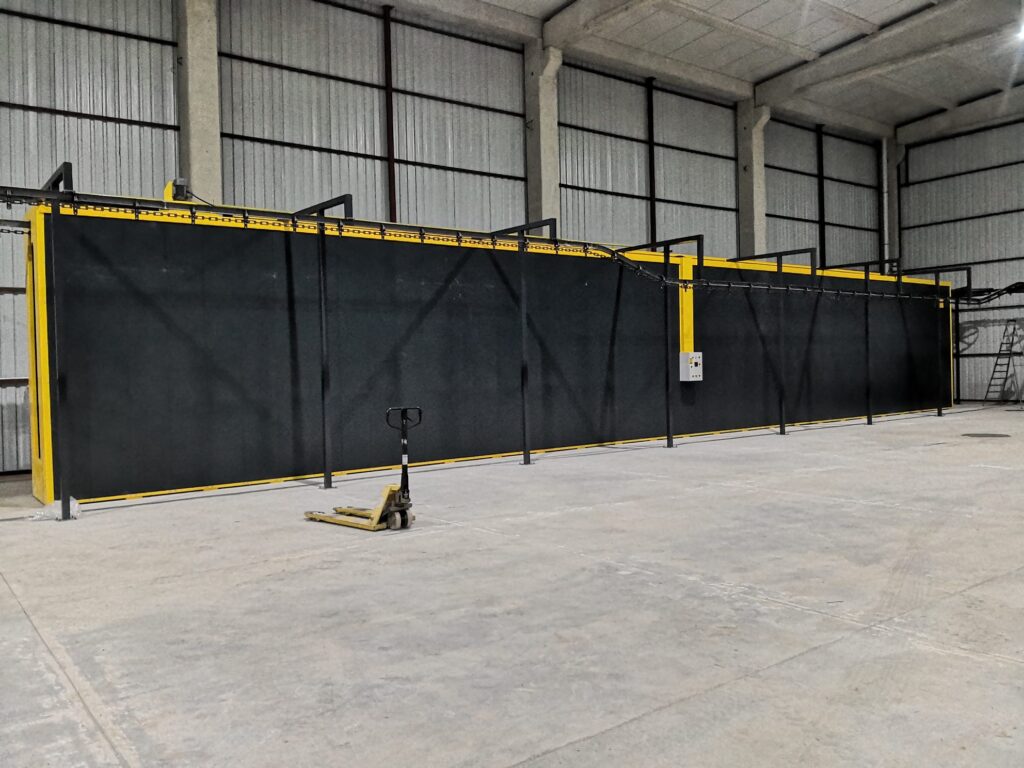
Los hornos para curado son equipos esenciales en numerosos procesos industriales, particularmente en la producción donde se aplican recubrimientos como pintura en polvo o líquidos que requieren un proceso de secado y endurecimiento para obtener los resultados deseados. Estos hornos son altamente versátiles y pueden adaptarse a una variedad de usos industriales, desde el curado de pintura hasta el tratamiento térmico de metales y cerámicas.
Introducción a los Hornos de Curado
Un horno de curado es un dispositivo que se utiliza para secar o endurecer un material, generalmente tras la aplicación de un recubrimiento o para llevar a cabo procesos térmicos específicos. En el contexto de la pintura en polvo, los hornos de curado son cruciales para asegurar que el polvo aplicado sobre las superficies se derrita y se adhiera correctamente, formando una capa homogénea y resistente. Sin este paso, el recubrimiento no tendría la durabilidad ni la calidad estética que requieren muchos productos industriales.
Tipos de Hornos para Curado
Existen varios tipos de hornos de curado, cada uno diseñado para cumplir con las especificaciones de diferentes procesos industriales. Los más comunes incluyen:
- Hornos de convección: Utilizan aire caliente circulante para calentar las piezas y asegurar que el recubrimiento se cure de manera uniforme. Estos hornos son ideales para el curado de pintura en polvo y se utilizan ampliamente en industrias como la automotriz, electrodomésticos, y muebles metálicos.
- Hornos de infrarrojos: Estos hornos usan radiación infrarroja para calentar las superficies directamente, lo que permite un calentamiento más rápido y eficiente en algunos casos. Son útiles cuando se necesitan tiempos de curado más cortos o cuando se aplican recubrimientos en superficies irregulares o complejas.
- Hornos de inducción: En este tipo de horno, se utiliza una corriente eléctrica para calentar las superficies metálicas de manera rápida y precisa. Estos hornos son más comunes en aplicaciones de tratamientos térmicos, pero también se usan en procesos de curado especializados.
- Hornos continuos: Utilizados en líneas de producción de gran escala, estos hornos permiten que las piezas se muevan continuamente a través del proceso de curado. Son ideales para plantas que operan sin interrupciones y manejan grandes volúmenes de producción.
- Hornos batch: También conocidos como hornos de lote, son diseñados para curar lotes pequeños de productos a la vez. Son adecuados para operaciones más pequeñas o para piezas que requieren un tratamiento específico y no están orientadas a la producción en masa.
Usos Industriales de los Hornos de Curado
Los hornos de curado se encuentran en una amplia gama de industrias debido a su capacidad para ofrecer soluciones de recubrimiento duraderas y de alta calidad. Algunos de los usos industriales más comunes incluyen:
- Curado de pintura en polvo: Uno de los usos más extendidos es en la industria de la pintura en polvo. Tras la aplicación de la pintura, las piezas pasan por el horno donde se calientan hasta que el polvo se funde y se adhiere a la superficie de manera uniforme, formando una capa protectora y decorativa.
- Tratamiento térmico de metales: En la industria metalúrgica, los hornos de curado también se utilizan para aplicar tratamientos térmicos a los metales, como el recocido, el endurecimiento y el templado. Estos tratamientos mejoran las propiedades mecánicas del metal, aumentando su resistencia y durabilidad.
- Curado de adhesivos y resinas: En algunos procesos de fabricación, los hornos de curado se utilizan para endurecer adhesivos, selladores o resinas que se aplican a productos industriales, como en la fabricación de componentes electrónicos o de piezas aeroespaciales.
- Industria cerámica: Los hornos son también esenciales en el proceso de curado de cerámicas, donde se requieren temperaturas extremadamente altas para transformar el barro o la arcilla en productos cerámicos duros y duraderos.
Ventajas de Utilizar Hornos de Curado
La implementación de hornos de curado en los procesos industriales ofrece una serie de beneficios clave, entre ellos:
- Consistencia y uniformidad: Los hornos de curado garantizan que los recubrimientos se apliquen y endurezcan de manera uniforme en toda la superficie del producto, lo que mejora la calidad general del acabado y la durabilidad del recubrimiento.
- Mayor durabilidad del producto final: En el caso del curado de pintura en polvo, el calor hace que el polvo se adhiera firmemente a la superficie, creando una barrera protectora contra la corrosión, el desgaste y otros factores ambientales que podrían deteriorar el producto con el tiempo.
- Eficiencia energética: Los hornos modernos están diseñados para ser energéticamente eficientes, lo que reduce los costos operativos a largo plazo. Esto es especialmente importante en grandes líneas de producción donde el horno funciona de manera continua.
- Versatilidad: Al poder ajustarse para cumplir con diferentes temperaturas y tiempos de curado, los hornos de curado son extremadamente versátiles y pueden adaptarse a una variedad de aplicaciones industriales.
Desafíos Asociados al Uso de Hornos de Curado
Aunque los hornos de curado son esenciales en muchos procesos industriales, también presentan algunos desafíos:
- Costos operativos: Los hornos, especialmente aquellos que operan de manera continua, consumen grandes cantidades de energía, lo que puede ser costoso a largo plazo si no se gestionan adecuadamente. Sin embargo, los avances en la eficiencia energética han mitigado en parte este problema.
- Mantenimiento: Los hornos requieren un mantenimiento regular para garantizar que sigan funcionando de manera eficiente. Cualquier mal funcionamiento puede interrumpir la producción y resultar en tiempos de inactividad costosos. Además, el mantenimiento debe realizarse por personal calificado, lo que puede generar costos adicionales.
- Espacio físico: En instalaciones más pequeñas, el tamaño de los hornos puede ser una limitación. Los hornos continuos, en particular, requieren un espacio considerable, lo que puede ser un desafío para algunas fábricas o plantas con espacio limitado.
Innovaciones y Tendencias Futuras en Hornos de Curado
La tecnología de hornos de curado está evolucionando rápidamente, con innovaciones enfocadas en mejorar la eficiencia energética y la precisión del curado. Una de las áreas de desarrollo más prometedoras es el uso de sensores inteligentes y controladores automatizados para ajustar con precisión la temperatura y el tiempo de curado en tiempo real, mejorando la calidad del recubrimiento y reduciendo el consumo energético.
Además, se está explorando el uso de nuevas fuentes de energía más sostenibles para los hornos, como la energía solar o el uso de calor residual de otros procesos industriales para calentar los hornos. Estas innovaciones no solo buscan reducir los costos operativos, sino también mejorar la sostenibilidad de las plantas industriales.
Impacto Ambiental de los Hornos de Curado
El impacto ambiental de los hornos de curado es un tema que ha ganado importancia en los últimos años. La necesidad de reducir el consumo energético y minimizar las emisiones de gases de efecto invernadero ha llevado a muchas industrias a adoptar tecnologías más eficientes. Además, los hornos de curado que utilizan pintura en polvo, en lugar de recubrimientos líquidos, también son más respetuosos con el medio ambiente, ya que la pintura en polvo no contiene solventes ni emite compuestos orgánicos volátiles (VOCs).
Algunos fabricantes de hornos están investigando el uso de tecnologías de curado UV o curado con microondas, que requieren menos energía y proporcionan tiempos de curado más rápidos, lo que no solo beneficia a las empresas en términos de costos, sino que también contribuye a la sostenibilidad ambiental.
Conclusión
Los hornos para diversos usos de curado son componentes clave en una amplia gama de procesos industriales, desde la aplicación de pintura en polvo hasta el tratamiento térmico de materiales. Su capacidad para proporcionar consistencia y durabilidad hace que sean esenciales para muchas industrias, aunque su operación eficiente requiere de inversiones tanto en equipos como en mantenimiento especializado. Con las tendencias hacia la sostenibilidad y la eficiencia energética, el futuro de los hornos de curado está lleno de oportunidades para mejorar aún más los procesos industriales y su impacto ambiental.
Hornos de Curado de Pintura
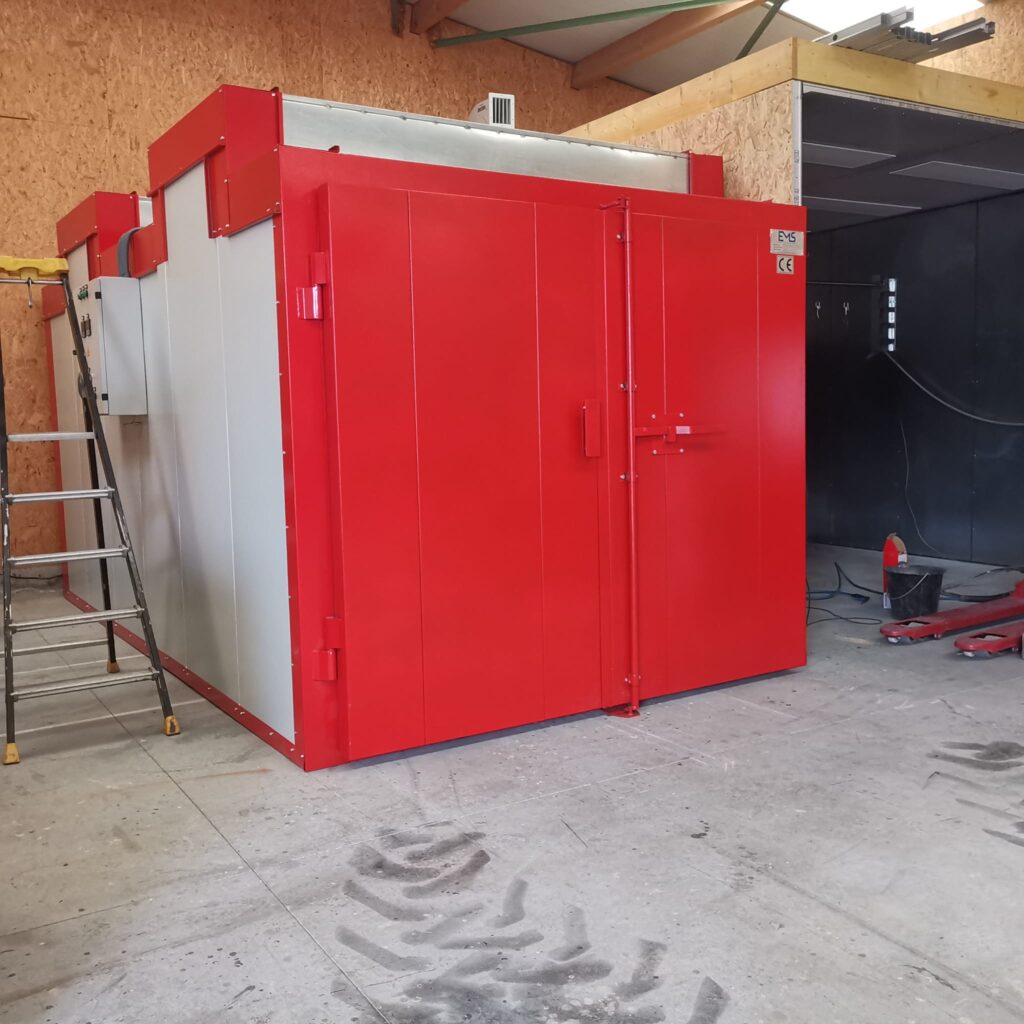
Los hornos de curado de pintura son esenciales en la industria del recubrimiento, ya que permiten que la pintura aplicada sobre una superficie, ya sea en polvo o líquida, se adhiera correctamente mediante un proceso de calentamiento controlado. Este proceso asegura que la pintura se endurezca y forme una capa resistente, protegiendo la superficie y garantizando un acabado de alta calidad.
Proceso de Curado en Pintura
El proceso de curado es un paso final crucial después de la aplicación de la pintura. La pintura en polvo, al ser aplicada mediante un proceso electrostático, necesita pasar por un ciclo de curado en un horno especializado, donde se funde y se adhiere a la superficie. Este calentamiento promueve la reacción química necesaria para que el recubrimiento alcance su máxima dureza y propiedades protectoras.
En el caso de la pintura líquida, el curado es ligeramente diferente, ya que implica la evaporación de los solventes y la polimerización de los compuestos de la pintura, lo que también requiere temperaturas controladas.
Tipos de Hornos de Curado para Pintura
Existen varios tipos de hornos diseñados específicamente para el curado de pinturas, dependiendo de las necesidades de producción y el tipo de pintura utilizada. Los principales tipos de hornos incluyen:
- Hornos de convección: Utilizan aire caliente que circula alrededor de las piezas pintadas para garantizar un curado uniforme. Este tipo de horno es el más común en la industria de la pintura en polvo, debido a su capacidad para manejar grandes volúmenes de producción y su eficacia en la distribución del calor.
- Hornos de infrarrojos (IR): Usan radiación infrarroja para calentar rápidamente las superficies pintadas. Son particularmente útiles para piezas con geometrías complejas, donde el calor puede concentrarse en áreas específicas sin afectar otras partes de la pieza.
- Hornos de inducción: Estos hornos calientan las superficies metálicas a través de campos electromagnéticos, lo que permite un curado extremadamente rápido. Son eficaces cuando se necesita acelerar el proceso de producción.
- Hornos continuos: Ideales para líneas de producción a gran escala, estos hornos permiten que las piezas pintadas se muevan continuamente a través del sistema, lo que reduce los tiempos de espera entre lotes y maximiza la producción.
- Hornos batch: Diseñados para producir lotes más pequeños o productos personalizados. Son más flexibles, ya que permiten que diferentes tipos de productos sean tratados en una misma instalación sin necesidad de grandes ajustes en la configuración del horno.
Parámetros Críticos en el Curado de Pintura
Los hornos de curado deben operar bajo parámetros cuidadosamente controlados para asegurar que el recubrimiento se adhiera correctamente y se forme una capa protectora uniforme. Entre los factores más importantes están:
- Temperatura: Cada tipo de pintura tiene una temperatura de curado óptima. La pintura en polvo, por ejemplo, generalmente requiere temperaturas que oscilan entre los 160 y 200 grados Celsius. Un control preciso de la temperatura es esencial para evitar un curado insuficiente o sobrecurado, lo que podría afectar la integridad del recubrimiento.
- Tiempo de curado: El tiempo que una pieza permanece en el horno depende del grosor de la pintura y del material de la pieza. Un curado adecuado requiere suficiente tiempo para que todo el recubrimiento alcance la temperatura óptima, pero sin excederse para evitar deformaciones o deterioros en la superficie.
- Distribución del calor: Es crucial que el calor se distribuya de manera uniforme dentro del horno, especialmente en hornos de gran capacidad. Los sistemas de convección forzada ayudan a garantizar que todas las piezas reciban la misma cantidad de calor durante el proceso.
Beneficios de los Hornos de Curado para Pintura
El uso de hornos de curado en el proceso de aplicación de pintura ofrece numerosos beneficios, tanto en términos de calidad del producto final como de eficiencia en la producción:
- Acabados duraderos: Un curado adecuado garantiza que la pintura forme una capa resistente y duradera que protege las superficies contra la corrosión, el desgaste y otros factores ambientales.
- Mayor resistencia química y mecánica: El proceso de curado mejora las propiedades químicas y mecánicas de la pintura, haciéndola más resistente a productos químicos, abrasión y rayaduras.
- Velocidad de producción: Los hornos, especialmente los continuos, permiten curar grandes volúmenes de piezas rápidamente, lo que es fundamental en industrias de alta demanda como la automotriz y la de electrodomésticos.
- Optimización del material: En el caso de la pintura en polvo, el proceso de curado en el horno asegura que todo el polvo aplicado se adhiera correctamente a la superficie, reduciendo el desperdicio y optimizando el uso del material.
Aplicaciones Industriales de los Hornos de Curado para Pintura
Los hornos de curado de pintura se utilizan en una amplia gama de sectores industriales debido a su capacidad para proporcionar acabados de alta calidad y mejorar la durabilidad de los productos. Entre las aplicaciones más comunes se incluyen:
- Industria automotriz: Los componentes metálicos, como las carrocerías de los vehículos, se benefician de los recubrimientos curados, que los protegen de la oxidación y el desgaste causado por la exposición a elementos como la lluvia y la nieve.
- Fabricación de electrodomésticos: Productos como lavadoras, secadoras y refrigeradores son recubiertos con pintura en polvo para mejorar su resistencia al uso cotidiano, así como a la exposición a humedad y productos de limpieza.
- Mobiliario metálico: Los muebles de metal, como sillas, mesas y estanterías, a menudo se recubren con pintura en polvo para proporcionarles un acabado estético y protector que resista el desgaste diario.
- Industria aeronáutica: Los hornos de curado también se utilizan en la fabricación de componentes aeronáuticos, donde se aplican recubrimientos protectores y resistentes al calor que garantizan la durabilidad de las piezas en condiciones extremas.
Desafíos en el Uso de Hornos de Curado para Pintura
A pesar de sus muchos beneficios, los hornos de curado también presentan algunos desafíos en su uso industrial:
- Consumo energético: Los hornos de curado, especialmente los de convección que requieren mantener altas temperaturas durante largos períodos, pueden ser intensivos en términos de consumo energético. Las empresas deben gestionar estos costos y buscar formas de mejorar la eficiencia energética de sus hornos.
- Mantenimiento regular: Los hornos requieren un mantenimiento constante para asegurar que el calor se distribuya uniformemente y que los componentes internos, como los ventiladores o las fuentes de calor, funcionen correctamente. El mantenimiento deficiente puede resultar en tiempos de inactividad y afectaciones a la calidad del producto.
- Tiempos de curado prolongados para ciertos materiales: Algunos materiales o recubrimientos especiales pueden requerir tiempos de curado más largos, lo que podría ralentizar la producción. Esto es particularmente relevante en líneas de producción continuas, donde los tiempos de ciclo deben ser optimizados.
Innovaciones en Hornos de Curado para Pintura
En los últimos años, ha habido varias innovaciones en el diseño y la tecnología de los hornos de curado, muchas de ellas enfocadas en mejorar la eficiencia energética y reducir el tiempo de curado. Algunas de estas innovaciones incluyen:
- Hornos híbridos: Estos combinan diferentes tecnologías de curado, como infrarrojos y convección, para proporcionar un calentamiento más rápido y eficiente. Los hornos híbridos son capaces de reducir los tiempos de curado sin comprometer la calidad del recubrimiento.
- Sistemas de control inteligente: Los hornos modernos están equipados con sensores y sistemas de control automatizados que monitorean y ajustan la temperatura y el flujo de aire en tiempo real. Esto permite optimizar el proceso de curado para diferentes tipos de recubrimientos y productos.
- Curado por microondas: Aunque todavía en desarrollo, la tecnología de curado por microondas promete reducir drásticamente los tiempos de curado al calentar los recubrimientos desde el interior hacia el exterior. Esto podría revolucionar el proceso de curado en industrias de alta demanda.
Impacto Ambiental de los Hornos de Curado para Pintura
El impacto ambiental de los hornos de curado, especialmente los que funcionan de manera continua, es una preocupación creciente en la industria. Las emisiones de gases de efecto invernadero y el alto consumo energético son aspectos que se están abordando mediante tecnologías más sostenibles. Los fabricantes de hornos están desarrollando modelos más eficientes que reducen el consumo de energía y utilizan fuentes de calor más limpias, como la electricidad o el gas natural, en lugar de combustibles fósiles.
Conclusión
Los hornos de curado de pintura son una pieza clave en el proceso de acabado industrial, garantizando la calidad, durabilidad y resistencia de los recubrimientos. A medida que la tecnología avanza, los hornos se están volviendo más eficientes y sostenibles, lo que no solo mejora la producción, sino que también reduce el impacto ambiental. El curado de pintura seguirá siendo una parte vital de muchas industrias, con innovaciones futuras que seguirán mejorando la calidad y la eficiencia de estos sistemas.
Hornos de Curado
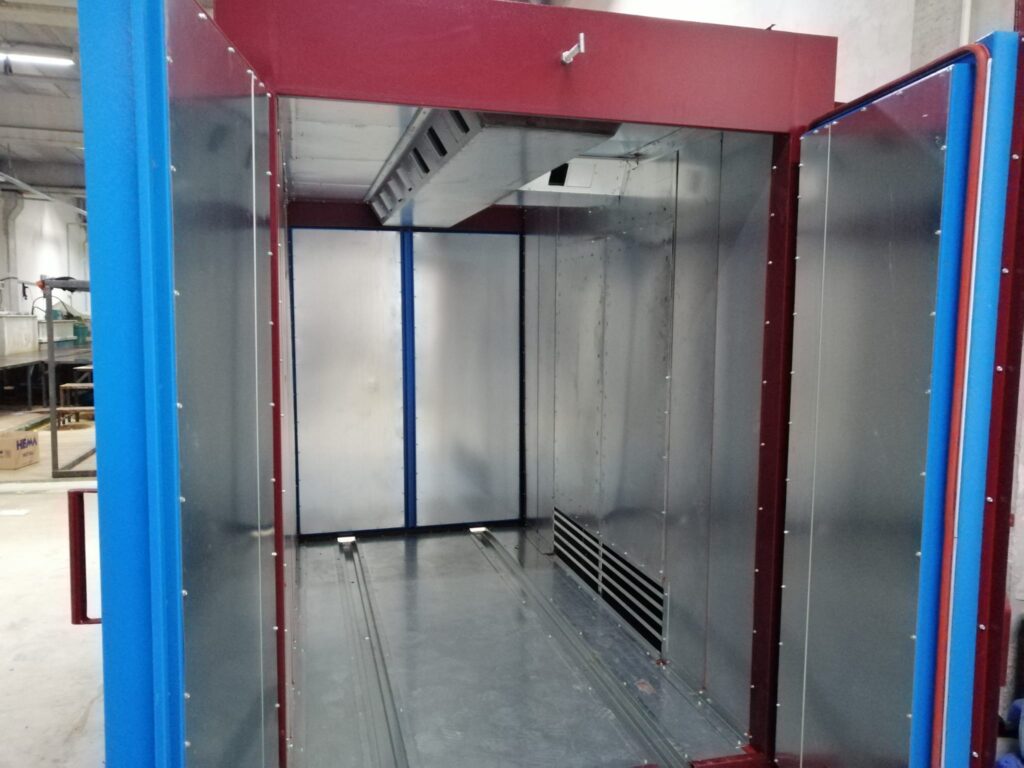
Los hornos de curado son una herramienta fundamental en el procesamiento industrial, especialmente en la fabricación de productos que requieren un acabado térmico o un tratamiento post-aplicación de recubrimientos. El curado, que implica el endurecimiento de una sustancia mediante la aplicación de calor, es esencial para garantizar la durabilidad y la resistencia de los recubrimientos, como la pintura en polvo, en una amplia gama de superficies.
¿Qué es el Curado?
El curado es un proceso en el cual una sustancia, ya sea pintura, adhesivo o un compuesto químico, se endurece o solidifica mediante la aplicación controlada de calor. Este proceso mejora las propiedades mecánicas y químicas del material tratado, haciendo que sea más resistente a los factores externos, como la humedad, el calor o los productos químicos.
En la industria de la pintura en polvo, el curado es fundamental para que el polvo aplicado sobre una superficie se derrita y forme una película continua y uniforme. Este recubrimiento, una vez curado, proporciona una capa protectora duradera que es resistente a la corrosión, el desgaste y la decoloración.
Tipos de Hornos de Curado
Los hornos de curado se pueden clasificar en varias categorías según su diseño y el método de calentamiento que utilizan. Los tipos más comunes incluyen:
- Hornos de convección: Son los más utilizados en la industria del recubrimiento en polvo. Funcionan mediante la circulación de aire caliente alrededor de las piezas que se están curando. El aire se distribuye uniformemente por todo el espacio del horno, garantizando que todas las superficies de las piezas reciban la misma cantidad de calor.
- Hornos de infrarrojos: Utilizan radiación infrarroja para calentar las piezas de manera más rápida y eficiente. Estos hornos son ideales para situaciones donde se requiere un curado rápido, ya que la radiación infrarroja calienta las superficies directamente sin la necesidad de calentar el aire circundante.
- Hornos de inducción: Emplean campos electromagnéticos para calentar las superficies metálicas, lo que permite un calentamiento más rápido y preciso. Aunque son menos comunes en el curado de pintura en polvo, se utilizan en procesos especializados donde se requiere un control térmico muy preciso.
- Hornos continuos: Estos hornos permiten que las piezas pasen a través de ellos de manera continua, lo que los hace ideales para líneas de producción en masa. Son altamente eficientes y se utilizan en plantas de producción que operan sin interrupciones.
- Hornos batch: Estos hornos están diseñados para procesar lotes más pequeños de productos. Son más flexibles y permiten realizar ajustes para diferentes tipos de piezas o recubrimientos, lo que los convierte en una opción adecuada para fábricas que manejan una variedad de productos.
Factores Clave en el Funcionamiento de los Hornos de Curado
El éxito del proceso de curado depende de varios factores clave, todos los cuales deben ser controlados cuidadosamente para asegurar un recubrimiento de alta calidad:
- Temperatura: Cada material tiene una temperatura de curado específica. En el caso de la pintura en polvo, las temperaturas de curado suelen estar entre los 160 y los 220 grados Celsius, dependiendo del tipo de polvo utilizado y del espesor del recubrimiento.
- Tiempo de curado: El tiempo que una pieza pasa en el horno también es crucial. Un tiempo de curado demasiado corto puede resultar en un recubrimiento débil que no ofrece la protección deseada, mientras que un tiempo demasiado largo puede deteriorar la calidad del recubrimiento o incluso dañar las piezas.
- Distribución del calor: Es esencial que el calor se distribuya uniformemente dentro del horno. Si una parte de la pieza recibe más calor que otra, el recubrimiento no se curará de manera uniforme, lo que podría llevar a defectos en la apariencia o en la durabilidad del recubrimiento.
Aplicaciones de los Hornos de Curado en la Industria
Los hornos de curado son esenciales en muchas industrias donde el acabado de los productos requiere un proceso de secado o endurecimiento. Algunas de las aplicaciones más comunes incluyen:
- Curado de pintura en polvo: La aplicación más conocida de los hornos de curado es en el tratamiento de superficies pintadas con polvo. Después de que el polvo se aplica mediante un proceso electrostático, las piezas se introducen en el horno, donde el calor funde el polvo y lo convierte en una capa uniforme.
- Industria automotriz: En la fabricación de automóviles, los hornos de curado son utilizados para el endurecimiento de la pintura en las carrocerías de los vehículos. La pintura curada ofrece protección contra la corrosión y mejora la estética del vehículo.
- Electrodomésticos: Productos como refrigeradores, lavadoras y estufas también pasan por un proceso de curado después de ser recubiertos con pintura en polvo, lo que les otorga mayor durabilidad y resistencia a la humedad y al uso diario.
- Componentes industriales: Muchas piezas metálicas utilizadas en maquinaria pesada y estructuras industriales son tratadas con recubrimientos protectores que requieren un curado adecuado para mejorar su resistencia a los elementos.
Ventajas de los Hornos de Curado
El uso de hornos de curado en procesos industriales ofrece una serie de ventajas, tanto en términos de la calidad del producto como en la eficiencia de producción. Algunas de las principales ventajas incluyen:
- Durabilidad del recubrimiento: Un curado adecuado garantiza que el recubrimiento se adhiera correctamente a la superficie, creando una capa resistente que puede soportar el desgaste, la corrosión y otros factores dañinos.
- Eficiencia en la producción: Los hornos de curado, especialmente los continuos, permiten curar grandes volúmenes de piezas en poco tiempo, lo que es crucial para mantener altos niveles de producción en fábricas con demanda constante.
- Control de calidad: Los hornos modernos están equipados con sistemas de control que permiten ajustar con precisión la temperatura y el tiempo de curado, asegurando que todas las piezas se traten de manera uniforme y con alta calidad.
Retos Asociados al Uso de Hornos de Curado
A pesar de sus múltiples beneficios, los hornos de curado también presentan algunos desafíos, especialmente en términos de costos operativos y mantenimiento:
- Consumo energético: Los hornos de curado pueden consumir grandes cantidades de energía, especialmente los de convección que deben mantener altas temperaturas durante largos períodos. Esto puede resultar en altos costos operativos, particularmente en fábricas de gran tamaño.
- Mantenimiento y reparación: Los hornos requieren un mantenimiento regular para asegurar su funcionamiento eficiente. Si un horno no se mantiene adecuadamente, puede haber problemas con la distribución del calor, lo que afectaría la calidad del curado y podría causar tiempos de inactividad en la producción.
- Espacio físico: Los hornos, especialmente los continuos, ocupan una cantidad significativa de espacio en las fábricas. Esto puede ser un desafío en plantas más pequeñas donde el espacio es limitado.
Innovaciones en Hornos de Curado
En los últimos años, la tecnología de hornos de curado ha avanzado significativamente, con innovaciones que mejoran la eficiencia y reducen el impacto ambiental. Algunas de estas innovaciones incluyen:
- Hornos de alta eficiencia energética: Los fabricantes han desarrollado hornos que utilizan menos energía al optimizar la distribución del calor y mejorar el aislamiento térmico, lo que reduce significativamente los costos operativos.
- Curado con infrarrojos y microondas: Estas tecnologías permiten un calentamiento más rápido y eficiente, lo que reduce el tiempo de curado y aumenta la producción.
- Sistemas de control inteligente: Los hornos modernos están equipados con sensores que monitorean continuamente la temperatura y ajustan el proceso de curado en tiempo real, asegurando un control preciso y una mayor eficiencia.
Impacto Ambiental y Sostenibilidad
El impacto ambiental de los hornos de curado, especialmente en términos de consumo energético, ha llevado a la industria a buscar soluciones más sostenibles. Los hornos de curado más nuevos están diseñados para ser más eficientes desde el punto de vista energético, utilizando fuentes de energía renovable y sistemas de recuperación de calor para minimizar el consumo de energía.
Conclusión
Los hornos de curado son una parte integral del proceso industrial, asegurando que los recubrimientos y otros materiales se adhieran correctamente y ofrezcan la durabilidad y protección necesarias. A medida que la tecnología avanza, los hornos se vuelven más eficientes, sostenibles y adaptables a las necesidades cambiantes de la industria moderna. Con una mayor conciencia sobre el impacto ambiental, las fábricas están adoptando hornos de curado más avanzados que no solo mejoran la calidad del producto, sino que también reducen su huella de carbono.
Horno Tipo Batch
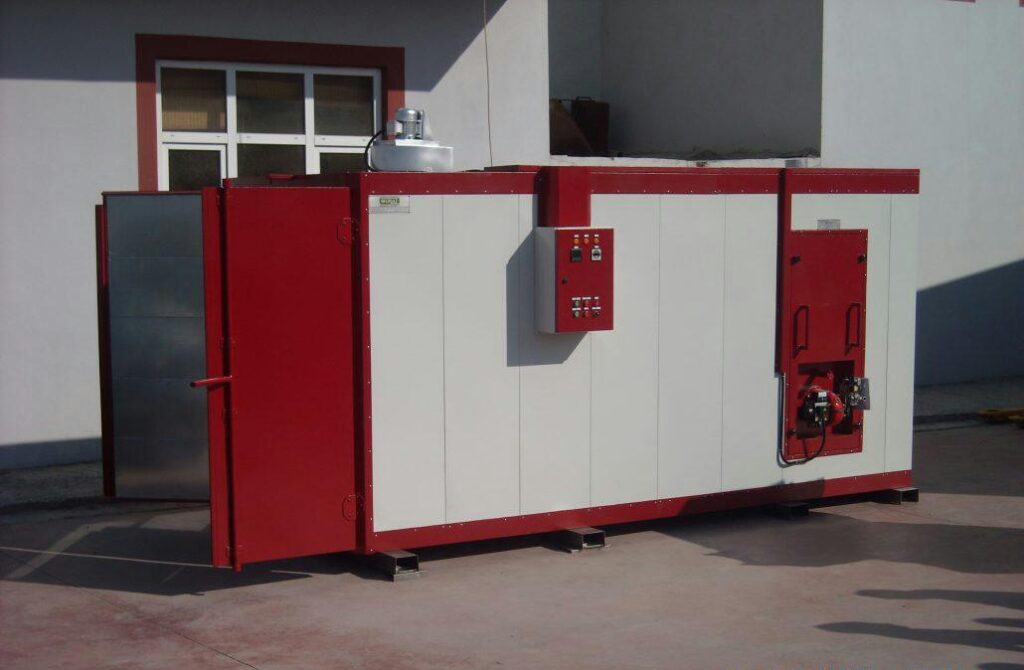
El horno tipo batch es uno de los equipos más versátiles y utilizados en la industria, especialmente en aplicaciones que requieren procesar pequeños lotes de productos o piezas que varían en tamaño y forma. Este tipo de horno es fundamental en industrias donde se busca flexibilidad y precisión en el tratamiento térmico de los materiales, y su diseño permite adaptarse a una amplia variedad de procesos, desde el curado de pinturas hasta el secado de materiales y el tratamiento térmico de metales.
¿Qué es un Horno Tipo Batch?
Un horno tipo batch, también conocido como horno por lotes, es un equipo de calentamiento diseñado para procesar un grupo o lote de piezas a la vez, en lugar de operarse de manera continua como los hornos de paso. En este tipo de horno, los productos se introducen en una cámara, donde se someten a un ciclo de calentamiento que puede variar en temperatura y duración según las necesidades del proceso.
Este tipo de horno es particularmente útil en aplicaciones donde las piezas tienen diferentes tamaños, formas o tratamientos específicos, lo que requiere un control individualizado del proceso. Los hornos tipo batch pueden ser utilizados en procesos de recubrimiento, curado, secado, templado y muchas otras aplicaciones industriales.
Ventajas de los Hornos Tipo Batch
Los hornos tipo batch ofrecen varias ventajas significativas, especialmente en términos de flexibilidad y control. Entre las principales ventajas destacan:
- Flexibilidad en la producción: A diferencia de los hornos continuos, los hornos batch permiten procesar una amplia variedad de piezas de diferentes tamaños y formas en un solo ciclo. Esto es especialmente útil en fábricas donde se trabaja con productos personalizados o donde las líneas de producción no operan de manera constante.
- Control preciso del proceso: Los hornos tipo batch permiten ajustar los parámetros de temperatura, tiempo de calentamiento y atmósfera interna según las necesidades de cada lote de productos. Esto asegura que cada pieza reciba el tratamiento térmico adecuado para garantizar la calidad y durabilidad del producto final.
- Menor desperdicio de material: Al procesar lotes más pequeños y específicos, se reduce el riesgo de defectos o sobrecalentamiento, lo que minimiza el desperdicio de material y mejora la eficiencia general del proceso.
- Mayor capacidad para productos de alta complejidad: Estos hornos son ideales para productos que requieren tiempos de curado más prolongados o procesos más detallados, como piezas de maquinaria o componentes electrónicos que necesitan un tratamiento térmico preciso.
- Versatilidad en la temperatura: Pueden operar en un amplio rango de temperaturas, lo que los hace útiles para una gran variedad de procesos industriales que incluyen curado de pintura, endurecimiento de metales y secado de compuestos.
Aplicaciones Industriales del Horno Tipo Batch
Los hornos tipo batch se utilizan en una amplia gama de industrias debido a su versatilidad y capacidad para procesar lotes de productos de manera eficiente y precisa. Algunas de las aplicaciones más comunes incluyen:
- Curado de pintura en polvo: En la industria de recubrimientos, los hornos batch son esenciales para el curado de pintura en polvo en piezas personalizadas o de tamaños variados. El proceso de curado en estos hornos asegura que la pintura se adhiera correctamente y forme una capa protectora uniforme y resistente.
- Tratamiento térmico de metales: En la fabricación de piezas metálicas, los hornos tipo batch son utilizados para procesos de templado, recocido y endurecimiento de metales. Estos procesos mejoran las propiedades mecánicas del metal, haciéndolo más resistente y duradero.
- Industria aeroespacial: En la fabricación de componentes para aeronaves, se utilizan hornos batch para el tratamiento térmico de piezas críticas que requieren un control preciso de temperatura y tiempo para asegurar su integridad estructural.
- Electrónica y semiconductores: Los hornos tipo batch son utilizados para el secado y curado de adhesivos, resinas y otros materiales utilizados en la fabricación de componentes electrónicos. El control preciso de la temperatura es fundamental en estos procesos para evitar daños a los componentes sensibles.
- Cerámica y vidrio: En la producción de artículos cerámicos y de vidrio, los hornos batch son utilizados para el secado y cocción de piezas, lo que mejora la resistencia y la durabilidad de los productos.
Componentes de un Horno Tipo Batch
El diseño de un horno tipo batch incluye varios componentes clave que permiten un control preciso del proceso de calentamiento y aseguran la eficiencia del horno. Algunos de los componentes más importantes incluyen:
- Cámara de calentamiento: Es el espacio interno donde se colocan las piezas a tratar. Esta cámara está equipada con elementos calefactores que generan calor mediante convección, radiación o inducción, dependiendo del tipo de horno.
- Controladores de temperatura: Estos sistemas permiten ajustar y monitorear la temperatura dentro de la cámara, asegurando que se mantenga dentro de los parámetros deseados durante todo el proceso.
- Sistemas de ventilación: Los hornos tipo batch a menudo están equipados con sistemas de ventilación que permiten una circulación adecuada del aire caliente, lo que garantiza un calentamiento uniforme de todas las piezas dentro de la cámara.
- Puertas aisladas: Las puertas del horno están diseñadas con aislamiento térmico para minimizar la pérdida de calor durante la apertura y cierre del horno. Esto también ayuda a mantener una temperatura estable dentro de la cámara.
- Sensores y sistemas de monitoreo: Los sensores de temperatura y otros sistemas de monitoreo garantizan que el proceso de curado o tratamiento térmico se realice de manera controlada y precisa, lo que es esencial para productos que requieren alta calidad y precisión en sus acabados.
Desafíos en el Uso de Hornos Tipo Batch
Aunque los hornos tipo batch ofrecen muchas ventajas, también presentan ciertos desafíos, especialmente en términos de eficiencia y tiempo de producción. Algunos de los desafíos más comunes incluyen:
- Menor capacidad de producción: Dado que los hornos batch procesan lotes más pequeños, su capacidad de producción es menor en comparación con los hornos continuos, lo que puede ser un problema en fábricas de alta demanda.
- Mayor tiempo de ciclo: El tiempo necesario para cargar, calentar, procesar y descargar los productos en un horno batch puede ser mayor, lo que resulta en tiempos de ciclo más largos en comparación con los hornos de paso continuo.
- Costos energéticos: Debido a que los hornos batch deben ser recalibrados y calentados para cada lote, su consumo de energía puede ser más alto, especialmente si los ciclos de producción no están optimizados.
Innovaciones en Hornos Tipo Batch
A medida que las demandas industriales evolucionan, también lo hacen los hornos tipo batch, con innovaciones que mejoran la eficiencia energética y optimizan los tiempos de ciclo. Algunas de las innovaciones más destacadas incluyen:
- Sistemas de recuperación de calor: Muchos hornos tipo batch modernos están equipados con sistemas que permiten recuperar el calor generado durante el proceso y reutilizarlo para precalentar los lotes siguientes, lo que reduce el consumo energético.
- Automatización y control avanzado: Los hornos batch actuales incluyen sistemas de control automatizados que permiten ajustar la temperatura, el tiempo de ciclo y otros parámetros de manera remota. Esto mejora la precisión del proceso y reduce el riesgo de error humano.
- Materiales de aislamiento avanzados: El uso de nuevos materiales de aislamiento térmico permite reducir la pérdida de calor, mejorando la eficiencia energética y manteniendo una temperatura constante dentro de la cámara del horno.
Impacto Ambiental de los Hornos Tipo Batch
El uso de hornos batch tiene un impacto ambiental relacionado con el consumo energético, especialmente en fábricas donde los ciclos de producción no son constantes. Sin embargo, las innovaciones en eficiencia energética y el uso de fuentes de energía más limpias han ayudado a reducir este impacto.
Las empresas están adoptando tecnologías más sostenibles, como el uso de electricidad de fuentes renovables, sistemas de recuperación de calor y mejores prácticas operativas para minimizar el consumo de energía y las emisiones de gases de efecto invernadero.
Los hornos para pintura electrostática juegan un papel fundamental en el proceso de curado de los recubrimientos aplicados a través de pintura en polvo. En el contexto industrial, la pintura electrostática es una técnica ampliamente utilizada debido a su eficiencia y su capacidad para proporcionar un acabado duradero y uniforme en superficies metálicas y otros materiales conductores. Los hornos utilizados en este proceso deben cumplir con ciertos requisitos de diseño y funcionamiento que aseguren un curado adecuado, tanto en términos de temperatura como de tiempo de exposición.
Características principales del horno para pintura electrostática
Los hornos para curado de pintura electrostática están diseñados para operar a temperaturas que oscilan entre los 180°C y 220°C, dependiendo del tipo de recubrimiento en polvo utilizado. Estos equipos permiten que el polvo, que previamente ha sido cargado eléctricamente y adherido a la superficie del objeto, se funda y se convierta en una película uniforme y resistente tras el enfriamiento.
Uno de los aspectos clave de los hornos para pintura electrostática es su capacidad para mantener una temperatura uniforme en todo el espacio de curado. Esto se logra mediante el uso de sistemas de ventilación forzada que garantizan la circulación constante del aire caliente. Adicionalmente, los hornos cuentan con paneles de control que permiten ajustar y monitorizar tanto la temperatura como la duración del proceso de curado, lo que asegura resultados consistentes y de alta calidad.
Tipos de hornos para pintura electrostática
Existen diversos tipos de hornos utilizados en la industria de la pintura electrostática, que varían en su diseño y aplicación según las necesidades de la producción. Entre los más comunes se encuentran:
- Hornos de curado tipo batch: Estos hornos están diseñados para manejar lotes pequeños o medianos de piezas, lo que los hace ideales para procesos de producción intermitente o personalizados. Las piezas son introducidas en el horno una vez aplicadas con polvo, y el proceso de curado se realiza de manera individual por cada lote.
- Hornos continuos: Diseñados para operaciones a gran escala, estos hornos permiten un flujo constante de piezas a través de una línea de producción. Las piezas se mueven mediante transportadores dentro del horno, lo que optimiza el tiempo de producción y reduce los costos operativos en grandes instalaciones industriales.
Beneficios del uso de hornos para pintura electrostática
Los hornos utilizados en el proceso de pintura electrostática ofrecen numerosos beneficios en términos de eficiencia, calidad del acabado y sostenibilidad. Entre los principales se incluyen:
- Curado rápido y eficiente: Al operar a altas temperaturas y contar con sistemas de distribución de calor optimizados, los hornos permiten que el polvo se cure rápidamente, lo que aumenta la productividad de la línea de producción.
- Acabado uniforme: La capacidad de mantener una temperatura constante en todo el horno garantiza que el recubrimiento de polvo se funda de manera uniforme sobre la superficie, lo que resulta en acabados consistentes y estéticamente atractivos.
- Reducción de emisiones: En comparación con otras técnicas de curado, como los hornos que utilizan solventes, los hornos para pintura electrostática producen menores emisiones de compuestos orgánicos volátiles (COV), lo que contribuye a procesos más limpios y respetuosos con el medio ambiente.
En conclusión, los hornos para pintura electrostática son una pieza esencial en cualquier instalación que busque aplicar recubrimientos en polvo de manera eficiente, ofreciendo acabados duraderos y de alta calidad con un impacto ambiental reducido.
Cabinas Continuas para Pintura en Polvo
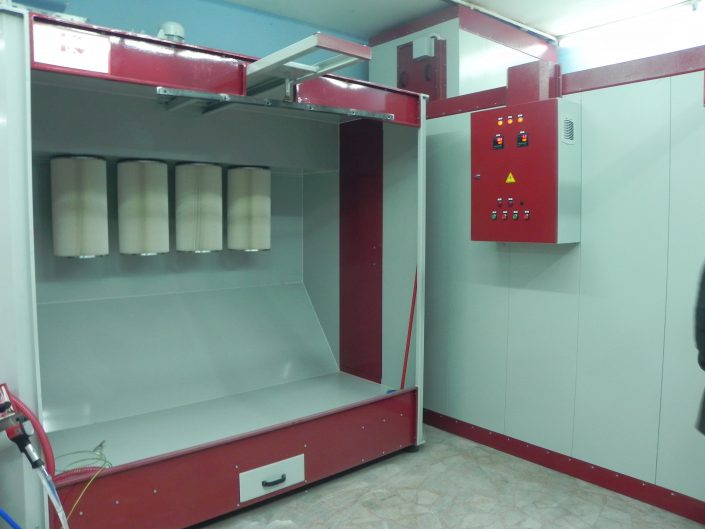
Las cabinas continuas para pintura en polvo son estructuras especializadas diseñadas para facilitar la aplicación del recubrimiento en polvo en procesos industriales de alta demanda. Estas cabinas están especialmente diseñadas para funcionar de manera continua, lo que permite una mayor productividad en líneas de producción donde se requiere un flujo constante de piezas que necesitan ser pintadas.
Características de las cabinas continuas
Una cabina continua para pintura en polvo debe contar con un sistema de transporte automático que mueva las piezas a través de las diferentes estaciones de la cabina, donde se lleva a cabo la aplicación del polvo. El uso de transportadores es clave en este tipo de cabinas, ya que asegura un flujo constante de piezas, optimizando así el proceso productivo. Además, estas cabinas suelen estar equipadas con pistolas automáticas para la aplicación del polvo, que están programadas para cubrir la superficie de las piezas de manera uniforme.
Una de las principales ventajas de las cabinas continuas es que permiten una gran flexibilidad en el tamaño y forma de las piezas que pueden ser pintadas. Además, muchas de estas cabinas están diseñadas para facilitar el cambio rápido de colores, lo que reduce el tiempo de inactividad y mejora la eficiencia operativa.
Ventajas de las cabinas continuas para pintura en polvo
- Productividad elevada: El diseño continuo de estas cabinas permite que el proceso de aplicación de polvo sea altamente eficiente, lo que resulta en una mayor cantidad de piezas pintadas en un menor tiempo.
- Control ambiental: Las cabinas están equipadas con sistemas de extracción y filtrado de aire que aseguran un ambiente controlado durante la aplicación del polvo. Esto no solo garantiza una aplicación más limpia, sino que también mejora la seguridad en el lugar de trabajo.
- Eficiencia en el uso de polvo: Los sistemas de recuperación de polvo en estas cabinas permiten recolectar el exceso de polvo no utilizado, lo que se traduce en un ahorro significativo de material.
Las cabinas continuas para pintura en polvo son, por tanto, una solución eficiente y rentable para las industrias que necesitan mantener un alto nivel de producción sin sacrificar la calidad del acabado.
Cabinas para Pintura en Polvo
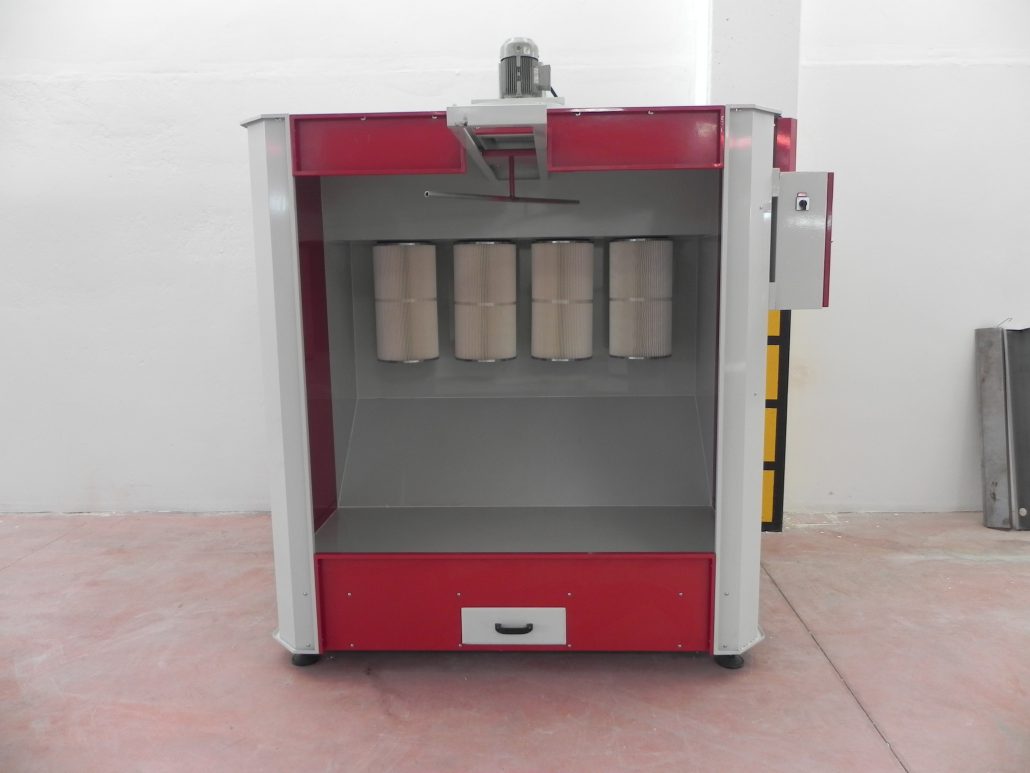
Las cabinas para pintura en polvo son espacios especialmente diseñados para la aplicación de recubrimientos en polvo en una amplia variedad de productos. Estas cabinas pueden ser tanto manuales como automáticas, dependiendo del tipo de producción y las necesidades de cada instalación industrial.
Función principal de las cabinas para pintura en polvo
Las cabinas para pintura en polvo están diseñadas para contener y controlar la aplicación del polvo, asegurando que el proceso se realice de manera eficiente y segura. Además de permitir la correcta aplicación del polvo sobre las superficies de los productos, estas cabinas también desempeñan un papel crucial en la recuperación del polvo no adherido, lo que mejora la eficiencia del proceso y reduce los costos operativos.
Hornos de Curado para Pintura Electrostática
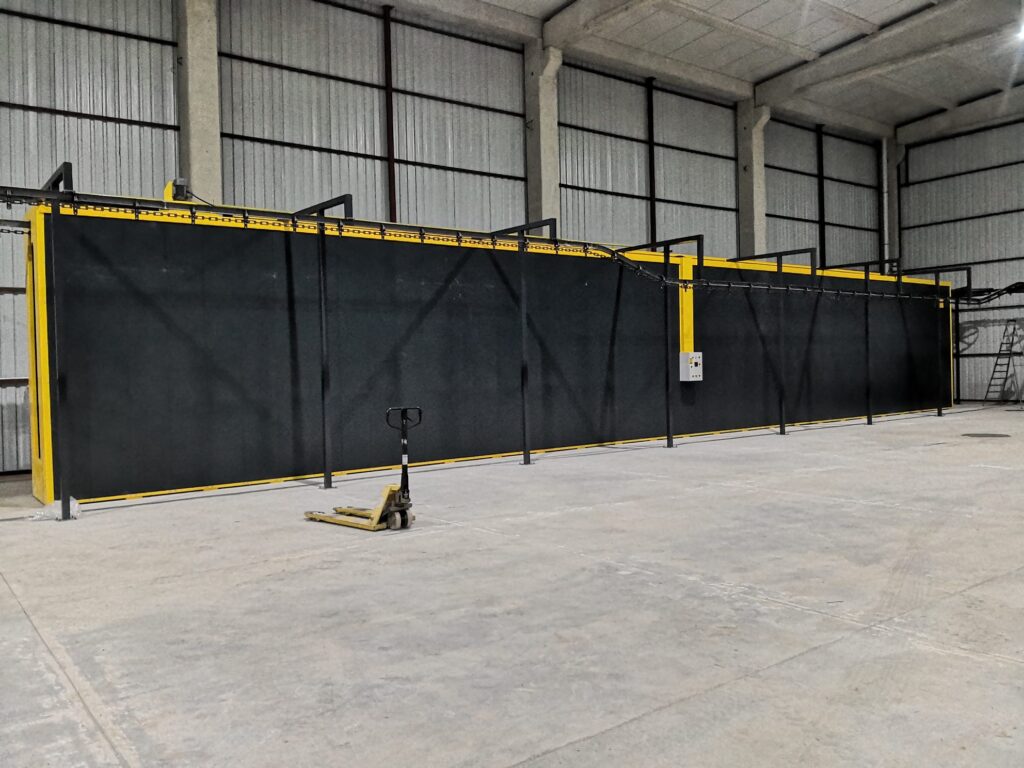
Los hornos de curado para pintura electrostática son fundamentales en el proceso de recubrimiento en polvo, ya que garantizan que la pintura aplicada sobre las superficies se endurezca adecuadamente, formando una capa duradera y uniforme. El curado es un proceso clave donde el polvo se funde y reacciona químicamente para formar un acabado liso y resistente.
Proceso de curado en hornos para pintura electrostática
El curado de la pintura electrostática implica calentar las piezas pintadas a temperaturas específicas, generalmente entre 180°C y 220°C, dependiendo del tipo de polvo utilizado. Durante este proceso, el polvo aplicado se funde y fluye para formar una película uniforme, la cual se adhiere firmemente al sustrato y ofrece protección contra la corrosión, el desgaste y otras agresiones externas.
El horno de curado debe mantener una temperatura uniforme en todo el recinto para evitar variaciones en el acabado. Los sistemas de control de temperatura y distribución de calor son críticos para asegurar que todas las piezas reciban el mismo nivel de tratamiento térmico, lo que a su vez garantiza un acabado consistente.
Tipos de hornos de curado para pintura electrostática
Existen varios tipos de hornos utilizados para curar la pintura electrostática:
- Hornos de convección forzada: Utilizan ventiladores para distribuir el calor de manera uniforme por todo el espacio del horno. Son ideales para grandes lotes de piezas de diferentes tamaños y formas.
- Hornos infrarrojos: Usan radiación infrarroja para calentar rápidamente las superficies, lo que reduce el tiempo de curado y aumenta la eficiencia energética. Son especialmente útiles para piezas más delgadas o cuando se requiere un tiempo de curado más corto.
- Hornos híbridos: Combinan convección e infrarrojos para ofrecer lo mejor de ambos mundos: la distribución uniforme del calor con la rapidez del calentamiento infrarrojo.
Ventajas del curado con hornos de pintura electrostática
- Alta durabilidad: El curado correcto en estos hornos asegura que el recubrimiento en polvo se adhiera de manera uniforme y duradera, lo que mejora la resistencia a la abrasión, la corrosión y el impacto.
- Acabado de alta calidad: La temperatura uniforme y controlada garantiza un acabado uniforme, sin imperfecciones como burbujas o zonas sin cubrir.
- Eficiencia energética: Los hornos modernos están diseñados para ser energéticamente eficientes, con sistemas de control avanzados que optimizan el consumo de energía sin comprometer la calidad del curado.
En resumen, los hornos de curado para pintura electrostática son esenciales para obtener acabados duraderos y de alta calidad en piezas pintadas con polvo. Su correcto funcionamiento y mantenimiento son clave para maximizar la productividad y la eficiencia del proceso de pintura.
Hornos Continuos de Curado para Pintura Electrostática
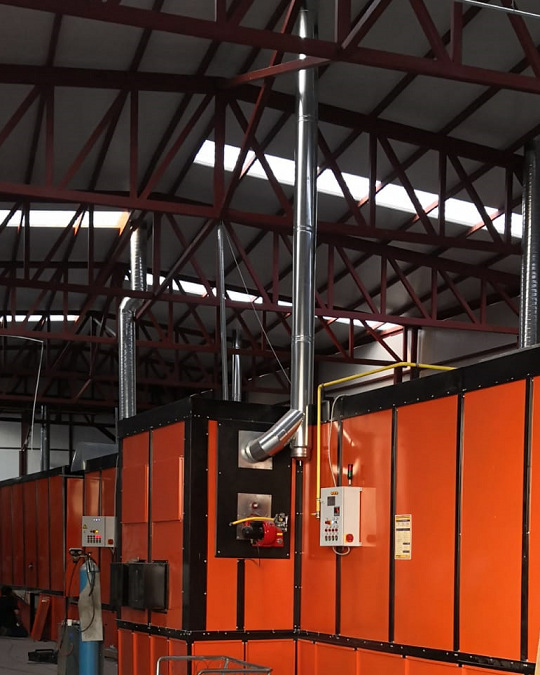
Los hornos continuos de curado para pintura electrostática están diseñados para líneas de producción de alta velocidad, donde se requiere un flujo constante de piezas a través del proceso de curado. Estos hornos permiten una mayor productividad al procesar grandes volúmenes de productos de manera continua, reduciendo los tiempos de inactividad y optimizando los recursos.
Funcionamiento de los hornos continuos
En este tipo de hornos, las piezas pintadas con polvo son transportadas automáticamente a través del horno mediante sistemas de transporte, como cadenas o rodillos. La velocidad del transportador y la temperatura del horno se configuran cuidadosamente para garantizar que cada pieza pase el tiempo necesario dentro del horno para un curado completo.
El diseño de los hornos continuos incluye zonas de calentamiento progresivo para permitir que las piezas se calienten de manera uniforme, evitando puntos calientes o fríos que puedan afectar el acabado final.
Aplicaciones industriales de los hornos continuos
Estos hornos son comúnmente utilizados en industrias que requieren altos volúmenes de producción, como la automotriz, la fabricación de electrodomésticos y la producción de componentes metálicos para la construcción. Gracias a su capacidad de manejar un flujo constante de piezas, los hornos continuos son ideales para entornos de producción donde se necesita minimizar el tiempo de ciclo y maximizar la eficiencia operativa.
Ventajas de los hornos continuos
- Mayor capacidad de producción: Estos hornos permiten el curado continuo de piezas sin interrupciones, lo que resulta en una mayor cantidad de productos procesados por hora.
- Eficiencia energética: El diseño optimizado de estos hornos permite un uso más eficiente de la energía, ya que el flujo constante de piezas reduce el tiempo necesario para recalentar el horno entre lotes.
- Curado uniforme: Los hornos continuos están diseñados para mantener temperaturas constantes a lo largo de todo el proceso, lo que asegura un curado uniforme en todas las piezas.
En conclusión, los hornos continuos de curado para pintura electrostática son esenciales para líneas de producción de gran escala, donde la velocidad, eficiencia y calidad del curado son fundamentales para cumplir con los requisitos de producción.
Hornos de Curado Tipo Batch
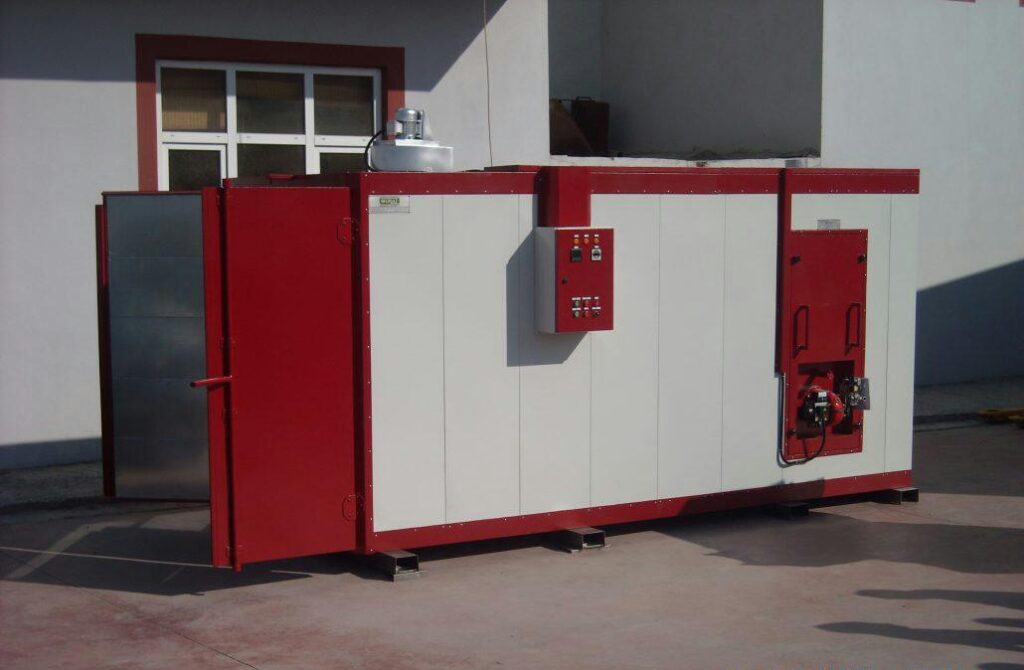
Los hornos de curado tipo batch son una alternativa eficiente para producciones de menor escala o cuando se requiere un curado específico de lotes de piezas individuales o personalizadas. Este tipo de hornos permite un control más preciso sobre el proceso de curado y es adecuado para empresas que no requieren una producción continua.
Características de los hornos tipo batch
Los hornos de curado tipo batch están diseñados para manejar lotes específicos de piezas, lo que significa que el horno se carga con un conjunto de piezas, se somete a un ciclo de curado, y luego las piezas son retiradas antes de cargar el siguiente lote. Estos hornos pueden ser manuales o semi-automáticos, dependiendo de las necesidades de producción.
Uno de los beneficios clave de los hornos tipo batch es la capacidad de ajustarse a diferentes tamaños y formas de piezas, lo que permite una gran flexibilidad. Además, son ideales para procesos que requieren un tiempo de curado más largo o específico, como ocurre con ciertos tipos de recubrimientos en polvo que requieren temperaturas o tiempos más precisos.
Ventajas del uso de hornos tipo batch
- Flexibilidad en la producción: Estos hornos permiten procesar piezas de diferentes tamaños y formas en un solo lote, lo que es ideal para producciones personalizadas o de baja escala.
- Control preciso del proceso: Los hornos tipo batch ofrecen un mayor control sobre el tiempo y la temperatura de curado, lo que garantiza que cada lote reciba el tratamiento adecuado.
- Eficiencia energética: A pesar de ser menos eficientes para producciones continuas, los hornos tipo batch son energéticamente eficientes cuando se utilizan para lotes específicos, ya que se evita la necesidad de mantener el horno en funcionamiento constante.
Los hornos tipo batch son una solución práctica y económica para empresas que no requieren la alta capacidad de producción de los hornos continuos, pero que buscan un curado preciso y de calidad.
Pistola Automática para Pintura Electrostática
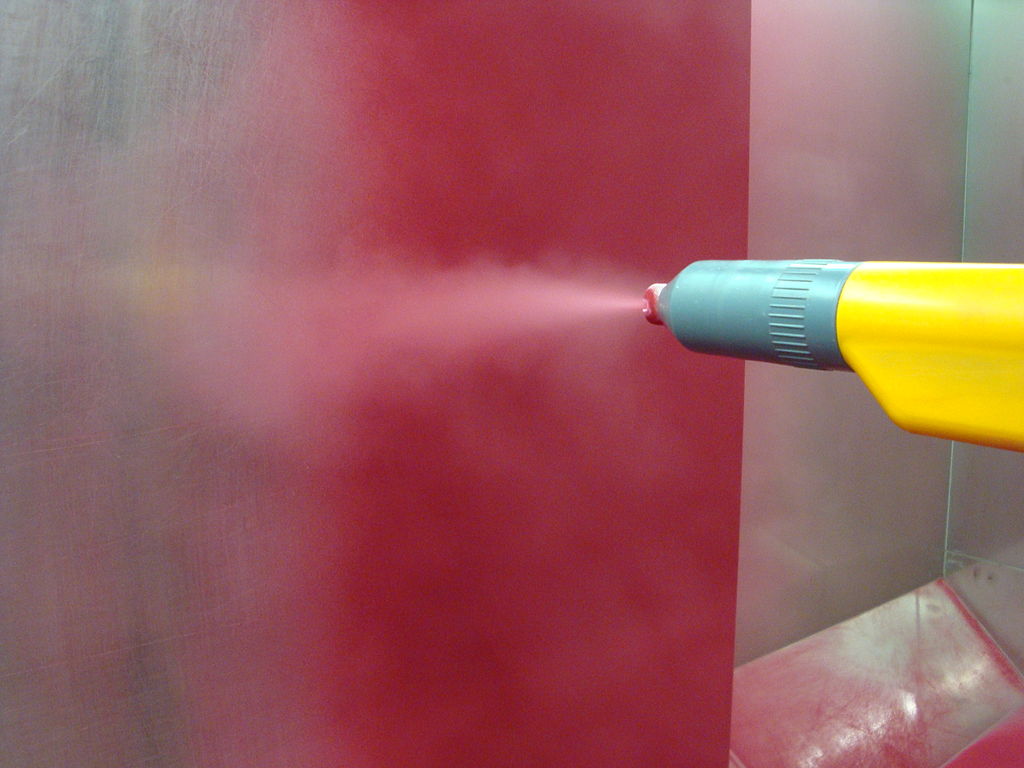
Las pistolas automáticas para pintura electrostática son equipos diseñados para aplicar el polvo de recubrimiento de manera eficiente y uniforme en superficies metálicas o conductoras. A diferencia de las pistolas manuales, las automáticas permiten un proceso continuo y controlado, lo que es ideal para entornos de producción de alta demanda.
Funcionamiento de la pistola automática
La pistola automática funciona cargando eléctricamente el polvo de pintura, que es atraído a la superficie de la pieza por la diferencia de carga entre el polvo y el objeto. Esta carga electrostática permite que el polvo se adhiera de manera uniforme a la superficie antes del proceso de curado.
El uso de pistolas automáticas garantiza una aplicación precisa del polvo, minimizando el desperdicio de material y asegurando que el recubrimiento cubra completamente todas las áreas del objeto, incluidas las zonas más difíciles de alcanzar.
Ventajas de la pistola automática para pintura electrostática
- Uniformidad en la aplicación: Al estar automatizadas, estas pistolas aplican el polvo de manera uniforme, lo que reduce la posibilidad de errores humanos y asegura un acabado consistente.
- Mayor velocidad de producción: Al automatizar el proceso de aplicación del polvo, se aumenta considerablemente la velocidad del proceso, lo que resulta en una mayor productividad en líneas de producción grandes.
- Eficiencia en el uso de material: Las pistolas automáticas están diseñadas para minimizar el desperdicio de polvo, lo que no solo reduce costos de operación, sino que también contribuye a un proceso más sostenible.
En resumen, las pistolas automáticas para pintura electrostática son una herramienta esencial para cualquier instalación que busque mejorar la calidad del recubrimiento y aumentar la eficiencia de su línea de producción.
Reciprocador para Pintura Electrostática
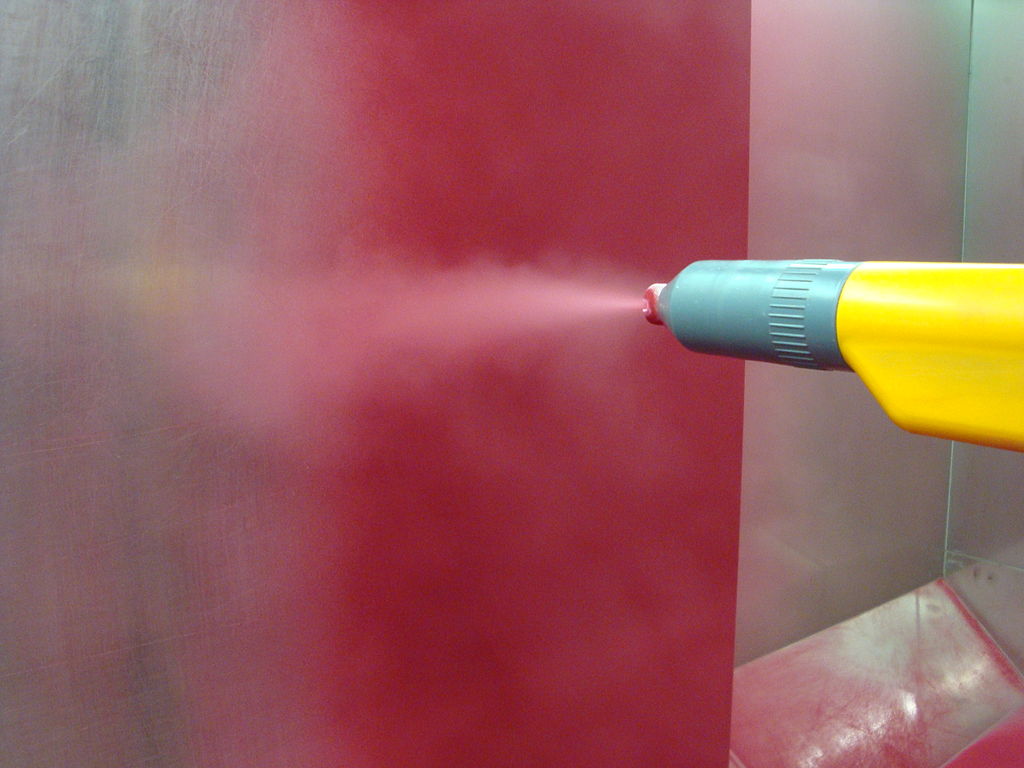
El reciprocador para pintura electrostática es un dispositivo que automatiza el movimiento de las pistolas de pintura electrostática en un plano vertical. Este equipo permite que las pistolas se muevan de manera controlada y repetitiva, asegurando una cobertura uniforme de las piezas en el proceso de recubrimiento en polvo.
Función del reciprocador
El reciprocador está diseñado para sostener varias pistolas automáticas de pintura electrostática, las cuales se mueven hacia arriba y hacia abajo siguiendo un patrón preestablecido. Este movimiento constante garantiza que el polvo se aplique de manera uniforme en toda la superficie del objeto, independientemente de su tamaño o forma.
El uso de un reciprocador es especialmente beneficioso en líneas de producción automáticas, donde se requiere que las pistolas cubran una gran cantidad de piezas con precisión y eficiencia.
Beneficios del reciprocador
- Cobertura uniforme: El movimiento repetitivo asegura que todas las áreas de la pieza reciban una capa uniforme de polvo, incluso en superficies irregulares o complejas.
- Reducción de mano de obra: El reciprocador automatiza el proceso de aplicación del polvo, lo que reduce la necesidad de intervención manual y aumenta la velocidad de producción.
- Optimización del tiempo: Gracias a su funcionamiento automatizado, el reciprocador optimiza el tiempo de aplicación, lo que permite que la línea de producción funcione de manera más fluida y rápida.
El reciprocador es un componente clave en sistemas de pintura electrostática automatizados, permitiendo una mayor eficiencia y mejor calidad en el recubrimiento de piezas industriales.
Equipos Electrostáticos
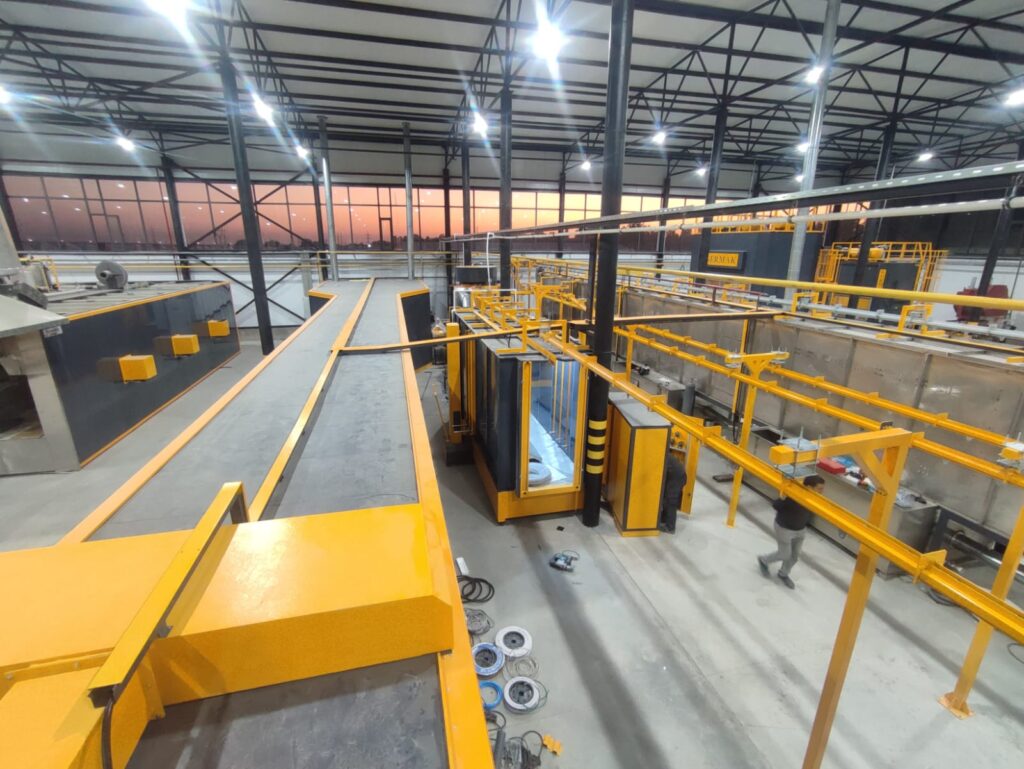
Los equipos electrostáticos son fundamentales en los procesos industriales de aplicación de recubrimientos, especialmente en la industria de la pintura. Estos equipos permiten una aplicación más precisa, eficiente y ecológica de materiales como la pintura en polvo o líquida sobre una variedad de superficies, utilizando el principio de la electrostática para atraer y adherir el recubrimiento a las superficies conductoras.
¿Qué Son los Equipos Electrostáticos?
Los equipos electrostáticos son sistemas diseñados para aplicar recubrimientos a través del uso de cargas eléctricas. Este método se basa en el principio de la electrostática, que consiste en la atracción de partículas cargadas hacia superficies opuestas con cargas contrarias. En el caso de la pintura electrostática, el recubrimiento (ya sea en polvo o líquido) recibe una carga eléctrica, mientras que la superficie a ser pintada se conecta a tierra, creando una diferencia de potencial que hace que las partículas de pintura se adhieran uniformemente a la superficie.
Este proceso tiene numerosas ventajas, ya que permite una aplicación más eficiente del recubrimiento, minimizando el desperdicio de material y mejorando la calidad del acabado. Además, al utilizar la carga electrostática, las partículas de pintura se distribuyen de manera uniforme incluso en superficies con formas complejas o difíciles de alcanzar.
Componentes de un Sistema Electrostático
Un sistema electrostático de aplicación de recubrimientos está compuesto por varios elementos clave que trabajan juntos para lograr una aplicación eficiente y controlada del material. Algunos de los componentes más importantes incluyen:
- Generador de carga electrostática: Este dispositivo genera la carga eléctrica que se transfiere a las partículas de pintura. El generador puede ajustar el voltaje según el tipo de recubrimiento y el material de la superficie a ser pintada, asegurando que la carga sea suficiente para una adhesión óptima.
- Pistola de aplicación: La pistola es la herramienta que se utiliza para aplicar la pintura cargada electrostáticamente sobre la superficie. Las pistolas electrostáticas pueden ser manuales o automáticas y están diseñadas para atomizar el recubrimiento y cargarlo eléctricamente antes de que alcance la pieza a ser recubierta.
- Sistema de alimentación de pintura: Este sistema suministra la pintura en polvo o líquida desde un depósito hasta la pistola de aplicación. En sistemas de pintura en polvo, este componente incluye un alimentador que controla la cantidad de polvo que se introduce en la pistola.
- Conexión a tierra: Las piezas que se van a recubrir deben estar conectadas a tierra para que puedan atraer las partículas de pintura cargadas. La conexión a tierra es fundamental para que el proceso funcione correctamente, ya que sin ella no habría una diferencia de potencial entre las partículas y la superficie, lo que impediría que la pintura se adhiriera de manera efectiva.
- Sistema de control: Los equipos electrostáticos modernos incluyen sistemas de control avanzados que permiten ajustar y monitorear todos los parámetros del proceso, desde el voltaje aplicado hasta la cantidad de pintura utilizada. Estos sistemas garantizan una aplicación uniforme y eficiente del recubrimiento.
Tipos de Equipos Electrostáticos
Existen diferentes tipos de equipos electrostáticos, diseñados para adaptarse a las necesidades específicas de cada aplicación. Los principales tipos incluyen:
- Equipos de pintura en polvo electrostática: Estos sistemas están diseñados específicamente para la aplicación de pintura en polvo, que se adhiere a la superficie mediante una carga electrostática y luego se cura en un horno. Los equipos de pintura en polvo son muy eficientes y permiten recubrir grandes volúmenes de piezas con una mínima pérdida de material.
- Equipos de pintura líquida electrostática: En estos sistemas, la pintura líquida es atomizada y cargada electrostáticamente antes de ser aplicada sobre la superficie. La pintura líquida es comúnmente utilizada en la industria automotriz y otras aplicaciones donde se requieren acabados muy detallados y de alta calidad.
- Pistolas automáticas y reciprocadores: Las pistolas automáticas se utilizan en líneas de producción donde la aplicación de pintura se realiza de manera continua y a gran escala. Los reciprocadores, por otro lado, son dispositivos automatizados que mueven las pistolas de aplicación de un lado a otro, asegurando una cobertura uniforme en toda la pieza.
Aplicaciones de los Equipos Electrostáticos
Los equipos electrostáticos tienen una amplia variedad de aplicaciones industriales debido a su eficiencia y versatilidad. Algunas de las industrias que más utilizan estos sistemas incluyen:
- Industria automotriz: En la fabricación de vehículos, los equipos electrostáticos se utilizan para aplicar pintura tanto en la carrocería como en otras piezas metálicas. La pintura electrostática proporciona una capa uniforme, resistente a la corrosión y con un acabado estéticamente agradable.
- Electrodomésticos: Los fabricantes de electrodomésticos utilizan sistemas electrostáticos para aplicar recubrimientos protectores en productos como refrigeradores, lavadoras y estufas. Estos recubrimientos no solo mejoran la durabilidad de los productos, sino que también les dan un acabado más atractivo.
- Mobiliario de metal: En la industria del mobiliario metálico, la pintura electrostática en polvo es ampliamente utilizada para recubrir sillas, mesas y estanterías, proporcionando una protección duradera contra el desgaste y la corrosión.
- Componentes industriales: En la fabricación de maquinaria y equipos industriales, los recubrimientos electrostáticos se utilizan para proteger las piezas metálicas de la corrosión y mejorar su resistencia a los elementos.
Beneficios de los Equipos Electrostáticos
El uso de equipos electrostáticos en la aplicación de recubrimientos ofrece varios beneficios importantes, tanto en términos de eficiencia como de calidad del producto final:
- Alta eficiencia de transferencia: El uso de cargas electrostáticas mejora la eficiencia de transferencia del recubrimiento, lo que significa que una mayor cantidad de pintura se adhiere a la superficie objetivo y menos se desperdicia en el proceso. Esto reduce los costos de material y mejora la sostenibilidad del proceso.
- Mejora de la calidad del acabado: La pintura electrostática se distribuye de manera uniforme sobre la superficie, lo que resulta en un acabado más suave y sin imperfecciones. Esto es especialmente importante en aplicaciones donde el aspecto estético es crucial, como en la industria automotriz y de electrodomésticos.
- Reducción del desperdicio: Dado que la pintura electrostática se adhiere mejor a la superficie, hay menos sobrepulverización y, por lo tanto, menos desperdicio de material. Esto no solo reduce los costos, sino que también minimiza el impacto ambiental del proceso.
- Seguridad y salud en el trabajo: Los sistemas electrostáticos minimizan la cantidad de polvo y vapor en el aire, lo que mejora las condiciones de trabajo y reduce el riesgo de exposición a sustancias potencialmente peligrosas para los trabajadores.
Desafíos en el Uso de Equipos Electrostáticos
A pesar de sus múltiples beneficios, el uso de equipos electrostáticos también presenta algunos desafíos que deben ser gestionados adecuadamente para asegurar un funcionamiento eficiente:
- Requiere una conexión a tierra adecuada: Para que el proceso funcione correctamente, las piezas deben estar bien conectadas a tierra. Si hay problemas con la conexión a tierra, la pintura no se adherirá de manera uniforme, lo que puede resultar en un acabado deficiente.
- Compatibilidad de materiales: La electrostática funciona mejor en superficies conductoras, por lo que puede haber dificultades al aplicar recubrimientos sobre materiales no conductores, como ciertos plásticos o maderas. En estos casos, se requieren tratamientos especiales o aditivos para mejorar la adhesión de la pintura.
- Costos iniciales: La inversión en equipos electrostáticos puede ser considerable, especialmente para pequeñas empresas o fábricas que recién comienzan a implementar este tipo de tecnología. Sin embargo, los ahorros a largo plazo en términos de eficiencia y reducción de desperdicios suelen justificar la inversión inicial.
Innovaciones en Equipos Electrostáticos
En los últimos años, ha habido importantes avances en la tecnología de equipos electrostáticos, dirigidos a mejorar la eficiencia, la precisión y la sostenibilidad del proceso. Algunas de las innovaciones más recientes incluyen:
- Sistemas automatizados: El uso de robots y sistemas automatizados ha permitido mejorar la precisión de la aplicación de pintura electrostática, especialmente en líneas de producción masivas. Estos sistemas son capaces de ajustar automáticamente la cantidad de pintura aplicada y los parámetros del proceso, lo que reduce los errores y optimiza el uso de material.
- Mejoras en la eficiencia energética: Los equipos electrostáticos modernos están diseñados para consumir menos energía, lo que no solo reduce los costos operativos, sino que también contribuye a un menor impacto ambiental.
- Control inteligente del proceso: Los sistemas de control inteligentes permiten monitorear en tiempo real todos los aspectos del proceso de aplicación de pintura, desde el voltaje de carga hasta la cantidad de material utilizado. Esto garantiza una mayor precisión y uniformidad en el acabado final.
Sostenibilidad en el Uso de Equipos Electrostáticos
El uso de equipos electrostáticos contribuye a una mayor sostenibilidad en los procesos industriales, ya que permite reducir el consumo de materiales y energía. Además, al minimizar la cantidad de sobrepulverización y desperdicio de pintura, se reduce la generación de residuos y el impacto ambiental del proceso.
Relevancia en la Industria Moderna
En la industria moderna, la pintura en polvo se ha convertido en una tecnología esencial para el acabado de productos. Su capacidad para adaptarse a una amplia gama de materiales, desde metales hasta plásticos, la hace versátil y adecuada para numerosas aplicaciones. Además, su eficiencia y su menor impacto ambiental la convierten en una opción preferida para las empresas que buscan mejorar su sostenibilidad y reducir los costos operativos.
El uso de equipos de aplicación de pintura en polvo ha permitido a las empresas mejorar la calidad de sus productos al mismo tiempo que optimizan sus procesos de fabricación. La implementación de tecnologías avanzadas, como los sistemas automatizados de aplicación y los controles de calidad en tiempo real, ha llevado a un nivel superior de precisión y consistencia en los recubrimientos aplicados.
Principios de la Pintura en Polvo
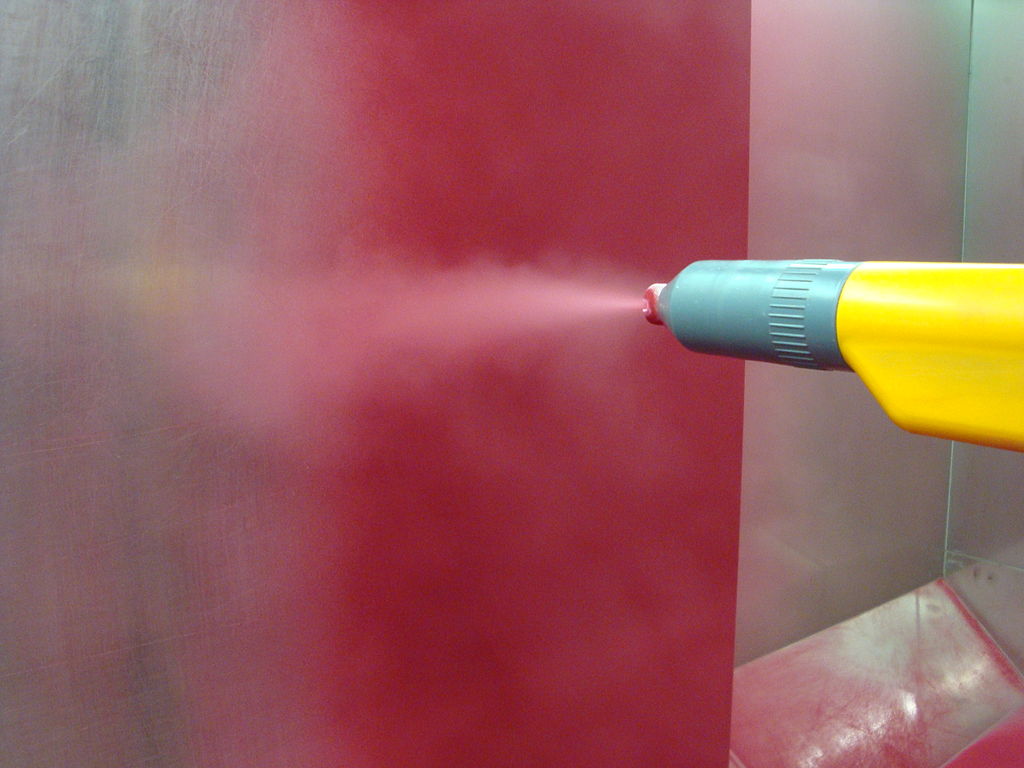
Fundamentos Físicos y Químicos
El proceso de aplicación de pintura en polvo se basa en principios físicos y químicos específicos que permiten la adherencia del polvo a la superficie del sustrato y la formación de un recubrimiento sólido y duradero después del curado. La clave del proceso es la carga electrostática que se aplica al polvo, lo que provoca que las partículas se adhieran al sustrato, que generalmente está conectado a tierra.
El polvo de pintura se compone de partículas finas de resinas, pigmentos, y aditivos, que al ser pulverizadas a través de una pistola electrostática, adquieren una carga eléctrica. Estas partículas cargadas buscan adherirse a la superficie del sustrato, creando una capa uniforme. Una vez aplicado, el objeto se introduce en un horno de curado, donde el calor hace que las partículas de polvo se fundan y formen una película continua.
Una Planta Automática de Pintura en Polvo Industrial es una instalación diseñada para aplicar recubrimientos en polvo a diversas piezas y componentes metálicos mediante un proceso automatizado. Este tipo de plantas se utiliza ampliamente en sectores industriales como el automotriz, electrodoméstico, y de maquinaria pesada, debido a las ventajas que ofrece la pintura en polvo, como mayor durabilidad, acabado uniforme y resistencia a la corrosión.
El proceso de una Planta Automática de Pintura en Polvo comienza con la preparación de las piezas, que incluye la limpieza y desengrasado para asegurar que la superficie esté libre de contaminantes que puedan afectar la adherencia del polvo. Esta etapa es crucial, ya que una superficie bien preparada garantiza un recubrimiento de calidad y una larga vida útil del producto final.
Una vez limpias, las piezas se dirigen al sistema de aplicación de polvo. Este sistema suele estar compuesto por una cabina de pulverización donde se aplica el polvo mediante pistolas electrostáticas. El polvo se adhiere a las piezas gracias a una carga eléctrica que se genera en el proceso, lo que permite un recubrimiento uniforme incluso en áreas de difícil acceso. Las cabinas de pulverización están diseñadas para minimizar el desperdicio de polvo, permitiendo su recuperación y reutilización, lo que hace que el proceso sea más eficiente y ecológico.
Después de la aplicación del polvo, las piezas se trasladan a un horno de curado. En este horno, las piezas se someten a altas temperaturas que permiten que el polvo se derrita y se adhiera de manera permanente a la superficie, formando una capa sólida y resistente. El tiempo y la temperatura del curado son controlados con precisión para asegurar un acabado de alta calidad. La consistencia en el curado es fundamental para obtener propiedades óptimas del recubrimiento, como la dureza, la resistencia química y el brillo.
El control y la automatización de una Planta Automática de Pintura en Polvo son esenciales para maximizar la eficiencia y la calidad. Los sistemas automatizados permiten un control preciso de cada etapa del proceso, reduciendo la variabilidad y los errores humanos. Además, los sistemas de monitoreo en tiempo real aseguran que el proceso se mantenga dentro de los parámetros establecidos, lo que resulta en un producto final consistente y de alta calidad.
El diseño de una Planta Automática de Pintura en Polvo también debe considerar aspectos de seguridad y sostenibilidad. La manipulación de polvos y el uso de hornos de alta temperatura requieren medidas de seguridad estrictas para proteger a los trabajadores y evitar accidentes. Asimismo, la planta debe cumplir con las normativas medioambientales, lo que implica un control adecuado de las emisiones y el manejo responsable de los residuos.
En resumen, una Planta Automática de Pintura en Polvo Industrial es una instalación compleja que integra tecnología avanzada y procesos controlados para ofrecer recubrimientos duraderos y de alta calidad en piezas metálicas. La eficiencia, la automatización y el enfoque en la sostenibilidad son claves para el éxito de estas plantas en la industria moderna.
Planta Automática de Pintura
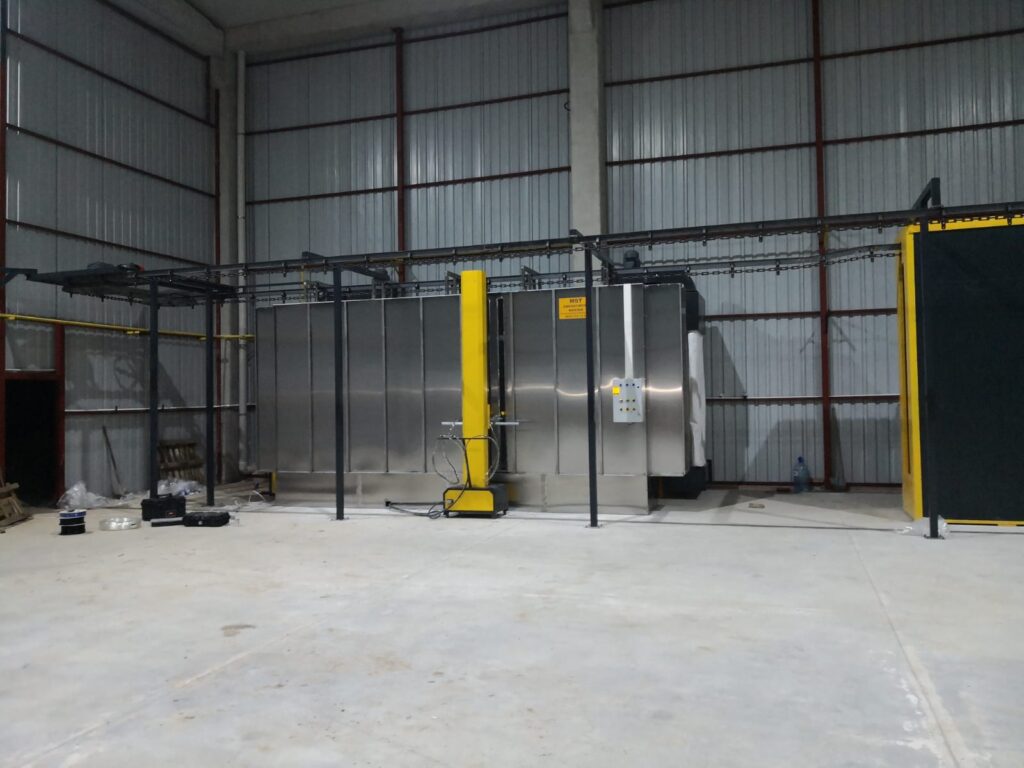
Además de los aspectos técnicos, una Planta Automática de Pintura en Polvo debe estar diseñada para manejar grandes volúmenes de producción, adaptándose a las necesidades específicas de cada cliente o industria. Esto implica la personalización de las líneas de pintura para distintos tamaños y formas de piezas, así como la flexibilidad para cambiar rápidamente entre diferentes colores o tipos de recubrimientos en polvo. Esta flexibilidad es fundamental en un entorno industrial donde la demanda puede variar y la capacidad de respuesta rápida a las necesidades del mercado es una ventaja competitiva clave.
El uso de sistemas de transporte automatizados es otra característica distintiva de estas plantas. Estos sistemas, como las cintas transportadoras o los transportadores aéreos, mueven las piezas de una etapa a otra del proceso de manera eficiente, reduciendo el tiempo de manipulación manual y mejorando la consistencia del proceso. La sincronización de estos sistemas es crítica para asegurar que cada pieza pase por cada etapa del proceso en el momento adecuado, evitando cuellos de botella y asegurando un flujo de trabajo constante.
En términos de mantenimiento, las Plantas Automáticas de Pintura en Polvo requieren una gestión cuidadosa para garantizar su operación continua y eficiente. El mantenimiento preventivo es esencial para evitar fallos en los equipos y asegurar que las líneas de producción no sufran interrupciones. Esto incluye la limpieza regular de las cabinas de pulverización, el mantenimiento de las pistolas electrostáticas, y la revisión de los hornos de curado. Además, el mantenimiento de los sistemas de recuperación de polvo es crucial para mantener la eficiencia y minimizar el desperdicio de materiales.
La tecnología juega un papel central en la operación de estas plantas. Los sistemas de control avanzado permiten la supervisión y el ajuste de parámetros clave en tiempo real, lo que mejora la calidad del producto y reduce el desperdicio. El uso de sensores y software de monitoreo permite a los operadores detectar y corregir problemas rápidamente, asegurando que el proceso se mantenga dentro de los estándares de calidad.
Además, la integración de soluciones de Industria 4.0, como el Internet de las Cosas (IoT) y el análisis de datos, está transformando la manera en que operan las Plantas Automáticas de Pintura en Polvo. Estas tecnologías permiten una mayor conectividad entre los distintos componentes de la planta, proporcionando datos en tiempo real sobre el rendimiento de los equipos, el consumo de energía, y la calidad del recubrimiento. Este enfoque basado en datos permite una toma de decisiones más informada y una mejora continua del proceso.
La formación y capacitación del personal también es fundamental en la operación de una Planta Automática de Pintura en Polvo. Los operadores deben estar bien entrenados en el manejo de los sistemas automatizados, así como en las medidas de seguridad necesarias para trabajar con materiales y equipos potencialmente peligrosos. Un personal bien capacitado es clave para asegurar que la planta funcione de manera segura y eficiente, y para mantener la calidad del producto final.
En conclusión, una Planta Automática de Pintura en Polvo Industrial es un ejemplo de cómo la tecnología y la automatización pueden mejorar significativamente la eficiencia y la calidad en la industria manufacturera. Desde la preparación de las piezas hasta el curado del recubrimiento, cada etapa del proceso está diseñada para maximizar la eficiencia, minimizar el desperdicio, y asegurar un acabado de alta calidad. Con el avance continuo de la tecnología, estas plantas seguirán evolucionando, ofreciendo nuevas oportunidades para mejorar la productividad y la sostenibilidad en la industria.
A medida que las demandas del mercado continúan cambiando y las expectativas de los consumidores evolucionan, las Plantas Automáticas de Pintura en Polvo también deben adaptarse. La personalización de los acabados y la capacidad de ofrecer una variedad más amplia de colores y texturas son cada vez más importantes en muchos sectores. Esta flexibilidad es facilitada por los avances en la tecnología de pulverización y curado, lo que permite un mayor control sobre los resultados estéticos y funcionales del recubrimiento.
El futuro de las Plantas Automáticas de Pintura en Polvo también está estrechamente ligado a la sostenibilidad ambiental. A medida que las regulaciones medioambientales se vuelven más estrictas, las plantas deben ser cada vez más conscientes del impacto ecológico de sus operaciones. Esto implica no solo el uso de recubrimientos más ecológicos, como los que no contienen compuestos orgánicos volátiles (COV), sino también la mejora de los sistemas de reciclaje de polvo y la gestión eficiente de los residuos. El reciclaje del polvo, que antes se consideraba un desafío, se ha convertido en una práctica común en las plantas más modernas, ya que permite reducir el desperdicio de material y minimizar la contaminación del aire.
Otra área importante es la reducción del consumo de energía. Las plantas automatizadas deben optimizar sus operaciones para usar la menor cantidad de energía posible sin comprometer la calidad del proceso. Esto incluye la mejora de la eficiencia energética de los hornos de curado, la optimización de la iluminación y los sistemas de ventilación, y la utilización de fuentes de energía renovables cuando sea posible. Algunas instalaciones también están implementando tecnologías de recuperación de calor, lo que les permite reutilizar la energía térmica generada en el proceso para otras etapas de la producción, reduciendo así el consumo global de energía.
Además, la trazabilidad y la transparencia en el proceso de producción están ganando relevancia. Los consumidores y las industrias están cada vez más interesados en conocer el origen de los materiales, el proceso de fabricación y el impacto ambiental de los productos que compran. Las plantas automáticas de pintura en polvo pueden beneficiarse de la implementación de sistemas de gestión de calidad certificados, que permiten un seguimiento completo de cada pieza, desde su entrada en la planta hasta el producto final, lo que ofrece una mayor confianza a los clientes y facilita la auditoría de las operaciones.
El análisis predictivo es otro componente emergente en estas plantas. Al integrar algoritmos de inteligencia artificial y machine learning, las plantas pueden anticipar fallos en los equipos antes de que ocurran, optimizar el mantenimiento y mejorar la calidad del producto final. Los sistemas de inteligencia artificial también pueden ayudar a predecir patrones de demanda, permitiendo una producción más eficiente y adaptada a las necesidades del mercado.
El papel de la automatización en la reducción de costos también es fundamental. Con el aumento de la complejidad de los procesos industriales, las Plantas Automáticas de Pintura en Polvo permiten a las empresas reducir los costos asociados con la mano de obra, el tiempo de producción y el consumo de materiales. La automatización de tareas repetitivas y la integración de procesos también hacen posible que las empresas ofrezcan productos de alta calidad a precios más competitivos, lo que es esencial para mantenerse a la vanguardia en mercados globales cada vez más exigentes.
Finalmente, el aspecto de la seguridad sigue siendo una prioridad en las operaciones de las plantas. La manipulación de productos químicos, la exposición a temperaturas extremas en los hornos y el trabajo con equipos pesados requieren estrictos protocolos de seguridad. Las plantas de pintura en polvo están implementando tecnologías avanzadas, como sensores de seguridad, monitoreo remoto de condiciones y sistemas de alarma, para minimizar los riesgos y garantizar un entorno de trabajo seguro para los empleados.
En resumen, las Plantas Automáticas de Pintura en Polvo Industriales están en constante evolución, impulsadas por la innovación tecnológica, las necesidades del mercado y las exigencias medioambientales. A medida que la automatización, la sostenibilidad y la personalización se convierten en prioridades clave, estas plantas seguirán mejorando su eficiencia, reduciendo costos y ofreciendo productos de mayor calidad. La integración de nuevas tecnologías y la constante adaptación a las demandas del mercado garantizarán que las plantas de pintura en polvo continúen siendo una parte vital de la fabricación industrial en las próximas décadas.
1. Innovación y Avances Tecnológicos en las Plantas Automáticas de Pintura en Polvo
Las plantas automáticas de pintura en polvo están experimentando avances tecnológicos que mejoran la precisión, la velocidad y la calidad del recubrimiento. Uno de los desarrollos más notables es la incorporación de sistemas de control avanzado basados en la inteligencia artificial (IA) y el aprendizaje automático. Estos sistemas son capaces de ajustar dinámicamente las condiciones del proceso en función de datos en tiempo real, optimizando los parámetros de aplicación, como la cantidad de polvo, la carga eléctrica y la velocidad de la línea. Además, la implementación de robots de pulverización avanzados ha permitido un control aún más preciso, mejorando la cobertura uniforme de las piezas, especialmente en formas complejas o de difícil acceso.
El uso de sistemas de visión artificial también ha mejorado la calidad del proceso, permitiendo la inspección continua de las piezas en busca de defectos y ajustes automáticos del proceso. Esto no solo garantiza un acabado de alta calidad, sino que también minimiza el desperdicio de material y mejora la eficiencia general de la planta.
2. Sostenibilidad y Eficiencia Energética en la Planta
Con la creciente preocupación por el impacto ambiental, las plantas automáticas de pintura en polvo están adoptando tecnologías más ecológicas y sostenibles. El uso de recubrimientos sin compuestos orgánicos volátiles (COV) ha ganado popularidad, ya que estos materiales no solo son más seguros para los trabajadores, sino que también reducen las emisiones contaminantes al medio ambiente. Además, la mejora en los sistemas de recuperación de polvo ha permitido reducir el desperdicio de material, recuperando el polvo no aplicado y reintroduciéndolo en el proceso, lo que reduce tanto los costos operativos como la huella ambiental.
La eficiencia energética también es una prioridad. Las plantas modernas están adoptando tecnologías como hornos de curado de alta eficiencia energética, que utilizan menos energía para alcanzar las temperaturas necesarias para el proceso de curado. Algunas plantas también están implementando sistemas de recuperación de calor, lo que les permite aprovechar la energía térmica generada durante el proceso para calentar otras áreas de la planta, reduciendo aún más el consumo energético.
3. Personalización de Productos y Flexibilidad en la Producción
Uno de los principales beneficios de las plantas automáticas de pintura en polvo es la capacidad de adaptarse a diversas demandas de personalización. En sectores como la industria automotriz y de electrodomésticos, la capacidad de ofrecer una variedad de colores, acabados y texturas es esencial. Las plantas de pintura en polvo han mejorado sus capacidades de cambio rápido entre diferentes colores y tipos de recubrimientos, reduciendo el tiempo necesario para realizar estos cambios y minimizando los residuos generados durante el proceso de transición.
Además, la flexibilidad de las líneas de producción automatizadas permite a las plantas adaptarse rápidamente a los cambios en la demanda del mercado. Las plantas pueden ajustar la velocidad de la línea de producción o el tipo de recubrimiento utilizado sin afectar la calidad o la eficiencia del proceso, lo que les permite mantener la competitividad en un mercado global de rápido cambio.
4. Seguridad Laboral y Protección en el Proceso
La seguridad en las plantas automáticas de pintura en polvo es de suma importancia debido a los riesgos asociados con la manipulación de productos químicos, las altas temperaturas y la maquinaria pesada. Para mitigar estos riesgos, las plantas implementan estrictos protocolos de seguridad, como sistemas de ventilación avanzada para asegurar la circulación de aire limpio y la eliminación de vapores tóxicos. Las cabinas de pulverización están diseñadas con sistemas de filtrado para evitar la exposición a partículas finas de polvo y asegurar que el aire dentro de la planta esté limpio.
Además, el monitoreo en tiempo real de las condiciones de trabajo mediante sensores de seguridad y sistemas de alarmas automáticas ha mejorado la capacidad para identificar problemas antes de que se conviertan en situaciones peligrosas. Las tecnologías de monitoreo remoto también permiten a los operadores supervisar las condiciones de la planta desde cualquier ubicación, lo que aumenta la eficiencia y la seguridad al permitir una rápida respuesta ante cualquier eventualidad.
5. Impacto de la Automatización en la Competitividad del Mercado
La automatización no solo mejora la eficiencia, sino que también juega un papel crucial en la competitividad de las empresas. La automatización de procesos repetitivos reduce la dependencia de la mano de obra, lo que permite una reducción de los costos laborales y una mayor consistencia en la calidad del producto. Al mismo tiempo, la mayor velocidad de producción permite a las plantas cumplir con plazos más cortos, lo que es crucial para satisfacer las expectativas del cliente en un mercado global altamente competitivo.
La capacidad de las plantas automáticas de pintura en polvo para optimizar el uso de materiales y minimizar el desperdicio también contribuye significativamente a reducir los costos operativos. La mejora en la precisión y la personalización de los recubrimientos permite a las empresas ofrecer productos de mayor calidad a precios competitivos, lo que les permite posicionarse mejor frente a la competencia y ganar participación en el mercado. La automatización también facilita la integración de procesos adicionales, como el almacenamiento y la distribución, en una cadena de producción continua, lo que mejora aún más la eficiencia y reduce los tiempos de entrega.
Innovación y Avances Tecnológicos en las Plantas Automáticas de Pintura en Polvo
La innovación y los avances tecnológicos en las Plantas Automáticas de Pintura en Polvo han transformado significativamente la forma en que se gestionan los procesos de recubrimiento industrial. Estas mejoras han permitido aumentar la eficiencia, reducir los costos operativos, mejorar la calidad del acabado y adaptarse a las crecientes demandas del mercado. El principal avance tecnológico en este tipo de plantas ha sido la integración de sistemas de automatización que permiten una gestión precisa y eficiente de las diferentes etapas del proceso de pintura. La automatización no solo reduce la intervención humana, sino que también asegura un control de calidad más consistente y menos susceptible a errores.
Uno de los avances más destacados es la incorporación de robots de pulverización. Estos robots están equipados con sistemas de control avanzado que permiten una aplicación del polvo más precisa y uniforme. Gracias a la capacidad de estos robots para ajustar automáticamente la distancia, el ángulo y la velocidad de pulverización, se consigue una cobertura más homogénea en todo tipo de piezas, incluso en aquellas con formas complejas o de difícil acceso. Esta precisión no solo mejora la calidad del acabado, sino que también reduce el desperdicio de material, ya que el polvo es depositado únicamente en las áreas necesarias, lo que aumenta la eficiencia y reduce los costos operativos.
El uso de sistemas de visión artificial es otro avance importante en las plantas automáticas de pintura en polvo. Estos sistemas permiten realizar una inspección continua de las piezas en tiempo real, detectando imperfecciones o irregularidades en el recubrimiento antes de que las piezas pasen a la siguiente etapa del proceso. La integración de estas tecnologías ha permitido que las plantas identifiquen problemas de calidad de forma temprana, lo que facilita la corrección de errores en el proceso sin afectar la producción. Los sistemas de visión artificial también contribuyen a la mejora del control de calidad, garantizando que cada pieza cumpla con los estándares establecidos.
Además, la implementación de tecnologías de inteligencia artificial (IA) y aprendizaje automático está comenzando a jugar un papel crucial en la optimización de las operaciones. Estos sistemas pueden analizar grandes cantidades de datos generados durante el proceso de pintura para identificar patrones y hacer predicciones sobre el rendimiento de los equipos. Por ejemplo, pueden anticipar posibles fallos en los componentes de la planta antes de que ocurran, lo que permite llevar a cabo un mantenimiento predictivo que minimiza el tiempo de inactividad y reduce los costos de reparación. Además, los algoritmos de IA pueden ajustar en tiempo real los parámetros del proceso, como la cantidad de polvo utilizado, la temperatura de los hornos de curado o la velocidad de la línea de producción, para mejorar la eficiencia energética y asegurar la calidad del recubrimiento.
La mejora en los sistemas de recuperación de polvo es otro avance tecnológico significativo en las plantas automáticas de pintura en polvo. Estos sistemas permiten recuperar el polvo no utilizado durante el proceso de pulverización, lo que reduce el desperdicio de material y hace que el proceso sea más sostenible. El polvo recuperado puede ser reutilizado en su totalidad, lo que no solo minimiza los costos operativos, sino que también ayuda a reducir el impacto ambiental de la planta al disminuir la cantidad de material que se desecha. La eficiencia de los sistemas de recuperación ha mejorado considerablemente con la incorporación de nuevas tecnologías de filtración y separación, lo que ha permitido un proceso más limpio y económico.
En cuanto al curado de las piezas pintadas, los avances en la tecnología de hornos de curado han permitido un control más preciso de la temperatura y la distribución del calor. Esto ha resultado en una mayor uniformidad en el curado de las piezas, lo que garantiza que el recubrimiento sea de alta calidad y tenga una mayor durabilidad. Los hornos de curado modernos también son más eficientes desde el punto de vista energético, utilizando menos energía para alcanzar las temperaturas necesarias y reduciendo los costos operativos de la planta. Algunos de estos hornos incluso incorporan sistemas de recuperación de calor, lo que permite reutilizar la energía térmica generada durante el proceso para calentar otras partes de la planta, mejorando aún más la eficiencia energética.
Además de la mejora en los equipos, los avances tecnológicos en las Plantas Automáticas de Pintura en Polvo también han afectado la forma en que se gestionan los procesos a nivel de software. Los sistemas de control de procesos basados en software ahora pueden integrar todas las etapas de producción en una única plataforma, lo que permite a los operadores supervisar y ajustar todos los parámetros desde un solo lugar. Estos sistemas proporcionan información en tiempo real sobre el rendimiento de los equipos, la calidad del recubrimiento y el consumo de materiales, lo que facilita la toma de decisiones informadas y mejora la eficiencia general de la planta.
El uso de tecnologías de conectividad y monitoreo remoto también ha mejorado la gestión de las plantas automáticas de pintura en polvo. Los operadores ahora pueden supervisar las condiciones de la planta y los equipos desde cualquier ubicación, lo que permite una respuesta rápida ante cualquier problema y mejora la capacidad de intervención en tiempo real. Además, la implementación de soluciones basadas en la nube permite almacenar y analizar grandes volúmenes de datos generados durante el proceso, lo que facilita la optimización continua y el aprendizaje a largo plazo.
En conjunto, estos avances tecnológicos están transformando las plantas automáticas de pintura en polvo, haciéndolas más eficientes, precisas y sostenibles. La integración de la automatización, la inteligencia artificial, la visión artificial y la conectividad en tiempo real está llevando a la industria a un nivel de rendimiento y competitividad nunca antes alcanzado. Estos desarrollos no solo mejoran la calidad del producto final, sino que también reducen los costos operativos, minimizan el desperdicio y permiten una mayor flexibilidad para adaptarse a las cambiantes demandas del mercado. Con la continua evolución de estas tecnologías, las plantas de pintura en polvo seguirán desempeñando un papel clave en la fabricación de productos de alta calidad en una variedad de sectores industriales.
Además de los avances mencionados, la digitalización de las Plantas Automáticas de Pintura en Polvo está marcando una nueva era en la optimización de los procesos. La introducción de la Industria 4.0 ha permitido que las plantas adopten sistemas interconectados que facilitan la gestión y el control de los procesos de manera más eficiente y precisa. A través de la recopilación masiva de datos generados por los sensores de las máquinas, los sistemas de control y los equipos de pulverización, es posible realizar análisis detallados y en tiempo real sobre el desempeño de cada componente de la planta. Esto no solo optimiza el rendimiento operativo, sino que también proporciona a los gerentes y operadores una visión más clara de cómo se puede mejorar la producción.
La implementación de sensores de alta precisión en las diversas fases del proceso, desde la preparación de las piezas hasta el curado, está permitiendo a las plantas realizar ajustes automáticos para asegurar que el recubrimiento se aplique de la manera más eficiente posible. Estos sensores monitorean factores como la temperatura, la humedad, el flujo de aire, y la concentración de polvo, asegurando que todas las condiciones se mantengan dentro de los parámetros ideales. En caso de que los datos de estos sensores se desvíen de los valores predeterminados, los sistemas automatizados pueden realizar ajustes inmediatos sin intervención humana, lo que minimiza los errores y mejora la consistencia del producto.
Otro aspecto clave en la evolución de las plantas automáticas de pintura en polvo es la optimización del tiempo de inactividad y los ciclos de mantenimiento. La implementación de tecnologías de mantenimiento predictivo, basadas en el análisis de datos de sensores y el aprendizaje automático, permite anticipar posibles fallos en los equipos antes de que ocurran, lo que reduce significativamente el tiempo de inactividad no planificado. Este enfoque ayuda a maximizar la utilización de los equipos, minimizando el impacto de los fallos y asegurando que las plantas continúen operando de manera eficiente.
El software de gestión avanzado que controla estos sistemas interconectados puede analizar patrones históricos y actuales de funcionamiento de la planta, lo que permite realizar predicciones y generar alertas sobre posibles fallos en los equipos. Esta información también puede ser utilizada para realizar mantenimiento preventivo, programado en momentos óptimos, cuando la producción es más baja o cuando las líneas de producción pueden ser detenidas sin afectar el flujo de trabajo. Este tipo de enfoque proactivo no solo reduce los costos de mantenimiento, sino que también mejora la vida útil de los equipos y asegura un rendimiento constante.
Otro avance importante ha sido el desarrollo de nuevos tipos de recubrimientos en polvo que ofrecen mayores beneficios tanto en términos de rendimiento como de sostenibilidad. Los recubrimientos en polvo avanzados están siendo diseñados para ofrecer mayor resistencia a la abrasión, la corrosión, y la intemperie, lo que los hace ideales para una variedad de aplicaciones industriales. A su vez, muchos de estos recubrimientos están formulados para ser más ecológicos, utilizando ingredientes menos contaminantes y reduciendo la huella ambiental de las plantas de pintura. Estos recubrimientos también pueden ser más fáciles de aplicar, lo que reduce la complejidad del proceso y mejora la eficiencia general.
Además, las nuevas formulaciones de polvo están mejorando la versatilidad de las plantas automáticas de pintura, permitiendo la aplicación de recubrimientos con diferentes acabados estéticos, como acabados mate, satinados o brillantes, sin necesidad de modificaciones importantes en el equipo. Esta flexibilidad permite a las empresas diversificar su oferta de productos y adaptarse mejor a las demandas específicas de los consumidores o de los sectores industriales.
El impacto de la tecnología de automatización no solo se limita al proceso de aplicación de la pintura, sino también a la gestión logística dentro de la planta. Los sistemas automatizados de transporte, como las cintas transportadoras y los robots autónomos, están permitiendo mover las piezas a través de las diversas etapas de producción de manera más rápida y precisa. Estos sistemas pueden ser programados para dirigir las piezas hacia diferentes rutas dependiendo de las necesidades específicas de cada trabajo, lo que aumenta la eficiencia y reduce los tiempos de espera.
La integración de tecnologías de simulación avanzada también está ayudando a las plantas a optimizar sus procesos. Los sistemas de simulación permiten a los ingenieros probar diferentes configuraciones de producción y técnicas de aplicación antes de implementarlas en la planta real. Esto permite identificar posibles cuellos de botella, mejorar la distribución de los recursos y optimizar el flujo de trabajo. Además, las simulaciones pueden ayudar a predecir cómo las modificaciones en los parámetros de la línea de producción afectarán la calidad del producto, lo que facilita la toma de decisiones informadas.
Finalmente, la incorporación de la realidad aumentada (RA) y la realidad virtual (RV) en las plantas automáticas de pintura en polvo está proporcionando nuevas formas de capacitación y mantenimiento. Los operadores pueden utilizar gafas de RA para recibir información en tiempo real sobre los procesos de producción, lo que mejora la eficiencia y la toma de decisiones. Por ejemplo, si un operador necesita ajustar un parámetro de la línea de producción, puede consultar las instrucciones a través de un visor de RA mientras realiza la tarea. En cuanto a la capacitación, las simulaciones de RV permiten a los nuevos empleados aprender a operar el equipo de manera segura y eficiente sin tener que intervenir en la planta real.
En resumen, los avances tecnológicos en las Plantas Automáticas de Pintura en Polvo están revolucionando todos los aspectos de la producción, desde la aplicación del recubrimiento hasta el mantenimiento de los equipos. La integración de tecnologías de automatización, inteligencia artificial, sensores avanzados, y sistemas de gestión de datos en tiempo real está transformando la industria, permitiendo una producción más eficiente, flexible y sostenible. A medida que estas tecnologías continúan evolucionando, las plantas de pintura en polvo seguirán siendo una parte fundamental de la fabricación industrial moderna, ofreciendo soluciones de recubrimiento de alta calidad para una amplia gama de aplicaciones.
Sostenibilidad y Eficiencia Energética en la Planta
La sostenibilidad y la eficiencia energética son aspectos clave en la operación de las Plantas Automáticas de Pintura en Polvo, especialmente en un contexto donde las empresas buscan minimizar su impacto ambiental y reducir los costos operativos. Estas plantas, que a menudo operan en ciclos continuos y utilizan grandes cantidades de energía, están adoptando diversas tecnologías y estrategias para hacer más eficientes sus procesos y reducir su huella ecológica. A medida que las normativas medioambientales se vuelven más estrictas y los consumidores se vuelven más conscientes del impacto de la producción industrial, las plantas de pintura en polvo se ven obligadas a incorporar prácticas más sostenibles sin comprometer la calidad del producto ni la rentabilidad.
Uno de los enfoques más comunes para mejorar la sostenibilidad en estas plantas es la optimización del uso de energía. Los hornos de curado, que son una parte esencial del proceso de pintura en polvo, consumen grandes cantidades de energía para alcanzar las altas temperaturas necesarias para curar los recubrimientos. Para abordar este desafío, muchas plantas están invirtiendo en hornos más eficientes energéticamente, que no solo alcanzan temperaturas más rápidamente, sino que también mantienen un control más preciso sobre el calor durante el proceso. Además, algunos de estos hornos incorporan sistemas de recuperación de calor, lo que les permite reutilizar el calor residual generado durante el proceso de curado para calentar otras áreas de la planta, reduciendo la necesidad de energía adicional y mejorando la eficiencia general del proceso.
La mejora de la eficiencia energética no se limita únicamente al curado, sino que también se extiende a otros aspectos de la planta, como la iluminación y la ventilación. La transición a sistemas de iluminación LED de bajo consumo, por ejemplo, no solo reduce el consumo de electricidad, sino que también mejora la durabilidad de las lámparas y reduce la necesidad de mantenimiento. De manera similar, las plantas están adoptando sistemas de ventilación más eficientes que optimizan el flujo de aire y mantienen un ambiente saludable sin desperdiciar energía.
Además de la eficiencia energética, las plantas de pintura en polvo también están enfocadas en la gestión de los materiales y el reciclaje. En el proceso de pintura en polvo, una cantidad significativa de material no se adhiere a las piezas y termina siendo recuperada, pero en muchas plantas antiguas, este polvo recuperado se desecha o se malgasta. Hoy en día, la mayoría de las plantas de pintura en polvo modernas utilizan sistemas avanzados de recuperación que permiten capturar este polvo y reutilizarlo, lo que no solo reduce el desperdicio de material sino que también minimiza la necesidad de comprar más polvo nuevo. Esto no solo reduce los costos operativos, sino que también ayuda a disminuir la cantidad de residuos generados, lo que tiene un impacto positivo en el medio ambiente.
La sostenibilidad también se extiende a los recubrimientos utilizados en estas plantas. Los recubrimientos en polvo, por naturaleza, son más sostenibles que las pinturas líquidas tradicionales porque no contienen disolventes, lo que reduce las emisiones de compuestos orgánicos volátiles (COV). Los COV son una de las principales causas de contaminación del aire en muchas industrias, y su eliminación o reducción significativa es un objetivo fundamental para las plantas de pintura en polvo. Además, los recubrimientos en polvo tienen una mayor durabilidad y resistencia que los recubrimientos líquidos, lo que significa que las piezas tratadas con pintura en polvo tienen una vida útil más larga y requieren menos mantenimiento, lo que contribuye aún más a la sostenibilidad a largo plazo.
La gestión de residuos en las plantas de pintura en polvo también ha evolucionado significativamente. En lugar de simplemente descartar el polvo recuperado o los productos defectuosos, las plantas están implementando sistemas de reciclaje más sofisticados. Los residuos de pintura que no se pueden recuperar pueden ser gestionados de manera que minimicen su impacto ambiental, ya sea mediante su tratamiento y eliminación adecuada o a través de procesos de reciclaje que permitan la recuperación de ciertos materiales. Estas prácticas ayudan a reducir el volumen de residuos que se envían a los vertederos y contribuyen a la economía circular al reintegrar materiales reciclados en el proceso productivo.
Otro aspecto importante de la sostenibilidad en las plantas de pintura en polvo es el uso de tecnologías de monitoreo en tiempo real para gestionar el consumo de recursos. Los sistemas de control avanzados y los sensores en las plantas permiten monitorear continuamente los parámetros de consumo de energía y materiales. Esta información es crucial para detectar ineficiencias o áreas donde se pueda reducir el consumo de recursos. Por ejemplo, si una máquina está funcionando a una capacidad superior a la necesaria, los operadores pueden recibir alertas para ajustar los parámetros y reducir el uso innecesario de energía. Además, estos sistemas pueden ayudar a prever necesidades de mantenimiento y asegurar que las máquinas operen con la mayor eficiencia posible.
La adopción de energías renovables también está ganando terreno en las plantas automáticas de pintura en polvo. Algunas instalaciones están comenzando a incorporar fuentes de energía renovables, como paneles solares o turbinas eólicas, para complementar sus necesidades energéticas. Estas fuentes de energía no solo reducen la dependencia de los combustibles fósiles, sino que también ayudan a las plantas a cumplir con las normativas medioambientales cada vez más estrictas y a mejorar su imagen corporativa al demostrar un compromiso con la sostenibilidad.
Por otro lado, la reducción de emisiones de gases contaminantes es otro objetivo clave en las plantas de pintura en polvo. A través de sistemas de filtración avanzados, como los filtros de mangas o los sistemas de captura de polvo, las plantas pueden minimizar las emisiones de partículas finas al aire, lo que ayuda a cumplir con las normativas de calidad del aire y contribuye a la salud y seguridad de los trabajadores. Estos sistemas de filtración también permiten reciclar el aire dentro de la planta, lo que reduce la necesidad de ventilación externa y, por lo tanto, ahorra energía.
Finalmente, la sostenibilidad en las plantas de pintura en polvo no solo se refiere al proceso de producción, sino también al diseño y la operación general de las instalaciones. Las plantas están adoptando principios de diseño ecológico en su construcción y operación, como el uso de materiales reciclables, la optimización de la distribución de los recursos y la implementación de soluciones que maximicen la eficiencia del espacio y minimicen los impactos negativos sobre el medio ambiente. Estos enfoques no solo mejoran la sostenibilidad de la planta, sino que también crean un entorno de trabajo más seguro y saludable para los empleados, lo que se traduce en una mayor productividad y bienestar en el lugar de trabajo.
En conclusión, la sostenibilidad y la eficiencia energética son factores esenciales en la operación de las Plantas Automáticas de Pintura en Polvo. A través de la implementación de tecnologías avanzadas, la mejora en los procesos de reciclaje, la optimización del uso de recursos y la adopción de prácticas más ecológicas, las plantas de pintura en polvo están no solo reduciendo su impacto ambiental, sino también mejorando su rentabilidad y competitividad en un mercado cada vez más centrado en la sostenibilidad. La constante innovación en estos campos garantiza que estas plantas continúen evolucionando hacia modelos de producción más responsables y eficientes, contribuyendo a la protección del medio ambiente y a la reducción de costos operativos.
Personalización de Productos y Flexibilidad en la Producción
La personalización de productos y la flexibilidad en la producción son dos aspectos fundamentales que han cobrado gran relevancia en la industria moderna, especialmente en las Plantas Automáticas de Pintura en Polvo. La capacidad de adaptar los procesos de fabricación para satisfacer las necesidades específicas de los clientes, sin perder eficiencia ni calidad, es un factor clave que permite a las empresas diferenciarse en un mercado cada vez más competitivo. La demanda de productos personalizados ha crecido significativamente, impulsada por la necesidad de ofrecer soluciones más específicas para una variedad de aplicaciones y sectores. Esto ha llevado a las plantas de pintura en polvo a adoptar tecnologías y métodos que permitan una mayor flexibilidad en sus líneas de producción.
La personalización en la industria de pintura en polvo abarca una amplia gama de opciones, desde la elección del color y el acabado de las superficies hasta la aplicación de propiedades específicas, como mayor resistencia a la corrosión, a la abrasión o a condiciones climáticas extremas. En lugar de producir solo una versión estándar de un producto, las plantas ahora deben ser capaces de adaptarse a las especificaciones exactas de cada cliente. Esto requiere una gran flexibilidad en la configuración de las líneas de producción, lo que implica que las máquinas y los procesos deben poder ajustarse rápidamente para trabajar con diferentes tipos de recubrimientos, diferentes métodos de aplicación y diferentes configuraciones de producto.
La tecnología juega un papel crucial en la personalización de los productos y la flexibilidad en la producción. Las plantas automáticas de pintura en polvo están utilizando sistemas de automatización avanzados, como robots de pulverización y máquinas de curado de última generación, que se pueden programar y ajustar con facilidad para aplicar distintos tipos de recubrimientos y acabados en función de los requisitos del cliente. Los robots de pulverización, por ejemplo, pueden cambiar de manera rápida y precisa la distancia, el ángulo y la velocidad de pulverización, lo que permite la aplicación de un recubrimiento uniforme y eficiente en piezas de diversas formas y tamaños. Esta flexibilidad en la programación de los robots también permite la personalización de los acabados, como el brillo, la textura o la opacidad de la pintura.
Además, la personalización no solo se refiere a las características estéticas del producto, sino también a su rendimiento. Los avances en los recubrimientos en polvo han permitido la creación de productos con propiedades específicas adaptadas a las necesidades de diversos sectores industriales, como la automoción, la construcción, la electrónica o la fabricación de maquinaria. Por ejemplo, los recubrimientos pueden ser formulados para resistir altas temperaturas, ofrecer protección adicional contra los rayos UV o proporcionar una mayor resistencia al impacto. Estos recubrimientos especializados requieren una mayor flexibilidad en el proceso de producción, ya que las plantas deben ser capaces de manejar una variedad de formulaciones y ajustar los parámetros de la producción en función de las necesidades específicas del cliente.
Para facilitar esta flexibilidad, muchas plantas están adoptando sistemas de control de procesos basados en software que permiten realizar ajustes rápidos en tiempo real. Estos sistemas integrados permiten a los operadores ajustar fácilmente los parámetros de la línea de producción, como la velocidad de la cinta transportadora, la cantidad de polvo utilizado, la temperatura del horno de curado o el flujo de aire, sin necesidad de parar la producción. Esta capacidad de realizar ajustes rápidos y precisos no solo mejora la flexibilidad en la personalización de los productos, sino que también optimiza el rendimiento general de la planta, minimizando los tiempos de inactividad y mejorando la eficiencia de la producción.
Otro aspecto importante en la personalización de los productos y la flexibilidad de la producción es la capacidad de manejar volúmenes pequeños o medianos de productos de diferentes características. Las plantas de pintura en polvo tradicionales a menudo están diseñadas para producir grandes volúmenes de productos homogéneos, lo que hace que la personalización sea más difícil y costosa. Sin embargo, las nuevas tecnologías de automatización y la mejora de los sistemas de manejo de materiales han permitido a las plantas adaptarse a la producción de lotes más pequeños, sin sacrificar la eficiencia ni la rentabilidad. Esto es especialmente relevante para los sectores que requieren productos de alta gama o diseños específicos que no se fabrican en grandes cantidades, como la industria automotriz, el mobiliario o los electrodomésticos de diseño personalizado.
La capacidad de las plantas para personalizar los productos también está estrechamente relacionada con la demanda de plazos de entrega más rápidos. Los consumidores de hoy en día esperan recibir productos en plazos más cortos, lo que exige una mayor agilidad en la producción. Las plantas automáticas de pintura en polvo han respondido a este desafío mediante la implementación de sistemas de producción más rápidos y flexibles que pueden adaptarse rápidamente a cambios en los pedidos o en las especificaciones de los productos. Los sistemas de control y monitoreo avanzados permiten una programación eficiente de las órdenes de producción, lo que optimiza el flujo de trabajo y reduce los tiempos de cambio entre diferentes productos o tipos de recubrimientos.
Además de la flexibilidad en los procesos de producción, la personalización también se extiende a la gestión de la cadena de suministro. Las plantas automáticas de pintura en polvo ahora están trabajando más estrechamente con sus proveedores para garantizar que los materiales necesarios para la personalización, como los pigmentos y las formulaciones específicas, estén disponibles en el momento adecuado. La gestión eficiente de inventarios y el control preciso de los materiales son esenciales para garantizar que la planta pueda responder rápidamente a las demandas de personalización sin incurrir en retrasos o costos adicionales. En algunos casos, las plantas están colaborando con sus clientes para desarrollar recubrimientos exclusivos que se adapten a sus necesidades específicas, lo que añade un nivel adicional de personalización y valor añadido al producto final.
La personalización también se ha visto favorecida por el avance de la tecnología de impresión digital. Algunas plantas de pintura en polvo están incorporando sistemas de impresión digital que permiten aplicar patrones y diseños complejos directamente sobre la superficie de las piezas. Este tipo de tecnología facilita la creación de productos personalizados con detalles precisos, como logotipos, gráficos o patrones artísticos, sin la necesidad de plantillas o procesos adicionales. La impresión digital, combinada con la pintura en polvo, ofrece una solución eficiente y de alta calidad para la personalización de productos en diversos sectores, incluidos el diseño de interiores, la publicidad y la fabricación de productos de consumo.
En resumen, la personalización de productos y la flexibilidad en la producción son esenciales para satisfacer las crecientes demandas de los consumidores y las industrias que requieren productos a medida. Las Plantas Automáticas de Pintura en Polvo han adoptado tecnologías avanzadas y procesos más ágiles que les permiten ofrecer una mayor variedad de productos con especificaciones personalizadas sin comprometer la eficiencia o la calidad. La automatización, la digitalización, los sistemas de control avanzados y la impresión digital son solo algunas de las herramientas que han permitido a las plantas mejorar su flexibilidad y capacidad de personalización, ofreciendo soluciones innovadoras para una amplia gama de sectores. La capacidad de adaptarse rápidamente a los cambios en la demanda y ofrecer productos únicos ha convertido a la personalización en un factor clave para el éxito en la industria moderna.
Seguridad Laboral y Protección en el Proceso
La seguridad laboral y la protección en el proceso son fundamentales en cualquier tipo de planta industrial, y las Plantas Automáticas de Pintura en Polvo no son la excepción. Estas instalaciones, debido a la naturaleza de los procesos involucrados, presentan varios riesgos que deben ser gestionados cuidadosamente para garantizar la seguridad de los trabajadores, así como la calidad y eficiencia de la producción. El proceso de pintura en polvo, que implica el uso de productos químicos, altas temperaturas y maquinaria pesada, requiere una serie de medidas de seguridad para prevenir accidentes, enfermedades laborales y otros incidentes que puedan poner en riesgo la salud de los empleados.
Una de las primeras áreas clave en la seguridad de las plantas de pintura en polvo es la protección contra la exposición a sustancias químicas. Los recubrimientos en polvo, aunque más ecológicos que las pinturas líquidas tradicionales, contienen compuestos que pueden ser peligrosos si se inhalan o entran en contacto con la piel. Además, el proceso de pulverización genera partículas de polvo fino que, si no se manejan adecuadamente, pueden ser una amenaza para la salud respiratoria de los operarios. Para mitigar estos riesgos, las plantas deben implementar sistemas de ventilación adecuados, como campanas de extracción de aire y sistemas de filtrado de partículas, que capturan el polvo en suspensión y lo dirigen hacia áreas de tratamiento especializado. Estos sistemas deben ser mantenidos y monitoreados regularmente para asegurar su funcionamiento eficaz.
El uso de equipos de protección personal (EPP) es otro componente esencial para garantizar la seguridad en la planta. Los trabajadores deben contar con ropa adecuada, guantes, gafas de protección y mascarillas para evitar el contacto directo con productos químicos y partículas de polvo. Además, en áreas donde se manipulan sustancias más peligrosas, como los productos de curado o disolventes, el uso de equipos de protección respiratoria es indispensable. Las plantas deben proporcionar formación continua sobre el uso adecuado del EPP y asegurarse de que todos los empleados estén conscientes de los riesgos específicos de sus puestos de trabajo y de las medidas preventivas que deben adoptar.
Además de los riesgos químicos, las plantas automáticas de pintura en polvo también enfrentan peligros derivados del manejo de maquinaria pesada y del trabajo con equipos de alta temperatura. Los hornos de curado, que son una parte crucial del proceso, operan a temperaturas muy altas, lo que representa un riesgo importante de quemaduras y accidentes relacionados con el calor. Para minimizar estos riesgos, los hornos están diseñados con sistemas de seguridad que incluyen aislamiento térmico, puertas de acceso con mecanismos de cierre automáticos y sistemas de alerta para indicar posibles fallos en el funcionamiento. Los operarios deben estar capacitados en procedimientos seguros de trabajo alrededor de estas áreas calientes y en el uso de sistemas de emergencia en caso de que se produzca un fallo o una situación de riesgo.
La automatización de los procesos en las plantas de pintura en polvo ha jugado un papel crucial en la mejora de la seguridad laboral. El uso de robots y sistemas automáticos para la pulverización, el manejo de materiales y el control de calidad ha reducido la necesidad de intervención humana en áreas peligrosas. Esto no solo mejora la eficiencia y la calidad de la producción, sino que también minimiza la exposición de los trabajadores a riesgos laborales. Sin embargo, aunque la automatización reduce muchos de los peligros asociados con el trabajo manual, también requiere que los operarios estén bien entrenados en la programación, operación y mantenimiento de los sistemas automatizados, lo que garantiza que no se produzcan accidentes debido a errores humanos o mal funcionamiento de los equipos.
La seguridad en la planta también está estrechamente vinculada a la gestión de riesgos relacionados con el fuego. Dado que el polvo utilizado en el proceso de pintura es inflamable, las plantas deben contar con medidas estrictas de prevención y control de incendios. Esto incluye la instalación de sistemas de extinción automática, la capacitación del personal en procedimientos de evacuación y el uso de detectores de humo y sistemas de alarma en las áreas de alto riesgo. Además, las plantas deben realizar inspecciones periódicas de las instalaciones eléctricas y de las maquinarias para asegurarse de que no existan fallos que puedan provocar chispas o sobrecalentamientos, lo que podría dar lugar a incendios. Las áreas donde se almacenan los productos inflamables también deben estar adecuadamente ventiladas y contar con medidas de seguridad específicas, como extintores de incendios y material ignífugo.
La seguridad también debe abordarse desde una perspectiva integral que incluya la cultura de seguridad dentro de la organización. Esto significa fomentar la comunicación abierta entre los empleados y la dirección sobre los posibles riesgos, las condiciones de trabajo y las prácticas de seguridad. Las plantas deben promover la participación activa de todos los trabajadores en la identificación de riesgos y en la implementación de soluciones de seguridad. La formación continua es una herramienta esencial en este sentido, ya que mantiene a los empleados informados sobre los riesgos asociados con su trabajo y las mejores prácticas para prevenir accidentes. Además, los programas de seguridad deben incluir simulacros de emergencia, tanto para incidentes de incendio como para otros tipos de accidentes industriales, lo que garantiza que todos los trabajadores estén preparados para reaccionar rápidamente y de manera segura en caso de una emergencia.
El diseño de la planta y la disposición de los equipos también juegan un papel crucial en la prevención de accidentes. Las plantas de pintura en polvo deben ser diseñadas de manera que se minimicen los riesgos de accidentes laborales. Esto implica una planificación cuidadosa de la distribución de las áreas de trabajo, el mantenimiento de un entorno limpio y ordenado y la eliminación de cualquier obstrucción que pueda representar un peligro para los empleados. Los pasillos deben ser lo suficientemente anchos para permitir una circulación fluida y segura, y los equipos deben estar ubicados de manera que los operarios puedan acceder a ellos sin necesidad de exponerse a situaciones peligrosas.
En la actualidad, las normativas y regulaciones sobre seguridad laboral son cada vez más estrictas, lo que ha llevado a las plantas de pintura en polvo a adoptar tecnologías y prácticas más avanzadas para garantizar la seguridad de los trabajadores. Las inspecciones regulares y el cumplimiento de las normativas son fundamentales para evitar sanciones y garantizar que las plantas operen dentro de los parámetros de seguridad establecidos por las autoridades competentes.
En conclusión, la seguridad laboral y la protección en el proceso son elementos esenciales para el funcionamiento de las Plantas Automáticas de Pintura en Polvo. A través de la implementación de medidas preventivas, el uso de equipos de protección personal, la automatización de procesos y la adopción de tecnologías de seguridad, estas plantas pueden minimizar los riesgos para los trabajadores y garantizar un entorno laboral seguro. La formación continua, el cumplimiento de las normativas de seguridad y la promoción de una cultura de seguridad en la empresa son factores clave para reducir los accidentes y enfermedades laborales, lo que contribuye no solo al bienestar de los empleados, sino también a la eficiencia y la rentabilidad a largo plazo de la planta.
Impacto de la Automatización en la Competitividad del Mercado
La automatización ha transformado profundamente la industria moderna, y su impacto en la competitividad del mercado es especialmente notable en sectores como la pintura en polvo, donde la eficiencia, la calidad y la capacidad de respuesta son factores clave para el éxito. La adopción de tecnologías automáticas en las plantas de pintura en polvo no solo ha permitido a las empresas mejorar sus procesos internos, sino también adaptarse rápidamente a las demandas del mercado, reducir costos y ofrecer productos con características personalizadas. En un mercado cada vez más competitivo y globalizado, las plantas que implementan soluciones automatizadas se posicionan favorablemente para satisfacer las expectativas de los clientes y superar a sus competidores.
Uno de los principales beneficios de la automatización en la planta de pintura en polvo es la mejora en la eficiencia operativa. La automatización permite una mayor rapidez y precisión en las tareas repetitivas, como la pulverización del polvo, el curado y el control de calidad. Los sistemas automáticos, como los robots de pintura, pueden operar de manera continua, sin los descansos que necesitaría un trabajador humano, lo que aumenta la producción y reduce los tiempos de inactividad. Además, los robots pueden trabajar con una precisión mucho mayor que los operarios manuales, lo que minimiza los errores y mejora la consistencia del recubrimiento aplicado. Esto se traduce en una mayor capacidad de producción y en una reducción significativa de los costos asociados con los defectos y el retrabajo, lo que mejora la competitividad de la empresa.
La automatización también permite una mejor gestión de los recursos, lo que repercute directamente en la rentabilidad. En lugar de depender de un número elevado de trabajadores para realizar tareas de control y ajuste, los sistemas automáticos pueden monitorear continuamente los parámetros de producción y hacer ajustes en tiempo real. Esto no solo reduce la necesidad de mano de obra, sino que también optimiza el uso de materiales y energía, lo que se traduce en una mayor eficiencia en el consumo de recursos. Por ejemplo, la automatización en la pulverización del polvo permite un uso más eficiente del material, reduciendo el desperdicio de polvo que no se adhiere a las superficies y disminuyendo la cantidad de recubrimientos necesarios para lograr la calidad deseada. En consecuencia, las plantas pueden operar de manera más sostenible y con menores costos, lo que mejora su competitividad en un entorno donde los márgenes de beneficio son cada vez más ajustados.
La flexibilidad también es una ventaja clave que la automatización aporta a las plantas de pintura en polvo. Los sistemas automatizados pueden ser ajustados rápidamente para adaptarse a diferentes tipos de productos o especificaciones, lo que permite a las empresas ofrecer una mayor variedad de productos a sus clientes sin sacrificar la eficiencia o la calidad. Esto es especialmente importante en mercados donde los consumidores demandan productos personalizados o de edición limitada. La capacidad de adaptarse a estas demandas de manera rápida y eficiente es un factor clave que distingue a las empresas líderes de sus competidores. Las plantas automatizadas tienen la capacidad de realizar cambios de línea de producción de manera más ágil, lo que les permite responder a cambios en la demanda sin interrumpir la producción o aumentar los costos de manera significativa.
Además, la automatización puede ayudar a las empresas a reducir los costos laborales, un factor clave en la competitividad de cualquier mercado. Al disminuir la necesidad de mano de obra humana en las tareas más repetitivas y físicamente exigentes, las plantas pueden redistribuir sus recursos a áreas más estratégicas, como la investigación y desarrollo, el diseño de nuevos productos o la mejora continua de los procesos. Esto no solo mejora la eficiencia, sino que también permite a las empresas invertir en innovaciones que pueden darles una ventaja competitiva a largo plazo. Las soluciones automatizadas también contribuyen a reducir los riesgos laborales y mejorar la seguridad en el lugar de trabajo, lo que no solo tiene beneficios en términos de bienestar de los empleados, sino que también contribuye a la estabilidad operativa y a la reducción de costos asociados con accidentes y enfermedades laborales.
La automatización también impacta de manera directa en la calidad del producto. Los sistemas automáticos, como los robots de pintura, aplican una cantidad precisa y constante de recubrimiento, lo que resulta en una mayor uniformidad en la calidad del producto final. Esto es particularmente importante en mercados donde la calidad es un diferenciador clave, como la industria automotriz, la fabricación de electrodomésticos de gama alta o los productos de diseño. La capacidad de producir productos con una calidad consistente y sin defectos también reduce los costos asociados con el retrabajo y las devoluciones, lo que mejora la rentabilidad y la competitividad de la empresa. Al mantener altos estándares de calidad, las empresas pueden establecer una reputación de fiabilidad y excelencia, lo que les permite ganar la lealtad de los clientes y diferenciarse de la competencia.
La capacidad de la automatización para proporcionar datos en tiempo real también es un factor importante en la mejora de la competitividad. Los sistemas automatizados, al estar equipados con sensores y software de monitoreo avanzado, generan una gran cantidad de datos que pueden ser utilizados para analizar el rendimiento de la planta, detectar ineficiencias o áreas de mejora y prever necesidades de mantenimiento. Este análisis de datos en tiempo real permite a las empresas tomar decisiones informadas rápidamente, lo que contribuye a una mayor agilidad en la respuesta a las demandas del mercado. La toma de decisiones basada en datos también ayuda a las empresas a identificar oportunidades de mejora continua, lo que les permite mantenerse a la vanguardia en un mercado competitivo.
Además, la automatización permite una mejor integración con otras tecnologías avanzadas, como la inteligencia artificial y el Internet de las Cosas (IoT). Estas tecnologías pueden ser utilizadas para optimizar aún más los procesos de producción, predecir fallos en el equipo antes de que ocurran, y mejorar la eficiencia general de la planta. Al integrar la automatización con otras tecnologías emergentes, las plantas pueden mantenerse a la vanguardia de la innovación y ofrecer soluciones más avanzadas a sus clientes. Esto no solo mejora la competitividad en términos de costos y eficiencia, sino que también posiciona a la empresa como líder en innovación dentro de su sector.
En resumen, el impacto de la automatización en la competitividad del mercado es profundo y multifacético. Al mejorar la eficiencia, reducir los costos, aumentar la flexibilidad y garantizar una calidad constante, la automatización permite a las empresas destacar en un mercado global cada vez más competitivo. Además, al integrar tecnologías avanzadas y optimizar el uso de los recursos, las plantas automatizadas pueden ofrecer productos personalizados con plazos de entrega más rápidos, lo que les permite satisfacer las demandas cambiantes de los clientes de manera más eficaz. En un entorno empresarial donde la capacidad de adaptarse rápidamente a los cambios es crucial, la automatización se ha convertido en una herramienta indispensable para mantener una ventaja competitiva.
Equipos De Aplicación De Pintura Electrostática
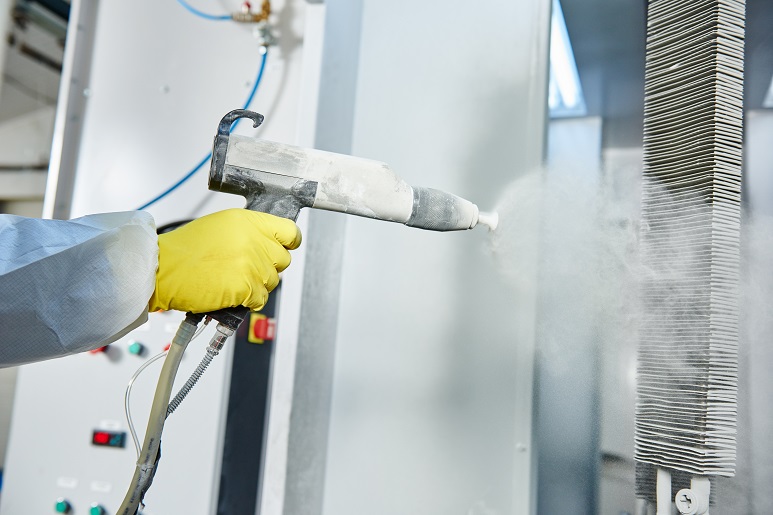
Los equipos de aplicación de pintura electrostática han revolucionado la forma en que se lleva a cabo el proceso de recubrimiento en diversas industrias, proporcionando soluciones más eficientes y de mayor calidad en comparación con los métodos tradicionales. Estos sistemas utilizan la electricidad para cargar las partículas de pintura, que se adhieren a las superficies metálicas, lo que resulta en una aplicación más precisa, uniforme y económica. La adopción de estos equipos ha tenido un impacto significativo en la competitividad del mercado, permitiendo a las empresas optimizar sus procesos de producción y ofrecer productos de alta calidad a precios más competitivos.
Una de las principales ventajas de los equipos de aplicación de pintura electrostática es la mejora en la eficiencia de la aplicación. A diferencia de los métodos convencionales, donde una parte considerable de la pintura puede ser desperdiciada debido a la pulverización en áreas no deseadas, los sistemas electrostáticos minimizan este desperdicio al asegurar que las partículas de pintura se adhieran de manera efectiva a la superficie a recubrir. Esto no solo reduce los costos asociados con el consumo de material, sino que también hace que el proceso sea más ecológico al generar menos residuos. Esta eficiencia en el uso del material se traduce en menores costos operativos y una mayor rentabilidad para las empresas, lo que les permite mantenerse competitivas en un mercado donde la optimización de recursos es esencial.
La calidad del recubrimiento aplicado con equipos electrostáticos también es un factor determinante en la competitividad de una planta de pintura. Estos sistemas permiten una distribución más uniforme de la pintura, lo que garantiza un acabado de mayor calidad y sin irregularidades. La carga electrostática ayuda a que la pintura cubra de manera eficiente las superficies, incluso aquellas de formas complejas o difíciles de alcanzar, lo que asegura una cobertura completa. Esto es especialmente importante en sectores como la automoción, la fabricación de electrodomésticos y la industria metálica, donde la calidad del acabado es fundamental para la durabilidad del producto y la satisfacción del cliente. La capacidad de garantizar una calidad consistente a lo largo de la producción aumenta la competitividad de las empresas al establecerlas como proveedores fiables y de alto nivel.
Además, los equipos de pintura electrostática son más rápidos en su aplicación, lo que mejora el rendimiento general de la planta. El proceso electrostático permite una cobertura eficiente y uniforme en menos tiempo en comparación con los métodos tradicionales. Esta reducción en los tiempos de aplicación contribuye a una mayor productividad y una mayor capacidad para cumplir con plazos de entrega más cortos, lo que es una ventaja significativa en un entorno de mercado altamente competitivo. Las empresas que implementan esta tecnología pueden mejorar sus tiempos de respuesta ante pedidos urgentes o cambios en la demanda, lo que les permite ofrecer un mejor servicio al cliente y destacarse frente a la competencia.
Otro aspecto importante en el que los equipos de aplicación de pintura electrostática impactan la competitividad es en la reducción de los costos de mantenimiento. Estos sistemas están diseñados para ser más fáciles de limpiar y mantener que los equipos convencionales. La mayor precisión en la aplicación reduce la acumulación de pintura en las partes de la máquina, lo que a su vez disminuye la necesidad de mantenimiento frecuente y los costos asociados. La reducción de tiempo y recursos dedicados al mantenimiento permite a las empresas destinar más esfuerzos a la producción y la innovación, contribuyendo a un mejor desempeño general en el mercado.
Los equipos de aplicación de pintura electrostática también tienen una menor huella ambiental en comparación con los sistemas de pintura tradicionales. Esto se debe a que los sistemas electrostáticos producen menos emisiones de compuestos orgánicos volátiles (COV), lo que reduce el impacto ambiental de la planta de pintura. Las regulaciones ambientales son cada vez más estrictas, y las empresas que implementan tecnologías más limpias y sostenibles no solo cumplen con las normativas, sino que también se benefician de una imagen corporativa más positiva y un mayor atractivo para los consumidores conscientes del medio ambiente. Esta ventaja puede traducirse en una mayor demanda de productos, mejorando la competitividad de las empresas que adoptan estos sistemas.
La versatilidad de los equipos de aplicación de pintura electrostática también juega un papel importante en la competitividad de las empresas. Estos sistemas son aptos para una amplia variedad de materiales y productos, lo que permite a las plantas de pintura adaptarse rápidamente a cambios en la demanda o a nuevas oportunidades de mercado. La posibilidad de trabajar con diferentes tipos de pinturas y recubrimientos también proporciona a las empresas la flexibilidad para ofrecer productos personalizados que se ajusten a las necesidades específicas de los clientes. Esta capacidad de diversificación es crucial en un entorno de mercado dinámico, donde las expectativas de los consumidores y las tendencias de la industria pueden cambiar rápidamente.
La automatización en los equipos de aplicación de pintura electrostática contribuye a una mayor consistencia en el acabado y a una mejor gestión de los procesos de producción. Los sistemas automatizados permiten controlar de manera precisa la cantidad de pintura aplicada, la velocidad y el ángulo de pulverización, lo que mejora la calidad del recubrimiento y reduce los errores humanos. Además, estos sistemas pueden integrarse con otros procesos de producción, como el control de calidad y la inspección automatizada, para garantizar que cada pieza reciba el recubrimiento adecuado y cumpla con los estándares de calidad establecidos. La capacidad de controlar todos los aspectos del proceso con gran precisión no solo mejora la calidad del producto final, sino que también optimiza el flujo de trabajo, reduciendo los tiempos de producción y aumentando la eficiencia operativa.
La mejora en la eficiencia energética es otro beneficio que los equipos de aplicación de pintura electrostática aportan a las plantas. Al utilizar menos pintura y energía en comparación con los sistemas tradicionales, estos equipos contribuyen a una menor demanda de recursos y a una reducción de los costos operativos. Las plantas de pintura que adoptan esta tecnología pueden reducir su consumo energético y los costos asociados, lo que les permite ofrecer precios más competitivos en el mercado sin sacrificar la calidad de los productos. Además, el uso más eficiente de la energía también ayuda a reducir la huella de carbono de la planta, lo que es una ventaja en términos de sostenibilidad y responsabilidad social empresarial.
En resumen, los equipos de aplicación de pintura electrostática tienen un impacto significativo en la competitividad del mercado, al mejorar la eficiencia, la calidad, la flexibilidad y la sostenibilidad de las plantas de pintura. Estos sistemas permiten a las empresas reducir costos, aumentar la productividad, ofrecer productos de mayor calidad y adaptarse rápidamente a las demandas del mercado. En un entorno industrial donde la innovación, la eficiencia y la sostenibilidad son factores clave, la implementación de equipos de pintura electrostática se ha convertido en una herramienta esencial para mantener una ventaja competitiva, lo que permite a las empresas destacarse frente a sus competidores y satisfacer las expectativas de los clientes de manera más efectiva.
Tecnología de los Equipos de Aplicación de Pintura Electrostática
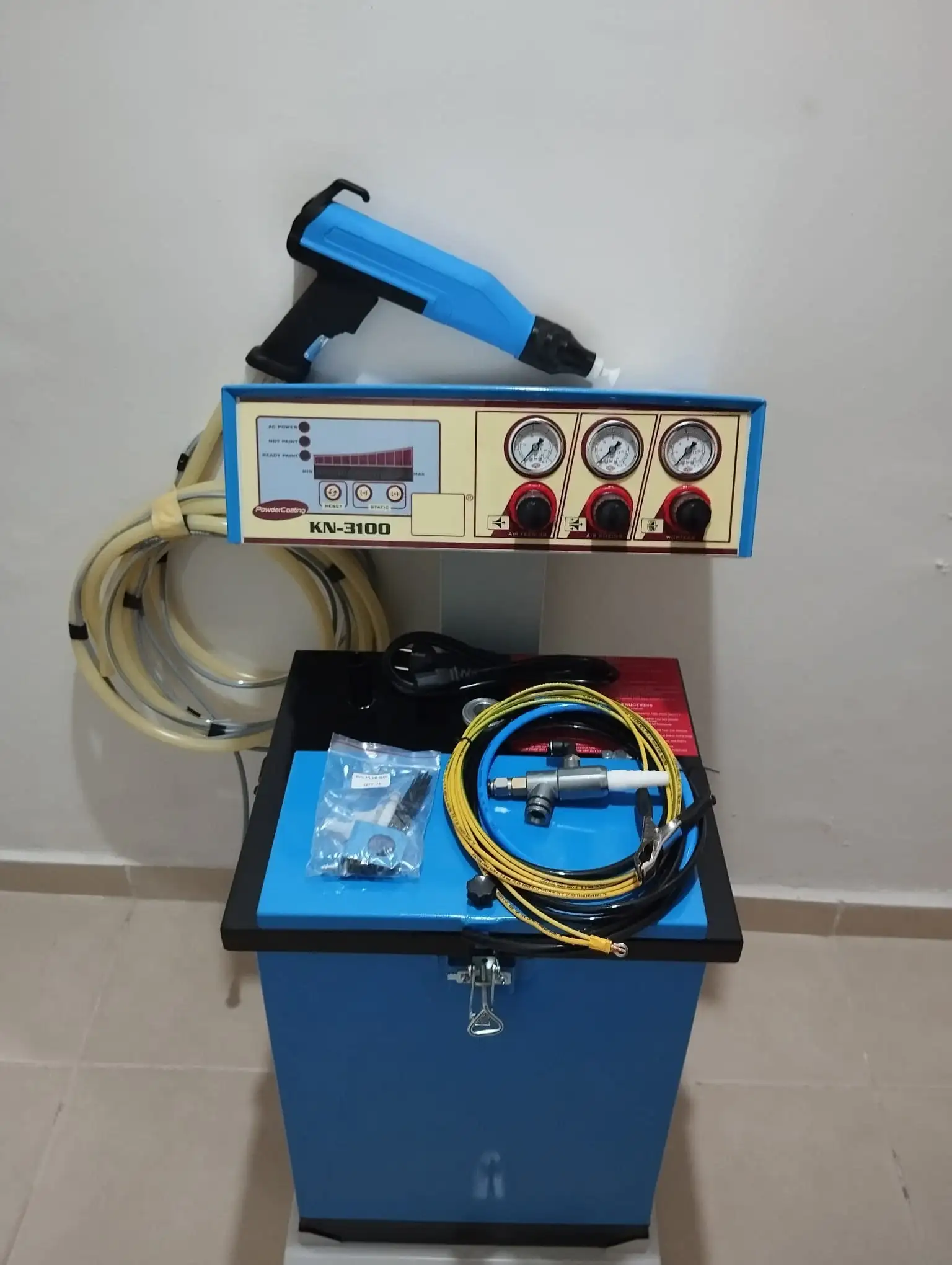
La tecnología de los equipos de aplicación de pintura electrostática ha transformado la industria del recubrimiento al proporcionar soluciones más precisas, eficientes y sostenibles. La pintura electrostática utiliza un campo eléctrico para cargar las partículas de pintura, lo que permite que estas se adhieran con gran eficacia a las superficies metálicas y otras estructuras. Este método de aplicación reduce considerablemente el desperdicio de material, lo que se traduce en menores costos operativos y un uso más eficiente de los recursos, un aspecto crucial en un mercado cada vez más competitivo y consciente de la sostenibilidad. Las empresas que adoptan esta tecnología no solo mejoran sus márgenes de ganancia, sino que también ofrecen productos con acabados de mayor calidad, más duraderos y uniformes.
Uno de los principales beneficios de los equipos de aplicación de pintura electrostática es la alta precisión con la que se aplica la pintura. Gracias a la carga electrostática, las partículas de pintura se adhieren de manera uniforme a la superficie, incluso en áreas complejas o de difícil acceso. Esto asegura que la pintura se distribuya de manera constante y eficiente, lo que mejora la calidad del producto final. A diferencia de los métodos tradicionales, que pueden generar exceso de pintura en áreas no deseadas o perder material en el aire, los sistemas electrostáticos permiten una aplicación mucho más controlada. Esto no solo mejora la apariencia del acabado, sino que también reduce la necesidad de retrabajos y correcciones, lo que a su vez disminuye los costos y mejora la productividad.
La velocidad del proceso es otro aspecto clave que mejora la competitividad de las plantas de pintura que utilizan equipos electrostáticos. Estos sistemas permiten un recubrimiento más rápido en comparación con los métodos tradicionales, lo que aumenta la eficiencia operativa. Al reducir el tiempo necesario para aplicar la pintura y permitir una mayor capacidad de producción, las empresas pueden cumplir con plazos de entrega más cortos y adaptarse rápidamente a los cambios en la demanda del mercado. Esta capacidad para responder con rapidez a las solicitudes de los clientes se ha convertido en un factor diferenciador en la industria, donde los tiempos de respuesta ágiles son esenciales para mantener una ventaja competitiva.
Además de mejorar la productividad y la calidad, los equipos de aplicación de pintura electrostática contribuyen significativamente a la sostenibilidad de las operaciones. Al utilizar menos pintura y generar menos residuos, estos sistemas no solo son más económicos, sino también más ecológicos. La reducción de emisiones de compuestos orgánicos volátiles (COV) y el menor desperdicio de material ayudan a las empresas a cumplir con las normativas medioambientales cada vez más estrictas. Las plantas de pintura que adoptan esta tecnología pueden beneficiarse de una imagen corporativa más positiva, ya que los consumidores y los reguladores valoran cada vez más a las empresas comprometidas con la sostenibilidad y la reducción de su huella de carbono.
Los equipos de aplicación de pintura electrostática también permiten una mayor flexibilidad en la producción. Estos sistemas pueden adaptarse fácilmente a diferentes tipos de materiales, colores y acabados, lo que les otorga una versatilidad considerable. Esta capacidad de personalización es especialmente importante en sectores como la automoción, la fabricación de electrodomésticos y la producción de componentes metálicos, donde los clientes a menudo requieren productos específicos que cumplen con sus exigencias en términos de diseño y acabado. Además, la capacidad para ajustar rápidamente los parámetros del proceso de pintura permite a las plantas de producción adaptarse a nuevas tendencias del mercado sin necesidad de realizar modificaciones costosas en los equipos.
La facilidad de mantenimiento y la fiabilidad de los equipos electrostáticos también son factores importantes que contribuyen a su ventaja competitiva. Estos sistemas están diseñados para ser más duraderos y requieren menos mantenimiento en comparación con los métodos de aplicación convencionales. La limpieza de los equipos es más sencilla debido a la menor acumulación de pintura, lo que reduce el tiempo de inactividad y los costos asociados con el mantenimiento. La fiabilidad de los equipos también minimiza el riesgo de fallos en el proceso de producción, lo que asegura que las operaciones sean más consistentes y menos propensas a interrupciones.
Otro factor crucial en la competitividad de los equipos de aplicación de pintura electrostática es la integración de tecnología avanzada, como la automatización y el monitoreo en tiempo real. Los sistemas modernos de aplicación de pintura electrostática pueden conectarse con otros procesos de producción, como el control de calidad y la supervisión de los parámetros de aplicación. Esto permite a las empresas obtener información detallada sobre el rendimiento de los equipos, lo que facilita la toma de decisiones informadas y la identificación de áreas de mejora. La capacidad de ajustar los parámetros en tiempo real también mejora la eficiencia y reduce el riesgo de defectos en el producto final.
Además, la evolución de los sistemas de pintura electrostática ha permitido la implementación de tecnologías que no solo mejoran la calidad y la eficiencia, sino también la seguridad en el lugar de trabajo. Al reducir la exposición de los trabajadores a compuestos químicos peligrosos y mejorar la precisión en la aplicación, los sistemas electrostáticos contribuyen a un entorno de trabajo más seguro. La reducción de los riesgos laborales no solo beneficia a los empleados, sino que también reduce los costos asociados con accidentes y enfermedades, lo que mejora aún más la rentabilidad de la planta.
En resumen, los equipos de aplicación de pintura electrostática ofrecen una serie de ventajas que mejoran significativamente la competitividad de las empresas en el mercado. Al permitir una aplicación más precisa y eficiente de la pintura, reducir los costos operativos, mejorar la sostenibilidad y aumentar la flexibilidad en la producción, estos sistemas se han convertido en una herramienta indispensable para las industrias que buscan mantenerse competitivas. Además, su capacidad para adaptarse a nuevas tecnologías y satisfacer las demandas de un mercado en constante cambio asegura que las plantas de pintura puedan seguir siendo relevantes y exitosas a largo plazo.
La adopción de equipos de aplicación de pintura electrostática no solo está impulsada por la mejora en la eficiencia y la reducción de costos, sino también por su capacidad para innovar continuamente. A medida que las industrias evolucionan, las expectativas de los consumidores cambian, exigiendo productos más personalizados, con acabados de mayor calidad y plazos de entrega más cortos. Los sistemas de pintura electrostática están diseñados para adaptarse a estos cambios, lo que permite a las empresas ofrecer soluciones innovadoras sin comprometer la eficiencia ni la rentabilidad. Esta capacidad de adaptación es fundamental para mantenerse competitivo en un mercado cada vez más exigente.
La integración de la inteligencia artificial (IA) y la analítica avanzada también juega un papel importante en la mejora de la competitividad de los equipos de aplicación de pintura electrostática. Con la implementación de algoritmos de IA, los sistemas de pintura pueden aprender de los datos históricos de producción, identificar patrones y predecir posibles fallos o ineficiencias en el proceso. Este tipo de inteligencia predictiva permite a las plantas optimizar sus procesos, realizar mantenimientos preventivos y mejorar aún más la calidad del producto final, minimizando el tiempo de inactividad y maximizando la productividad. Además, la integración de sensores avanzados permite monitorear continuamente los parámetros clave del proceso, como la temperatura, la velocidad de aplicación y la cantidad de pintura utilizada, lo que mejora la toma de decisiones en tiempo real y asegura que cada pieza cumpla con los estándares más exigentes.
La competitividad también se ve favorecida por la capacidad de los equipos de aplicación de pintura electrostática para ofrecer una experiencia de cliente más satisfactoria. En industrias como la automotriz, la electrónica o la fabricación de electrodomésticos, donde los acabados estéticos son tan importantes como la funcionalidad, la calidad del recubrimiento es esencial para la percepción del cliente final. Los sistemas electrostáticos aseguran acabados suaves, duraderos y sin defectos, lo que contribuye a la reputación de la marca y a la lealtad del cliente. Las empresas que utilizan esta tecnología pueden garantizar productos con acabados consistentes y de alta calidad, lo que genera confianza y satisfacción entre los consumidores.
El uso de equipos de aplicación de pintura electrostática también puede ser un diferenciador clave en términos de cumplimiento con las regulaciones de sostenibilidad. Los estándares medioambientales son cada vez más estrictos, y las empresas que adoptan tecnologías más limpias y eficientes están mejor posicionadas para cumplir con estas normativas, evitando posibles sanciones y mejorando su imagen ante los clientes, inversionistas y organismos reguladores. Además, al reducir las emisiones de compuestos volátiles y minimizar el desperdicio de pintura, las empresas no solo reducen su huella de carbono, sino que también contribuyen a la preservación del medio ambiente, lo que refuerza su compromiso con la sostenibilidad y la responsabilidad social corporativa.
La facilidad de integración de estos equipos con otros sistemas automatizados y procesos industriales también permite a las empresas lograr una mayor eficiencia operativa en toda la planta. Los equipos de aplicación de pintura electrostática pueden conectarse fácilmente con líneas de producción automatizadas, sistemas de control de calidad y plataformas de gestión empresarial. Esto permite una mayor visibilidad en tiempo real de todo el proceso de producción, facilita el seguimiento de los productos y mejora la trazabilidad, lo que es esencial en sectores como la automoción, donde la calidad y el control de los procesos son fundamentales. La conectividad y la integración de sistemas permiten a las empresas optimizar no solo el proceso de pintura, sino toda la cadena de producción, lo que mejora la eficiencia global y la competitividad.
Además, la evolución de los equipos de aplicación de pintura electrostática está permitiendo la incorporación de tecnologías innovadoras, como los sistemas de pintura 3D y las impresoras 3D para recubrimientos. Estos avances están abriendo nuevas posibilidades para la personalización de productos, ofreciendo soluciones de acabado innovadoras y adaptadas a las necesidades específicas de los clientes. La capacidad de imprimir recubrimientos en 3D no solo permite crear diseños más complejos y detallados, sino que también mejora la eficiencia del proceso y reduce el tiempo de fabricación, lo que posiciona aún más a las empresas que adoptan estas tecnologías como líderes en innovación.
En cuanto al futuro, se espera que los equipos de aplicación de pintura electrostática sigan mejorando, incorporando avances en materiales, robótica, automatización y tecnología digital. Con el desarrollo de nuevas técnicas y la mejora de los sistemas de pulverización, la industria de la pintura en polvo se acercará cada vez más a la perfección en términos de eficiencia, calidad y sostenibilidad. Las empresas que inviertan en estas tecnologías avanzadas estarán mejor posicionadas para enfrentar los desafíos del mercado global y mantener su competitividad en un entorno empresarial cada vez más dinámico y exigente.
En resumen, los equipos de aplicación de pintura electrostática son una herramienta esencial para las empresas que buscan mantenerse competitivas en un mercado cada vez más exigente. Gracias a su capacidad para mejorar la eficiencia, reducir costos, garantizar calidad y flexibilidad, y cumplir con los estándares de sostenibilidad, estos sistemas ofrecen ventajas clave que permiten a las empresas destacar frente a la competencia. A medida que la tecnología continúa avanzando, la adopción de soluciones de pintura electrostática se convierte en una estrategia clave para las empresas que desean mantenerse a la vanguardia de la innovación y el rendimiento en la industria.
Pistola Automática
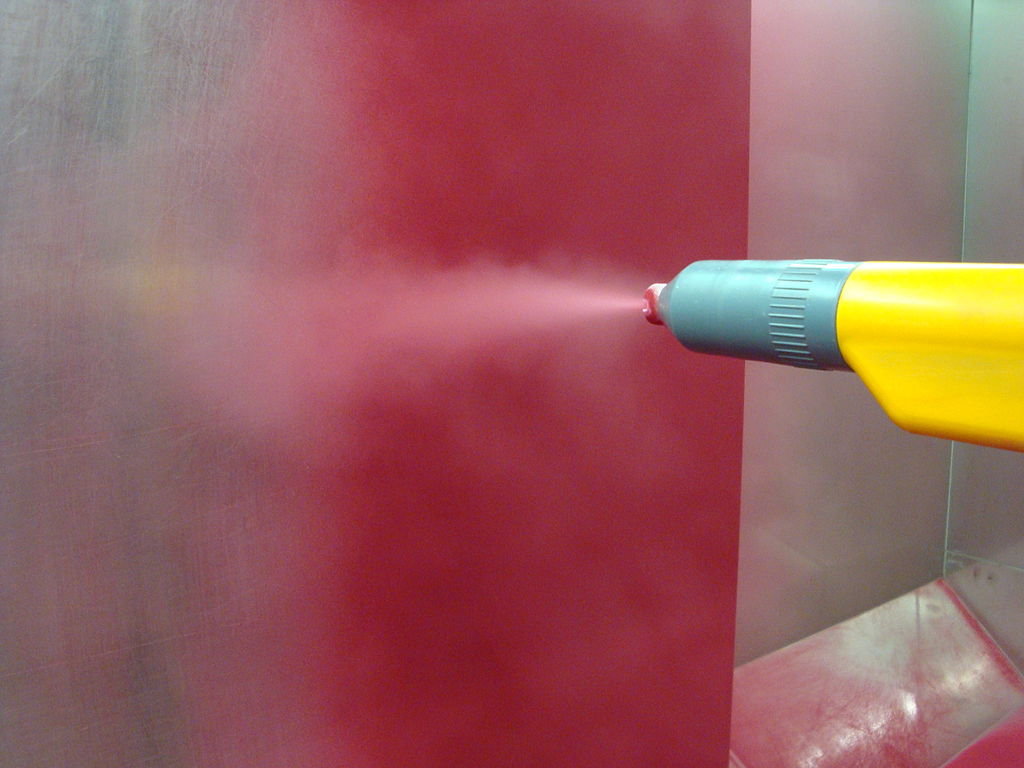
Las pistolas automáticas de aplicación de pintura electrostática han transformado la industria de recubrimientos, permitiendo un proceso de aplicación más eficiente, preciso y rentable. Estos dispositivos son esenciales en plantas de pintura automatizadas, ya que optimizan el uso de materiales, reducen los desperdicios y aseguran acabados consistentes y de alta calidad. Utilizando la carga electrostática para atraer las partículas de pintura hacia la superficie a recubrir, las pistolas automáticas permiten una aplicación más uniforme y controlada que los métodos tradicionales. Este tipo de tecnología es especialmente beneficioso para aplicaciones en sectores como la automoción, la fabricación de electrodomésticos y la producción de componentes metálicos, donde la precisión y la estética del acabado son fundamentales.
Una de las principales ventajas de las pistolas automáticas es la reducción significativa en el desperdicio de pintura. Al utilizar la carga eléctrica para atraer la pintura hacia la superficie, se evita que el material se disperse en el aire o en áreas no deseadas. Esto no solo mejora la eficiencia del proceso, sino que también reduce los costos operativos, ya que se necesita menos pintura para cubrir la misma superficie. Además, al aplicar la pintura de manera más controlada, las pistolas automáticas también reducen el consumo de energía y las emisiones de compuestos orgánicos volátiles (COV), lo que contribuye a una planta de pintura más sostenible y con un menor impacto ambiental.
La precisión en la aplicación es otra característica clave de las pistolas automáticas. Estas herramientas pueden ajustar automáticamente la cantidad de pintura aplicada, el ángulo y la velocidad de pulverización, lo que permite una cobertura más uniforme y consistente. Esta capacidad para controlar con precisión el proceso de aplicación es crucial para lograr acabados de alta calidad, sin goteos ni acumulaciones de pintura en áreas no deseadas. Las pistolas automáticas también pueden adaptarse a diferentes tipos de materiales y formas complejas, lo que les permite ser versátiles y eficaces en una amplia variedad de aplicaciones industriales. La capacidad de lograr un acabado perfecto en cada pieza no solo mejora la calidad del producto final, sino que también aumenta la satisfacción del cliente y la reputación de la empresa.
La automatización del proceso de pintura mediante el uso de pistolas automáticas también mejora la productividad. Al ser capaces de trabajar de forma continua y a alta velocidad, estas pistolas permiten una mayor capacidad de producción en menos tiempo, lo que ayuda a las empresas a cumplir con plazos de entrega más cortos. Esta mejora en la eficiencia operativa se traduce directamente en una mayor rentabilidad, ya que las plantas de pintura pueden producir más productos con el mismo nivel de recursos. Además, la reducción en el tiempo de aplicación y la eliminación de retrabajos o correcciones en el acabado permiten a las empresas optimizar su flujo de trabajo y aprovechar al máximo su capacidad de producción.
Otro beneficio importante de las pistolas automáticas es su capacidad para mejorar la seguridad en el lugar de trabajo. Al reducir la necesidad de intervención manual y minimizar el contacto directo de los trabajadores con materiales tóxicos, como la pintura y los disolventes, las pistolas automáticas contribuyen a un entorno de trabajo más seguro. Los operarios pueden estar menos expuestos a los riesgos asociados con la pintura en aerosol, como la inhalación de vapores y la exposición a productos químicos peligrosos. Además, los sistemas automáticos están diseñados para operar de manera eficiente y con poco mantenimiento, lo que reduce los tiempos de inactividad y el riesgo de fallos en el equipo, mejorando aún más la seguridad en la planta.
El impacto en la competitividad de las empresas que implementan pistolas automáticas de pintura es significativo. La capacidad de mejorar la eficiencia, reducir los costos operativos y garantizar un acabado de alta calidad permite a las empresas mantenerse competitivas en mercados donde la demanda de productos bien acabados y entregados a tiempo es cada vez mayor. Los sistemas automatizados también permiten a las empresas adaptarse más fácilmente a los cambios en la demanda y ofrecer soluciones personalizadas, ya que pueden ajustar rápidamente los parámetros de aplicación según las especificaciones del cliente. Esta flexibilidad es especialmente valiosa en industrias donde la personalización de los productos y la rapidez en la producción son esenciales para satisfacer las expectativas del mercado.
En cuanto a la sostenibilidad, las pistolas automáticas contribuyen significativamente a la reducción de la huella ambiental de la planta de pintura. Al utilizar de manera más eficiente los recursos, como la pintura y la energía, y al minimizar las emisiones de compuestos nocivos, estas herramientas ayudan a las empresas a cumplir con las normativas ambientales cada vez más estrictas. Además, la eficiencia en el uso de materiales también reduce la cantidad de residuos generados durante el proceso de pintura, lo que resulta en un menor impacto en los vertederos y una menor necesidad de tratamiento de residuos. Esto no solo ayuda a las empresas a cumplir con las regulaciones ambientales, sino que también mejora su imagen ante los consumidores y otras partes interesadas que valoran las prácticas empresariales sostenibles.
La tecnología detrás de las pistolas automáticas de pintura está en constante evolución. Los avances en materiales, diseño y control de calidad permiten mejorar aún más la precisión y eficiencia de estos dispositivos. Las pistolas de última generación están equipadas con sensores inteligentes que ajustan los parámetros de aplicación en tiempo real, garantizando que la cantidad de pintura aplicada se ajuste perfectamente a las necesidades de cada pieza. Esto no solo mejora la calidad del acabado, sino que también optimiza el uso de pintura y reduce el impacto ambiental. Además, los avances en la conectividad y la integración con otros sistemas automatizados permiten que las pistolas automáticas se integren de manera eficiente en líneas de producción completamente automatizadas, lo que facilita la supervisión, el control y la optimización de todo el proceso de pintura.
El mantenimiento de las pistolas automáticas también es más sencillo que en los sistemas de aplicación tradicionales. Los diseños modernos facilitan la limpieza y el mantenimiento regular de los equipos, lo que reduce los tiempos de inactividad y asegura que las pistolas continúen funcionando a su máxima eficiencia durante toda su vida útil. El mantenimiento preventivo y el monitoreo en tiempo real permiten detectar posibles fallos antes de que se conviertan en problemas graves, lo que mejora la fiabilidad y reduce los costos de reparación.
En resumen, las pistolas automáticas de aplicación de pintura electrostática ofrecen una serie de beneficios que mejoran la eficiencia, la calidad y la sostenibilidad de los procesos de pintura industrial. Gracias a su precisión, capacidad de adaptación, eficiencia operativa y contribución a un entorno de trabajo más seguro y ecológico, las empresas que adoptan esta tecnología pueden mejorar significativamente su competitividad en el mercado. A medida que la tecnología continúa avanzando, es probable que las pistolas automáticas sigan desempeñando un papel fundamental en la innovación y el éxito de las plantas de pintura, permitiendo a las empresas mantenerse a la vanguardia de la producción de recubrimientos de alta calidad.
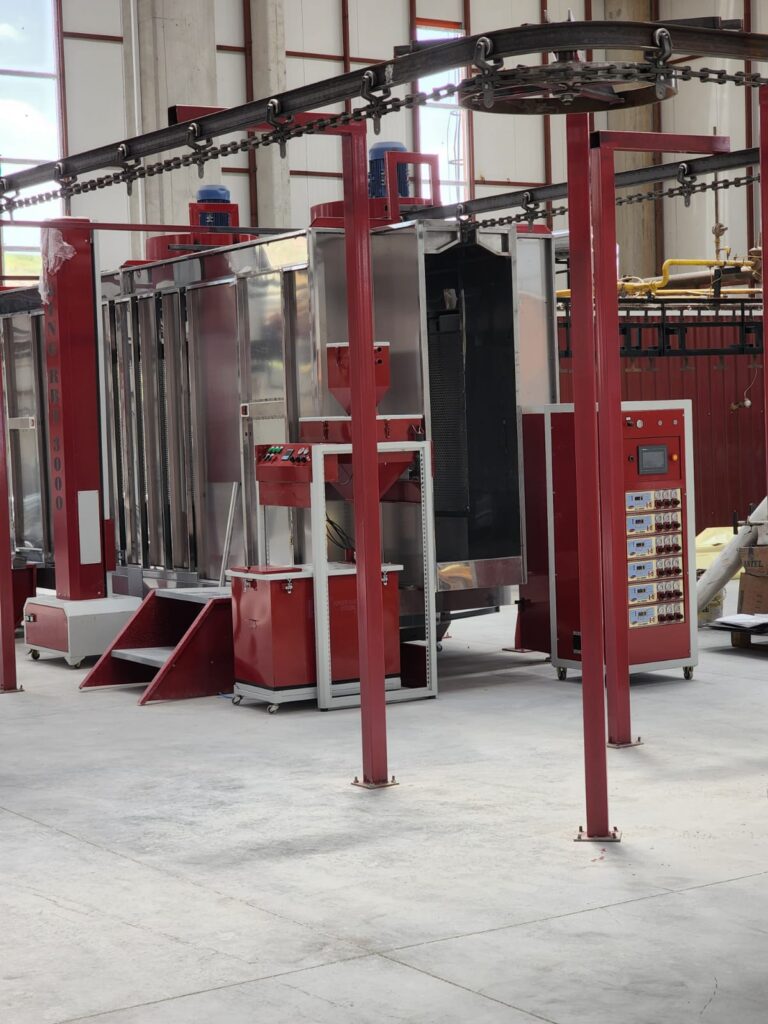
A medida que las pistolas automáticas de pintura electrostática continúan evolucionando, se espera que su integración con tecnologías más avanzadas, como la inteligencia artificial (IA) y el Internet de las Cosas (IoT), transforme aún más los procesos de recubrimiento industrial. Los sistemas equipados con IA pueden aprender de los datos generados durante las aplicaciones previas, analizando patrones y ajustando automáticamente los parámetros de pulverización para optimizar los resultados y prevenir posibles defectos. Por ejemplo, los algoritmos pueden predecir variaciones en la calidad de la pintura o detectar cambios en las condiciones del ambiente que puedan afectar la aplicación, ajustando la máquina en tiempo real para asegurar un acabado perfecto.
Además, la conectividad proporcionada por el IoT permite que las pistolas automáticas se integren de manera aún más eficiente con otras partes del sistema de producción. Mediante sensores avanzados y monitoreo en tiempo real, las empresas pueden obtener información detallada sobre el estado de la pistola, la cantidad de pintura utilizada, el tiempo de operación y cualquier mantenimiento necesario. Esto no solo ayuda a mejorar la eficiencia y reducir el tiempo de inactividad, sino que también facilita la gestión proactiva de los equipos, lo que lleva a una mayor longevidad y una menor probabilidad de fallos imprevistos. Los datos recolectados pueden ser utilizados para realizar ajustes finos en los procesos de pintura, garantizando que las piezas no solo cumplan con los estándares estéticos, sino también con los requisitos técnicos y funcionales más exigentes.
El enfoque hacia la automatización también tiene un impacto significativo en la personalización de productos. Las pistolas automáticas de pintura permiten realizar ajustes rápidos y precisos en los procesos de recubrimiento, lo que facilita la producción de lotes pequeños o la personalización masiva, sin sacrificar la eficiencia. Esto es especialmente valioso en industrias donde las preferencias de los consumidores son cada vez más específicas, como en la fabricación de dispositivos electrónicos, productos automotrices y electrodomésticos. La capacidad de ofrecer soluciones personalizadas rápidamente no solo mejora la satisfacción del cliente, sino que también fortalece la posición competitiva de las empresas en mercados que exigen alta flexibilidad y velocidad de respuesta.
Además de la flexibilidad, las pistolas automáticas permiten una mejor gestión de los recursos a lo largo de toda la cadena de producción. La reducción en el desperdicio de materiales y la energía, junto con la optimización de la aplicación de pintura, no solo contribuye a la rentabilidad de las empresas, sino también a la sostenibilidad de sus operaciones. Esto se alinea con la creciente presión sobre las industrias para reducir su impacto ambiental y operar de manera más responsable. Al lograr una aplicación más eficiente y reducir la cantidad de pintura no utilizada, las empresas también disminuyen el volumen de residuos que generan, contribuyendo a la economía circular y promoviendo un ciclo de vida más sostenible para los productos manufacturados.
La mejora en la precisión y eficiencia también reduce la necesidad de procesos de retrabajo, lo que ahorra tiempo y recursos. En industrias como la automotriz, donde los defectos en el acabado pueden resultar en costosos retrasos y pérdidas de producción, la capacidad de contar con un sistema de pintura preciso y fiable es crucial. Los sistemas automatizados también permiten un control constante sobre el grosor de la capa de pintura, lo que es fundamental para mantener la calidad del recubrimiento y evitar defectos que puedan comprometer tanto la apariencia como la durabilidad del producto.
Otro aspecto importante es la seguridad laboral. El uso de pistolas automáticas minimiza la exposición de los trabajadores a la pintura y otros productos químicos potencialmente peligrosos. Esto no solo mejora la salud y el bienestar de los empleados, sino que también reduce el riesgo de accidentes relacionados con la manipulación de equipos pesados o peligrosos. Además, la automatización del proceso permite a las empresas cumplir con los estándares de seguridad laboral más rigurosos, lo que resulta en un entorno de trabajo más seguro y eficiente.
El futuro de las pistolas automáticas de pintura parece estar enfocado en la continua mejora de la interacción entre la máquina y el operario, con interfaces más intuitivas y fáciles de usar. Esto permitirá a los operarios ajustar y controlar el proceso de pintura con mayor facilidad, sin necesidad de conocimientos técnicos profundos. Con sistemas inteligentes que proporcionan retroalimentación continua sobre el estado del proceso y la calidad del acabado, las plantas de pintura automatizadas se volverán aún más fáciles de gestionar, lo que permitirá a las empresas operar de manera más eficiente y centrarse en la innovación de productos.
Finalmente, la integración de las pistolas automáticas de pintura con sistemas de gestión empresarial y plataformas de análisis de datos abre nuevas oportunidades para mejorar la toma de decisiones estratégicas. La recopilación y el análisis de datos en tiempo real permitirán a las empresas ajustar sus operaciones en función de la demanda del mercado, optimizar sus procesos y reducir costos. La capacidad de realizar ajustes rápidos y precisos en los parámetros de aplicación también ofrece ventajas competitivas, ya que las empresas pueden responder rápidamente a cambios en los requisitos del cliente o las condiciones del mercado, lo que fortalece su posicionamiento en la industria.
En conclusión, las pistolas automáticas de pintura electrostática continúan siendo una de las herramientas más valiosas en la industria de recubrimientos. Su capacidad para mejorar la precisión, reducir el desperdicio, aumentar la eficiencia operativa y garantizar una mayor seguridad laboral las convierte en una inversión clave para las empresas que buscan mantenerse competitivas en un mercado cada vez más exigente. A medida que la tecnología avanza y se integran nuevas soluciones inteligentes, las pistolas automáticas de pintura seguirán jugando un papel fundamental en la optimización de los procesos de producción, mejorando no solo la calidad del producto final, sino también la rentabilidad y sostenibilidad de las operaciones industriales.
El continuo desarrollo y perfeccionamiento de las pistolas automáticas de pintura está impulsado por la necesidad de mejorar cada vez más la productividad, la calidad y la sostenibilidad. Uno de los avances más notables en esta tecnología es la incorporación de sistemas de monitoreo en tiempo real, que permiten realizar ajustes instantáneos en el proceso de pintura. Estos sistemas avanzados son capaces de identificar problemas en el proceso de pulverización, como irregularidades en la distribución de la pintura, y corregirlos automáticamente, lo que garantiza que cada pieza reciba un acabado consistente y de alta calidad sin la intervención manual. Este tipo de automatización no solo aumenta la precisión, sino que también minimiza el riesgo de defectos, reduciendo así la cantidad de retrabajos y desperdicios.
La incorporación de materiales más avanzados también está mejorando el rendimiento de las pistolas automáticas. Los avances en la tecnología de los componentes de la pistola, como las boquillas, los sistemas de pulverización y las piezas de conexión, están permitiendo una aplicación de pintura más uniforme y eficiente. Estos materiales no solo son más duraderos, sino que también son más resistentes a la corrosión y a la acumulación de residuos, lo que prolonga la vida útil de las pistolas y reduce la necesidad de mantenimiento. Además, el uso de estos materiales avanzados mejora la capacidad de las pistolas para trabajar con pinturas y recubrimientos más especializados, como las pinturas de acabado mate o metálico, lo que amplía las posibilidades de aplicación y la personalización de los productos.
La interoperabilidad de las pistolas automáticas con otros sistemas de producción es otro factor clave que está impulsando su adopción. Hoy en día, muchas plantas de pintura están integrando las pistolas automáticas con otros equipos automatizados, como robots de manipulación y líneas de ensamblaje. Esta integración permite una mayor sincronización entre las diferentes etapas del proceso de producción, lo que optimiza el flujo de trabajo y minimiza los tiempos de inactividad. La capacidad de las pistolas automáticas para trabajar en conjunto con otros sistemas de automatización también permite la personalización de la producción, ya que se pueden ajustar las configuraciones de la pistola en función de las especificaciones exactas de cada lote o cliente, sin necesidad de intervención manual.
Los avances en la conectividad, a través de plataformas de software y aplicaciones móviles, están haciendo que la gestión de las pistolas automáticas sea aún más accesible y eficiente. Los operarios pueden controlar y monitorear las pistolas desde dispositivos móviles, lo que les permite ajustar los parámetros de pulverización, realizar diagnósticos remotos y recibir notificaciones sobre el estado del equipo en tiempo real. Esto no solo mejora la capacidad de respuesta en caso de que se detecten problemas, sino que también permite una gestión más efectiva del mantenimiento, ya que los operarios pueden programar las intervenciones de forma preventiva antes de que ocurran fallos graves, lo que reduce los costos asociados al tiempo de inactividad inesperado.
El papel de las pistolas automáticas de pintura en la mejora de la sostenibilidad sigue siendo fundamental. Además de reducir el desperdicio de pintura y minimizar la emisión de compuestos volátiles, estos sistemas están diseñados para ser más eficientes en el uso de energía. El desarrollo de pistolas que consumen menos energía durante el proceso de aplicación, a la vez que mantienen una calidad constante en el recubrimiento, está ayudando a las empresas a reducir su huella de carbono y a cumplir con las normativas ambientales más estrictas. La adopción de tecnologías limpias, junto con la implementación de procesos más eficientes, no solo mejora la competitividad de las empresas, sino que también refuerza su compromiso con el medio ambiente y la responsabilidad social corporativa.
La automatización también está haciendo que las plantas de pintura sean más seguras para los trabajadores. Al reducir la intervención manual, se minimizan los riesgos de exposición a sustancias químicas peligrosas y a la inhalación de vapores tóxicos. Las pistolas automáticas también están diseñadas para operar en condiciones más estables y controladas, lo que disminuye el riesgo de accidentes y mejora la seguridad general en el entorno laboral. Además, la implementación de sistemas automatizados facilita el cumplimiento de las normativas de seguridad laboral, ya que los procesos son más predecibles y se pueden monitorear de manera continua.
A medida que el mercado de recubrimientos sigue evolucionando, las pistolas automáticas de pintura seguirán desempeñando un papel crucial en la optimización de los procesos de fabricación. Las empresas que invierten en esta tecnología pueden esperar no solo mejoras en la calidad del producto, sino también una mayor eficiencia operativa, un impacto ambiental reducido y una mejor competitividad en el mercado. La capacidad de las pistolas automáticas para adaptarse a una variedad de procesos y tipos de pintura, junto con su capacidad para integrar tecnologías de vanguardia como la inteligencia artificial y el Internet de las Cosas, garantiza que estas herramientas continúen siendo una de las principales fuerzas impulsoras en la industria de recubrimientos.
En el futuro cercano, es probable que veamos avances en la conectividad y la automatización de las pistolas de pintura, con interfaces más intuitivas, mejoras en los sistemas de mantenimiento predictivo y un mayor enfoque en la sostenibilidad. Las empresas que continúan explorando e invirtiendo en la última tecnología en equipos de aplicación de pintura estarán mejor posicionadas para adaptarse a las demandas cambiantes del mercado, mejorar la calidad de sus productos y reducir sus costos operativos. Las pistolas automáticas de pintura representan, sin duda, una de las inversiones más rentables y estratégicas para las empresas que buscan mantenerse a la vanguardia de la innovación y la eficiencia en el proceso de recubrimiento industrial.
Reciprocador para Pintura Electrostática
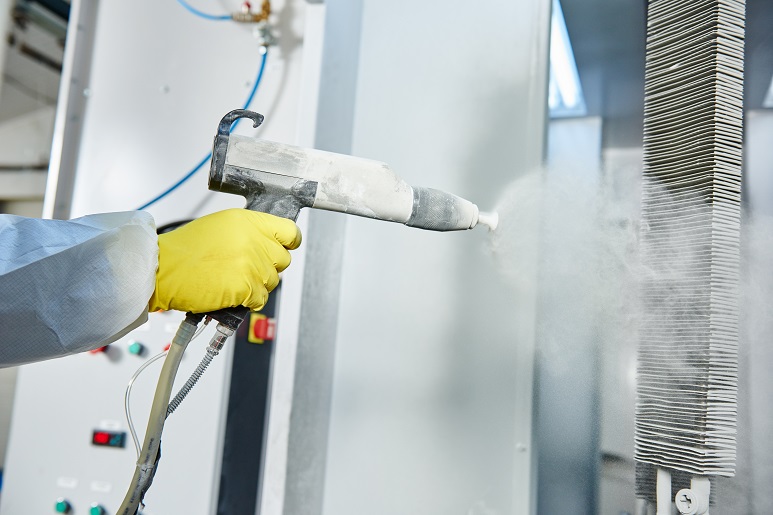
El reciprocador para pintura electrostática es un componente crucial en las plantas de recubrimiento automatizadas, especialmente cuando se busca mejorar la eficiencia en la aplicación de la pintura y garantizar una cobertura uniforme y de alta calidad. Este dispositivo se utiliza para mover la pistola de pintura de manera controlada y precisa sobre la superficie que se va a recubrir, permitiendo una distribución uniforme del material. A través de movimientos lineales o circulares, el reciprocador asegura que la pintura se aplique de manera consistente en cada parte de la pieza, incluso en las áreas más complejas y de difícil acceso, lo que mejora la calidad del acabado y reduce el desperdicio de material.
Una de las principales ventajas del reciprocador es su capacidad para cubrir grandes áreas de forma eficiente y con un mínimo de intervención humana. Al automatizar el movimiento de la pistola de pintura, se optimiza el tiempo de aplicación y se mejora la precisión, lo que permite una cobertura más uniforme y consistente. Esto es especialmente importante en industrias como la automotriz, la fabricación de electrodomésticos o la producción de componentes metálicos, donde las piezas suelen tener formas complejas que requieren una aplicación precisa de la pintura. Gracias al reciprocador, la pintura se aplica de manera óptima, garantizando un acabado de alta calidad en cada parte de la pieza.
El reciprocador también mejora la productividad de la planta de pintura, ya que su capacidad para operar de manera continua sin la necesidad de intervención manual reduce los tiempos de inactividad y aumenta la capacidad de producción. Esto es especialmente beneficioso en entornos industriales donde la demanda es alta y los plazos de entrega son estrictos. El sistema automatizado permite una producción más rápida y eficiente, lo que resulta en un aumento de la rentabilidad para las empresas que implementan este tipo de tecnología.
En términos de sostenibilidad, el reciprocador contribuye a la reducción de desperdicios de pintura. Dado que los movimientos son precisos y controlados, la cantidad de pintura que se utiliza en el proceso de aplicación es más eficiente, lo que no solo reduce los costos operativos sino que también minimiza el impacto ambiental. La reducción de desperdicio de pintura también implica un menor consumo de recursos y una menor cantidad de residuos que deben ser gestionados, lo que favorece las prácticas sostenibles dentro de las plantas de pintura.
El mantenimiento del reciprocador para pintura electrostática es relativamente sencillo, lo que lo convierte en una opción atractiva para las plantas de pintura que buscan minimizar los costos de mantenimiento y maximizar el tiempo de producción. Estos sistemas suelen estar diseñados con materiales duraderos y resistentes al desgaste, lo que garantiza una larga vida útil y una operación continua sin fallos frecuentes. Además, algunos modelos avanzados de reciprocadores están equipados con sistemas de monitoreo en tiempo real que permiten realizar un seguimiento constante de su funcionamiento. Esto ayuda a detectar cualquier anomalía o desgaste en las piezas antes de que pueda producirse un fallo importante, lo que facilita el mantenimiento preventivo y reduce los costos asociados con reparaciones inesperadas.
La flexibilidad en la configuración y programación de los reciprocadores también es un factor clave en su éxito. Los sistemas más avanzados permiten ajustar los parámetros del movimiento, como la velocidad, la amplitud y la dirección, lo que permite adaptarse a las necesidades específicas de cada trabajo. Además, la capacidad de programar diferentes patrones de movimiento para diferentes tipos de piezas permite una mayor personalización de los procesos de pintura, lo que es especialmente importante en industrias donde se requiere un acabado único para cada producto. Esta versatilidad hace que el reciprocador sea adecuado para una amplia variedad de aplicaciones y sectores industriales.
Además, la integración de reciprocadores con sistemas avanzados de control y monitoreo, como los basados en la inteligencia artificial y el Internet de las Cosas (IoT), ofrece una mayor optimización en la aplicación de pintura. Los algoritmos inteligentes pueden ajustar automáticamente los parámetros del reciprocador en función de las condiciones en tiempo real, como la variabilidad del ambiente de trabajo o los cambios en las características del producto. Esto asegura una aplicación de pintura más precisa y uniforme, lo que contribuye a la mejora continua de la calidad del acabado y a la reducción de la variabilidad en la producción.
El impacto de los reciprocadores también se extiende a la seguridad en el lugar de trabajo. Al automatizar los movimientos de la pistola de pintura, se reduce la exposición directa de los trabajadores a los vapores y partículas de pintura, lo que mejora la salud y seguridad laboral. Esto es especialmente relevante en ambientes industriales donde la manipulación de productos químicos y la exposición a sustancias tóxicas pueden representar un riesgo significativo para los operarios. La automatización también reduce el riesgo de accidentes relacionados con el movimiento manual de la pistola de pintura, como caídas o movimientos bruscos que puedan causar daños a los trabajadores o a las piezas que se están recubriendo.
En resumen, el reciprocador para pintura electrostática juega un papel esencial en la mejora de los procesos de aplicación de pintura en diversas industrias. Su capacidad para garantizar una aplicación precisa, eficiente y uniforme no solo mejora la calidad del producto final, sino que también aumenta la productividad y reduce los costos operativos. Además, su contribución a la sostenibilidad y a la seguridad laboral lo convierte en una herramienta valiosa en la evolución de las plantas de pintura automatizadas. A medida que la tecnología continúa avanzando, es probable que los reciprocadores sigan incorporando características más inteligentes y adaptativas, lo que permitirá a las empresas mantenerse competitivas en un mercado cada vez más exigente y orientado hacia la eficiencia y la sostenibilidad.
La evolución de los reciprocadores para pintura electrostática está orientada a una mayor integración con tecnologías emergentes, lo que abre nuevas posibilidades en términos de rendimiento, control y personalización. Por ejemplo, la incorporación de sistemas basados en visión artificial está permitiendo a los reciprocadores ajustar su movimiento en tiempo real en función de las características específicas de la pieza que se está pintando. Esto se logra mediante el uso de cámaras o sensores que analizan la geometría de la pieza y ajustan la trayectoria de la pistola de pintura para asegurar una cobertura óptima, incluso en las áreas más complejas o de difícil acceso.
Asimismo, los avances en la conectividad y la integración de los reciprocadores con redes industriales y plataformas de gestión empresarial están permitiendo un control más sofisticado sobre los procesos de pintura. A través de la conectividad IoT, los reciprocadores pueden enviar datos sobre su rendimiento, el estado de los componentes y la cantidad de pintura aplicada a sistemas centralizados de gestión, lo que permite una supervisión continua y una gestión más eficiente del proceso. Esto facilita no solo la optimización del uso de los recursos, sino también la programación de mantenimientos predictivos, lo que reduce los costos asociados a fallos imprevistos y mejora la disponibilidad de los equipos.
Además, la automatización avanzada ha permitido que los reciprocadores se adapten mejor a las necesidades de producción dinámica. En un entorno industrial donde la demanda de productos personalizados está en constante aumento, los reciprocadores modernos pueden ser configurados para adaptarse a diferentes tipos de productos y lotes con cambios mínimos en el proceso. Los sistemas de programación flexible permiten que los operarios ajusten los parámetros de la máquina rápidamente, lo que facilita la transición entre diferentes estilos de acabado y especificaciones de producto, sin sacrificar la calidad o la eficiencia.
La mejora de la precisión en la aplicación de la pintura a través del uso de reciprocadores también ha tenido un impacto significativo en la reducción de los costos asociados a los retrabajos y a la calidad. Gracias a la capacidad del reciprocador para controlar de manera exacta la cantidad de pintura que se aplica, se reduce la posibilidad de que se produzcan defectos como sobrecargas de pintura, manchas o inconsistencias en el acabado. Esto no solo mejora la calidad estética de los productos, sino que también aumenta la durabilidad y resistencia del recubrimiento, lo que tiene un impacto positivo en la vida útil de las piezas pintadas y reduce los costos a largo plazo.
En términos de sostenibilidad, la reducción del desperdicio de pintura y la optimización de los recursos son áreas clave en las que los reciprocadores están haciendo una diferencia. Al utilizar tecnologías avanzadas que permiten una pulverización más eficiente y controlada, las empresas pueden reducir significativamente la cantidad de pintura sobrante, lo que no solo reduce los costos de material, sino que también minimiza el impacto ambiental asociado con la fabricación. Este enfoque en la sostenibilidad está siendo cada vez más valorado en un mercado global que exige prácticas industriales responsables y respetuosas con el medio ambiente.
La automatización también ha transformado la seguridad laboral en las plantas de pintura. Con los reciprocadores asumiendo el control de los movimientos de las pistolas, se minimiza la necesidad de que los operarios manipulen directamente los equipos en áreas donde la exposición a sustancias químicas y vapores es alta. Esta reducción de la interacción directa con los procesos peligrosos no solo mejora las condiciones de trabajo, sino que también cumple con normativas de seguridad laboral más estrictas, creando un ambiente de trabajo más saludable y reduciendo el riesgo de accidentes laborales.
Además, el uso de reciprocadores no solo mejora la eficiencia de la planta, sino que también optimiza el espacio en las líneas de producción. Al reducir la intervención manual y permitir que el reciprocador opere de manera continua y precisa, se optimiza la organización de los recursos y se reducen los tiempos de operación, lo que contribuye a un mejor flujo de trabajo y a una mayor capacidad de producción. Este tipo de optimización es fundamental en industrias con grandes volúmenes de producción, donde la velocidad y la eficiencia son cruciales para mantenerse competitivos en el mercado.
A medida que la tecnología continúa evolucionando, es probable que los reciprocadores para pintura electrostática sigan avanzando hacia soluciones aún más automatizadas e inteligentes. La combinación de inteligencia artificial, robótica avanzada y sistemas de monitoreo en tiempo real permitirá a estos dispositivos anticiparse a las necesidades del proceso de pintura, ajustando dinámicamente los parámetros de aplicación según las condiciones cambiantes y las características del producto. Esto mejorará aún más la calidad de la pintura aplicada y reducirá la necesidad de intervención manual, lo que llevará a un aumento en la automatización de las plantas de pintura y a una mayor reducción de los costos operativos.
En conclusión, los reciprocadores para pintura electrostática están jugando un papel fundamental en la transformación de la industria de recubrimientos, al mejorar la precisión, la eficiencia y la sostenibilidad de los procesos de aplicación de pintura. A medida que continúan evolucionando y se integran con tecnologías más avanzadas, su capacidad para optimizar el rendimiento y reducir los costos operativos se incrementará, posicionándolos como una herramienta clave para las empresas que buscan mantenerse competitivas en un mercado que exige alta calidad, eficiencia y sostenibilidad. La adopción de reciprocadores avanzados no solo mejora la calidad del acabado y la productividad, sino que también refuerza el compromiso de las empresas con la seguridad, la innovación y la responsabilidad ambiental.
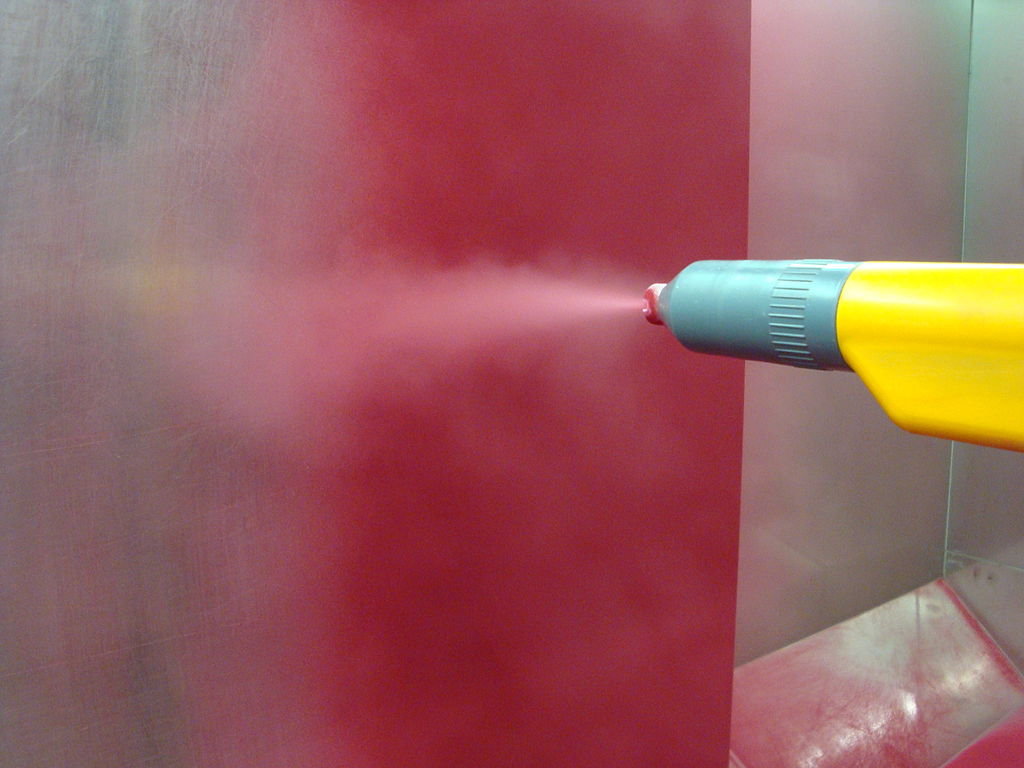
El futuro de los reciprocadores para pintura electrostática está estrechamente vinculado a la tendencia de digitalización e inteligencia en la industria manufacturera. A medida que más plantas adoptan tecnologías como el Internet de las Cosas (IoT) y el Big Data, los reciprocadores también se beneficiarán de una mayor interconectividad con otros sistemas de producción y control. Esto permitirá una supervisión más precisa y en tiempo real del rendimiento del equipo, así como la recopilación de datos que podrán ser analizados para mejorar continuamente los procesos de pintura.
Un ejemplo de esta integración es la implementación de algoritmos de aprendizaje automático (machine learning), que podrían analizar patrones en los datos recogidos por los reciprocadores y otros dispositivos del sistema. Esto podría permitir a la máquina aprender y ajustarse automáticamente a diferentes tipos de productos y condiciones operativas, optimizando el uso de recursos y mejorando la calidad del recubrimiento sin necesidad de intervención humana. Además, este tipo de inteligencia adaptativa puede prever problemas antes de que ocurran, lo que reduce aún más el tiempo de inactividad y aumenta la fiabilidad de los equipos.
Con el avance de la tecnología, también es probable que los reciprocadores sean diseñados para ser más compactos y modulares, lo que facilitaría su integración en líneas de producción más pequeñas o en configuraciones flexibles. Esto sería particularmente útil en entornos donde se producen lotes pequeños o productos personalizados, ya que permitiría cambiar fácilmente entre diferentes configuraciones de pistolas y patrones de aplicación, todo mientras se mantiene la eficiencia del proceso. La modularidad también podría contribuir a reducir los costos operativos, ya que las empresas solo tendrían que adaptar sus equipos según las necesidades específicas de producción, sin incurrir en gastos adicionales por equipamientos innecesarios.
Además, la mejora de la eficiencia energética seguirá siendo un aspecto crucial en el desarrollo de los reciprocadores. A medida que los costos de energía y las regulaciones medioambientales aumentan, la optimización del consumo energético en los equipos de pintura será esencial. Los fabricantes de reciprocadores están invirtiendo en tecnologías que permitan un consumo mínimo de energía sin comprometer la calidad de la aplicación de la pintura. Esto no solo beneficiará a las empresas al reducir sus costos operativos, sino que también contribuirá a la sostenibilidad de la industria al disminuir las emisiones de carbono.
La industria automotriz, una de las más importantes en la aplicación de pintura electrostática, es uno de los sectores donde se espera una mayor innovación en el uso de reciprocadores. Con la creciente demanda de vehículos eléctricos y la producción de piezas más ligeras y complejas, los reciprocadores deberán adaptarse a nuevos desafíos en términos de precisión y velocidad. Los avances en las capacidades de los reciprocadores permitirán a las plantas de pintura automotriz abordar estos desafíos de manera más eficiente, garantizando acabados de alta calidad y consistentes en un proceso de producción cada vez más rápido y automatizado.
El sector de la fabricación de electrodomésticos es otro que se beneficiará de las mejoras en los reciprocadores. Con la creciente demanda de electrodomésticos más estéticamente atractivos y duraderos, la aplicación de recubrimientos de alta calidad es fundamental. Los reciprocadores avanzados permitirán una aplicación precisa de pinturas especializadas, como las de acabado mate o metálico, lo que elevará el nivel de los productos terminados y proporcionará un valor añadido a los consumidores. Además, la mejora en la eficiencia del proceso y la reducción de desperdicios será crucial para que las empresas mantengan su competitividad en un mercado en el que las expectativas de los clientes son cada vez más altas.
Por último, la integración de tecnologías de sostenibilidad en el diseño de reciprocadores contribuirá a que las plantas de pintura no solo sean más eficientes desde el punto de vista económico, sino también más responsables desde el punto de vista ambiental. El diseño de equipos que utilicen materiales reciclables, que consuman menos recursos o que operen de manera más eficiente en cuanto a energía, contribuirá a la reducción de la huella ambiental de las plantas. En un mundo donde la sostenibilidad es un tema clave, los reciproca-dores diseñados con una mentalidad de economía circular podrían convertirse en una de las tecnologías más atractivas y rentables de la industria de recubrimientos.
En resumen, los avances en los reciprocadores para pintura electrostática están transformando la industria de recubrimientos de manera profunda. Con la incorporación de nuevas tecnologías de conectividad, inteligencia artificial, eficiencia energética y sostenibilidad, estos dispositivos no solo mejorarán la calidad del recubrimiento y la productividad de las plantas de pintura, sino que también jugarán un papel fundamental en la adaptación de la industria a las nuevas demandas del mercado. La capacidad de los reciprocadores para ofrecer flexibilidad, precisión y eficiencia continúa evolucionando, asegurando que seguirán siendo una herramienta esencial para las empresas que buscan mantenerse competitivas, innovadoras y responsables en un entorno industrial cada vez más desafiante.
No solo fabricamos nuestros equipos de recubrimiento en polvo, sino que también los enviamos a sus instalaciones con cuidado en todo el mundo.
No somos sólo los fabricantes de su equipo de recubrimiento en polvo, también somos sus socios de entrega en todo el mundo.
En Equipo de recubrimiento en polvo EMS, entendemos que entregarle su equipo de recubrimiento en polvo de manera rápida y segura es tan importante como fabricarlo con los más altos estándares. Es por eso que ofrecemos servicios de entrega en todo el mundo a todos nuestros clientes.
Trabajamos con una red de socios de envío experimentados y confiables para garantizar que su equipo llegue a tiempo y en perfectas condiciones. También ofrecemos una variedad de opciones de envío que se adaptan a su presupuesto y necesidades.
Ya sea que necesite que le envíen su equipo a una dirección local o a un destino internacional, podemos ayudarlo. Trabajaremos con usted para elegir la mejor opción de envío para sus necesidades y para mantenerlo actualizado sobre el estado de su envío en cada paso del camino.
Entonces, cuando elige EMS para su equipo de recubrimiento en polvo, no solo obtiene los mejores productos del mercado, sino que también obtiene la mejor experiencia de entrega posible.
Contáctenos hoy para obtener más información sobre nuestros servicios de entrega en todo el mundo.
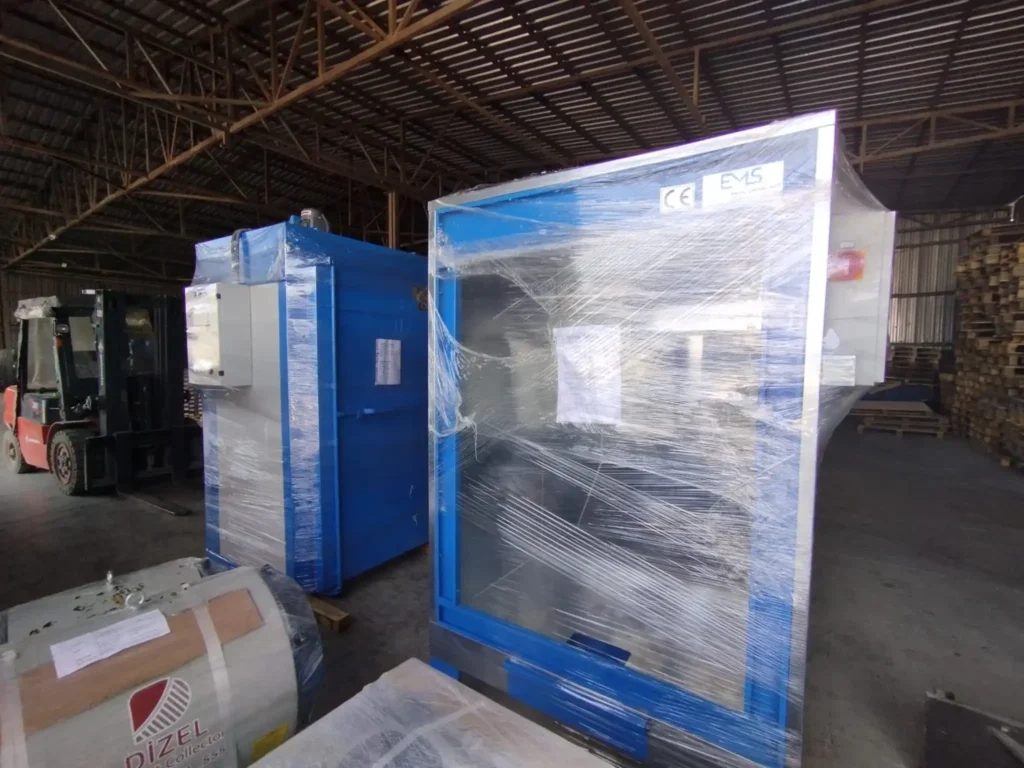
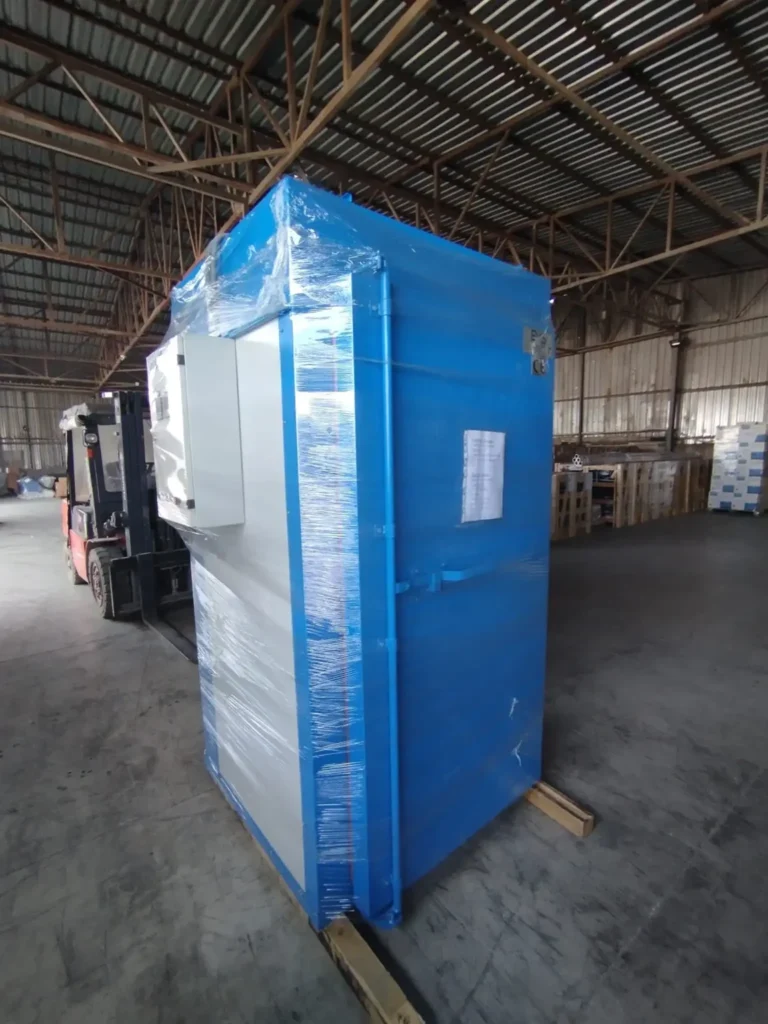
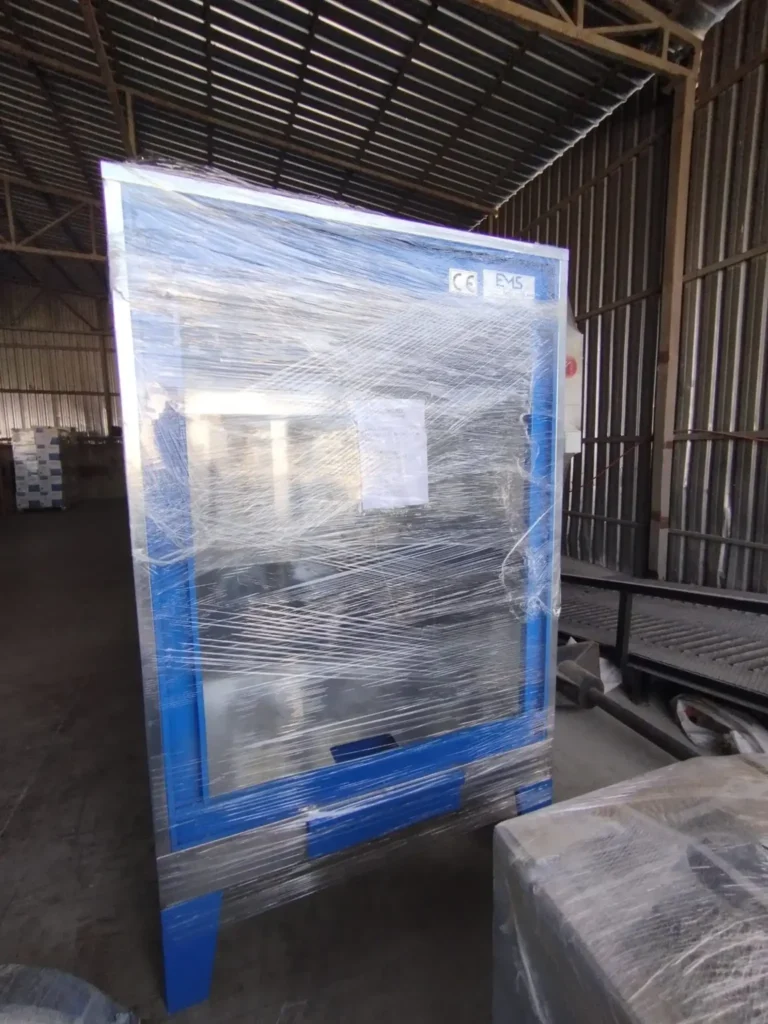
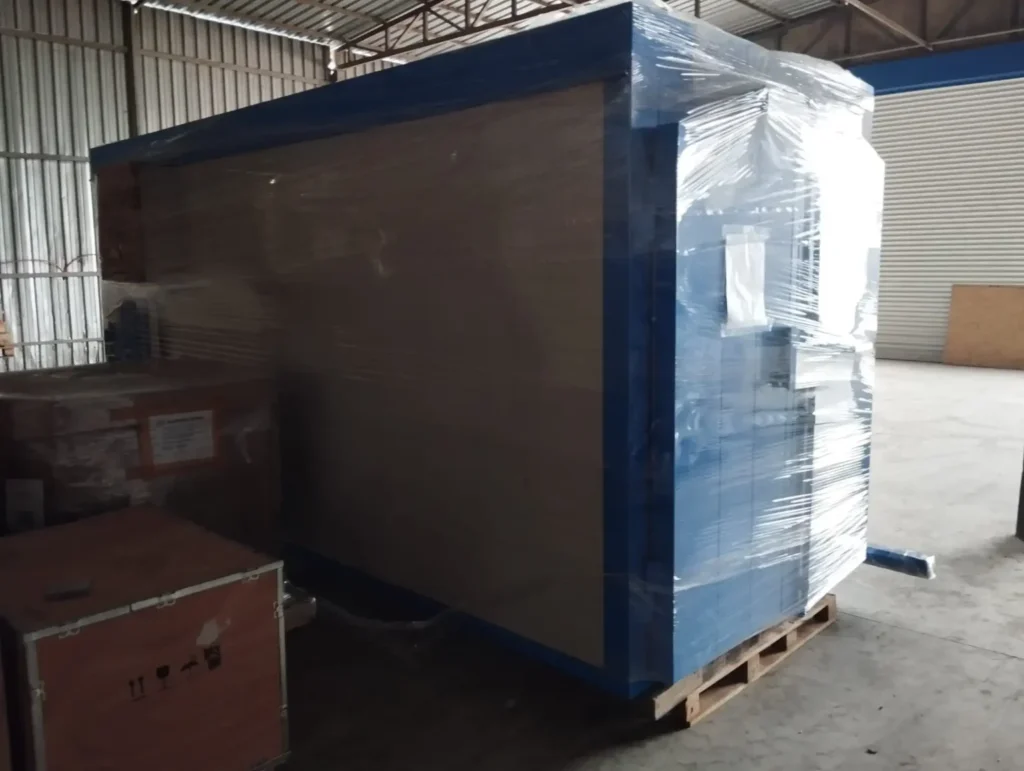